Introduction to Copper-Clad Laminate
Copper-Clad Laminate (CCL) is a fundamental material used in the manufacturing of Printed Circuit Boards (PCBs). It consists of a thin layer of copper foil bonded to one or both sides of an insulating substrate, such as fiberglass, epoxy resin, or polyimide. The copper layer serves as the conductive material for the electrical connections, while the insulating substrate provides mechanical support and electrical isolation between the copper traces.
CCL plays a crucial role in the electronics industry, as it is the foundation for creating the complex circuitry found in various electronic devices, including smartphones, computers, televisions, and automotive systems. The quality and properties of the CCL directly impact the performance, reliability, and durability of the final PCB.
Composition of Copper-Clad Laminate
A typical Copper-Clad Laminate consists of three main components:
-
Copper Foil: The copper foil is a thin, conductive layer that is bonded to the insulating substrate. The thickness of the copper foil can vary depending on the application and the desired electrical properties of the PCB. Common copper foil thicknesses range from 9 µm to 70 µm (0.0004 to 0.0028 inches).
-
Insulating Substrate: The insulating substrate is the base material that provides mechanical support and electrical isolation for the copper traces. The most commonly used substrates in CCL are:
- FR-4: A composite material made of woven fiberglass cloth impregnated with epoxy resin. FR-4 is the most widely used substrate due to its excellent mechanical and electrical properties, as well as its cost-effectiveness.
- Polyimide: A high-performance polymer known for its exceptional thermal stability, chemical resistance, and flexibility. Polyimide-based CCLs are often used in applications that require high reliability and the ability to withstand harsh environments.
-
CEM-1 and CEM-3: Composite Epoxy Materials that combine a woven fiberglass cloth and a non-woven fiberglass mat, respectively, with epoxy resin. These substrates offer a balance between cost and performance.
-
Bonding Agent: The bonding agent is a thin layer of adhesive that ensures a strong and reliable bond between the copper foil and the insulating substrate. The most common bonding agents are epoxy resins, which provide excellent adhesion, chemical resistance, and thermal stability.
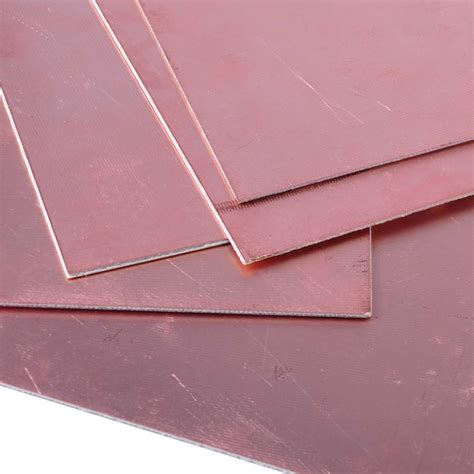
Manufacturing Process of Copper-Clad Laminate
The manufacturing process of Copper-Clad Laminate involves several steps to ensure a high-quality and consistent product:
-
Substrate Preparation: The insulating substrate, such as FR-4 or polyimide, is cut to the desired size and shape. The surface of the substrate is then cleaned and treated to improve adhesion with the copper foil.
-
Copper Foil Preparation: The copper foil is also cut to the appropriate size and cleaned to remove any contaminants or oxidation that may affect the bonding process.
-
Lamination: The prepared substrate and copper foil are placed in a lamination press, where they are subjected to high temperature and pressure. The bonding agent, typically an epoxy resin, is activated by the heat and pressure, creating a strong and uniform bond between the copper foil and the substrate.
-
Cooling and Inspection: After lamination, the CCL is cooled to room temperature and inspected for any defects, such as delamination, blisters, or voids. Quality control measures, including visual inspection and electrical testing, ensure that the CCL meets the required specifications.
-
Cutting and Packaging: The cooled CCL is then cut to the desired panel sizes and packaged for shipping to PCB Manufacturers.
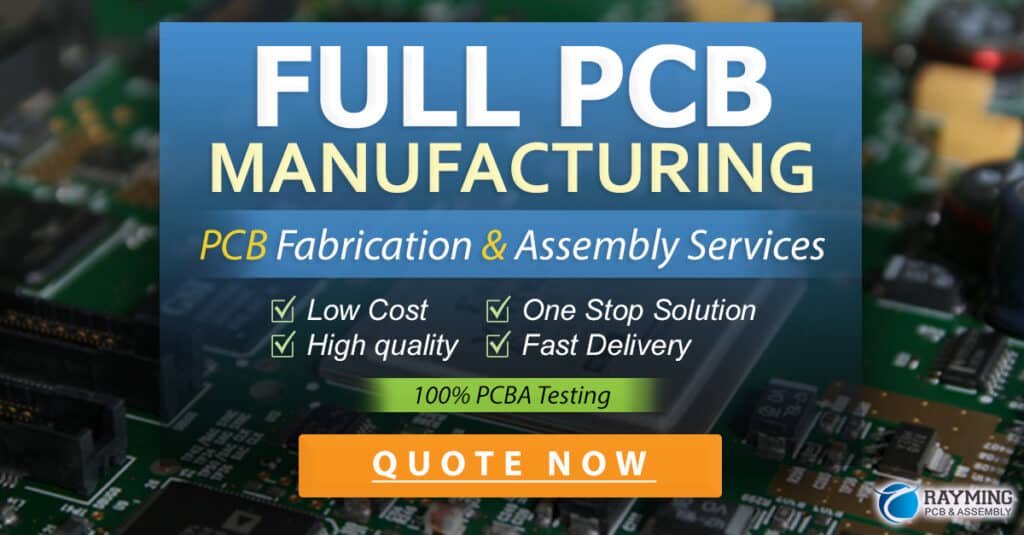
Properties and Characteristics of Copper-Clad Laminate
The performance and reliability of a PCB are heavily dependent on the properties and characteristics of the Copper-Clad Laminate used in its construction. Some of the key properties and characteristics of CCL include:
- Dielectric Constant (Dk): The dielectric constant is a measure of the insulating substrate’s ability to store electrical energy. A lower Dk value indicates better electrical performance, particularly at high frequencies. Typical Dk values for common CCL substrates are:
- FR-4: 4.2 to 4.5
- Polyimide: 3.2 to 3.6
-
CEM-1 and CEM-3: 4.2 to 4.5
-
Dissipation Factor (Df): The dissipation factor, also known as the loss tangent, is a measure of the insulating substrate’s ability to dissipate electrical energy as heat. A lower Df value indicates better Signal Integrity and lower power loss. Typical Df values for common CCL substrates are:
- FR-4: 0.02 to 0.03
- Polyimide: 0.002 to 0.003
-
CEM-1 and CEM-3: 0.02 to 0.03
-
Thermal Conductivity: Thermal conductivity is a measure of the CCL’s ability to transfer heat from the copper traces to the surrounding environment. A higher thermal conductivity helps to dissipate heat more effectively, improving the thermal management of the PCB. Typical thermal conductivity values for common CCL substrates are:
- FR-4: 0.3 to 0.4 W/mK
- Polyimide: 0.2 to 0.3 W/mK
-
CEM-1 and CEM-3: 0.3 to 0.4 W/mK
-
Peel Strength: Peel strength is a measure of the bond strength between the copper foil and the insulating substrate. A higher peel strength indicates better adhesion and reduces the risk of delamination during the PCB manufacturing process or in the field. Typical peel strength values for CCL range from 8 to 20 N/cm (4.6 to 11.4 lbf/in).
-
Dimensional Stability: Dimensional stability refers to the CCL’s ability to maintain its size and shape when exposed to changes in temperature and humidity. High dimensional stability is essential for maintaining the accuracy of the copper traces and preventing warpage or distortion of the PCB. Dimensional stability is typically expressed as a percentage change in dimensions per degree Celsius (ppm/°C) or per percent relative humidity (ppm/%RH).
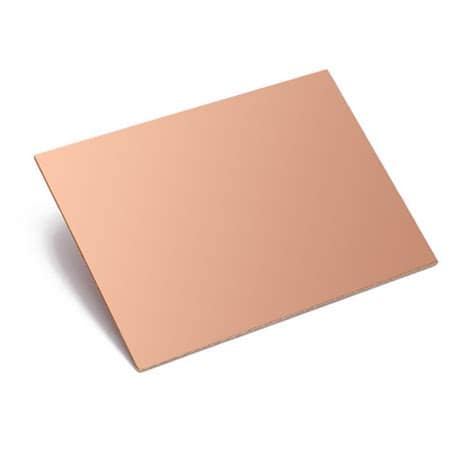
Applications of Copper-Clad Laminate
Copper-Clad Laminate is used in a wide range of electronic applications, from consumer electronics to industrial and aerospace systems. Some of the most common applications of CCL include:
-
Consumer Electronics: CCL is used in the production of PCBs for smartphones, tablets, laptops, televisions, gaming consoles, and other consumer electronic devices.
-
Automotive Electronics: Modern automobiles rely heavily on electronic systems for engine management, safety, entertainment, and communication. CCL is used in the manufacturing of PCBs for these automotive electronic systems.
-
Industrial Electronics: CCL is used in the production of PCBs for industrial control systems, power electronics, automation equipment, and instrumentation.
-
Medical Electronics: CCL is used in the manufacturing of PCBs for medical devices, such as patient monitors, diagnostic equipment, and implantable devices.
-
Aerospace and Defense Electronics: High-reliability CCLs, such as polyimide-based laminates, are used in the production of PCBs for aerospace and defense applications, where the electronics must withstand harsh environments and meet stringent performance requirements.
Advancements and Future Trends in Copper-Clad Laminate Technology
As electronic devices continue to become more complex, compact, and high-performance, there is a growing demand for advanced Copper-Clad Laminate materials that can meet these challenges. Some of the key advancements and future trends in CCL technology include:
-
High-Frequency Materials: With the increasing adoption of 5G wireless technology and the growth of high-speed data communication, there is a need for CCLs that can support high-frequency applications. Advanced CCL materials, such as low-loss dielectrics and ultra-low Dk/Df substrates, are being developed to meet these requirements.
-
Thermally Conductive Materials: As electronic devices become more powerful and compact, thermal management becomes a critical issue. Thermally conductive CCLs, which incorporate materials such as ceramics or metal particles into the insulating substrate, are being developed to improve heat dissipation and prevent thermal-related failures.
-
Flexible and Stretchable Materials: The growing demand for flexible and wearable electronics has led to the development of flexible and stretchable CCLs. These materials, often based on polyimide or other flexible polymers, enable the production of PCBs that can bend, fold, or stretch without losing their electrical and mechanical properties.
-
Eco-Friendly Materials: With increasing environmental concerns and regulations, there is a growing interest in eco-friendly CCL materials. Bio-based and recyclable substrates, as well as halogen-free flame retardants, are being developed to reduce the environmental impact of PCB manufacturing.
-
Embedded Components: Embedded component technology, which involves integrating passive components (such as resistors and capacitors) directly into the CCL, is gaining traction as a way to increase PCB density and reduce manufacturing costs. Advanced CCLs with embedded components are being developed to support this trend.
Frequently Asked Questions (FAQ)
-
What is the difference between single-sided and double-sided Copper-Clad Laminate?
Single-sided CCL has a copper foil bonded to one side of the insulating substrate, while double-sided CCL has copper foil bonded to both sides. Double-sided CCL allows for more complex circuitry and higher component density on the PCB. -
Can Copper-Clad Laminate be recycled?
Yes, Copper-Clad Laminate can be recycled. The copper foil can be separated from the insulating substrate and recycled as scrap metal, while the substrate can be recycled into new CCL or other plastic products. However, the recycling process can be complex and costly, and not all CCL materials are easily recyclable. -
How does the thickness of the copper foil affect the performance of the PCB?
The thickness of the copper foil on the CCL directly affects the current-carrying capacity and the resistance of the copper traces on the PCB. Thicker copper foils allow for higher current-carrying capacity and lower resistance, which can be important for power electronics and high-current applications. However, thicker copper foils also make the PCB heavier and more expensive, and can limit the minimum trace width and spacing that can be achieved. -
What is the shelf life of Copper-Clad Laminate?
The shelf life of Copper-Clad Laminate depends on the storage conditions and the specific material composition. In general, CCL should be stored in a cool, dry place, away from direct sunlight and sources of heat or humidity. Properly stored CCL can have a shelf life of several years, but it is always best to consult the manufacturer’s recommendations for specific storage and handling guidelines. -
How do I choose the right Copper-Clad Laminate for my application?
Choosing the right Copper-Clad Laminate for your application depends on several factors, including the electrical performance requirements, the thermal management needs, the mechanical constraints, and the budget. Some key considerations include the dielectric constant and dissipation factor of the substrate, the thermal conductivity of the material, the copper foil thickness, and the overall cost and availability of the CCL. It is often best to consult with a PCB manufacturer or material supplier to determine the most suitable CCL for your specific application.
Conclusion
Copper-Clad Laminate is a critical material in the manufacturing of printed circuit boards, serving as the foundation for the complex circuitry that powers our modern electronic devices. The composition, properties, and characteristics of the CCL directly impact the performance, reliability, and durability of the final PCB.
As electronic devices continue to advance and evolve, so too must the Copper-Clad Laminate materials used in their construction. From high-frequency materials and thermally conductive substrates to flexible and eco-friendly laminates, the future of CCL technology is focused on meeting the ever-increasing demands of the electronics industry.
By understanding the basics of Copper-Clad Laminate, its manufacturing process, properties, and applications, engineers and designers can make informed decisions when selecting the right material for their PCB projects. As the electronics industry continues to push the boundaries of innovation, the development and advancement of CCL technology will play a crucial role in enabling the next generation of electronic devices.
No responses yet