Understanding BGA Footprint and Land Pattern
Ball Grid Array (BGA) is a surface-mount packaging used for integrated circuits (ICs) that utilizes a grid of solder balls underneath the package for connection to the printed circuit board (PCB). The BGA footprint and land pattern are crucial aspects of PCB design that ensure proper connectivity and reliability of the mounted components.
What is a BGA Footprint?
A BGA footprint refers to the arrangement of solder balls on the underside of a BGA package. The footprint is determined by the package size, ball pitch (distance between the centers of adjacent balls), and the number of balls. The footprint is usually represented by a matrix, such as 10×10, 12×12, or 14×14, indicating the number of rows and columns of solder balls.
What is a BGA Land Pattern?
A BGA land pattern, on the other hand, is the corresponding arrangement of copper pads on the PCB that match the BGA footprint. The land pattern is designed to accommodate the solder balls of the BGA package and provide electrical connectivity between the package and the PCB. The land pattern must be accurately designed to ensure proper alignment and prevent short circuits or open connections.
Designing BGA Land Patterns
Designing a BGA land pattern involves several considerations to ensure optimal performance and reliability. Some of the key factors to consider include:
1. Pad Size and Shape
The pad size and shape are critical in ensuring a reliable solder joint between the BGA package and the PCB. The pad size should be slightly larger than the solder ball diameter to allow for some misalignment during assembly. The most common pad shapes are circular and oval, with oval pads providing more tolerance for misalignment in one direction.
2. Pad Pitch
The pad pitch is the distance between the centers of adjacent pads on the PCB. It must match the ball pitch of the BGA package to ensure proper alignment. Common pitches for BGA packages range from 0.5mm to 1.27mm, with finer pitches becoming more prevalent as package sizes decrease.
3. Solder Mask Opening
The solder mask opening is the area around the copper pad that is exposed through the solder mask layer. The opening should be slightly larger than the copper pad to prevent solder mask from encroaching on the pad and interfering with the solder joint. The solder mask opening also helps to contain the solder during reflow and prevent bridging between adjacent pads.
4. Via Placement
Vias are used to connect the BGA pads to other layers of the PCB. The placement of vias is critical to ensure signal integrity and prevent interference. Vias should be placed as close to the pad as possible to minimize the inductance and resistance of the connection. However, the via should not be placed too close to the pad edge, as this can cause the solder to wick down the via and create a void in the solder joint.
5. Thermal Management
BGAs generate significant heat during operation, which must be dissipated to prevent damage to the package and the PCB. Thermal vias can be added to the land pattern to provide a path for heat to be conducted away from the package and into the PCB. The number and placement of thermal vias depend on the power dissipation of the package and the thermal requirements of the application.
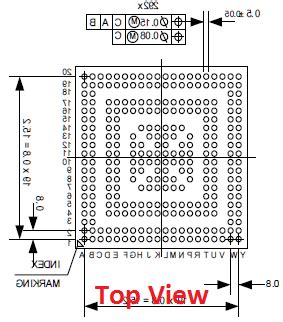
Common BGA Footprints and Land Patterns
There are several standard BGA footprints and land patterns that are widely used in the industry. Some of the most common include:
1. Plastic BGA (PBGA)
PBGAs are the most common type of BGA package, with a plastic substrate and a matrix of solder balls. Typical ball counts range from 36 to over 1000, with pitches from 0.5mm to 1.27mm. The land pattern for a PBGA typically consists of circular pads with a diameter slightly larger than the solder ball diameter.
2. Ceramic BGA (CBGA)
CBGAs use a ceramic substrate instead of plastic, which provides better thermal and mechanical performance. CBGAs are often used in high-reliability applications such as aerospace and defense. The land pattern for a CBGA is similar to that of a PBGA, but the pad size and pitch may be different due to the different properties of the ceramic substrate.
3. Tape BGA (TBGA)
TBGAs use a flexible tape substrate instead of a rigid plastic or ceramic substrate. TBGAs are often used in applications that require a low profile or flexibility, such as mobile devices. The land pattern for a TBGA is similar to that of a PBGA, but the pad size and pitch may be different due to the different properties of the tape substrate.
4. Fine-Pitch BGA (FBGA)
FBGAs have a finer pitch than standard BGAs, typically 0.5mm or less. FBGAs are used in high-density applications where space is limited, such as mobile devices and wearables. The land pattern for an FBGA requires tighter tolerances and more precise manufacturing processes to ensure proper alignment and prevent short circuits.
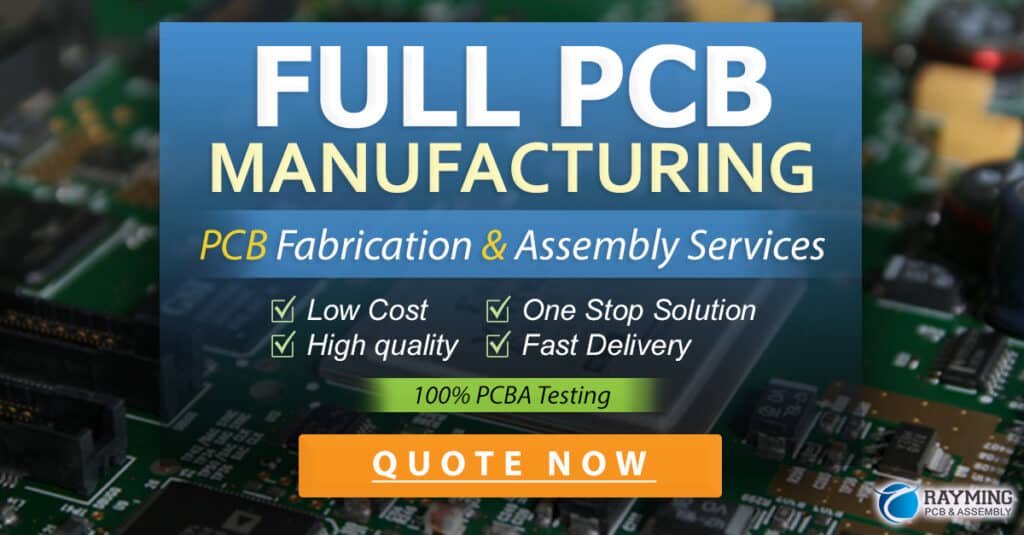
BGA Land Pattern Design Guidelines
To ensure optimal performance and reliability of BGA assemblies, follow these design guidelines:
- Use a pad size that is slightly larger than the solder ball diameter, typically 10-20% larger.
- Use a solder mask opening that is slightly larger than the copper pad, typically 50-100 microns larger.
- Place vias as close to the pad as possible, but not closer than 100 microns to the pad edge.
- Use enough thermal vias to dissipate the heat generated by the package, typically 1-4 vias per pad depending on the power dissipation.
- Follow the manufacturer’s recommended land pattern for the specific BGA package being used.
- Use a stencil thickness that is appropriate for the solder ball size and pitch, typically 100-150 microns for standard BGAs and 75-100 microns for FBGAs.
- Use a solder paste with a particle size that is appropriate for the solder ball size and pitch, typically Type 3 or Type 4 for standard BGAs and Type 5 or Type 6 for FBGAs.
- Use a reflow profile that is appropriate for the solder paste and substrate material, typically a ramp-to-spike profile with a peak temperature of 235-245°C for lead-free solder.
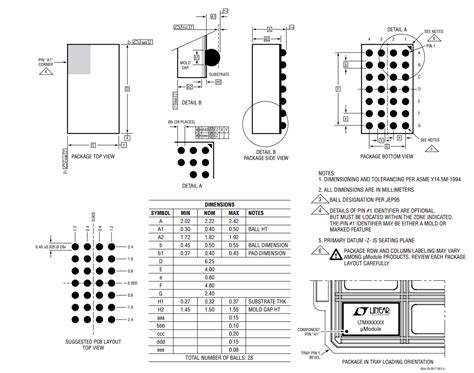
FAQ
1. What is the difference between a BGA footprint and a land pattern?
A BGA footprint refers to the arrangement of solder balls on the underside of the BGA package, while a land pattern refers to the corresponding arrangement of copper pads on the PCB.
2. What is the most common pad shape for BGA land patterns?
The most common pad shapes for BGA land patterns are circular and oval. Oval pads provide more tolerance for misalignment in one direction.
3. What is the purpose of the solder mask opening in a BGA land pattern?
The solder mask opening helps to contain the solder during reflow and prevent bridging between adjacent pads. It also prevents the solder mask from encroaching on the pad and interfering with the solder joint.
4. How many thermal vias are typically used per pad in a BGA land pattern?
The number of thermal vias used per pad depends on the power dissipation of the package, but typically ranges from 1-4 vias per pad.
5. What is the typical stencil thickness used for BGA assembly?
The typical stencil thickness used for BGA assembly is 100-150 microns for standard BGAs and 75-100 microns for FBGAs.
BGA Type | Pitch (mm) | Ball Count | Pad Shape | Stencil Thickness (microns) |
---|---|---|---|---|
PBGA | 0.5 – 1.27 | 36 – 1000+ | Circular | 100 – 150 |
CBGA | 0.5 – 1.27 | 36 – 1000+ | Circular | 100 – 150 |
TBGA | 0.5 – 1.27 | 36 – 1000+ | Circular | 100 – 150 |
FBGA | 0.3 – 0.5 | 100 – 1000+ | Circular | 75 – 100 |
In conclusion, designing a BGA land pattern requires careful consideration of pad size, shape, pitch, solder mask opening, via placement, and thermal management. By following the recommended design guidelines and using standard footprints and land patterns, designers can ensure optimal performance and reliability of BGA assemblies. As package sizes continue to shrink and ball counts continue to increase, the importance of accurate and precise BGA land pattern design will only continue to grow.
No responses yet