Understanding IoT in Manufacturing
Definition and Key Components
IoT in manufacturing involves the deployment of connected devices, sensors, and software applications to collect, analyze, and exchange data in real-time. The key components of an IoT Manufacturing system include:
- Connected Devices: Machines, equipment, and tools equipped with sensors and communication capabilities.
- Sensors: Devices that collect data on various parameters such as temperature, pressure, vibration, and humidity.
- Network Infrastructure: Wired or wireless networks that enable data transmission between connected devices and the cloud.
- Cloud Computing: Platforms that store, process, and analyze the collected data.
- Analytics and Visualization Tools: Software applications that convert raw data into actionable insights and present them in a user-friendly format.
Benefits of IoT in Manufacturing
Implementing IoT in manufacturing offers numerous benefits, including:
- Increased Efficiency: Real-time data collection and analysis enable manufacturers to identify bottlenecks, optimize processes, and reduce waste.
- Predictive Maintenance: IoT sensors can detect potential equipment failures before they occur, allowing for proactive maintenance and minimizing downtime.
- Enhanced Product Quality: Continuous monitoring of production processes ensures consistent product quality and helps identify and address quality issues promptly.
- Improved Safety: Connected devices can monitor and alert operators about potential safety hazards, reducing the risk of accidents and injuries.
- Cost Savings: Optimized processes, reduced downtime, and improved resource utilization lead to significant cost savings for manufacturers.
Applications of IoT in Manufacturing
Asset Tracking and Management
IoT-enabled asset tracking allows manufacturers to monitor the location, status, and performance of their equipment, tools, and inventory in real-time. This helps optimize asset utilization, prevent theft or loss, and streamline maintenance schedules.
Predictive Maintenance
By analyzing data from IoT sensors, manufacturers can predict when equipment is likely to fail and schedule maintenance accordingly. This approach reduces unplanned downtime, extends equipment lifespan, and minimizes repair costs.
Quality Control and Inspection
IoT devices can monitor production processes and product quality in real-time, identifying defects or deviations from specifications. This enables manufacturers to take corrective actions promptly, reducing scrap and rework.
Energy Management
IoT sensors can monitor energy consumption across the manufacturing facility, identifying areas of inefficiency and optimizing energy usage. This leads to reduced energy costs and supports sustainability initiatives.
Supply Chain Optimization
IoT technology can track raw materials, work-in-progress, and finished goods throughout the supply chain. This visibility enables manufacturers to optimize inventory levels, streamline logistics, and improve responsiveness to customer demands.
Implementing IoT in Manufacturing
Challenges and Considerations
While IoT offers significant benefits, implementing it in manufacturing comes with its own set of challenges:
- Data Security and Privacy: Ensuring the security of sensitive data collected by IoT devices is crucial to prevent unauthorized access and protect intellectual property.
- Integration with Legacy Systems: Integrating IoT technology with existing manufacturing systems and processes can be complex and require significant investment.
- Skill Gap: Implementing and maintaining IoT systems requires specialized skills, which may be lacking among the existing workforce.
- Scalability and Interoperability: Ensuring that IoT solutions can scale as the manufacturing operation grows and that devices from different vendors can communicate seamlessly is essential.
Best Practices for Successful Implementation
To ensure a successful IoT implementation in manufacturing, consider the following best practices:
- Define Clear Objectives: Identify the specific business problems you want to solve with IoT and set measurable goals.
- Develop a Roadmap: Create a detailed plan outlining the steps, timelines, and resources required for implementation.
- Pilot Projects: Start with small-scale pilot projects to validate the technology and refine the implementation approach before scaling up.
- Invest in Security: Implement robust security measures to protect data and devices from cyber threats.
- Train and Upskill Workforce: Provide training and development opportunities to equip employees with the necessary skills to work with IoT technology.
Case Studies and Success Stories
Several manufacturing companies have successfully implemented IoT and achieved significant benefits. Here are a few examples:
Company | Application | Results |
---|---|---|
ABB | Predictive maintenance for robots | 70% reduction in robot downtime |
Bosch | Connected manufacturing for power tools | 25% increase in productivity and 50% reduction in inventory |
Ford | Real-time production monitoring | 50% reduction in production line stoppages |
Siemens | Energy management in manufacturing facilities | 20% reduction in energy consumption |
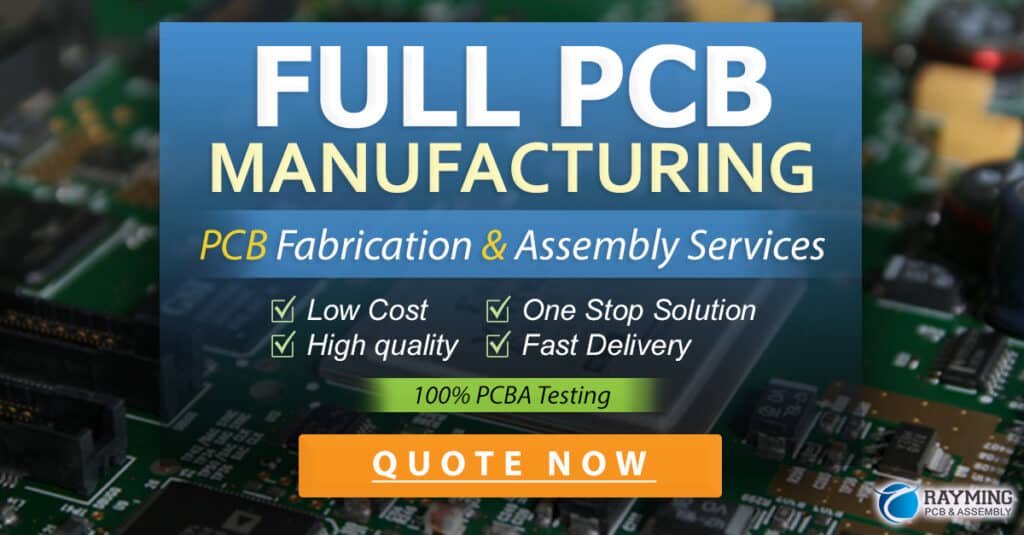
Future of IoT in Manufacturing
As IoT technology continues to evolve, we can expect to see even more innovative applications in manufacturing. Some of the emerging trends include:
- Edge Computing: Processing data closer to the source to reduce latency and improve real-time decision-making.
- Artificial Intelligence and Machine Learning: Leveraging AI and ML algorithms to analyze IoT data and optimize manufacturing processes.
- 5G Networks: Faster and more reliable wireless connectivity to support the growing number of connected devices in manufacturing.
- Digital Twins: Creating virtual replicas of physical assets to simulate and optimize their performance.
Frequently Asked Questions (FAQ)
-
What is the difference between IoT and IIoT?
IoT refers to the general concept of connected devices, while IIoT specifically focuses on the application of IoT in industrial settings, such as manufacturing. -
How much does it cost to implement IoT in manufacturing?
The cost of implementing IoT in manufacturing varies depending on the scale of the project, the complexity of the systems, and the specific technologies used. It can range from a few thousand dollars for small pilot projects to millions of dollars for large-scale implementations. -
What are the key challenges in implementing IoT in manufacturing?
The key challenges include data security and privacy, integration with legacy systems, skill gaps among the workforce, and ensuring scalability and interoperability of IoT solutions. -
How long does it take to see the benefits of IoT in manufacturing?
The time to realize the benefits of IoT in manufacturing depends on the scope of the project and the specific goals. Some benefits, such as improved visibility and real-time monitoring, can be achieved relatively quickly, while others, like predictive maintenance and process optimization, may take longer to materialize. -
What skills are required to work with IoT in manufacturing?
Working with IoT in manufacturing requires a combination of technical skills (e.g., data analytics, programming, and network management) and domain knowledge (e.g., manufacturing processes, equipment, and industry standards). Upskilling existing employees and hiring new talent with relevant expertise is essential for successful IoT implementation.
Conclusion
IoT in manufacturing has the potential to transform the industry, driving efficiency, quality, and innovation. By leveraging connected devices, sensors, and data analytics, manufacturers can optimize processes, reduce downtime, and improve product quality. However, successful implementation requires careful planning, investment in security and skill development, and a focus on achieving measurable business outcomes. As IoT technology continues to evolve, we can expect to see even more exciting applications and benefits in the manufacturing sector.
No responses yet