Composition of HAL lead-free solder
HAL lead-free solder typically consists of a combination of tin (Sn), silver (Ag), and copper (Cu). The most common composition is known as SAC305, which contains 96.5% tin, 3% silver, and 0.5% copper. Other variations of HAL lead-free solder may include small amounts of additional elements such as bismuth (Bi), indium (In), or antimony (Sb) to improve specific properties like wettability, mechanical strength, or melting temperature.
The table below shows the composition of some common HAL lead-free solder alloys:
Alloy | Tin (Sn) | Silver (Ag) | Copper (Cu) | Other Elements |
---|---|---|---|---|
SAC305 | 96.5% | 3% | 0.5% | – |
SAC387 | 95.5% | 3.8% | 0.7% | – |
SAC105 | 98.5% | 1% | 0.5% | – |
SACX0307 | 99% | 0.3% | 0.7% | Bi, In, or Sb |
Advantages of HAL lead-free solder
1. Environmental and health benefits
The primary advantage of HAL lead-free solder is the elimination of lead from the soldering process. Lead is a toxic substance that can cause serious health problems, especially in children, when ingested or inhaled. By using lead-free solder, the electronics industry can reduce the risk of lead exposure and minimize the environmental impact of electronic waste.
2. Compliance with regulations
Many countries have implemented regulations that restrict the use of lead in electronic products. The European Union’s RoHS directive, for example, limits the maximum concentration of lead in electronic components to 0.1% by weight. By using HAL lead-free solder, manufacturers can ensure compliance with these regulations and avoid penalties or market access restrictions.
3. Improved reliability
HAL lead-free solder has been shown to provide better mechanical strength and thermal cycling performance compared to traditional lead-based solder. The higher melting temperature of lead-free solder alloys (typically around 217°C for SAC305) can help prevent issues like thermal fatigue and whisker growth, which can lead to premature failure of electronic components.
Challenges of using HAL lead-free solder
1. Higher melting temperature
One of the main challenges of using HAL lead-free solder is its higher melting temperature compared to lead-based solder. This higher temperature can cause thermal stress on electronic components during the soldering process, potentially leading to damage or reduced reliability. To mitigate this issue, manufacturers may need to adjust their soldering processes and equipment to accommodate the higher temperatures required for lead-free solder.
2. Wetting and spreading
Lead-free solder alloys often have different wetting and spreading characteristics compared to lead-based solder. This can result in challenges in achieving good solder joint formation and reliability. Manufacturers may need to optimize their soldering processes, such as adjusting the flux composition or preheating temperatures, to ensure adequate wetting and spreading of HAL lead-free solder.
3. Cost considerations
The transition to HAL lead-free solder can involve additional costs for manufacturers. These costs may include investments in new soldering equipment, training for personnel, and potential increases in raw material costs due to the use of silver and other elements in lead-free solder alloys. However, the long-term benefits of using lead-free solder, such as improved environmental and health outcomes and compliance with regulations, can outweigh these initial costs.
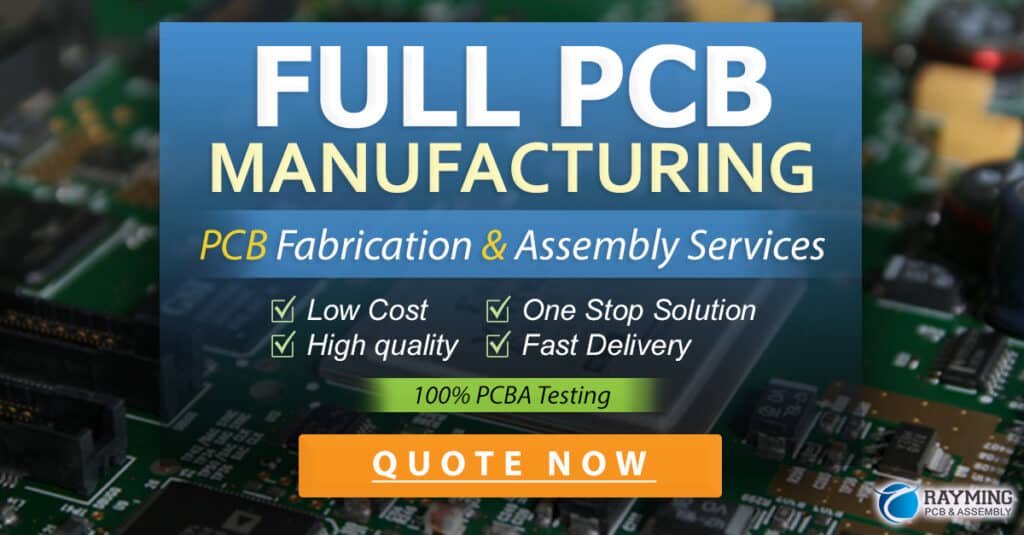
Applications of HAL lead-free solder
HAL lead-free solder is widely used in various electronic applications, including:
- Consumer electronics: Smartphones, tablets, laptops, televisions, and home appliances.
- Automotive electronics: Engine control units, sensors, infotainment systems, and safety devices.
- Industrial electronics: Process control systems, automation equipment, and power electronics.
- Medical devices: Diagnostic equipment, monitoring systems, and implantable devices.
- Aerospace and defense: Avionics, communication systems, and military equipment.
The use of HAL lead-free solder in these applications ensures compliance with environmental regulations and helps reduce the potential health risks associated with lead exposure.
Future developments in lead-free soldering
As the electronics industry continues to evolve, research and development efforts are focused on improving the performance and reliability of lead-free solder alloys. Some areas of interest include:
- Low-temperature soldering: Developing lead-free solder alloys with lower melting temperatures to reduce thermal stress on electronic components during the soldering process.
- High-reliability alloys: Formulating new lead-free solder compositions that provide enhanced mechanical strength, thermal cycling performance, and resistance to common failure modes like tin whiskers.
- Eco-friendly fluxes: Developing more environmentally friendly fluxes that minimize the use of harmful chemicals and improve the recyclability of electronic waste.
- Advanced soldering techniques: Exploring new soldering methods, such as laser soldering or ultrasonic soldering, that can improve the efficiency and reliability of lead-free soldering processes.
As these developments progress, the use of HAL lead-free solder is expected to become even more widespread, contributing to a more sustainable and health-conscious electronics industry.
FAQs
-
Q: What is the main difference between HAL lead-free solder and traditional lead-based solder?
A: The main difference is that HAL lead-free solder does not contain lead, which is a toxic heavy metal. Instead, it consists of a combination of tin, silver, and copper, with occasional small amounts of other elements like bismuth, indium, or antimony. -
Q: Why is it important to use lead-free solder in electronic products?
A: Using lead-free solder is important because lead is a toxic substance that can cause serious health problems when ingested or inhaled. By eliminating lead from electronic products, the industry can reduce the risk of lead exposure and minimize the environmental impact of electronic waste. -
Q: What are the most common compositions of HAL lead-free solder?
A: The most common composition of HAL lead-free solder is SAC305, which contains 96.5% tin, 3% silver, and 0.5% copper. Other variations include SAC387 (95.5% tin, 3.8% silver, 0.7% copper) and SAC105 (98.5% tin, 1% silver, 0.5% copper). -
Q: What challenges do manufacturers face when using HAL lead-free solder?
A: Some of the main challenges include the higher melting temperature of lead-free solder alloys, which can cause thermal stress on electronic components, and differences in wetting and spreading characteristics compared to lead-based solder. Manufacturers may need to adjust their soldering processes and equipment to accommodate these differences. -
Q: What are some of the future developments in lead-free soldering?
A: Research and development efforts are focused on improving the performance and reliability of lead-free solder alloys. Some areas of interest include developing low-temperature soldering alloys, formulating high-reliability alloys, creating eco-friendly fluxes, and exploring advanced soldering techniques like laser or ultrasonic soldering.
Conclusion
HAL lead-free solder represents a significant advancement in the electronics industry, addressing the environmental and health concerns associated with the use of lead in electronic products. By using tin-silver-copper alloys and other lead-free compositions, manufacturers can ensure compliance with regulations like the RoHS directive and reduce the risk of lead exposure.
While the transition to HAL lead-free solder presents some challenges, such as higher melting temperatures and differences in wetting and spreading characteristics, the long-term benefits of using lead-free solder are substantial. As research and development efforts continue to improve the performance and reliability of lead-free solder alloys, the use of HAL lead-free solder is expected to become even more widespread, contributing to a more sustainable and health-conscious electronics industry.
No responses yet