Introduction
An Arc Flash is a dangerous and potentially deadly electrical event that can occur in various industrial settings, such as power plants, manufacturing facilities, and construction sites. It is crucial for workers, managers, and safety professionals to understand the risks associated with arc flash and the preventive measures that can be taken to ensure a safe working environment.
In this comprehensive article, we will explore the definition of arc flash, its causes, and the preventive measures that can be implemented to minimize the risk of occurrence. We will also discuss the importance of proper training, personal protective equipment (PPE), and adherence to safety standards and regulations.
What is Arc Flash?
Definition and Explanation
An arc flash is an intense burst of energy caused by an electrical arc, which occurs when there is a fault or short circuit in an electrical system. This event can generate extreme heat, bright light, and a powerful pressure wave that can cause severe burns, injuries, and even death to anyone in close proximity.
The temperature of an arc flash can reach up to 35,000 degrees Fahrenheit (19,426 degrees Celsius), which is four times hotter than the surface of the sun. The intense heat can vaporize metal, causing molten projectiles to be expelled at high velocities. The pressure wave generated by an arc flash can be strong enough to throw a person across a room, resulting in blunt force trauma or impact injuries.
Difference between Arc Flash and Electric Shock
It is important to distinguish between an arc flash and an electric shock. While both events involve electricity, they have different characteristics and effects on the human body.
An electric shock occurs when electrical current passes through a person’s body, causing muscle contractions, burns, and potentially fatal heart arrhythmias. The severity of an electric shock depends on factors such as the voltage, current, and duration of exposure.
On the other hand, an arc flash does not require direct contact with an electrical source. The intense heat, light, and pressure wave generated by an arc flash can cause severe injuries even if the person is not in direct contact with the electrical equipment.
Causes of Arc Flash
Several factors can contribute to the occurrence of an arc flash in an electrical system. Understanding these causes is essential for identifying potential hazards and implementing preventive measures.
Inadequate Maintenance and Testing
One of the primary causes of arc flash incidents is inadequate maintenance and testing of electrical equipment. Over time, electrical components can deteriorate, leading to increased resistance, overheating, and potential failure. Regular maintenance, such as cleaning, tightening connections, and replacing worn or damaged parts, can help prevent arc flash incidents.
Additionally, periodic testing of electrical equipment, such as insulation resistance testing and infrared thermography, can identify potential issues before they lead to an arc flash event.
Improper Work Practices
Improper work practices, such as working on energized equipment without proper safety precautions, can significantly increase the risk of an arc flash. Some examples of improper work practices include:
- Failure to follow lockout/tagout procedures
- Using improper tools or equipment
- Lack of proper PPE
- Working on energized equipment without proper justification or authorization
Equipment Failure and Malfunction
Equipment failure and malfunction can also contribute to the occurrence of an arc flash. Some common causes of equipment failure include:
- Insulation breakdown
- Loose or corroded connections
- Overloading or short-circuiting
- Mechanical damage or wear
Regular inspections and preventive maintenance can help identify and address potential equipment issues before they lead to an arc flash event.
Dust, Moisture, and Other Environmental Factors
Environmental factors, such as dust, moisture, and corrosive atmospheres, can contribute to the deterioration of electrical equipment and increase the risk of an arc flash. Dust and moisture can accumulate on electrical components, leading to insulation breakdown and short-circuiting. Corrosive atmospheres can accelerate the degradation of metal parts, resulting in increased resistance and overheating.
Proper enclosure and protection of electrical equipment, as well as regular cleaning and maintenance, can help mitigate the effects of environmental factors on arc flash risk.
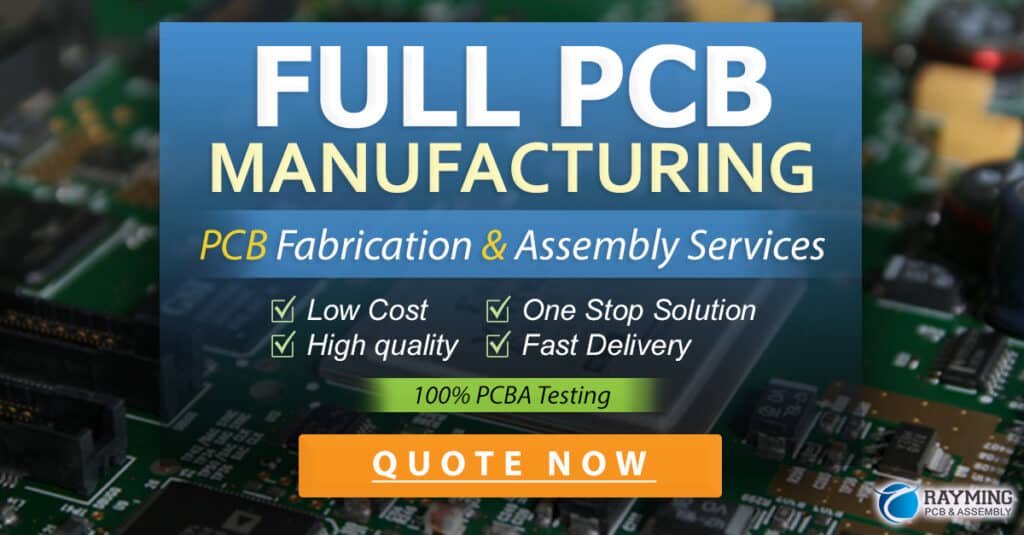
Preventive Measures
To minimize the risk of arc flash incidents and ensure a safe working environment, several preventive measures can be implemented. These measures include proper training, use of personal protective equipment (PPE), adherence to safety standards and regulations, and implementation of engineering controls.
Training and Education
Proper training and education are essential for preventing arc flash incidents. All workers who may be exposed to electrical hazards should receive training on:
- The hazards associated with arc flash
- Proper work practices and procedures
- Proper use and maintenance of PPE
- Emergency response and first aid
Training should be conducted by qualified instructors and should be regularly updated to reflect changes in safety standards and best practices.
Personal Protective Equipment (PPE)
The use of appropriate PPE is critical for protecting workers from the hazards of arc flash. PPE for arc flash protection typically includes:
- Arc-rated clothing, such as shirts, pants, and coveralls
- Arc-rated face shields and hoods
- Insulated gloves and leather protectors
- Safety glasses or goggles
- Hearing protection
- Voltage-rated tools and equipment
The selection of PPE should be based on the results of an arc flash hazard analysis, which determines the incident energy level and the required level of protection.
Adherence to Safety Standards and Regulations
Adherence to safety standards and regulations is essential for preventing arc flash incidents and ensuring a safe working environment. Some of the key standards and regulations related to arc flash safety include:
- NFPA 70E: Standard for Electrical Safety in the Workplace
- OSHA 29 CFR 1910 Subpart S: Electrical standards
- IEEE 1584: Guide for Performing Arc-Flash Hazard Calculations
These standards provide guidelines for safe work practices, PPE requirements, and methods for calculating arc flash hazard levels.
Engineering Controls
Engineering controls can be implemented to reduce the risk of arc flash incidents and minimize the potential for injury. Some examples of engineering controls include:
- Installing current-limiting fuses or circuit breakers
- Using arc-resistant switchgear and motor control centers
- Providing remote operation and monitoring of electrical equipment
- Installing insulation and barriers to prevent accidental contact
- Implementing an effective grounding system
By incorporating engineering controls into the design and operation of electrical systems, the risk of arc flash incidents can be significantly reduced.
Arc Flash Hazard Analysis
An arc flash hazard analysis is a critical component of an effective arc flash safety program. The purpose of the analysis is to determine the incident energy level at various points in an electrical system and to identify the appropriate level of PPE required for safe work.
Methods for Calculating Incident Energy
There are several methods for calculating the incident energy level associated with an arc flash. The most widely used methods are:
- IEEE 1584 method
- NFPA 70E tables method
The IEEE 1584 method involves collecting data on the electrical system, such as voltage, available fault current, and clearing time, and using complex equations to calculate the incident energy level.
The NFPA 70E tables method provides a simplified approach to determining the incident energy level based on the equipment type, voltage, and available fault current.
Importance of Regular Updates
It is important to conduct regular updates to the arc flash hazard analysis to ensure that the incident energy levels and PPE requirements remain accurate. Changes to the electrical system, such as the addition of new equipment or modifications to existing equipment, can affect the incident energy levels and require updates to the analysis.
Regular updates to the arc flash hazard analysis should be conducted at least every five years or whenever significant changes are made to the electrical system.
Conclusion
Arc flash is a serious and potentially fatal hazard that can occur in various industrial settings. Understanding the causes of arc flash and implementing effective preventive measures are essential for ensuring a safe working environment.
By providing proper training and education, requiring the use of appropriate PPE, adhering to safety standards and regulations, and implementing engineering controls, the risk of arc flash incidents can be significantly reduced.
Regular updates to the arc flash hazard analysis are also critical for maintaining an accurate understanding of the incident energy levels and PPE requirements associated with different parts of the electrical system.
By prioritizing arc flash safety and taking a proactive approach to prevention, organizations can protect their workers and maintain a safe and productive workplace.
Frequently Asked Questions (FAQ)
- What is the difference between arc flash and arc blast?
An arc flash is the intense heat, light, and pressure wave generated by an electrical arc, while an arc blast is the physical force that can throw a person or object across a room. Arc flash and arc blast often occur together during an arc flash incident.
- Can arc flash occur in low-voltage systems?
Yes, arc flash can occur in low-voltage systems, such as 480V or 120V systems. While the incident energy levels may be lower than in high-voltage systems, low-voltage arc flash events can still cause serious injuries and damage.
- How often should workers receive arc flash safety training?
Workers should receive arc flash safety training upon initial assignment to a job that involves potential exposure to electrical hazards, and at least every three years thereafter. Additional training may be required if there are changes to the electrical system, work practices, or safety standards.
- What is the purpose of arc-rated clothing?
Arc-rated clothing is designed to protect workers from the intense heat and flames generated by an arc flash. The clothing is made from materials that have been tested and rated for their ability to resist ignition and provide insulation from heat.
- Can arc flash be prevented entirely?
While it is not possible to prevent arc flash incidents entirely, the risk can be significantly reduced through proper training, use of PPE, adherence to safety standards, and implementation of engineering controls. By taking a proactive approach to arc flash safety, organizations can minimize the likelihood of incidents and protect their workers from harm.
Voltage Level | Typical Arc Flash Boundary |
---|---|
208V | 5 feet |
480V | 10 feet |
4,160V | 20 feet |
13,800V | 50 feet |
Table 1: Typical arc flash boundaries for different voltage levels (based on NFPA 70E guidelines)
No responses yet