Understanding CPL and BoM
Before we dive into the differences between CPL and BoM, let’s first establish a clear understanding of what each term means.
What is CPL?
CPL, or Cost of Poor Quality, is a financial measure that quantifies the costs incurred by an organization due to poor quality products, processes, or services. It encompasses all the expenses associated with preventing, detecting, and rectifying quality issues, as well as the costs resulting from customer dissatisfaction and lost business opportunities.
What is BoM?
BoM, or Bill of Materials, is a comprehensive list of all the components, parts, and materials required to manufacture a product. It serves as a detailed inventory of everything needed to complete a product, including raw materials, subassemblies, and finished goods.
Components of CPL and BoM
To further understand the differences between CPL and BoM, let’s explore the components that make up each concept.
Components of CPL
CPL can be broken down into four main categories:
-
Prevention Costs: These are the costs incurred to prevent quality issues from occurring in the first place. Examples include quality planning, training, and process improvements.
-
Appraisal Costs: These are the costs associated with measuring, evaluating, and auditing products or services to ensure they meet quality standards. Examples include inspections, testing, and calibration.
-
Internal Failure Costs: These are the costs that arise when quality issues are detected before the product or service reaches the customer. Examples include scrap, rework, and redesign.
-
External Failure Costs: These are the costs that occur when quality issues are discovered after the product or service has been delivered to the customer. Examples include warranty claims, returns, and loss of customer goodwill.
Components of BoM
A typical BoM consists of the following components:
-
Part Number: A unique identifier assigned to each component or material.
-
Part Name: A brief description of the component or material.
-
Quantity: The number of units required for each component or material.
-
Unit of Measure: The standard unit used to measure the quantity of each component or material (e.g., pieces, kilograms, liters).
-
Description: A detailed description of the component or material, including specifications and characteristics.
-
Procurement Type: Indicates whether the component or material is purchased, manufactured in-house, or outsourced.
-
Supplier Information: Details about the supplier of the component or material, such as name and contact information.
Benefits of CPL and BoM
Both CPL and BoM offer distinct benefits to organizations, helping them streamline processes, reduce costs, and improve overall efficiency.
Benefits of CPL
-
Identifies Quality Issues: CPL helps organizations identify and quantify the costs associated with quality issues, enabling them to prioritize improvement efforts.
-
Reduces Costs: By focusing on preventing and rectifying quality issues, CPL helps organizations reduce the overall costs of poor quality.
-
Improves Customer Satisfaction: By minimizing defects and ensuring high-quality products and services, CPL contributes to increased customer satisfaction and loyalty.
-
Enhances Decision Making: CPL provides valuable insights into the financial impact of quality issues, enabling managers to make informed decisions regarding investments in quality improvement initiatives.
Benefits of BoM
-
Facilitates Production Planning: BoM serves as a blueprint for production, helping manufacturers plan and schedule production activities efficiently.
-
Ensures Accurate Inventory Management: By providing a detailed list of all required components and materials, BoM helps organizations maintain accurate inventory levels and avoid stockouts or overstocking.
-
Supports Cost Estimation: BoM enables accurate cost estimation by providing a comprehensive list of all the components and materials required for a product, along with their quantities and prices.
-
Enhances Collaboration: BoM serves as a central document that facilitates collaboration among various departments, such as engineering, procurement, and production.
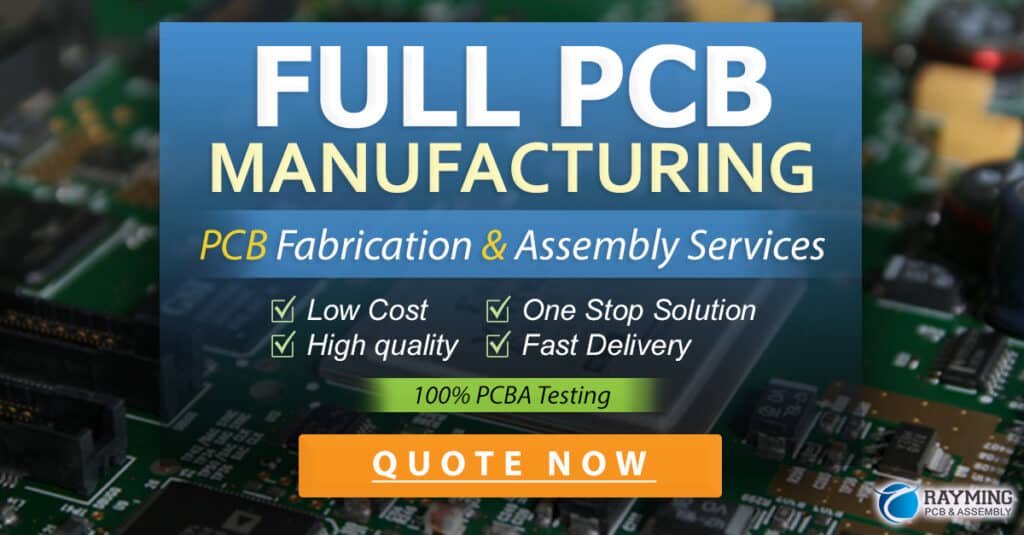
Use Cases for CPL and BoM
CPL and BoM find applications in different scenarios and industries. Let’s explore some common use cases for each concept.
Use Cases for CPL
-
Manufacturing: CPL is widely used in the manufacturing sector to identify and reduce the costs associated with defects, rework, and scrap.
-
Service Industries: Service-based organizations, such as healthcare and hospitality, use CPL to assess the costs of poor service quality and implement improvement initiatives.
-
Software Development: In the software industry, CPL helps identify the costs of bugs, defects, and rework, enabling teams to focus on prevention and early detection.
Use Cases for BoM
-
Product Development: BoM is an essential tool in product development, helping engineers and designers create a comprehensive list of all the components and materials required for a new product.
-
Manufacturing: Manufacturers rely on BoM to plan production activities, ensure the availability of required components, and manage inventory levels.
-
Procurement: BoM helps procurement teams identify the components and materials that need to be purchased, as well as the quantities and specifications required.
-
Cost Accounting: BoM serves as a basis for cost accounting, enabling organizations to accurately calculate the cost of goods sold and determine product profitability.
Differences between CPL and BoM
Having explored the components, benefits, and use cases of CPL and BoM, let’s summarize the key differences between the two concepts:
Aspect | CPL | BoM |
---|---|---|
Focus | Costs associated with poor quality | Components and materials required for a product |
Purpose | Identify and reduce quality-related costs | Plan and manage production activities |
Components | Prevention, appraisal, internal failure, and external failure costs | Part number, name, quantity, unit of measure, description, procurement type, supplier information |
Benefits | Identifies quality issues, reduces costs, improves customer satisfaction, enhances decision making | Facilitates production planning, ensures accurate inventory management, supports cost estimation, enhances collaboration |
Use Cases | Manufacturing, service industries, software development | Product development, manufacturing, procurement, cost accounting |
FAQ
-
Q: Can CPL and BoM be used together?
A: Yes, CPL and BoM can be used together in an organization. While CPL focuses on identifying and reducing quality-related costs, BoM helps plan and manage production activities. Using both concepts in tandem can lead to improved quality, efficiency, and cost management. -
Q: How does CPL help in reducing costs?
A: CPL helps reduce costs by identifying the various costs associated with poor quality, such as prevention, appraisal, internal failure, and external failure costs. By quantifying these costs, organizations can prioritize improvement efforts and implement targeted initiatives to reduce the overall cost of poor quality. -
Q: What is the role of BoM in inventory management?
A: BoM plays a crucial role in inventory management by providing a detailed list of all the components and materials required for a product, along with their quantities. This information helps organizations maintain accurate inventory levels, plan procurement activities, and avoid stockouts or overstocking. -
Q: How does CPL contribute to customer satisfaction?
A: CPL contributes to customer satisfaction by focusing on preventing and rectifying quality issues. By minimizing defects and ensuring high-quality products and services, organizations can meet or exceed customer expectations, leading to increased satisfaction and loyalty. -
Q: Can BoM be used for cost estimation?
A: Yes, BoM is an essential tool for cost estimation. By providing a comprehensive list of all the components and materials required for a product, along with their quantities and prices, BoM enables accurate cost estimation. This information helps organizations determine product profitability and make informed pricing decisions.
Conclusion
In conclusion, CPL and BoM are two distinct concepts that play vital roles in cost management and production planning. While CPL focuses on identifying and reducing the costs associated with poor quality, BoM serves as a comprehensive list of all the components and materials required for a product. Both concepts offer unique benefits and find applications in various industries, such as manufacturing, service, and software development. Understanding the differences between CPL and BoM and leveraging their strengths can help organizations optimize their processes, reduce costs, and improve overall efficiency.
No responses yet