Introduction
Drones have become increasingly popular in recent years, with applications ranging from aerial photography and videography to package delivery and even search and rescue missions. At the heart of every drone is a Custom Drone Board, which serves as the central control unit for the entire system. In this article, we will explore the core components of a custom drone board and how they work together to enable the drone to fly and perform its intended functions.
What is a Custom Drone Board?
A custom drone board is a printed circuit board (PCB) that is specifically designed and built for use in a drone. It contains all of the necessary components and circuitry to control the drone’s motors, sensors, and other peripherals. The custom drone board is the brain of the drone, responsible for processing sensor data, controlling the motors, and communicating with the user’s remote control or ground station.
Key Components of a Custom Drone Board
The core components of a custom drone board can be divided into several categories:
- Microcontroller or Flight Controller
- Motor Speed Controllers (ESCs)
- Sensors
- Power Management
- Communication Modules
Let’s take a closer look at each of these components and their roles in the custom drone board.
1. Microcontroller or Flight Controller
The microcontroller, also known as the flight controller, is the central processing unit of the custom drone board. It is responsible for running the drone’s software, processing sensor data, and controlling the motors and other peripherals. The flight controller is typically a small, lightweight, and low-power microcontroller such as an ARM Cortex-M or STM32 series.
Some popular flight controllers used in custom drone boards include:
- ArduPilot
- Pixhawk
- Naze32
- CC3D
These flight controllers come with their own software and development tools, which allow users to customize and program the drone’s behavior.
2. Motor Speed Controllers (ESCs)
Motor speed controllers, or ESCs, are responsible for controlling the speed and direction of the drone’s motors. Each motor on the drone requires its own ESC, which receives signals from the flight controller and adjusts the motor’s speed accordingly. ESCs are typically rated based on their maximum current handling capability, which determines the size and power of the motors they can control.
ESC Rating | Maximum Motor Size |
---|---|
10A | Small motors (< 100W) |
20A | Medium motors (100-200W) |
30A | Large motors (200-400W) |
40A+ | Extra-large motors (> 400W) |
3. Sensors
Sensors are an essential component of any custom drone board, as they provide the flight controller with the necessary data to maintain stable flight and perform autonomous functions. Some common sensors found on custom drone boards include:
- Inertial Measurement Unit (IMU): Measures the drone’s acceleration, rotation, and orientation using a combination of accelerometers, gyroscopes, and magnetometers.
- Barometer: Measures the drone’s altitude by detecting changes in air pressure.
- GPS: Provides the drone with its global position and allows for autonomous navigation and waypoint following.
- Optical Flow: Uses a downward-facing camera to measure the drone’s velocity and position relative to the ground.
4. Power Management
Power management is a critical aspect of any custom drone board, as it ensures that all of the components receive the necessary power to function properly. The power management system typically consists of several components:
- Battery: Provides the energy to power the drone’s motors, sensors, and other components. Lithium-polymer (LiPo) batteries are the most common type used in drones due to their high energy density and discharge rate.
- Power Distribution Board (PDB): Distributes power from the battery to the various components on the custom drone board, such as the flight controller, ESCs, and sensors.
- Voltage Regulator: Steps down the battery voltage to the appropriate level for the flight controller and other low-voltage components.
5. Communication Modules
Communication modules enable the custom drone board to communicate with the user’s remote control or ground station. The most common communication protocols used in drones are:
- Radio Frequency (RF): Uses a dedicated radio transmitter and receiver to send control signals and telemetry data between the drone and the user’s remote control.
- Wi-Fi: Allows the drone to connect to a Wi-Fi network and communicate with a ground station or mobile device using a web-based interface or mobile app.
- Bluetooth: Enables short-range communication between the drone and a mobile device for configuration and control purposes.
Designing a Custom Drone Board
Designing a custom drone board requires careful consideration of the drone’s intended purpose, size, and performance requirements. The first step in the design process is to select the appropriate components based on these factors.
Selecting the Right Components
When selecting components for a custom drone board, it’s important to consider the following factors:
- Size and weight: The components should be as small and lightweight as possible to minimize the drone’s overall weight and maximize its flight time.
- Power consumption: The components should be energy-efficient to maximize the drone’s battery life and flight time.
- Performance: The components should be powerful enough to meet the drone’s performance requirements, such as its maximum speed, payload capacity, and sensor capabilities.
- Compatibility: The components should be compatible with each other and with the drone’s software and communication protocols.
PCB Layout and Fabrication
Once the components have been selected, the next step is to design the PCB layout for the custom drone board. The PCB layout should be optimized for size, weight, and signal integrity, with careful consideration given to the placement of components and routing of traces.
After the PCB layout is complete, the board can be fabricated using a variety of methods, such as:
- In-house fabrication: For low-volume prototypes or small production runs, the PCB can be fabricated in-house using a desktop CNC machine or 3D printer.
- PCB fabrication service: For larger production runs or more complex designs, the PCB can be outsourced to a professional PCB fabrication service, which can provide higher-quality boards with tighter tolerances and faster turnaround times.
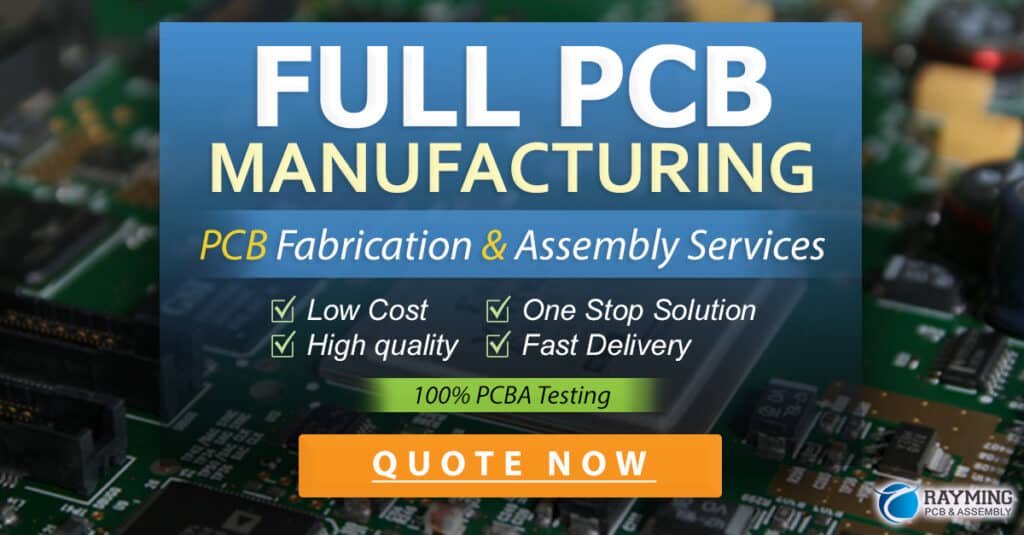
Assembling and Testing the Custom Drone Board
Once the PCB has been fabricated, the next step is to assemble the components onto the board and test the system to ensure that everything is working properly.
Component Placement and Soldering
The components should be carefully placed on the PCB according to the layout, with attention paid to the orientation and polarity of each component. The components can then be soldered onto the board using a variety of methods, such as:
- Hand soldering: For small batches or prototypes, the components can be soldered by hand using a soldering iron and solder wire.
- Reflow soldering: For larger production runs, the components can be soldered using a reflow oven, which melts the solder paste and bonds the components to the PCB in a controlled environment.
System Testing and Calibration
After the components have been soldered onto the board, the next step is to test the system to ensure that everything is working properly. This typically involves:
- Power-on test: Verifying that the board powers on and all of the components receive the necessary voltage and current.
- Sensor calibration: Calibrating the IMU, barometer, and other sensors to ensure accurate readings and stable flight.
- Motor test: Testing the motors and ESCs to ensure that they are spinning in the correct direction and responding properly to control inputs.
- Communication test: Verifying that the communication modules are functioning properly and able to send and receive data from the remote control or ground station.
Software Development
The final step in creating a custom drone board is to develop the software that will run on the flight controller and enable the drone to fly and perform its intended functions. This typically involves:
- Firmware development: Writing the low-level firmware that runs on the flight controller and interfaces with the sensors, motors, and communication modules.
- Middleware development: Developing higher-level software modules that provide additional functionality, such as autonomous navigation, object avoidance, or data logging.
- Ground station software: Creating a user interface for the ground station or mobile app that allows the user to monitor and control the drone remotely.
There are many open-source software platforms and libraries available for drone development, such as:
- ArduPilot: A popular open-source firmware for drones that supports a wide range of flight controllers and peripherals.
- PX4: Another open-source firmware that provides a flexible and modular architecture for drone development.
- DroneKit: A Python library that allows developers to create custom drone applications and interact with the drone’s sensors and actuators.
Conclusion
A custom drone board is a complex system that requires careful design, component selection, and software development to ensure optimal performance and reliability. By understanding the core components of a custom drone board and how they work together, developers can create drones that are tailored to their specific needs and applications.
As the drone industry continues to grow and evolve, we can expect to see even more advanced and specialized custom drone boards in the future, with new sensors, communication protocols, and software capabilities that enable drones to perform an ever-wider range of tasks and missions.
Frequently Asked Questions (FAQ)
- What is the difference between a flight controller and a microcontroller?
-
A flight controller is a specialized type of microcontroller that is designed specifically for use in drones and other unmanned aerial vehicles (UAVs). It typically includes additional features and peripherals that are optimized for flight control, such as IMUs, barometers, and GPS receivers. A microcontroller, on the other hand, is a more general-purpose device that can be used in a wide range of applications, including drones.
-
Can I use a regular ESC for a drone motor?
-
While it is possible to use a regular ESC for a drone motor, it is not recommended. Drone motors typically require higher current and more precise control than regular ESCs are designed for. Using a regular ESC in a drone can result in poor performance, overheating, and even damage to the motor or ESC. It is best to use an ESC that is specifically designed for use in drones and rated for the appropriate current and voltage of the motor.
-
What is the difference between an IMU and a barometer?
-
An IMU (Inertial Measurement Unit) is a sensor that measures the drone’s acceleration, rotation, and orientation in three-dimensional space. It typically consists of an accelerometer, gyroscope, and magnetometer. A barometer, on the other hand, is a sensor that measures the drone’s altitude by detecting changes in air pressure. Both sensors are essential for stable flight and accurate positioning of the drone.
-
What is the best battery type for a custom drone board?
-
Lithium-polymer (LiPo) batteries are the most common type used in drones due to their high energy density, high discharge rate, and lightweight. They are available in a range of capacities and voltages to suit different drone sizes and power requirements. However, LiPo batteries can be dangerous if not handled properly, as they are prone to overheating, swelling, and even catching fire if damaged or overcharged. It is important to use a compatible charger and follow proper safety guidelines when using LiPo batteries in a custom drone board.
-
Can I use Wi-Fi for long-range drone communication?
- While Wi-Fi can be used for short-range communication between a drone and a ground station or mobile device, it is not suitable for long-range communication due to its limited range and susceptibility to interference. For long-range drone communication, it is better to use a dedicated radio frequency (RF) link, such as a 900 MHz or 2.4 GHz transmitter and receiver. These RF links provide a more reliable and longer-range communication channel that is less affected by obstacles and interference.
No responses yet