Introduction to Halogen-free PCBs
Halogen-free printed circuit boards (PCBs) have gained significant attention in recent years due to growing concerns about the environmental impact and safety of electronic devices. As the demand for eco-friendly and sustainable electronics continues to rise, halogen-free PCBs have become an essential component in the manufacturing process. This ultimate guide, updated for 2024, will provide you with a comprehensive understanding of halogen-free PCBs, their benefits, and their applications in various industries.
What are Halogens?
Halogens are a group of chemical elements that include fluorine (F), chlorine (Cl), bromine (Br), iodine (I), and astatine (At). These elements are highly reactive and can form stable compounds with other elements. In the context of PCBs, the most commonly used halogens are bromine and chlorine, which are often found in flame retardants used in traditional PCBs.
The Need for Halogen-Free PCBs
Traditional PCBs contain halogenated flame retardants (HFRs) to prevent the spread of fire in case of overheating or short circuits. However, these HFRs have been found to pose significant environmental and health risks. When exposed to high temperatures, HFRs can release toxic fumes that are harmful to human health and the environment. Moreover, the disposal of PCBs containing HFRs can lead to the accumulation of these toxic substances in landfills and water bodies, causing long-term ecological damage.
To address these concerns, the electronics industry has been shifting towards the use of halogen-free PCBs. These PCBs are manufactured using materials that do not contain any of the halogen elements, making them a safer and more environmentally friendly alternative to traditional PCBs.
Advantages of Halogen-Free PCBs
1. Environmental Benefits
One of the primary advantages of halogen-free PCBs is their reduced environmental impact. By eliminating the use of HFRs, these PCBs minimize the release of toxic substances into the environment during their production, use, and disposal. This helps in preserving the ecosystem and reducing the carbon footprint of the electronics industry.
2. Improved Safety
Halogen-free PCBs offer enhanced safety for both manufacturers and end-users. In the event of a fire, these PCBs release significantly less toxic smoke compared to traditional PCBs, reducing the risk of harm to people in the vicinity. Additionally, the absence of halogens makes the manufacturing process safer for workers, as they are not exposed to harmful fumes.
3. Compliance with Regulations
With the increasing awareness of the environmental impact of electronic waste, governments and international organizations have introduced stricter regulations on the use of hazardous substances in electronics. Halogen-free PCBs help manufacturers comply with these regulations, such as the Restriction of Hazardous Substances (RoHS) directive and the Waste Electrical and Electronic Equipment (WEEE) directive, ensuring that their products meet the necessary standards for environmental protection.
4. Better Thermal Stability
Halogen-free PCBs exhibit better thermal stability compared to traditional PCBs. The absence of halogens reduces the risk of thermal decomposition, which can lead to the formation of conductive pathways and short circuits. This improved thermal stability enhances the reliability and longevity of electronic devices.
5. Recyclability
Halogen-free PCBs are easier to recycle compared to traditional PCBs. The absence of halogens simplifies the recycling process, as there is no need to separate the hazardous substances from the recyclable materials. This not only reduces the environmental impact of electronic waste but also promotes the sustainable use of resources.
Applications of Halogen-Free PCBs
Halogen-free PCBs find applications in a wide range of industries, including:
- Consumer Electronics
- Smartphones
- Laptops
- Tablets
-
Wearable devices
-
Automotive Industry
- In-vehicle infotainment systems
- Advanced driver assistance systems (ADAS)
-
Electric vehicle charging systems
-
Medical Devices
- Diagnostic equipment
- Monitoring systems
-
Implantable devices
-
Industrial Automation
- Robotics
- Process control systems
-
Sensors and actuators
-
Aerospace and Defense
- Avionics
- Satellite communication systems
- Military equipment
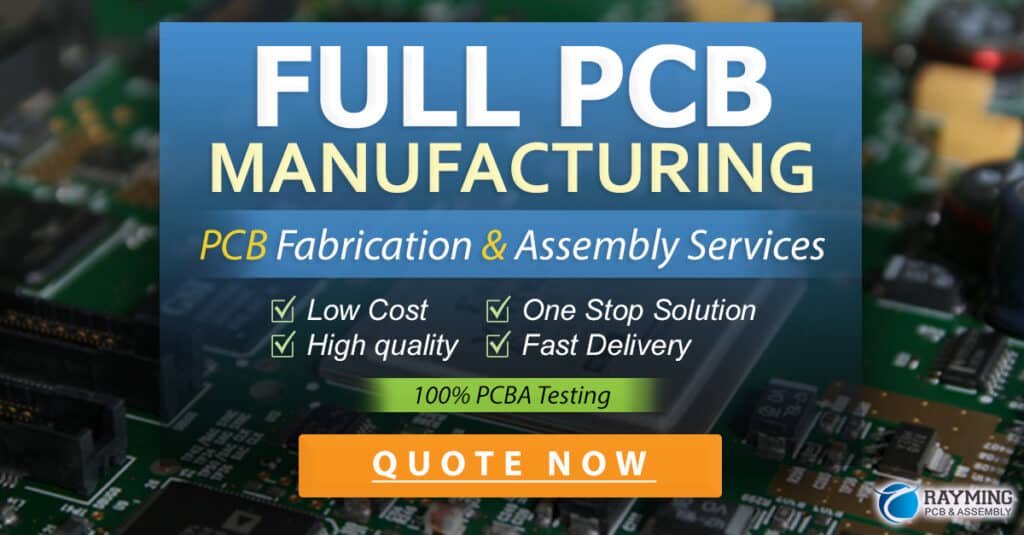
Materials Used in Halogen-Free PCBs
Halogen-free PCBs are manufactured using a variety of materials that provide the necessary electrical, thermal, and mechanical properties without the use of halogens. Some of the commonly used materials include:
1. Halogen-Free Laminates
Halogen-free laminates are the base material used in the construction of PCBs. These laminates are made from a combination of glass fiber and epoxy resin, with the addition of non-halogenated flame retardants. Examples of halogen-free laminates include:
- FR-4 (Flame Retardant 4) with non-halogenated flame retardants
- Polyimide (PI) with non-halogenated flame retardants
- Polytetrafluoroethylene (PTFE) with non-halogenated flame retardants
2. Halogen-Free Solder Masks
Solder masks are applied to the surface of PCBs to protect the copper traces from oxidation and prevent short circuits during the soldering process. Halogen-free solder masks are formulated using non-halogenated materials, such as acrylic or polyurethane-based resins.
3. Halogen-Free Inks and Coatings
Inks and coatings used in the manufacturing of halogen-free PCBs are also formulated without the use of halogens. These materials provide the necessary insulation, protection, and marking on the PCB surface while maintaining their eco-friendly properties.
Manufacturing Process of Halogen-Free PCBs
The manufacturing process of halogen-free PCBs is similar to that of traditional PCBs, with a few key differences in the materials used and the handling of waste. The process typically involves the following steps:
- Design and Layout
-
The PCB design is created using computer-aided design (CAD) software, taking into account the specific requirements of the halogen-free materials.
-
Material Selection
-
Halogen-free laminates, solder masks, inks, and coatings are selected based on the desired electrical, thermal, and mechanical properties of the PCB.
-
Copper Etching
-
The designed circuit pattern is transferred onto the copper-clad laminate using a photoresist and etching process.
-
Drilling and Plating
-
Holes are drilled into the PCB for component placement, and the holes are plated with copper to establish electrical connections between layers.
-
Solder Mask Application
-
A halogen-free solder mask is applied to the PCB surface to protect the copper traces and prevent short circuits.
-
Surface Finishing
-
The exposed copper areas are coated with a protective layer, such as immersion gold or electroless nickel/immersion gold (ENIG), to prevent oxidation and enhance solderability.
-
Silk Screen Printing
-
Halogen-free inks are used to print component designators, logos, and other markings on the PCB surface.
-
Waste Management
- The waste generated during the manufacturing process, such as copper-containing solutions and rinse water, is properly treated and disposed of in accordance with environmental regulations.
Challenges and Future Developments
While halogen-free PCBs offer numerous benefits, there are still some challenges that need to be addressed to further enhance their performance and adoption. Some of these challenges include:
- Higher Material Costs
-
Halogen-free materials, such as laminates and solder masks, are often more expensive than their halogenated counterparts, which can increase the overall cost of PCB production.
-
Balancing Performance and Eco-Friendliness
-
Achieving the right balance between the electrical and thermal performance of halogen-free PCBs and their environmental impact remains a challenge for manufacturers.
-
Compatibility with Existing Manufacturing Processes
- The transition to halogen-free PCBs may require modifications to existing manufacturing processes and equipment, which can be time-consuming and costly.
Despite these challenges, the future of halogen-free PCBs looks promising. As research and development efforts continue, new materials and technologies are being developed to address the limitations of current halogen-free solutions. Some of the future developments in this field include:
- Bio-Based Materials
-
The use of bio-based materials, such as plant-derived resins and natural fibers, in the production of halogen-free PCBs is being explored to further enhance their eco-friendliness.
-
Advanced Flame Retardants
-
The development of novel, non-halogenated flame retardants with improved performance and environmental compatibility is an ongoing area of research.
-
Recycling and Circular Economy
- Efforts are being made to develop more efficient recycling processes for halogen-free PCBs, promoting a circular economy approach in the electronics industry.
Frequently Asked Questions (FAQ)
-
Q: Are halogen-free PCBs more expensive than traditional PCBs?
A: Yes, halogen-free PCBs are generally more expensive than traditional PCBs due to the higher cost of halogen-free materials and the potential need for modifications to existing manufacturing processes. -
Q: Can halogen-free PCBs be used in high-temperature applications?
A: Yes, halogen-free PCBs can be used in high-temperature applications. In fact, they often exhibit better thermal stability compared to traditional PCBs, reducing the risk of thermal decomposition and short circuits. -
Q: Are halogen-free PCBs compliant with RoHS and WEEE directives?
A: Yes, halogen-free PCBs are designed to comply with the Restriction of Hazardous Substances (RoHS) and the Waste Electrical and Electronic Equipment (WEEE) directives, which aim to reduce the environmental impact of electronic waste. -
Q: Can halogen-free PCBs be recycled?
A: Yes, halogen-free PCBs are easier to recycle compared to traditional PCBs. The absence of halogens simplifies the recycling process, as there is no need to separate the hazardous substances from the recyclable materials. -
Q: What industries are driving the adoption of halogen-free PCBs?
A: The adoption of halogen-free PCBs is being driven by various industries, including consumer electronics, automotive, medical devices, industrial automation, and aerospace and defense, where environmental sustainability and safety are of utmost importance.
Conclusion
Halogen-free PCBs represent a significant step towards a more sustainable and environmentally friendly electronics industry. By eliminating the use of hazardous substances, these PCBs offer numerous benefits, including reduced environmental impact, improved safety, compliance with regulations, better thermal stability, and easier recyclability. As the demand for eco-friendly electronics continues to grow, the adoption of halogen-free PCBs is expected to increase across various industries.
Despite the challenges associated with the transition to halogen-free PCBs, ongoing research and development efforts are paving the way for new materials and technologies that will further enhance their performance and sustainability. As we move towards a more environmentally conscious future, halogen-free PCBs will undoubtedly play a crucial role in shaping the electronics industry and promoting a greener, safer, and more responsible approach to technology.
No responses yet