History of CNC
The concept of numerical control (NC) machines dates back to the 1940s when John T. Parsons, an American engineer, developed a method to manufacture helicopter rotor blades using a computer-controlled machine. However, it wasn’t until the 1950s that the first NC machines were built, thanks to the efforts of the U.S. Air Force and the Massachusetts Institute of Technology (MIT).
In the 1960s, the introduction of minicomputers and the development of computer-aided design (CAD) software further advanced the capabilities of NC machines. By the 1970s, the term “CNC” was coined to refer to the combination of computer numerical control and CAD software.
Throughout the following decades, CNC technology continued to evolve, with the introduction of more advanced controllers, servomotors, and software. Today, CNC machines are an integral part of modern manufacturing, used in a wide range of industries, from aerospace and automotive to medical and consumer goods.
How CNC Works
CNC machines operate by following a set of digital instructions, known as a program or G-code, which is created using CAD software. The program contains detailed information about the desired shape, size, and features of the final product, as well as the specific tools and operations required to produce it.
Once the program is loaded into the CNC machine’s controller, the machine can begin the manufacturing process. The controller interprets the G-code and sends signals to the machine’s motors, which move the cutting tools and workpiece in a precise, coordinated manner. This process is repeated until the final product is complete.
CNC machines typically have several key components, including:
- Controller: The “brain” of the machine, which reads and interprets the G-code and controls the motion of the machine’s axes.
- Axes: The linear (X, Y, and Z) and rotary (A, B, and C) motion paths along which the cutting tools and workpiece move.
- Spindle: The rotating part of the machine that holds the cutting tool.
- Tool magazine: A storage area for the various cutting tools used by the machine.
- Workpiece holding device: A fixture or jig that secures the workpiece in place during the manufacturing process.
Types of CNC Machines
There are several types of CNC machines, each designed for specific manufacturing processes and applications. Some of the most common types include:
- CNC Mills: Used for milling, drilling, and boring operations on a variety of materials, such as metals, plastics, and wood.
- CNC Lathes: Used for turning, facing, and threading operations on cylindrical workpieces.
- CNC Routers: Used for cutting, drilling, and shaping operations on wood, plastics, and composite materials.
- CNC Plasma Cutters: Used for cutting thin sheets of metal using a high-velocity jet of ionized gas (plasma).
- CNC Laser Cutters: Used for cutting and engraving operations on a wide range of materials, such as wood, plastics, and metals, using a high-power laser beam.
- CNC Electric Discharge Machines (EDMs): Used for creating complex shapes and intricate details in hard, conductive materials, such as hardened steel and titanium, using electrical discharges.
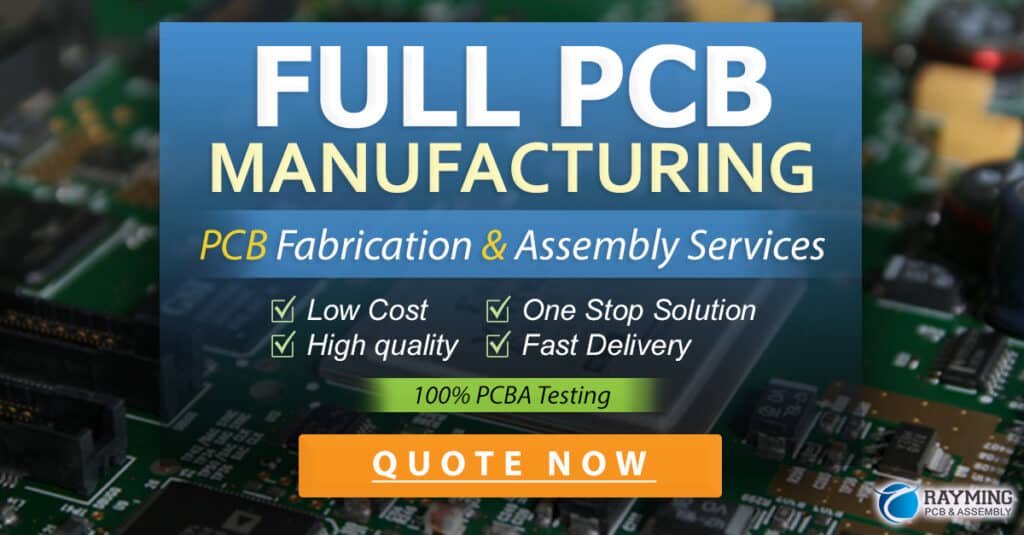
Advantages of CNC Machining
CNC machining offers several key advantages over traditional manufacturing methods, including:
- Precision: CNC machines can produce parts with extremely tight tolerances, often within a few microns, ensuring consistent quality and repeatability.
- Complexity: With the ability to move cutting tools along multiple axes simultaneously, CNC machines can create complex geometries and intricate details that would be difficult or impossible to achieve with manual machining.
- Efficiency: CNC machines can operate continuously, 24/7, with minimal human intervention, resulting in faster production times and lower labor costs.
- Flexibility: CNC machines can be quickly reprogrammed to produce different parts or adapt to design changes, reducing setup times and enabling shorter production runs.
- Safety: By automating the manufacturing process, CNC machines reduce the need for human operators to work in close proximity to dangerous cutting tools and moving parts, enhancing workplace safety.
Disadvantages of CNC Machining
Despite its many benefits, CNC machining does have some limitations and drawbacks, such as:
- High initial investment: CNC machines can be expensive to purchase and set up, requiring a significant upfront investment.
- Skilled operators: While CNC machines automate much of the manufacturing process, they still require skilled programmers and operators to create the G-code and oversee the machine’s operation.
- Limited materials: Some CNC machines may have limitations in terms of the materials they can process, depending on the specific cutting tools and techniques used.
- Maintenance and repair: CNC machines are complex systems with many moving parts, requiring regular maintenance and occasional repairs to ensure optimal performance and longevity.
Applications of CNC Machining
CNC machining is used in a wide range of industries and applications, including:
- Aerospace: CNC machines are used to produce high-precision components for aircraft and spacecraft, such as turbine blades, fuselage parts, and landing gear.
- Automotive: CNC machining is essential for creating engine components, transmission parts, and body panels for cars and trucks.
- Medical: CNC machines are used to manufacture surgical instruments, implants, and prosthetics with the highest degree of accuracy and biocompatibility.
- Electronics: CNC machining is used to create housings, heatsinks, and other components for electronic devices, such as smartphones, computers, and televisions.
- Consumer goods: CNC machines are used to produce a wide variety of consumer products, from furniture and home appliances to sporting goods and jewelry.
Future of CNC Machining
As technology continues to advance, the future of CNC machining looks bright. Some of the key trends and developments shaping the industry include:
- Automation and robotics: The integration of CNC machines with industrial robots and automated material handling systems is enabling even greater levels of efficiency and productivity.
- Additive manufacturing: The combination of CNC machining with 3D printing technologies is opening up new possibilities for creating complex, high-performance parts with unique material properties.
- IoT and data analytics: The adoption of Internet of Things (IoT) sensors and data analytics tools is enabling real-time monitoring and optimization of CNC machine performance, as well as predictive maintenance and quality control.
- AI and machine learning: The application of artificial intelligence and machine learning algorithms to CNC machining is helping to optimize tool paths, reduce cycle times, and improve overall process efficiency.
- Sustainable manufacturing: The development of more energy-efficient CNC machines and the use of eco-friendly cutting fluids and materials is helping to reduce the environmental impact of manufacturing operations.
Table: Comparison of Common CNC Machines
Machine Type | Typical Applications | Materials Processed | Axes of Motion |
---|---|---|---|
CNC Mill | Milling, drilling, boring | Metals, plastics, wood | 3-5 |
CNC Lathe | Turning, facing, threading | Cylindrical workpieces | 2-4 |
CNC Router | Cutting, drilling, shaping | Wood, plastics, composites | 3-5 |
CNC Plasma Cutter | Cutting thin metal sheets | Metals | 2-3 |
CNC Laser Cutter | Cutting, engraving | Wood, plastics, metals | 2-3 |
CNC EDM | Creating complex shapes | Hardened steel, titanium | 3-5 |
Frequently Asked Questions (FAQ)
-
Q: What is the difference between CNC and conventional machining?
A: CNC machining uses computer-controlled machines to automate the manufacturing process, while conventional machining relies on manual operation of machine tools by skilled machinists. -
Q: Can CNC machines work with any material?
A: CNC machines can work with a wide range of materials, including metals, plastics, wood, and composites. However, some machines may have limitations based on the specific cutting tools and techniques used. -
Q: How long does it take to program a CNC machine?
A: The time required to program a CNC machine depends on the complexity of the part being manufactured and the experience of the programmer. Simple parts may take a few hours, while more complex parts can take several days or weeks. -
Q: Are CNC machines expensive to operate and maintain?
A: While CNC machines can be expensive to purchase initially, they can offer significant cost savings in the long run through increased efficiency, reduced labor costs, and improved quality. Regular maintenance and occasional repairs are necessary to ensure optimal performance and longevity. -
Q: What skills are required to operate a CNC machine?
A: Operating a CNC machine requires a combination of technical skills, including knowledge of CAD software, G-code programming, and machine tool operation, as well as problem-solving and attention to detail. Many employers prefer candidates with formal training or apprenticeship experience in CNC machining.
Conclusion
CNC machining has transformed the manufacturing industry, enabling the production of highly precise and complex parts with unparalleled efficiency and consistency. From its origins in the 1940s to its current state-of-the-art applications, CNC technology continues to evolve and adapt to meet the ever-changing needs of modern manufacturing.
As automation, digitalization, and sustainability become increasingly important drivers of industrial innovation, the future of CNC machining looks promising. By embracing new technologies and best practices, manufacturers can harness the full potential of CNC machining to create better products, streamline operations, and stay competitive in a global marketplace.
No responses yet