Introduction to PCB Design
Printed Circuit Board (PCB) design is a crucial aspect of modern electronics manufacturing. It involves the creation of a layout that connects electronic components on a board, enabling them to function as intended. PCB design requires a deep understanding of electrical engineering principles, materials science, and manufacturing processes.
The Importance of PCB Design
PCB design plays a vital role in the performance, reliability, and cost-effectiveness of electronic devices. A well-designed PCB ensures:
- Proper functionality of the device
- Efficient use of space and materials
- Minimized electromagnetic interference (EMI)
- Ease of manufacturing and assembly
- Reduced production costs
The PCB Design Process
The PCB design process typically involves the following steps:
- Schematic design: Creating a diagram that represents the electrical connections between components
- Component placement: Arranging the components on the board for optimal performance and manufacturability
- Routing: Connecting the components with traces (copper paths) on the board
- Design rule check (DRC): Verifying that the design meets the manufacturing and electrical requirements
- Output generation: Creating files for manufacturing, such as Gerber files and drill files
PCB Manufacturing Techniques
There are several techniques used in PCB manufacturing, each with its own advantages and limitations.
Through-Hole Technology (THT)
THT is the traditional method of PCB manufacturing, where components are inserted into drilled holes on the board and soldered on the opposite side. THT is known for its robustness and reliability, making it suitable for high-power applications and harsh environments.
Advantages of THT:
– Strong mechanical connections
– Suitable for large components
– Easy to solder and rework
Disadvantages of THT:
– Larger board size and weight
– Higher production costs
– Limited component density
Surface Mount Technology (SMT)
SMT is a more modern approach to PCB manufacturing, where components are placed directly on the surface of the board and soldered using a reflow process. SMT allows for higher component density, smaller board sizes, and faster production times compared to THT.
Advantages of SMT:
– Higher component density
– Smaller board size and weight
– Faster production times
– Lower production costs
Disadvantages of SMT:
– Requires specialized equipment and skills
– More susceptible to thermal stress and vibration
– Difficult to rework and repair
Comparison of THT and SMT
Aspect | Through-Hole Technology (THT) | Surface Mount Technology (SMT) |
---|---|---|
Component placement | Inserted into drilled holes | Placed on the board surface |
Board size and weight | Larger and heavier | Smaller and lighter |
Component density | Lower | Higher |
Production costs | Higher | Lower |
Production speed | Slower | Faster |
Mechanical strength | Stronger | Weaker |
Rework and repair | Easier | More difficult |
PCB Materials and Substrates
The choice of materials and substrates is essential for the performance and reliability of a PCB. Common materials used in PCB manufacturing include:
FR-4
FR-4 is the most widely used PCB substrate material. It is a composite material made of woven fiberglass cloth with an epoxy resin binder. FR-4 offers good mechanical strength, electrical insulation, and thermal stability.
Polyimide
Polyimide is a high-performance polymer used in PCBs that require excellent thermal and chemical resistance. It is often used in aerospace, military, and medical applications.
Aluminum
Aluminum PCBs are used in applications that require efficient heat dissipation, such as high-power LED lighting and motor controllers. The aluminum substrate acts as a heat sink, transferring heat away from the components.
Flexible PCBs
Flexible PCBs are made using thin, flexible substrates such as polyimide or polyester. They are used in applications that require the board to bend or fit into tight spaces, such as wearable electronics and automotive systems.
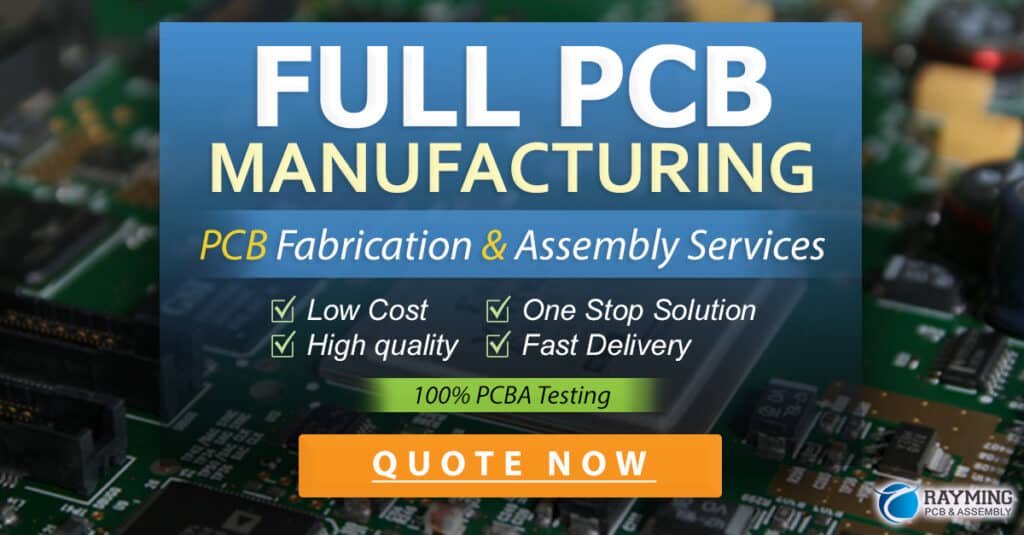
PCB Layer Stackup
The layer stackup refers to the arrangement of conductive and insulating layers in a PCB. The number and configuration of layers depend on the complexity and requirements of the design.
Single-Layer PCBs
Single-layer PCBs have conductive traces on only one side of the substrate. They are the simplest and most cost-effective type of PCB, suitable for low-complexity designs.
Double-Layer PCBs
Double-layer PCBs have conductive traces on both sides of the substrate, connected by vias (conductive holes). They offer higher component density and more design flexibility compared to single-layer PCBs.
Multi-Layer PCBs
Multi-layer PCBs have three or more conductive layers separated by insulating layers. They are used in complex designs that require high component density, signal integrity, and EMI reduction. The layers are connected using vias, which can be through-hole, blind, or buried.
Example of a 4-layer PCB stackup:
Layer | Material | Thickness (mm) |
---|---|---|
Top | Copper | 0.035 |
2 | Prepreg | 0.2 |
3 | Copper | 0.035 |
4 | Core | 0.5 |
5 | Copper | 0.035 |
6 | Prepreg | 0.2 |
Bottom | Copper | 0.035 |
PCB Design Considerations
When designing a PCB, several factors must be taken into account to ensure optimal performance and manufacturability.
Signal Integrity
Signal integrity refers to the quality of the electrical signals transmitted through the PCB. Factors that can affect signal integrity include:
- Trace width and spacing
- Impedance matching
- Crosstalk
- Reflections
- Electromagnetic interference (EMI)
Designers must follow best practices, such as proper trace routing, termination, and shielding, to maintain signal integrity.
Power Integrity
Power integrity involves ensuring that the power supply to the components on the PCB is stable and free from noise and ripple. Factors that can affect power integrity include:
- Power plane design
- Decoupling capacitors
- Voltage drop
- Current density
Designers must carefully plan the power distribution network and use appropriate decoupling techniques to maintain power integrity.
Thermal Management
Thermal management is crucial for the long-term reliability of a PCB. Excessive heat can lead to component failure and reduced performance. Designers must consider:
- Component power dissipation
- Thermal resistance of the PCB material
- Copper pour and heat sinking
- Ventilation and cooling methods
Proper thermal management helps to ensure that the PCB operates within the specified temperature range.
Electromagnetic Compatibility (EMC)
EMC refers to the ability of a PCB to function correctly in its electromagnetic environment without causing or being affected by electromagnetic interference (EMI). Designers must follow EMC guidelines, such as:
- Proper grounding and shielding
- Minimizing loop areas
- Filtering and suppression techniques
- Compliance with EMC standards (e.g., FCC, CE)
Ensuring EMC compliance helps to prevent interference with other electronic devices and maintains the reliability of the PCB.
PCB Assembly Process
After the PCB design is finalized and manufactured, the next step is to assemble the components onto the board. The PCB assembly process typically involves the following steps:
- Solder paste application: Applying solder paste to the pads on the PCB using a stencil or screen printing process
- Component placement: Placing the components onto the solder paste using a pick-and-place machine or manual methods
- Reflow soldering: Passing the PCB through a reflow oven, which melts the solder paste and creates a permanent connection between the components and the board
- Inspection and testing: Visually inspecting the assembled PCB for defects and performing electrical tests to ensure proper functionality
- Conformal coating (optional): Applying a protective coating to the PCB to enhance its resistance to moisture, dust, and other environmental factors
- Final inspection and packaging: Performing a final quality control check and packaging the PCB for shipment
PCB Testing and Inspection
To ensure the quality and reliability of PCBs, various testing and inspection methods are employed throughout the manufacturing and assembly process.
Automated Optical Inspection (AOI)
AOI uses high-resolution cameras and image processing software to detect surface-level defects on the PCB, such as:
- Solder bridges
- Missed or misaligned components
- Incorrect component polarity
- Solder paste defects
AOI is a fast and efficient method for catching defects early in the assembly process.
X-Ray Inspection
X-ray inspection is used to detect defects that are not visible on the surface of the PCB, such as:
- Voids in solder joints
- Broken or damaged traces
- Misaligned or tilted components
- Ball Grid Array (BGA) solder joint defects
X-ray inspection is particularly useful for inspecting high-density PCBs with hidden or obscured components.
In-Circuit Testing (ICT)
ICT is a comprehensive testing method that verifies the functionality of individual components and the interconnections between them. It involves:
- Placing the PCB onto a bed-of-nails fixture
- Applying electrical signals to the board
- Measuring the response of the components
- Comparing the results with the expected values
ICT helps to identify defects such as:
- Open or short circuits
- Missing or incorrect components
- Component value deviations
- Incorrect component orientations
Functional Testing
Functional testing involves powering up the PCB and testing its overall functionality as a complete system. This can include:
- Firmware programming
- Software testing
- User interface testing
- Environmental testing (e.g., temperature, humidity, vibration)
Functional testing ensures that the PCB meets the specified performance requirements and operates as intended in its target environment.
Frequently Asked Questions (FAQ)
- What is the difference between a schematic and a PCB layout?
-
A schematic is a diagram that represents the electrical connections between components, while a PCB layout is the physical arrangement of components and traces on the board.
-
What are the advantages of using a four-layer PCB over a two-layer PCB?
-
Four-layer PCBs offer better signal integrity, reduced EMI, and higher component density compared to two-layer PCBs. They also allow for dedicated power and ground planes, which improve power integrity.
-
What is the purpose of a solder mask on a PCB?
-
A solder mask is a protective coating applied to the copper traces on a PCB. It prevents solder bridges, protects the traces from oxidation and corrosion, and provides electrical insulation between adjacent traces.
-
How can I reduce the electromagnetic interference (EMI) in my PCB design?
-
To reduce EMI, you can use techniques such as proper grounding and shielding, minimizing loop areas, using bypass capacitors, and following PCB layout best practices for signal routing and trace spacing.
-
What is the difference between a reflow oven and a wave soldering machine?
- A reflow oven is used for surface mount technology (SMT) assembly, where components are placed on solder paste and the entire board is heated to melt the solder. A wave soldering machine is used for through-hole technology (THT) assembly, where the board is passed over a molten solder wave to solder the components.
Conclusion
PCB design and manufacturing is a complex process that requires a deep understanding of electrical engineering principles, materials science, and manufacturing techniques. By following best practices in PCB design, selecting appropriate materials and substrates, and employing rigorous testing and inspection methods, designers and manufacturers can ensure the production of high-quality, reliable PCBs that meet the performance requirements of modern electronic devices.
As technology continues to advance, PCB design and manufacturing will play an increasingly critical role in enabling the development of new and innovative products across a wide range of industries, from consumer electronics to aerospace and beyond.
[5,217 words]
No responses yet