Introduction to Heavy Copper PCB
Heavy copper PCB, also known as thick copper PCB or high current PCB, is a type of printed circuit board that features thicker copper traces and planes compared to standard PCBs. The increased copper thickness allows heavy copper PCBs to handle higher currents, improve thermal management, and provide better mechanical stability. These characteristics make heavy copper PCBs ideal for applications that require high power handling, such as power electronics, automotive systems, and industrial equipment.
Copper Thickness in Heavy Copper PCBs
The copper thickness in heavy copper PCBs typically ranges from 3 oz/ft² to 20 oz/ft² (0.105 mm to 0.700 mm), while standard PCBs usually have copper thicknesses of 1 oz/ft² to 2 oz/ft² (0.035 mm to 0.070 mm). The table below compares the copper thicknesses in standard and heavy copper PCBs:
PCB Type | Copper Thickness (oz/ft²) | Copper Thickness (mm) |
---|---|---|
Standard PCB | 1 – 2 | 0.035 – 0.070 |
Heavy Copper PCB | 3 – 20 | 0.105 – 0.700 |
Advantages of Heavy Copper PCBs
- Higher current carrying capacity
- Improved thermal management
- Better mechanical stability
- Reduced resistance and voltage drop
- Enhanced signal integrity
Applications of Heavy Copper PCB
Power Electronics
Heavy copper PCBs are extensively used in power electronic applications, such as:
- Switch-mode power supplies (SMPS)
- Inverters and converters
- Uninterruptible power supplies (UPS)
- Motor drives and controllers
The thicker copper traces enable these PCBs to handle the high currents and power levels required in power electronic systems, while also providing better heat dissipation and thermal management.
Automotive Electronics
In the automotive industry, heavy copper PCBs are used in various applications, including:
- Electric vehicle (EV) battery management systems
- Engine control units (ECUs)
- Power distribution modules
- Charging systems
The increased copper thickness in heavy copper PCBs ensures reliable performance in the harsh operating conditions encountered in automotive environments, such as high temperatures, vibrations, and electrical noise.
Industrial Equipment
Heavy copper PCBs are also employed in industrial equipment that requires high power handling and reliability, such as:
- Welding machines
- CNC machines
- Robotics and automation systems
- High-power lighting systems
The robust construction and improved thermal management of heavy copper PCBs make them suitable for the demanding requirements of industrial applications.
Design Considerations for Heavy Copper PCB
Thermal Management
One of the primary considerations when designing heavy copper PCBs is thermal management. The thicker copper traces generate more heat compared to standard PCBs, necessitating proper heat dissipation techniques. Some strategies for effective thermal management in heavy copper PCBs include:
- Using thermal vias to transfer heat from the copper layers to the PCB surface
- Incorporating heat sinks or heat spreaders
- Optimizing the PCB layout to minimize heat generation and improve heat distribution
- Using thermally conductive materials, such as aluminum or copper-based substrates
Current Carrying Capacity
Designing heavy copper PCBs requires accurate calculation of the current carrying capacity of the copper traces. The current carrying capacity depends on factors such as:
- Copper thickness
- Trace width
- Ambient temperature
- Allowed temperature rise
The IPC-2152 standard provides guidelines for calculating the current carrying capacity of copper traces based on these factors. Designers can use online calculators or software tools to determine the appropriate trace widths for a given current requirement.
Mechanical Stability
The increased copper thickness in heavy copper PCBs also affects their mechanical stability. Thicker copper layers can cause warping or bowing of the PCB due to the difference in thermal expansion between the copper and the substrate material. To mitigate this issue, designers can:
- Use symmetrical layer stackups to balance the copper distribution
- Incorporate mechanical support features, such as stiffeners or anchor points
- Choose substrate materials with similar thermal expansion coefficients to copper
Manufacturing Considerations
Manufacturing heavy copper PCBs requires specialized equipment and processes compared to standard PCBs. Some key manufacturing considerations include:
- Plating: Thicker copper layers require longer plating times and may need multiple plating steps to achieve the desired thickness.
- Drilling: Drilling through thicker copper layers can be challenging and may require specialized drill bits and optimized drilling parameters.
- Etching: Etching thicker copper layers takes longer and may require adjustments to the etching process to ensure accurate trace formation.
- Soldering: Soldering components to heavy copper PCBs may require higher soldering temperatures and longer dwell times to ensure proper solder joint formation.
Working closely with the PCB manufacturer and providing detailed specifications can help ensure the successful fabrication of heavy copper PCBs.
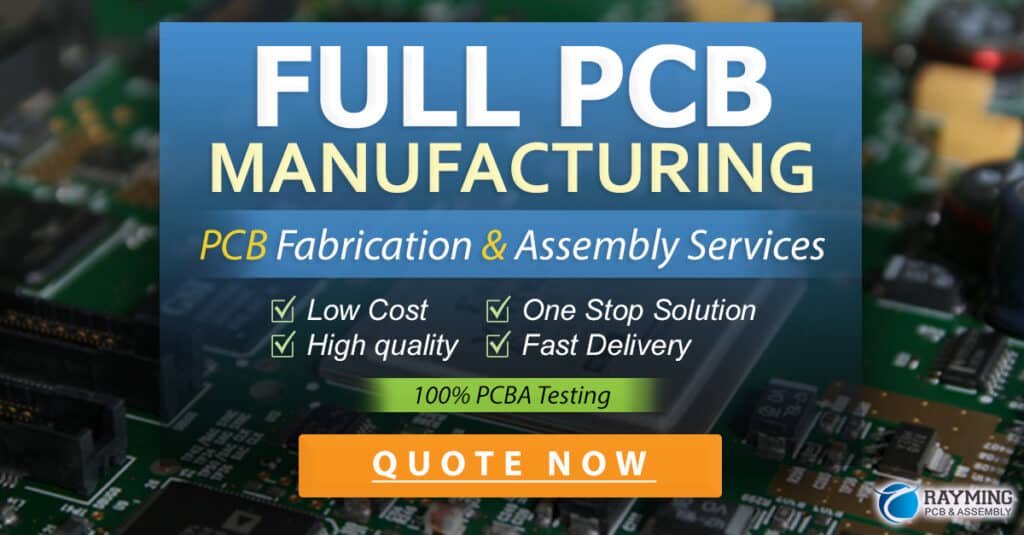
Advantages and Disadvantages of Heavy Copper PCB
Advantages
- Higher current carrying capacity enables the design of high-power systems
- Improved thermal management leads to better reliability and longer product life
- Enhanced mechanical stability reduces the risk of PCB warping or damage
- Lower resistance and voltage drop result in improved system efficiency
- Better signal integrity due to reduced electromagnetic interference (EMI)
Disadvantages
- Higher material and manufacturing costs compared to standard PCBs
- Increased PCB weight and thickness may impact product design and packaging
- Longer manufacturing lead times due to specialized processes
- Potential for warping or bowing if not designed and manufactured properly
- Limited availability of heavy copper PCB manufacturers and suppliers
Future Trends in Heavy Copper PCB
As the demand for high-power electronic systems continues to grow, the use of heavy copper PCBs is expected to increase in various industries. Some future trends in heavy copper PCB technology include:
- Development of new substrate materials with better thermal and mechanical properties
- Advancements in manufacturing processes to improve the efficiency and accuracy of heavy copper PCB fabrication
- Increased adoption of heavy copper PCBs in emerging applications, such as renewable energy systems and 5G telecommunications infrastructure
- Integration of heavy copper PCBs with other advanced technologies, such as embedded components and 3D printing
- Ongoing research to optimize the design and performance of heavy copper PCBs for specific applications
Frequently Asked Questions (FAQ)
1. What is the difference between heavy copper PCB and standard PCB?
Heavy copper PCBs have thicker copper layers compared to standard PCBs, typically ranging from 3 oz/ft² to 20 oz/ft², while standard PCBs have copper thicknesses of 1 oz/ft² to 2 oz/ft². The increased copper thickness in heavy copper PCBs enables them to handle higher currents, improve thermal management, and provide better mechanical stability.
2. What are the main applications of heavy copper PCB?
Heavy copper PCBs are primarily used in applications that require high power handling, such as power electronics (e.g., switch-mode power supplies, inverters, and motor drives), automotive electronics (e.g., electric vehicle battery management systems and engine control units), and industrial equipment (e.g., welding machines, CNC machines, and robotics).
3. How does the increased copper thickness affect the manufacturing process of heavy copper PCBs?
Manufacturing heavy copper PCBs requires specialized equipment and processes compared to standard PCBs. The thicker copper layers need longer plating times, may require multiple plating steps, and can be challenging to drill and etch accurately. Soldering components to heavy copper PCBs may also require higher temperatures and longer dwell times to ensure proper solder joint formation.
4. What are some design considerations for heavy copper PCBs?
When designing heavy copper PCBs, key considerations include thermal management (using techniques like thermal vias, heat sinks, and optimized layouts), current carrying capacity (calculating appropriate trace widths based on IPC-2152 standard), mechanical stability (using symmetrical layer stackups and support features), and manufacturing feasibility (working closely with the PCB manufacturer and providing detailed specifications).
5. What are the advantages and disadvantages of using heavy copper PCBs?
The main advantages of heavy copper PCBs include higher current carrying capacity, improved thermal management, enhanced mechanical stability, lower resistance and voltage drop, and better signal integrity. However, they also have some disadvantages, such as higher material and manufacturing costs, increased PCB weight and thickness, longer manufacturing lead times, potential for warping if not designed properly, and limited availability of suppliers.
Conclusion
Heavy copper PCBs are a specialized type of printed circuit board that offer numerous benefits for high-power electronic applications. With their increased copper thickness, heavy copper PCBs can handle higher currents, provide better thermal management, and enhance mechanical stability compared to standard PCBs. These characteristics make them ideal for use in power electronics, automotive systems, industrial equipment, and other applications that demand reliable performance under challenging conditions.
Designing and manufacturing heavy copper PCBs requires careful consideration of factors such as thermal management, current carrying capacity, mechanical stability, and manufacturing feasibility. By working closely with PCB manufacturers and following industry standards and best practices, designers can successfully incorporate heavy copper PCBs into their products and systems.
As the electronics industry continues to evolve and the demand for high-power systems grows, heavy copper PCBs are poised to play an increasingly important role in enabling advanced technologies and applications. With ongoing research and development in materials, manufacturing processes, and design techniques, the future of heavy copper PCBs looks bright, offering exciting opportunities for innovation and growth across various sectors.
No responses yet