Introduction to Flex Circuit
Flexible circuits, also known as flex circuits or flexible printed circuit boards (PCBs), have revolutionized the electronics industry by providing a versatile and reliable solution for interconnecting electronic components in a wide range of applications. Unlike traditional rigid PCBs, flex circuits are designed to bend, fold, and twist without compromising their electrical functionality or structural integrity. This unique property has made flex circuits an indispensable tool in the development of compact, lightweight, and flexible electronic devices.
In this article, we will explore the various scenarios where flex circuits are the ideal choice and discuss their advantages over traditional rigid PCBs. We will also delve into the different types of flex circuits available and their specific applications in industries such as consumer electronics, medical devices, aerospace, and automotive.
Advantages of Flex Circuits
Flex circuits offer several key advantages over rigid PCBs, making them the preferred choice in many applications:
-
Flexibility and Conformity: The most significant advantage of flex circuits is their ability to bend, fold, and twist without breaking or losing electrical connectivity. This flexibility allows designers to create electronics that can conform to complex shapes and fit into tight spaces, enabling the development of more compact and streamlined devices.
-
Lightweight and Thin: Flex circuits are typically thinner and lighter than their rigid counterparts, as they are made from thin, flexible materials such as polyimide or polyester. This makes them ideal for applications where weight and size are critical factors, such as in aerospace, wearable devices, and portable electronics.
-
High Reliability: Despite their flexibility, flex circuits are highly reliable and durable. They can withstand repeated bending and flexing without suffering from fatigue or failure, making them suitable for applications that require continuous motion or are subjected to vibrations and shocks.
-
Reduced Assembly Time and Cost: Flex circuits can significantly reduce assembly time and cost by eliminating the need for separate wiring and connectors. They allow for the integration of multiple components and functions into a single, compact package, simplifying the assembly process and reducing the number of parts required.
-
Improved Signal Integrity: Flex circuits offer better signal integrity compared to traditional wiring methods, as they minimize the distance between components and reduce the risk of signal interference. This is particularly important in high-speed and high-frequency applications, where signal integrity is critical.
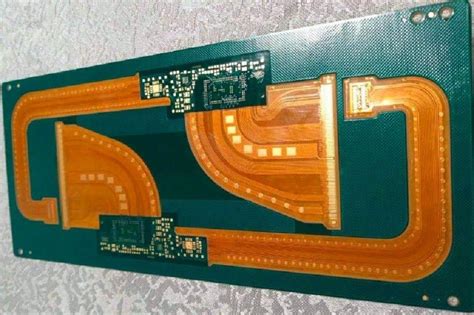
Types of Flex Circuits
There are three main types of flex circuits, each with its own unique characteristics and applications:
-
Single-Sided Flex Circuits: Single-sided flex circuits have conductive traces on only one side of the flexible substrate. They are the simplest and most cost-effective type of flex circuit and are commonly used in applications with low component density and simple interconnect requirements.
-
Double-Sided Flex Circuits: Double-sided flex circuits have conductive traces on both sides of the flexible substrate, allowing for higher component density and more complex interconnect designs. They are often used in applications that require a higher level of functionality and performance than single-sided flex circuits can provide.
-
Multi-Layer Flex Circuits: Multi-layer flex circuits consist of three or more conductive layers separated by flexible insulating layers. They offer the highest level of design flexibility and can accommodate the most complex interconnect requirements. Multi-layer flex circuits are used in applications that demand high component density, advanced signal routing, and superior electrical performance.
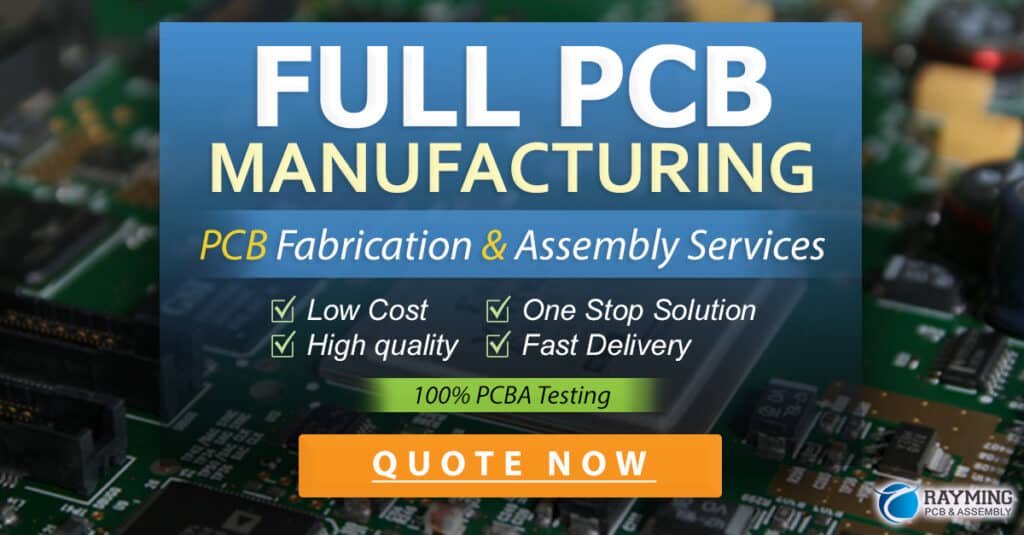
Applications of Flex Circuits
Flex circuits find applications in a wide range of industries, thanks to their unique properties and advantages. Some of the most common applications include:
Consumer Electronics
Flex circuits are extensively used in consumer electronics, such as smartphones, tablets, laptops, and wearable devices. They enable the development of slim, lightweight, and flexible designs that can withstand the rigors of daily use. Flex circuits are also used in the interconnection of displays, cameras, and other components within these devices, ensuring reliable performance and durability.
Medical Devices
The medical industry has embraced flex circuits for their ability to conform to the human body and enable the development of compact, lightweight, and non-invasive devices. Flex circuits are used in a variety of medical applications, such as:
-
Wearable Health Monitors: Flex circuits are used in the development of wearable health monitors, such as smart patches and sensors, that can continuously track vital signs and transmit data wirelessly to healthcare providers.
-
Implantable Devices: Flex circuits are used in the design of implantable medical devices, such as pacemakers, cochlear implants, and neural stimulators. Their flexibility and biocompatibility make them suitable for long-term use inside the human body.
-
Medical Imaging Equipment: Flex circuits are used in the interconnection of components within medical imaging equipment, such as X-ray machines, CT scanners, and MRI systems. They enable the development of more compact and efficient designs, while ensuring high signal integrity and reliability.
Aerospace and Defense
Flex circuits are widely used in the aerospace and defense industries, where weight, space, and reliability are critical factors. Some of the applications in these industries include:
-
Avionics: Flex circuits are used in the interconnection of electronic components within aircraft, such as navigation systems, communication equipment, and flight control systems. They enable the development of lightweight and compact designs that can withstand the harsh environmental conditions encountered in aviation.
-
Satellites: Flex circuits are used in the design of satellites and spacecraft, where weight and space are at a premium. They enable the efficient packaging of electronic components and ensure reliable performance in the extreme conditions of space.
-
Military Equipment: Flex circuits are used in a wide range of military equipment, such as portable communication devices, night vision systems, and unmanned aerial vehicles (UAVs). Their flexibility, durability, and resistance to harsh environments make them ideal for use in the field.
Automotive
The automotive industry has increasingly adopted flex circuits to enable the development of more advanced and efficient electronic systems. Some of the applications in the automotive sector include:
-
Infotainment Systems: Flex circuits are used in the interconnection of components within automotive infotainment systems, such as displays, audio systems, and navigation units. They enable the development of compact and integrated designs that enhance the user experience.
-
Advanced Driver Assistance Systems (ADAS): Flex circuits are used in the implementation of ADAS, such as adaptive cruise control, lane departure warning, and automatic emergency braking. They enable the integration of multiple sensors and processing units into a single, compact package, ensuring reliable performance and safety.
-
Electric and Hybrid Vehicles: Flex circuits are used in the design of electric and hybrid vehicle systems, such as battery management systems, motor controllers, and charging units. They enable the development of lightweight and efficient designs that optimize the performance and range of these vehicles.
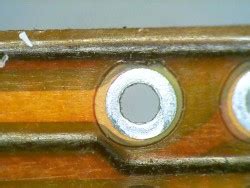
Designing with Flex Circuits
When designing with flex circuits, there are several key considerations to keep in mind:
-
Material Selection: Choosing the right flexible substrate and conductive materials is critical to ensuring the performance and reliability of the flex circuit. Common substrate materials include polyimide, polyester, and aramid, while conductive materials typically include copper, silver, and gold.
-
Bend Radius: The bend radius of a flex circuit refers to the minimum radius at which the circuit can be bent without causing damage or compromising its electrical performance. Designers must carefully consider the bend radius requirements of their application and select materials and designs that can accommodate these requirements.
-
Strain Relief: Proper strain relief is essential to preventing damage to the flex circuit during bending and flexing. This can be achieved through the use of stiffeners, adhesives, and other mechanical supports that distribute stress evenly across the circuit.
-
Signal Integrity: Maintaining signal integrity is critical in high-speed and high-frequency applications. Designers must carefully consider factors such as trace geometry, impedance control, and shielding to minimize signal loss and interference.
-
Manufacturing Process: The manufacturing process for flex circuits is more complex than that of rigid PCBs, requiring specialized equipment and expertise. Designers must work closely with their manufacturing partners to ensure that their designs can be effectively and efficiently produced.
FAQ
-
Q: What are the environmental benefits of using flex circuits?
A: Flex circuits offer several environmental benefits compared to traditional rigid PCBs. They require less material to manufacture, generate less waste during production, and are more easily recyclable due to their simple construction. Additionally, their lightweight and compact nature enables the development of more energy-efficient devices, reducing overall power consumption and carbon footprint. -
Q: Can flex circuits be used in high-temperature applications?
A: Yes, flex circuits can be designed to withstand high temperatures by using specialized materials and construction techniques. For example, polyimide substrates can maintain their mechanical and electrical properties at temperatures up to 200°C, while certain conductive materials, such as high-temperature copper alloys, can operate at even higher temperatures. -
Q: How do flex circuits compare to rigid PCBs in terms of cost?
A: The cost of flex circuits can vary depending on factors such as design complexity, material selection, and production volume. In general, flex circuits tend to have higher initial costs compared to rigid PCBs due to the specialized materials and manufacturing processes involved. However, they can offer significant cost savings in the long run by reducing assembly time, eliminating the need for separate connectors and wiring, and enabling more compact and lightweight designs. -
Q: Can flex circuits be used in applications that require high current carrying capacity?
A: Yes, flex circuits can be designed to handle high currents by using thicker conductive layers, wider traces, and specialized materials. For example, copper-clad aluminum (CCA) substrates can be used to enhance the current carrying capacity of flex circuits while maintaining their flexibility and lightweight properties. -
Q: What are the challenges associated with designing and manufacturing flex circuits?
A: Designing and manufacturing flex circuits can present several challenges, including: - Ensuring proper bend radius and strain relief to prevent damage during flexing
- Maintaining signal integrity in high-speed and high-frequency applications
- Selecting materials that can withstand the environmental and mechanical stresses of the application
- Achieving reliable and consistent manufacturing results, given the complex nature of the flex circuit production process
To overcome these challenges, designers must have a thorough understanding of flex circuit materials, design principles, and manufacturing processes, and work closely with experienced manufacturing partners to ensure the success of their projects.
Conclusion
Flex circuits have emerged as a critical technology in the development of modern electronic devices, offering unique advantages in terms of flexibility, weight, and reliability. Their ability to conform to complex shapes, fit into tight spaces, and withstand repeated bending and flexing has made them an indispensable tool in industries ranging from consumer electronics and medical devices to aerospace and automotive.
As the demand for more compact, lightweight, and flexible electronic devices continues to grow, the use of flex circuits is expected to expand even further. By understanding the advantages, types, and applications of flex circuits, as well as the key considerations in designing and manufacturing them, engineers and designers can harness the full potential of this innovative technology to create the next generation of electronic devices.
Industry | Applications |
---|---|
Consumer Electronics | Smartphones, tablets, laptops, wearable devices |
Medical Devices | Wearable health monitors, implantable devices, medical imaging equipment |
Aerospace and Defense | Avionics, satellites, military equipment |
Automotive | Infotainment systems, advanced driver assistance systems (ADAS), electric and hybrid vehicles |
No responses yet