What is an HDI PCB?
An HDI PCB is a printed circuit board that features a higher wiring density per unit area compared to conventional PCBs. This is achieved through the use of finer traces, smaller vias, and advanced manufacturing techniques. HDI PCBs can have multiple layers, with some designs incorporating up to 16 or more layers.
The following table compares the key characteristics of HDI PCBs and traditional PCBs:
Feature | HDI PCB | Traditional PCB |
---|---|---|
Trace width | 3 mil or less | 4 mil or more |
Via diameter | 6 mil or less | 8 mil or more |
Pad diameter | 10 mil or less | 16 mil or more |
Conductor spacing | 3 mil or less | 4 mil or more |
Layer count | Up to 16 or more | Typically 4 to 8 |
Density | High | Low to medium |
Cost | Higher | Lower |
Applications | Advanced electronics | General-purpose electronics |
Benefits of HDI PCBs
HDI PCBs offer several advantages over traditional PCBs, making them an ideal choice for many applications. Some of the key benefits include:
1. Miniaturization
One of the primary advantages of HDI PCBs is their ability to enable miniaturization. With finer traces and smaller vias, HDI PCBs can accommodate more components in a smaller area. This is particularly important for devices that require compact designs, such as smartphones, wearables, and medical implants.
2. Improved Signal Integrity
HDI PCBs offer better signal integrity compared to traditional PCBs. The shorter traces and reduced layer count minimize signal distortion and crosstalk, resulting in cleaner and more reliable signals. This is crucial for high-speed applications, such as 5G networks and high-frequency RF devices.
3. Enhanced Thermal Management
The compact design of HDI PCBs allows for better thermal management. With components placed closer together, heat dissipation is more efficient, reducing the risk of thermal-related failures. Additionally, HDI PCBs can incorporate advanced cooling techniques, such as embedded heat sinks or thermal vias, to further enhance thermal performance.
4. Increased Reliability
HDI PCBs are known for their increased reliability compared to traditional PCBs. The use of finer traces and smaller vias reduces the risk of manufacturing defects, such as open circuits or short circuits. Moreover, HDI PCBs can incorporate additional features, such as blind and buried vias, which further enhance reliability by minimizing the number of drill holes and layer transitions.
5. Cost-Effectiveness
Although HDI PCBs have a higher initial cost compared to traditional PCBs, they can be more cost-effective in the long run. The miniaturization and increased functionality enabled by HDI PCBs can reduce the overall system cost by eliminating the need for multiple boards or external components. Additionally, the improved reliability of HDI PCBs can lead to reduced maintenance and repair costs over the product’s lifecycle.
Applications of HDI PCBs
HDI PCBs find applications in a wide range of industries and products. Some of the most common applications include:
1. Consumer Electronics
HDI PCBs are extensively used in consumer electronics, such as smartphones, tablets, laptops, and wearables. The compact design and high-performance capabilities of HDI PCBs make them ideal for these devices, which require advanced features and functionality in a small form factor.
2. Automotive Electronics
The automotive industry is increasingly adopting HDI PCBs for various applications, such as infotainment systems, advanced driver assistance systems (ADAS), and autonomous driving technologies. HDI PCBs provide the necessary reliability and performance required for these safety-critical applications.
3. Medical Devices
HDI PCBs are used in a variety of medical devices, including implantable devices, diagnostic equipment, and wearable health monitors. The miniaturization and reliability offered by HDI PCBs are crucial for these applications, where size constraints and patient safety are paramount.
4. Aerospace and Defense
The aerospace and defense industries rely on HDI PCBs for applications that require high performance and reliability in harsh environments. HDI PCBs are used in avionics, satellite systems, radar equipment, and military communications devices.
5. Industrial Automation
HDI PCBs are increasingly being adopted in industrial automation systems, such as robotics, machine vision, and process control equipment. The improved signal integrity and reliability of HDI PCBs ensure seamless operation in demanding industrial environments.
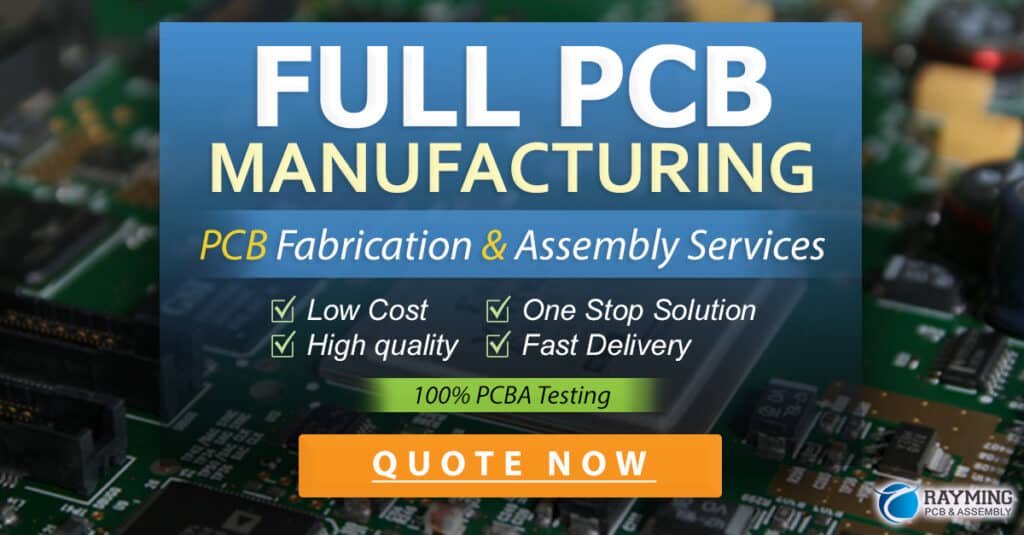
Designing HDI PCBs
Designing HDI PCBs requires careful consideration of various factors to ensure optimal performance and manufacturability. Some of the key design considerations include:
1. Layer Stackup
The layer stackup is a crucial aspect of HDI PCB Design. It determines the number of layers, their arrangement, and the interconnections between them. The layer stackup should be optimized for signal integrity, impedance control, and manufacturability.
2. Via Structure
HDI PCBs often incorporate advanced via structures, such as blind vias, buried vias, and microvias. These via structures enable higher routing density and improved signal integrity. However, they also require careful design and manufacturing considerations to ensure reliability.
3. Trace Width and Spacing
The trace width and spacing are critical parameters in HDI PCB design. Finer traces and tighter spacing enable higher density, but they also introduce challenges related to signal integrity and manufacturability. Designers must carefully balance these factors to achieve the desired performance and reliability.
4. Component Placement
Component placement is another important consideration in HDI PCB design. Components should be placed to minimize trace lengths, reduce signal distortion, and facilitate efficient routing. Designers should also consider the thermal requirements of components and ensure adequate cooling mechanisms are in place.
5. DFM Considerations
Design for manufacturability (DFM) is crucial for HDI PCBs. Designers must adhere to the manufacturing capabilities and guidelines of the chosen fabrication vendor to ensure the design can be reliably manufactured. This includes considerations such as minimum feature sizes, clearances, and tolerances.
Manufacturing HDI PCBs
Manufacturing HDI PCBs requires advanced techniques and processes compared to traditional PCBs. Some of the key manufacturing steps include:
1. Drilling
HDI PCBs often incorporate microvias, which are drilled using laser or mechanical drilling processes. Laser drilling is commonly used for microvias due to its precision and ability to create smaller via diameters.
2. Plating
After drilling, the vias are plated with copper to establish electrical connections between layers. HDI PCBs may require advanced plating techniques, such as via-in-pad plating or filled via technology, to ensure reliable interconnections.
3. Patterning
The circuit patterns are created on the PCB layers using photolithography and etching processes. HDI PCBs require high-resolution imaging and precise etching to achieve the fine features and tight tolerances required.
4. Lamination
The individual PCB layers are laminated together under high pressure and temperature to form a solid, multi-layer board. HDI PCBs may require specialized lamination processes to ensure proper bonding and alignment of the layers.
5. Surface Finish
The final step in HDI PCB manufacturing is the application of a surface finish to protect the exposed copper and facilitate component assembly. Common surface finishes for HDI PCBs include immersion gold (ENIG), electroless nickel/immersion gold (ENEPIG), and organic solderability preservative (OSP).
Frequently Asked Questions (FAQ)
1. What is the difference between HDI PCBs and traditional PCBs?
HDI PCBs have higher wiring density per unit area compared to traditional PCBs. They feature finer traces, smaller vias, and advanced manufacturing techniques, enabling miniaturization and improved performance.
2. What are the benefits of using HDI PCBs?
The benefits of using HDI PCBs include miniaturization, improved signal integrity, enhanced thermal management, increased reliability, and cost-effectiveness in the long run.
3. What are some common applications of HDI PCBs?
HDI PCBs are commonly used in consumer electronics, automotive electronics, medical devices, aerospace and defense systems, and industrial automation equipment.
4. What are the key design considerations for HDI PCBs?
The key design considerations for HDI PCBs include layer stackup, via structure, trace width and spacing, component placement, and design for manufacturability (DFM) considerations.
5. What are the manufacturing steps involved in producing HDI PCBs?
The manufacturing steps for HDI PCBs include drilling, plating, patterning, lamination, and surface finish application. These steps require advanced techniques and processes compared to traditional PCB manufacturing.
Conclusion
HDI PCBs offer numerous benefits and are well-suited for a wide range of applications that require high performance, reliability, and miniaturization. By understanding the advantages, design considerations, and manufacturing processes involved in HDI PCBs, you can determine whether they can meet your specific needs.
When deciding to use HDI PCBs, it is essential to work with an experienced design team and a reputable manufacturing partner. They can guide you through the design process, ensure adherence to best practices, and deliver high-quality HDI PCBs that meet your requirements.
As technology continues to advance, the demand for HDI PCBs is expected to grow. By staying informed about the latest developments and trends in HDI PCB technology, you can make informed decisions and leverage the benefits of these advanced circuit boards for your projects.
No responses yet