Introduction to Motor Drivers
A motor driver is an electronic circuit or device that enables the control and operation of electric motors. It acts as an interface between the motor and the control system, such as a microcontroller or computer. Motor drivers are essential components in various applications, including robotics, automation, and consumer electronics.
Types of Motors
Before diving into motor drivers, let’s briefly discuss the different types of motors commonly used:
- DC Motors
- Brushed DC Motors
- Brushless DC Motors (BLDC)
- Stepper Motors
- Servo Motors
Each type of motor has its own characteristics and requires specific control methods.
How Motor Drivers Work
Motor drivers work by taking low-power control signals from a microcontroller or computer and converting them into high-power signals that can drive the motor. They typically consist of power electronics components such as transistors, MOSFETs, or H-bridges.
Basic Functions of a Motor Driver
- Power Amplification
-
Motor drivers amplify the low-power control signals to provide sufficient current and voltage to drive the motor.
-
Direction Control
-
Motor drivers allow the direction of rotation to be controlled by providing the appropriate signals to the motor windings.
-
Speed Control
-
By varying the voltage or pulse width modulation (PWM) signal, motor drivers can control the speed of the motor.
-
Protection Features
- Motor drivers often include protection features such as over-current, over-voltage, and thermal protection to safeguard the motor and the driver itself.
Types of Motor Drivers
There are several types of motor drivers available, each designed for specific motor types and applications.
1. H-Bridge Motor Drivers
H-bridge motor drivers are commonly used for controlling DC motors. They consist of four switches arranged in an H-shaped configuration. By turning on and off specific switches, the direction of current flow through the motor can be reversed, allowing for bidirectional control.
Examples of H-bridge motor drivers include:
– L293D
– L298N
– TB6612FNG
2. Brushless DC (BLDC) Motor Drivers
BLDC motor drivers are specifically designed to control brushless DC motors. These drivers typically incorporate a three-phase inverter to generate the required commutation sequence for the motor windings.
Examples of BLDC motor drivers include:
– A4960
– DRV8313
– MC33035
3. Stepper Motor Drivers
Stepper motor drivers are used to control stepper motors, which require precise positioning and speed control. These drivers generate the necessary pulse sequences to energize the motor windings in a specific order, causing the motor to rotate in discrete steps.
Examples of stepper motor drivers include:
– A4988
– DRV8825
– TB6600
4. Servo Motor Drivers
Servo motor drivers are designed to control servo motors, which are commonly used in robotics and radio-controlled applications. These drivers generate pulse width modulation (PWM) signals to control the position of the servo motor.
Examples of servo motor drivers include:
– PCA9685
– Adafruit 16-Channel 12-bit PWM/Servo Driver
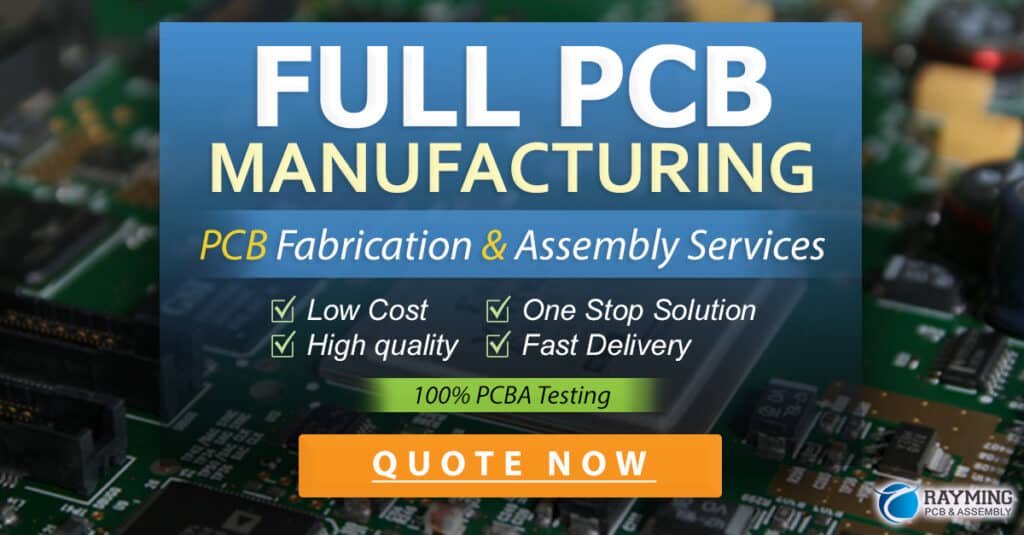
Choosing the Right Motor Driver
When selecting a motor driver for your application, consider the following factors:
- Motor Type
-
Ensure that the motor driver is compatible with the type of motor you are using (DC, BLDC, stepper, or servo).
-
Voltage and Current Requirements
-
Choose a motor driver that can handle the voltage and current requirements of your motor. Consider the maximum voltage and continuous current ratings of both the motor and the driver.
-
Control Interface
-
Consider the control interface required by your system. Some motor drivers accept simple digital signals, while others may require more advanced communication protocols like I2C or SPI.
-
Additional Features
- Look for motor drivers with additional features that may be beneficial for your application, such as built-in current sensing, fault protection, or microstepping capabilities for stepper motors.
Interfacing Motor Drivers with Microcontrollers
To control a motor using a motor driver, you need to interface it with a microcontroller or computer. The specific connections and programming requirements depend on the motor driver and microcontroller you are using.
Basic Connection Example
Here’s a basic connection example using an Arduino microcontroller and an L298N motor driver to control a DC motor:
Arduino L298N Motor Driver
-------------- -------------------
Digital Pin 2 -> IN1
Digital Pin 3 -> IN2
Digital Pin 4 -> IN3
Digital Pin 5 -> IN4
GND -> GND
5V -> +5V
L298N Motor Driver DC Motor
------------------- ---------
OUT1 -> Motor Terminal 1
OUT2 -> Motor Terminal 2
OUT3 -> Motor Terminal 3
OUT4 -> Motor Terminal 4
+12V -> +12V Power Supply
GND -> Power Supply Ground
Programming Example
Here’s a simple Arduino sketch that demonstrates how to control a DC motor using the L298N motor driver:
const int in1Pin = 2;
const int in2Pin = 3;
const int in3Pin = 4;
const int in4Pin = 5;
void setup() {
pinMode(in1Pin, OUTPUT);
pinMode(in2Pin, OUTPUT);
pinMode(in3Pin, OUTPUT);
pinMode(in4Pin, OUTPUT);
}
void loop() {
// Rotate motor clockwise
digitalWrite(in1Pin, HIGH);
digitalWrite(in2Pin, LOW);
digitalWrite(in3Pin, HIGH);
digitalWrite(in4Pin, LOW);
delay(2000);
// Stop motor
digitalWrite(in1Pin, LOW);
digitalWrite(in2Pin, LOW);
digitalWrite(in3Pin, LOW);
digitalWrite(in4Pin, LOW);
delay(1000);
// Rotate motor counterclockwise
digitalWrite(in1Pin, LOW);
digitalWrite(in2Pin, HIGH);
digitalWrite(in3Pin, LOW);
digitalWrite(in4Pin, HIGH);
delay(2000);
// Stop motor
digitalWrite(in1Pin, LOW);
digitalWrite(in2Pin, LOW);
digitalWrite(in3Pin, LOW);
digitalWrite(in4Pin, LOW);
delay(1000);
}
This example demonstrates basic motor control by rotating the motor clockwise, stopping it, rotating it counterclockwise, and stopping it again in a continuous loop.
Advanced Motor Control Techniques
Beyond basic motor control, there are several advanced techniques that can be implemented using motor drivers:
- PWM Speed Control
-
By applying pulse width modulation (PWM) signals to the motor driver inputs, you can control the speed of the motor. Varying the duty cycle of the PWM signal allows for smooth speed control.
-
PID Control
-
Proportional-Integral-Derivative (PID) control is a feedback control algorithm commonly used for precise motor position or speed control. It involves measuring the actual motor position or speed and adjusting the control signals accordingly.
-
Microstepping (for Stepper Motors)
-
Microstepping is a technique used with stepper motors to achieve higher resolution and smoother motion. It involves dividing each full step into smaller microsteps by precisely controlling the current in the motor windings.
-
Closed-Loop Control
- Closed-loop control involves using sensors, such as encoders or Hall Effect Sensors, to provide feedback about the motor’s position or speed. This feedback is used to make real-time adjustments to the motor control signals for improved accuracy and performance.
Motor Driver Applications
Motor drivers find applications in a wide range of fields, including:
- Robotics
-
Motor drivers are extensively used in robotics to control the motion of various actuators, such as wheels, joints, and grippers.
-
CNC Machines
-
In computer numerical control (CNC) machines, motor drivers are used to precisely control the movement of the machine axes for tasks like milling, drilling, and cutting.
-
3D Printers
-
Motor drivers are essential components in 3D printers, controlling the movement of the print head and the extruder motor.
-
Automotive Systems
-
In automotive applications, motor drivers are used for various purposes, such as controlling windshield wipers, power windows, and electric power steering.
-
Home Automation
- Motor drivers are used in home automation systems to control motorized blinds, curtains, and other automated fixtures.
Frequently Asked Questions (FAQ)
-
Q: Can I use any motor driver with any type of motor?
A: No, motor drivers are designed for specific types of motors. You need to choose a motor driver that is compatible with the type of motor you are using (DC, BLDC, stepper, or servo). -
Q: How do I determine the current rating required for my motor driver?
A: The current rating of the motor driver should be higher than the maximum current draw of your motor. Refer to the motor’s specifications to determine its rated current and choose a motor driver that can handle that current with some headroom. -
Q: Can I control multiple motors with a single motor driver?
A: It depends on the motor driver. Some motor drivers, like the L298N, have multiple channels and can control multiple motors independently. However, other motor drivers may be designed for controlling a single motor. -
Q: How can I control the speed of a DC motor using a motor driver?
A: You can control the speed of a DC motor by applying pulse width modulation (PWM) signals to the motor driver inputs. By varying the duty cycle of the PWM signal, you can adjust the average voltage supplied to the motor, effectively controlling its speed. -
Q: What is microstepping, and why is it used with stepper motors?
A: Microstepping is a technique used to divide each full step of a stepper motor into smaller microsteps. It allows for higher resolution and smoother motion by precisely controlling the current in the motor windings. Microstepping is commonly used in applications that require precise positioning, such as 3D printers and CNC machines.
Conclusion
Motor drivers are essential components in various applications that involve controlling and driving electric motors. They act as an interface between the low-power control signals from a microcontroller or computer and the high-power requirements of the motor.
Understanding the different types of motor drivers, their working principles, and how to choose the right one for your application is crucial for successful motor control projects. By interfacing motor drivers with microcontrollers and implementing advanced control techniques, you can achieve precise and efficient motor control in a wide range of applications.
Remember to consider factors such as motor type, voltage and current requirements, control interface, and additional features when selecting a motor driver. With the right motor driver and proper implementation, you can bring your motor control projects to life.
No responses yet