Introduction to Solder Mask
Solder mask, also known as solder resist or solder stop, is a thin layer of polymer applied to the copper traces of a printed circuit board (PCB) to protect them from oxidation, prevent solder bridges, and provide electrical insulation. It is an essential component in the manufacturing of PCBs, ensuring the reliability and functionality of electronic devices.
What is a Printed Circuit Board (PCB)?
A printed circuit board is a flat board made of insulating material, such as fiberglass or composite epoxy, with conductive copper traces etched onto its surface. These traces connect various electronic components, such as resistors, capacitors, and integrated circuits, to form a complete electrical circuit. PCBs are used in virtually all electronic devices, from smartphones and computers to industrial equipment and medical devices.
The Role of Solder Mask in PCB Manufacturing
Solder mask plays a crucial role in the manufacturing process of PCBs. Its primary functions include:
-
Protection: Solder mask protects the copper traces from oxidation, corrosion, and physical damage during the assembly process and throughout the lifespan of the electronic device.
-
Insulation: The solder mask layer provides electrical insulation between adjacent copper traces, preventing short circuits and ensuring proper electrical connectivity.
-
Solder Control: Solder mask defines the areas where solder can be applied during the soldering process. It prevents solder bridges from forming between closely spaced traces, which can cause short circuits and lead to device failure.
-
Aesthetics: Solder mask can be applied in various colors, with green being the most common. The colored solder mask enhances the visual appearance of the PCB and makes it easier to inspect for defects.
Types of Solder Mask
There are two main types of solder mask used in PCB manufacturing: liquid photoimageable solder mask (LPSM) and dry film solder mask (DFSM).
Liquid Photoimageable Solder Mask (LPSM)
LPSM is the most widely used type of solder mask in the PCB industry. It is a liquid polymer that is applied to the PCB surface using screen printing, curtain coating, or spraying techniques. The liquid solder mask is then exposed to ultraviolet (UV) light through a photomask, which hardens the exposed areas while leaving the unexposed areas in a liquid state. The unexposed areas are then removed using a chemical developer, revealing the copper traces that need to be soldered.
Advantages of LPSM include:
- High resolution and accuracy
- Excellent adhesion to the PCB surface
- Compatibility with fine-pitch components and high-density PCB Designs
- Availability in various colors and finishes (matte, glossy, or semi-glossy)
Disadvantages of LPSM include:
- Higher cost compared to DFSM
- Longer processing time due to the multiple steps involved (application, exposure, development, and curing)
- Potential for air bubbles or pinholes if not applied properly
Dry Film Solder Mask (DFSM)
DFSM is a solid photopolymer film that is laminated onto the PCB surface using heat and pressure. Like LPSM, it is exposed to UV light through a photomask, which crosslinks and hardens the exposed areas. The unexposed areas are then removed using a chemical developer.
Advantages of DFSM include:
- Lower cost compared to LPSM
- Faster processing time due to fewer steps involved (lamination, exposure, and development)
- Uniform thickness across the PCB surface
- Reduced risk of air bubbles or pinholes
Disadvantages of DFSM include:
- Lower resolution and accuracy compared to LPSM
- Limited compatibility with fine-pitch components and high-density PCB designs
- Potential for delamination or cracking if not applied properly
- Limited color options (typically green or blue)
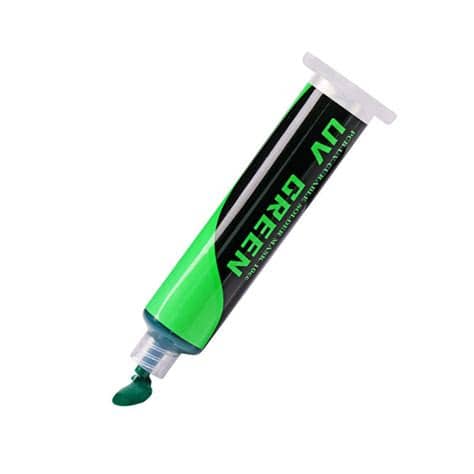
Solder Mask Application Process
The solder mask application process varies depending on the type of solder mask used (LPSM or DFSM) and the specific manufacturing requirements. However, the general steps involved in applying solder mask are as follows:
-
Surface Preparation: The PCB surface is cleaned and prepared to ensure proper adhesion of the solder mask. This may involve chemical cleaning, micro-etching, or plasma treatment.
-
Solder Mask Application: The solder mask is applied to the PCB surface using one of the following methods:
- Screen Printing (LPSM): A fine mesh screen is used to transfer the liquid solder mask onto the PCB surface.
- Curtain Coating (LPSM): The PCB is passed through a curtain of liquid solder mask, which coats the entire surface.
- Spraying (LPSM): The liquid solder mask is sprayed onto the PCB surface using a spray nozzle.
-
Lamination (DFSM): The dry film solder mask is laminated onto the PCB surface using heat and pressure.
-
Exposure: The solder mask-coated PCB is exposed to UV light through a photomask, which crosslinks and hardens the exposed areas. The photomask contains the desired pattern of the solder mask, with openings for the areas that need to be soldered (such as component pads and vias).
-
Development: The unexposed areas of the solder mask are removed using a chemical developer, revealing the copper traces that need to be soldered. The development process is carefully controlled to ensure complete removal of the unexposed solder mask without damaging the exposed areas.
-
Curing: The solder mask-coated PCB is heated to a specific temperature for a set duration to fully cure the solder mask. This process ensures that the solder mask achieves its final mechanical, electrical, and chemical properties.
-
Inspection: The solder mask-coated PCB is visually inspected for defects, such as pinholes, air bubbles, or incomplete coverage. Automated optical inspection (AOI) systems may be used to detect and analyze defects.
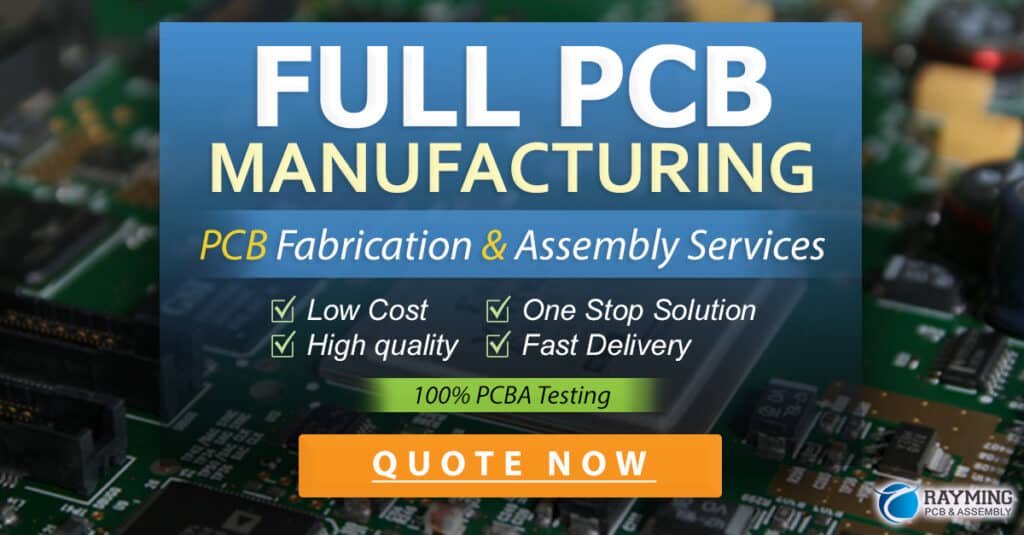
Solder Mask Properties and Specifications
Solder mask materials are designed to meet specific performance requirements to ensure the reliability and functionality of the PCB. Some of the key properties and specifications of solder mask include:
Electrical Properties
- Dielectric Strength: The ability of the solder mask to withstand high voltages without breaking down. Typical values range from 1000 to 1500 volts per mil (0.001 inch) of thickness.
- Insulation Resistance: The resistance of the solder mask to electrical current leakage. Typical values range from 10^12 to 10^14 ohms.
- Dielectric Constant: The ability of the solder mask to store electrical energy. Lower values (typically 3.0 to 4.0) are desirable for high-frequency applications.
Mechanical Properties
- Adhesion: The ability of the solder mask to adhere to the PCB surface. Adhesion is typically measured using a cross-hatch tape test (ASTM D3359) or a peel test (IPC-TM-650 2.4.28.1).
- Hardness: The resistance of the solder mask to indentation or penetration. Harder solder masks provide better protection against physical damage. Hardness is typically measured using the pencil hardness test (ASTM D3363).
- Flexibility: The ability of the solder mask to withstand bending or flexing without cracking or delaminating. Flexibility is essential for flexible PCBs and applications where the PCB may be subjected to mechanical stress.
Chemical Properties
- Chemical Resistance: The ability of the solder mask to withstand exposure to various chemicals, such as fluxes, cleaning agents, and solvents, without degradation. Chemical resistance is typically evaluated using a solvent resistance test (IPC-SM-840C).
- Flammability: The resistance of the solder mask to ignition and flame spread. Solder masks are typically rated according to the UL 94 flammability standard, with V-0 being the highest rating.
Environmental Properties
- Thermal Shock Resistance: The ability of the solder mask to withstand rapid changes in temperature without cracking or delaminating. Thermal shock resistance is typically evaluated using a thermal shock test (IPC-TM-650 2.6.7.1).
- Moisture Resistance: The ability of the solder mask to withstand exposure to high humidity without degradation. Moisture resistance is typically evaluated using a moisture resistance test (IPC-TM-650 2.6.2.1).
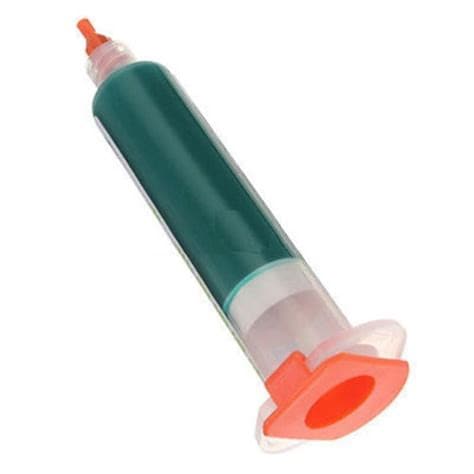
Solder Mask Color Options
Solder mask is available in a variety of colors, with green being the most common. Other popular color options include:
- Blue
- Red
- Yellow
- Black
- White
- Transparent (clear)
The choice of solder mask color is usually a matter of aesthetic preference or design requirements. However, there are some practical considerations:
- Green solder mask is the most widely used color due to its good contrast with copper traces and its compatibility with a wide range of component colors.
- Blue solder mask is often used for high-end or military-grade PCBs due to its perceived association with quality and reliability.
- Red, yellow, and black solder masks are sometimes used for PCBs in consumer electronics or for branding purposes.
- White solder mask is occasionally used for LED lighting applications to enhance light reflection and distribution.
- Transparent solder mask is used in some applications where the copper traces need to be visible for inspection or aesthetic reasons.
Solder Mask Finishes
In addition to color options, solder mask can be applied with different surface finishes to achieve specific properties or visual effects. Common solder mask finishes include:
- Matte: A non-glossy, textured finish that provides a smooth, even appearance and reduces glare. Matte finishes are the most common and are preferred for their ease of handling and inspection.
- Glossy: A shiny, reflective finish that enhances the visual appeal of the PCB. Glossy finishes are often used for consumer electronics or for branding purposes. However, they may be more prone to scratches and fingerprints.
- Semi-Glossy: A compromise between matte and glossy finishes, offering a moderate level of shine while maintaining good handling and inspection properties.
The choice of solder mask finish depends on the specific application requirements, such as visual appearance, ease of handling, and compatibility with automated inspection systems.
Solder Mask Design Considerations
When designing a PCB, there are several factors to consider regarding solder mask:
-
Solder Mask Clearance: The distance between the edge of a component pad or via and the edge of the solder mask opening. Adequate solder mask clearance is necessary to ensure proper solder joint formation and to prevent solder mask from interfering with the soldering process.
-
Solder Mask Expansion: The amount by which the solder mask opening is larger than the corresponding copper feature. Solder mask expansion compensates for potential misalignment during the solder mask application process and ensures that the copper features are fully exposed for soldering.
-
Solder Mask Sliver: The minimum width of a solder mask feature between two adjacent copper features. Solder mask slivers that are too narrow may be prone to cracking or delamination during the manufacturing process or in the field.
-
Solder Mask Dams: The use of solder mask to create barriers or dams between adjacent copper features to prevent solder bridging. Solder mask dams are especially important for fine-pitch components and high-density PCB designs.
-
Solder Mask Venting: The use of small openings or vents in the solder mask to allow trapped air or gases to escape during the soldering process. Solder mask venting helps to prevent void formation and ensures reliable solder joint formation.
PCB Designers must carefully consider these factors and work closely with the PCB manufacturer to ensure that the solder mask design meets the specific requirements of the application and the manufacturing process.
Frequently Asked Questions (FAQ)
1. What is the difference between solder mask and conformal coating?
Solder mask and conformal coating are both protective layers applied to PCBs, but they serve different purposes:
- Solder mask is applied before the soldering process and is used to define the areas where solder can be applied, prevent solder bridges, and provide electrical insulation between copper traces.
- Conformal coating is applied after the soldering process and is used to provide additional protection against moisture, dust, chemicals, and other environmental factors. Conformal coating covers the entire PCB surface, including components and solder joints.
2. Can solder mask be removed or reworked after application?
Yes, solder mask can be removed or reworked after application, but it requires specialized equipment and processes. Solder mask removal may be necessary for PCB repair, modification, or failure analysis. Common methods for solder mask removal include:
- Mechanical abrasion (sanding or grinding)
- Chemical stripping (using solvents or stripping agents)
- Laser ablation (using high-energy lasers to vaporize the solder mask)
After removing the solder mask, the PCB surface must be cleaned and prepared before applying new solder mask or performing other rework operations.
3. What is the typical thickness of solder mask?
The typical thickness of solder mask ranges from 0.0005 to 0.002 inches (12.7 to 50.8 microns). The specific thickness depends on the type of solder mask (LPSM or DFSM), the application method, and the performance requirements of the PCB.
- LPSM typically has a thickness of 0.0005 to 0.001 inches (12.7 to 25.4 microns) when applied using screen printing or curtain coating methods.
- DFSM typically has a thickness of 0.001 to 0.002 inches (25.4 to 50.8 microns) when applied using lamination methods.
Thicker solder masks provide better insulation and protection against physical damage, but they may be more prone to cracking or delamination. Thinner solder masks allow for finer feature resolution and are better suited for high-density PCB designs.
4. Can solder mask be used on flexible PCBs?
Yes, solder mask can be used on flexible PCBs, but it requires special considerations and materials. Flexible solder masks must be able to withstand repeated bending and flexing without cracking or delaminating. They must also be compatible with the flexible PCB substrate material (such as polyimide or polyester) and the specific application requirements.
Common flexible solder mask materials include:
- Polyimide-based solder masks: Offer excellent flexibility, thermal stability, and chemical resistance. They are typically applied using screen printing or curtain coating methods.
- Acrylic-based solder masks: Offer good flexibility and adhesion to flexible substrates. They are typically applied using screen printing or spray coating methods.
Flexible solder masks may have lower thickness and higher elasticity compared to rigid solder masks to accommodate the bending and flexing of the PCB.
5. What are the environmental and health concerns associated with solder mask?
Solder mask materials may contain hazardous chemicals and substances that can pose environmental and health risks if not handled properly. Some of the concerns associated with solder mask include:
- Volatile Organic Compounds (VOCs): Some solder mask formulations contain VOCs, which can contribute to air pollution and may be harmful to human health if inhaled.
- Heavy Metals: Some solder mask formulations may contain heavy metals, such as lead or cadmium, which can be toxic to humans and the environment if released into the air, water, or soil.
- Skin and Eye Irritation: Direct contact with solder mask materials can cause skin and eye irritation. Proper personal protective equipment (PPE), such as gloves and safety glasses, should be used when handling solder mask.
- Disposal and Recycling: Solder mask waste, including unused materials and contaminated cleaning agents, must be properly disposed of or recycled to prevent environmental contamination.
PCB manufacturers and designers must be aware of these concerns and take appropriate measures to minimize the environmental and health risks associated with solder mask. This may involve using eco-friendly or low-VOC solder mask formulations, implementing proper ventilation and waste management systems, and providing appropriate training and PPE for personnel handling solder mask.
Conclusion
Solder mask is a critical component in the manufacturing of PCBs, providing electrical insulation, protection against oxidation and physical damage, and defining the areas where solder can be applied. The choice of solder mask type (LPSM or DFSM), color, finish, and design parameters depends on the specific application requirements and manufacturing constraints.
As PCB technology continues to advance, with increasing complexity and miniaturization, the role of solder mask in ensuring the reliability and functionality of electronic devices becomes even more important. PCB designers and manufacturers must stay up-to-date with the latest solder mask materials, processes, and design guidelines to meet the evolving demands of the electronics industry.
By understanding the properties, applications, and design considerations of solder mask, PCB professionals can make informed decisions that optimize the performance, reliability, and cost-effectiveness of their products. As the electronics industry continues to grow and innovate, solder mask will remain an essential element in the production of high-quality, reliable PCBs.
No responses yet