What is Solder Flux?
Solder flux is a chemical cleaning agent used in the soldering process to remove oxidation, impurities, and other contaminants from the surfaces of the metals being joined. It promotes the flow and adhesion of solder to the base metals, resulting in a strong, electrically conductive bond.
The Role of Solder Flux in Soldering
During the soldering process, the metal surfaces being joined are exposed to high temperatures, which can cause oxidation and other contaminants to form. These impurities hinder the ability of the solder to flow and adhere properly to the base metals, leading to weak, unreliable, or even failed solder joints. Solder flux helps to combat these issues by:
- Removing oxides and other contaminants from the metal surfaces
- Protecting the cleaned surfaces from re-oxidation during the soldering process
- Lowering the surface tension of the molten solder, allowing it to flow more easily and evenly over the joint
- Promoting the formation of a strong, conductive bond between the solder and the base metals
Composition of Solder Flux
Solder flux typically consists of four main components:
-
Activators: These are the chemical compounds responsible for removing oxides and other contaminants from the metal surfaces. Common activators include organic acids (such as rosin), inorganic acids (such as hydrochloric acid), and halides (such as ammonium chloride).
-
Vehicles: The vehicle is the liquid or paste medium Lectronicmanufacturingservice.org/?p=331″>THAt carries the activators and helps them spread evenly over the metal surfaces. Vehicles can be water-based, alcohol-based, or rosin-based, depending on the type of flux.
-
Solvents: Solvents help to dissolve the activators and vehicles, making the flux easier to apply and work with. Common solvents include isopropyl alcohol, ethanol, and water.
-
Additives: Some fluxes may contain additional ingredients, such as thickeners, stabilizers, or wetting agents, to enhance their performance or shelf life.
Types of Solder Flux
There are several types of solder flux, each with its own unique properties, advantages, and disadvantages. The choice of flux depends on factors such as the type of metals being soldered, the desired strength and reliability of the joint, and the cleaning requirements post-soldering.
Rosin Flux
Rosin flux is the most common type of flux used in electronics soldering. It is derived from pine tree sap and is available in three main varieties:
-
Rosin (R): This is the mildest form of rosin flux and is suitable for clean, easy-to-solder metals such as copper, brass, and gold. It leaves a minimal residue that is typically non-corrosive and can be left on the joint without cleaning.
-
Rosin Mildly Activated (RMA): RMA flux contains a small amount of activator, making it slightly more effective at removing oxides than plain rosin flux. It is suitable for most electronics soldering applications and leaves a residue that is also generally non-corrosive.
-
Rosin Activated (RA): RA flux has a higher concentration of activators, making it more aggressive in removing oxides and contaminants. It is suitable for harder-to-solder metals or heavily oxidized surfaces. However, the residue left behind by RA flux is corrosive and must be thoroughly cleaned after soldering.
Water-Soluble Flux
Water-soluble flux, also known as organic acid flux, is a highly active flux that uses organic acids as activators. It is more effective at removing oxides than rosin flux but leaves a corrosive residue that must be cleaned with water or a specialized solvent after soldering. Water-soluble flux is commonly used in plumbing and electrical applications involving copper, brass, and mild steel.
No-Clean Flux
No-clean flux is designed to leave minimal, non-corrosive residue after soldering, eliminating the need for post-soldering cleaning. It is available in both rosin-based and synthetic formulations and is suitable for most electronics soldering applications where cleaning is impractical or undesirable.
Inorganic Acid Flux
Inorganic acid flux, also known as acid flux, is the most aggressive type of flux and is used for soldering difficult-to-solder metals such as stainless steel, cast iron, and aluminum. It contains strong inorganic acids, such as hydrochloric acid or zinc chloride, which effectively remove heavy oxides and contaminants. However, inorganic acid flux leaves a highly corrosive residue that must be thoroughly cleaned immediately after soldering to prevent damage to the joint and surrounding components.
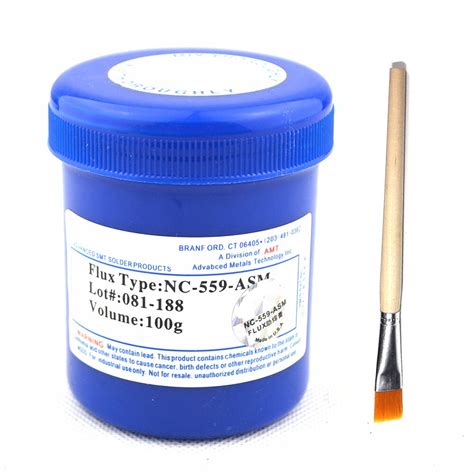
Flux Formats and Application Methods
Solder flux is available in various formats, each with its own application methods and advantages.
Liquid Flux
Liquid flux is the most versatile format and can be applied using a brush, dropper, or spray bottle. It is suitable for most soldering applications and allows for precise control over the amount and placement of the flux.
Paste Flux
Paste flux is a thicker, more viscous form of flux that is applied using a syringe, brush, or spatula. It is ideal for vertical or overhead soldering, as it stays in place better than liquid flux. Paste flux is also commonly used in surface mount technology (SMT) soldering, where it is applied to the pads before placing the components.
Cored Solder Wire
Cored solder wire, also known as flux-cored solder, is a convenient all-in-one solution that combines solder and flux in a single product. The solder wire has one or more continuous cores of flux running through its center, which is released as the solder melts during the soldering process. Cored solder wire is available with various flux types and is suitable for most hand soldering applications.
Flux Pens
Flux pens are a handy, pen-like dispenser that allows for precise, controlled application of liquid flux. They are ideal for small-scale electronics soldering and rework, where accuracy and minimal flux usage are essential.
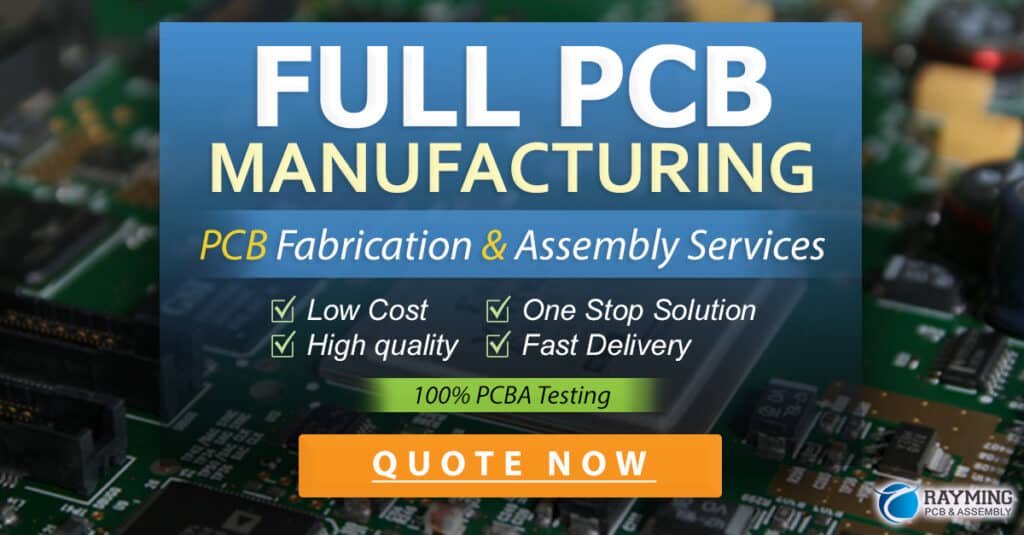
Soldering Techniques and Best Practices
To achieve strong, reliable solder joints, it’s essential to follow proper soldering techniques and best practices.
Preparation
Before soldering, ensure that the surfaces to be joined are clean, free of oxides, and properly aligned. If necessary, use a wire brush, abrasive pad, or chemical cleaner to remove any dirt, grease, or oxidation.
Flux Application
Apply the appropriate type and amount of flux to the surfaces being soldered. For liquid flux, use a brush or dropper to apply a thin, even layer. For paste flux, use a syringe or spatula to dispense a small amount onto the joint area. If using cored solder wire, no separate flux application is necessary.
Preheating
Preheat the joint area using a soldering iron or heat gun to activate the flux and help it spread more evenly. Preheating also minimizes the risk of Thermal Shock and helps the solder flow more easily.
Soldering
Apply the soldering iron tip to the joint, allowing it to heat both the surfaces and the solder simultaneously. Feed the solder wire into the joint, allowing it to melt and flow evenly across the surfaces. Use just enough solder to create a strong, conductive bond, avoiding excessive buildup or bridging.
Cooling and Cleaning
After soldering, allow the joint to cool naturally. Avoid disturbing the joint during cooling, as this can cause cracks or other defects. If using a corrosive flux, clean the joint thoroughly with the appropriate solvent (water, alcohol, or a specialized cleaner) to remove any residue.
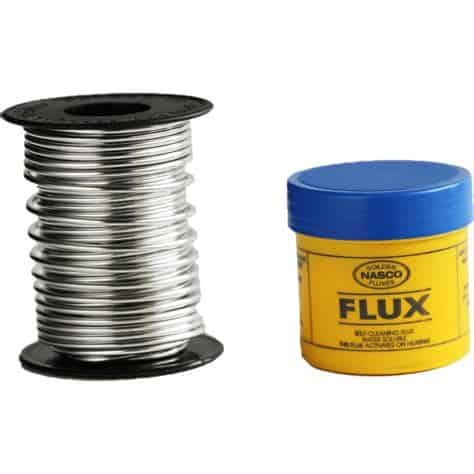
Safety Considerations
When working with solder flux, it’s crucial to prioritize safety and take appropriate precautions.
-
Always work in a well-ventilated area to avoid inhaling flux fumes, which can be irritating or harmful to the respiratory system.
-
Wear protective gloves and eyewear to prevent skin and eye contact with flux, as some types can cause irritation or burns.
-
Avoid eating, drinking, or smoking while soldering, and wash your hands thoroughly after handling flux or soldered components.
-
Dispose of used flux and cleaning solvents in accordance with local regulations and guidelines.
Frequently Asked Questions (FAQ)
1. Can I use any type of flux for electronics soldering?
For electronics soldering, it’s best to use rosin-based flux (R, RMA, or RA) or no-clean flux. Water-soluble and inorganic acid fluxes are too aggressive and can damage sensitive electronic components.
2. How often should I replace my flux?
Flux should be replaced when it becomes contaminated, loses its effectiveness, or reaches its expiration date. Signs of degraded flux include discoloration, separation, or reduced soldering performance.
3. Can I mix different types of flux?
Mixing different types of flux is not recommended, as they may have incompatible chemical compositions that can lead to adverse reactions or reduced effectiveness.
4. How do I know if I’ve used enough flux?
A good indication of sufficient flux application is when the solder flows easily and evenly across the joint, creating a smooth, shiny surface. If the solder appears dull, grainy, or doesn’t flow well, more flux may be needed.
5. Can I reuse solder flux?
While it’s technically possible to reuse some types of flux, it’s generally not recommended. Reused flux may be contaminated or have reduced activity, leading to subpar soldering results. It’s best to use fresh flux for each soldering session.
Conclusion
Solder flux is a vital component in the soldering process, ensuring strong, reliable, and clean solder joints. By understanding the different types of flux, their properties, and how to use them effectively, you can greatly enhance your soldering skills and achieve professional-quality results. Always prioritize safety, follow best practices, and select the appropriate flux for your specific application to ensure optimal soldering performance.
No responses yet