Table of Contents
- Production of Copper Foil
- Types of Copper Foil
- Properties of Copper Foil
- Applications of Copper Foil
- Frequently Asked Questions (FAQ)
Production of Copper Foil
Copper foil is produced through a process called electrodeposition. This process involves the following steps:
- A large cylindrical drum, called a mandrel, is partially immersed in an electrolyte solution containing copper ions.
- The mandrel acts as the cathode (negative electrode), while copper plates surrounding the mandrel serve as the anode (positive electrode).
- An electric current is applied, causing the copper ions in the solution to be attracted to the mandrel and deposited on its surface.
- As the mandrel rotates, a thin, continuous layer of copper is deposited evenly on its surface.
- The thickness of the copper foil is controlled by adjusting the current density and the rotational speed of the mandrel.
- Once the desired thickness is achieved, the copper foil is peeled off the mandrel and wound onto a roll.
Electrolyte Solution Composition
The electrolyte solution used in the production of copper foil typically consists of the following components:
Component | Concentration |
---|---|
Copper sulfate (CuSO4) | 200-250 g/L |
Sulfuric acid (H2SO4) | 50-70 g/L |
Chloride ions (Cl-) | 50-70 ppm |
Organic additives | As required |
The organic additives help to control the grain structure and mechanical properties of the deposited copper foil.
Types of Copper Foil
Copper foil can be classified into different types based on various factors, such as thickness, manufacturing process, and surface treatment. Some common types of copper foil include:
Electrodeposited Copper Foil
Electrodeposited copper foil is the most common type and is produced using the electrodeposition process described earlier. It is further classified based on its thickness and surface treatment:
- Standard Copper Foil: Thickness ranges from 9 to 140 μm (0.0004 to 0.0055 in).
- Thin Copper Foil: Thickness ranges from 5 to 9 μm (0.0002 to 0.0004 in).
- Ultra-Thin Copper Foil: Thickness is less than 5 μm (0.0002 in).
- Treated Copper Foil: Electrodeposited foil with additional surface treatments, such as anti-tarnish, passivation, or adhesion promotion.
Rolled Copper Foil
Rolled copper foil is produced by mechanically rolling copper sheets to the desired thickness. This type of foil is generally thicker than electrodeposited foil and is used in applications where higher mechanical strength is required.
Annealed Copper Foil
Annealed copper foil is electrodeposited or rolled foil that has undergone a heat treatment process to improve its ductility and reduce its hardness. This type of foil is easier to form and shape compared to non-annealed foil.
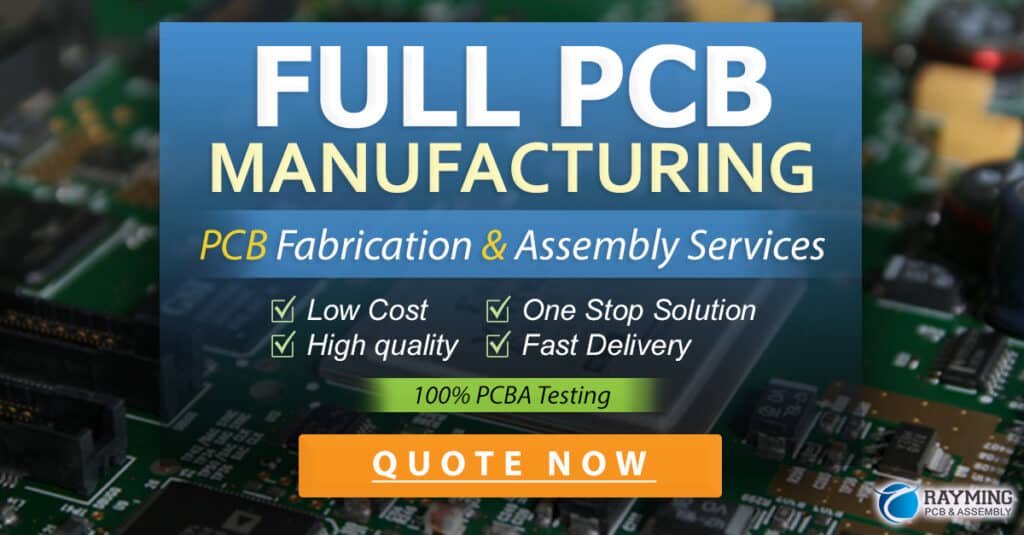
Properties of Copper Foil
Copper foil possesses several unique properties that make it suitable for various applications. Some of the key properties of copper foil include:
Electrical Conductivity
Copper foil has excellent electrical conductivity, making it an ideal material for use in electrical and electronic applications. The electrical conductivity of copper foil is dependent on its purity and can be as high as 101% IACS (International Annealed Copper Standard).
Thermal Conductivity
Copper foil also has high thermal conductivity, which allows it to efficiently dissipate heat. This property is particularly useful in applications where heat management is critical, such as in electronic devices and heat exchangers.
Malleability and Ductility
Copper foil is highly malleable and ductile, meaning it can be easily bent, shaped, and stretched without breaking. This property allows copper foil to be used in applications where conformability is required, such as in flexible printed circuits and EMI shielding.
Corrosion Resistance
Copper foil has a natural resistance to corrosion due to the formation of a protective oxide layer on its surface. This property makes copper foil suitable for use in harsh environments and applications where corrosion resistance is important.
Applications of Copper Foil
Copper foil finds use in a wide range of industries and applications, including:
Electronics Industry
- Printed Circuit Boards (PCBs): Copper foil is used as the conductive layer in PCBs, which are the backbone of modern electronic devices.
- Flexible Printed Circuits (FPCs): Thin and ultra-thin copper foil is used in the production of FPCs, which are used in applications where flexibility and space constraints are critical, such as in mobile devices and wearable electronics.
- EMI Shielding: Copper foil is used as a shielding material to protect electronic devices from electromagnetic interference (EMI).
Energy Industry
- Lithium-Ion Batteries: Copper foil is used as the current collector in the anode of lithium-ion batteries, which are used in various applications, including electric vehicles and portable electronics.
- Solar Cells: Copper foil is used as the conductive layer in some types of solar cells, such as copper indium gallium selenide (CIGS) solar cells.
Automotive Industry
- Automotive Electronics: Copper foil is used in the production of various automotive electronic components, such as engine control units, infotainment systems, and advanced driver assistance systems (ADAS).
- Electric Vehicle Battery Packs: As mentioned earlier, copper foil is a key component in lithium-ion batteries, which are used in electric vehicle battery packs.
Other Applications
- Decorative Applications: Copper foil is used in various decorative applications, such as in art and crafts, furniture, and architectural elements.
- Shielding Applications: Apart from EMI shielding in electronics, copper foil is also used for shielding in other applications, such as in the production of shielded cables and in the construction of MRI rooms.
Frequently Asked Questions (FAQ)
1. What is the difference between copper foil and copper sheet?
The main difference between copper foil and copper sheet is their thickness. Copper foil is typically less than 0.15 mm (0.006 in) thick, while copper sheets are thicker than 0.15 mm. Copper foil is produced by electrodeposition or rolling, while copper sheets are usually produced by rolling.
2. Can copper foil be soldered?
Yes, copper foil can be soldered. In fact, copper foil is commonly used in the production of printed circuit boards (PCBs), where electronic components are soldered onto the copper foil traces.
3. How is the thickness of copper foil measured?
The thickness of copper foil is typically measured in micrometers (μm) or ounces per square foot (oz/ft²). In the PCB industry, the thickness of copper foil is often expressed in ounces, with 1 oz/ft² being equivalent to a thickness of about 35 μm (0.0014 in).
4. What is the purity of copper foil?
The purity of copper foil can vary depending on the manufacturing process and the intended application. High-purity copper foil, such as that used in the production of PCBs, typically has a purity of 99.8% or higher.
5. Is copper foil recyclable?
Yes, copper foil is recyclable. Copper is a valuable material and can be recycled indefinitely without losing its properties. Recycling copper foil helps to conserve natural resources and reduce environmental impact.
No responses yet