What is an Outer Annular Ring?
An Outer Annular Ring is a circular component that is typically installed around a rotating shaft or bearing. It is designed to provide a smooth, low-friction surface for the shaft or bearing to rotate against, thus reducing wear and tear on the system. OARs are usually made from high-quality materials such as steel, bronze, or ceramic, depending on the specific application and operating conditions.
Key Features of Outer Annular Rings
- Precision manufacturing: OARs are manufactured to tight tolerances to ensure a perfect fit and optimal performance.
- Durability: Made from high-quality materials, OARs are designed to withstand harsh operating conditions and provide long-lasting service.
- Low friction: The smooth surface of an OAR minimizes friction, reducing energy loss and heat generation in the system.
- Customizable: OARs can be customized to suit specific applications, with variations in size, material, and surface finish.
Applications of Outer Annular Rings
Outer Annular Rings find applications in various industries, including:
Aerospace Industry
In the aerospace industry, OARs are used in a variety of components, such as:
- Jet engine bearings: OARs provide a smooth, low-friction surface for jet engine bearings, ensuring efficient operation and reduced wear.
- Helicopter rotor systems: OARs are used in helicopter rotor systems to minimize friction and vibration, enhancing the overall performance and stability of the aircraft.
- Satellite positioning systems: High-precision OARs are used in satellite positioning systems to ensure accurate and reliable operation.
Automotive Industry
OARs are widely used in the automotive industry, particularly in:
- Wheel bearings: OARs provide a smooth, low-friction surface for wheel bearings, reducing wear and ensuring smooth rotation of the wheels.
- Transmission systems: OARs are used in automotive transmission systems to minimize friction and ensure efficient power transfer.
- Engine components: OARs are found in various engine components, such as crankshafts and camshafts, to reduce friction and enhance engine performance.
Industrial Machinery
In industrial machinery, OARs are used in:
- Pumps and compressors: OARs are used in pumps and compressors to minimize friction and ensure efficient operation.
- Turbines: OARs are used in turbines to provide a smooth, low-friction surface for the rotating components, enhancing efficiency and reducing wear.
- Machine tools: High-precision OARs are used in machine tools, such as lathes and milling machines, to ensure accurate and reliable operation.
Advantages of Outer Annular Rings
The use of Outer Annular Rings offers several advantages, including:
- Reduced friction: The smooth surface of an OAR minimizes friction, reducing energy loss and heat generation in the system.
- Enhanced efficiency: By reducing friction, OARs contribute to improved system efficiency, leading to energy savings and reduced operating costs.
- Increased component life: The low-friction environment provided by OARs reduces wear on the rotating components, extending their service life.
- Improved performance: OARs enhance the overall performance of mechanical systems by ensuring smooth, reliable operation.
- Reduced maintenance: The use of high-quality OARs minimizes the need for frequent maintenance, reducing downtime and associated costs.
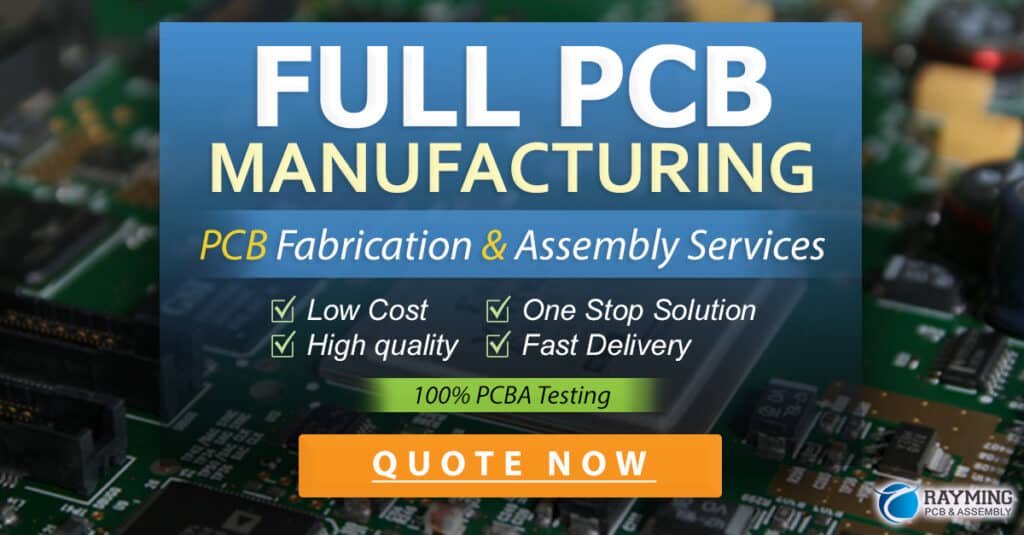
Maintenance of Outer Annular Rings
To ensure optimal performance and longevity of Outer Annular Rings, regular maintenance is essential. Some key maintenance practices include:
- Lubrication: Regular lubrication of OARs is crucial to maintain a low-friction environment and prevent premature wear.
- Inspection: Periodic inspection of OARs for signs of wear, damage, or contamination is essential to identify potential issues before they lead to system failure.
- Cleaning: Regular cleaning of OARs to remove dirt, debris, and contaminants helps maintain their smooth surface and optimal performance.
- Replacement: When an OAR reaches the end of its service life or shows signs of excessive wear, it should be replaced to ensure the continued reliable operation of the system.
Frequently Asked Questions (FAQ)
-
Q: What materials are Outer Annular Rings typically made from?
A: Outer Annular Rings are typically made from high-quality materials such as steel, bronze, or ceramic, depending on the specific application and operating conditions. -
Q: How do Outer Annular Rings reduce friction in mechanical systems?
A: OARs provide a smooth, low-friction surface for rotating components to move against, minimizing friction and ensuring efficient operation. -
Q: Are Outer Annular Rings used in the aerospace industry?
A: Yes, OARs are widely used in the aerospace industry, particularly in jet engine bearings, helicopter rotor systems, and satellite positioning systems. -
Q: What are the advantages of using Outer Annular Rings in mechanical systems?
A: The advantages of using OARs include reduced friction, enhanced efficiency, increased component life, improved performance, and reduced maintenance requirements. -
Q: How often should Outer Annular Rings be replaced?
A: The replacement frequency of OARs depends on various factors, such as the specific application, operating conditions, and the level of wear. Regular inspection and monitoring can help determine when an OAR needs to be replaced.
Conclusion
Outer Annular Rings are critical components in various mechanical systems, providing a smooth, low-friction surface for rotating components. They play a vital role in reducing wear, enhancing efficiency, and improving the overall performance of machinery. With applications spanning across the aerospace, automotive, and industrial sectors, OARs are essential for ensuring the reliable and efficient operation of a wide range of equipment.
By understanding the key features, applications, advantages, and maintenance requirements of Outer Annular Rings, engineers and technicians can make informed decisions when designing, operating, and maintaining mechanical systems. As technology continues to advance, the development of new materials and manufacturing techniques is expected to further enhance the performance and durability of OARs, making them an indispensable component in modern machinery.
No responses yet