Introduction to Peelable Soldermask
Peelable soldermask, also known as temporary or removable soldermask, is a specialized coating applied to printed circuit boards (PCBs) to protect the copper traces and pads during the soldering process. Unlike permanent soldermask, which remains on the PCB throughout its lifespan, peelable soldermask is designed to be easily removed after soldering, leaving behind clean and exposed copper surfaces for further processing or inspection.
How Peelable Soldermask Works
Peelable soldermask is typically applied as a liquid or film to the PCB surface, covering the areas that need protection during soldering. The mask is then cured using heat or ultraviolet (UV) light, forming a solid, protective layer. After soldering, the peelable soldermask can be easily removed by hand or with the help of a peeling tool, revealing the underlying copper traces and pads.
Advantages of Using Peelable Soldermask
There are several advantages to using peelable soldermask in PCB manufacturing:
-
Temporary protection: Peelable soldermask provides temporary protection to the copper traces and pads during soldering, preventing bridging, shorts, and other soldering defects.
-
Easy removal: Unlike permanent soldermask, peelable soldermask can be easily removed after soldering, allowing for further processing or inspection of the PCB.
-
Cost-effective: Peelable soldermask is often more cost-effective than permanent soldermask, especially for prototyping or low-volume production runs.
-
Flexibility: Peelable soldermask can be applied selectively to specific areas of the PCB, providing protection where needed while leaving other areas exposed for testing or debugging purposes.
Types of Peelable Soldermask
There are two main types of peelable soldermask: liquid and film.
Liquid Peelable Soldermask
Liquid peelable soldermask is applied to the PCB surface using a screen printing process. The liquid mask is dispensed onto the PCB and then spread evenly using a squeegee. After curing, the mask forms a solid, protective layer over the copper traces and pads.
Advantages of liquid peelable soldermask:
– Easy to apply using standard screen printing equipment
– Can be applied selectively to specific areas of the PCB
– Provides good coverage and protection
Disadvantages of liquid peelable soldermask:
– May require multiple coats to achieve adequate thickness
– Curing process can be time-consuming
– May leave residue on the PCB surface after removal
Film Peelable Soldermask
Film peelable soldermask, also known as dry film soldermask, is applied to the PCB surface as a pre-formed, solid film. The film is laminated onto the PCB using heat and pressure, and then cured using UV light.
Advantages of film peelable soldermask:
– Provides consistent thickness and coverage
– Fast and easy to apply using standard lamination equipment
– Minimal residue after removal
Disadvantages of film peelable soldermask:
– May be more expensive than liquid peelable soldermask
– Less flexible for selective application to specific areas of the PCB
Applications of Peelable Soldermask
Peelable soldermask is used in various PCB manufacturing applications, such as:
-
Prototyping: Peelable soldermask is often used in PCB Prototyping to provide temporary protection during soldering, allowing for easy removal and inspection of the board.
-
Low-volume production: For low-volume PCB production runs, peelable soldermask can be a cost-effective alternative to permanent soldermask.
-
Rework and repair: Peelable soldermask can be used to protect specific areas of a PCB during rework or repair processes, allowing for targeted soldering without affecting other components.
-
Selective soldering: In some cases, peelable soldermask can be used to selectively expose certain areas of a PCB for soldering, while protecting others.
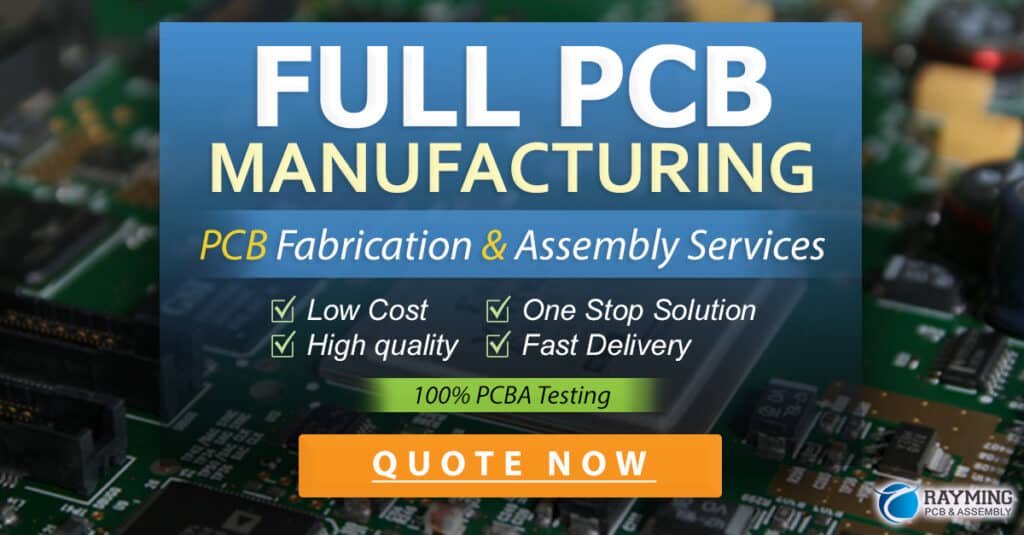
Peelable Soldermask Application Process
The application process for peelable soldermask varies depending on the type of mask being used (liquid or film), but generally follows these steps:
-
PCB Cleaning: The PCB surface is cleaned to remove any contaminants or debris that could affect the adhesion of the soldermask.
-
Soldermask application: The peelable soldermask is applied to the PCB surface, either by screen printing (for liquid mask) or lamination (for film mask).
-
Curing: The soldermask is cured using heat or UV light, depending on the type of mask being used. This process hardens the mask and ensures good adhesion to the PCB surface.
-
Soldering: The PCB is then soldered, with the peelable soldermask protecting the copper traces and pads from bridging, shorts, and other defects.
-
Mask removal: After soldering, the peelable soldermask is removed by hand or with the help of a peeling tool, exposing the clean copper surfaces beneath.
Choosing the Right Peelable Soldermask
When selecting a peelable soldermask for your PCB manufacturing process, consider the following factors:
-
Compatibility: Ensure that the peelable soldermask is compatible with your PCB Material, soldering process, and any other chemicals or materials used in your manufacturing process.
-
Ease of removal: Choose a peelable soldermask that can be easily removed after soldering, without leaving residue or damaging the PCB surface.
-
Thermal stability: Select a peelable soldermask that can withstand the temperatures involved in your soldering process without degrading or losing its protective properties.
-
Thickness: Consider the required thickness of the peelable soldermask for your application, taking into account the depth of the copper traces and pads, as well as the soldering process being used.
-
Cost: Evaluate the cost of the peelable soldermask in relation to your overall PCB manufacturing budget, considering factors such as the type of mask (liquid or film), the volume of PCBs being produced, and the ease of application and removal.
Troubleshooting Peelable Soldermask Issues
While peelable soldermask is generally easy to use and remove, some common issues may arise during the application and removal process:
-
Poor adhesion: If the peelable soldermask does not adhere properly to the PCB surface, it may not provide adequate protection during soldering. This can be caused by contaminants on the PCB surface, incompatible materials, or incorrect curing parameters.
-
Difficult removal: In some cases, the peelable soldermask may be difficult to remove after soldering, leaving residue or damaging the PCB surface. This can be caused by over-curing the mask, using an incompatible mask material, or incorrect removal techniques.
-
Incomplete coverage: If the peelable soldermask does not provide complete coverage of the desired areas, it may not adequately protect the copper traces and pads during soldering. This can be caused by incorrect application techniques, insufficient mask thickness, or poor mask flow properties.
To troubleshoot these issues, consider the following:
- Ensure that the PCB surface is clean and free of contaminants before applying the peelable soldermask.
- Verify that the peelable soldermask is compatible with your PCB material and soldering process.
- Follow the manufacturer’s recommended application and curing parameters for the specific peelable soldermask being used.
- Use the correct removal techniques and tools to avoid damaging the PCB surface or leaving residue behind.
Frequently Asked Questions (FAQ)
-
Can peelable soldermask be used on any type of PCB?
Peelable soldermask can be used on most types of PCBs, including rigid and flexible boards. However, it is essential to ensure that the specific peelable soldermask being used is compatible with the PCB material and the soldering process being employed. -
How long does peelable soldermask take to cure?
The curing time for peelable soldermask varies depending on the type of mask being used (liquid or film) and the curing method (heat or UV light). Typically, liquid peelable soldermask takes longer to cure than film masks, with curing times ranging from several minutes to an hour or more. -
Can peelable soldermask be reused?
In most cases, peelable soldermask is designed for single use and should be discarded after removal from the PCB. Attempting to reuse peelable soldermask may result in poor adhesion, incomplete coverage, or other issues that could compromise the protection of the PCB during soldering. -
Is peelable soldermask suitable for high-volume PCB production?
Peelable soldermask is more commonly used in prototyping, low-volume production, and rework/repair applications. For high-volume PCB production, permanent soldermask is often more suitable, as it provides long-term protection and durability without the need for removal. -
How do I choose the right thickness for my peelable soldermask?
The appropriate thickness for peelable soldermask depends on factors such as the depth of the copper traces and pads, the soldering process being used, and the level of protection required. In general, thicker masks provide better protection but may be more difficult to remove. Consult with your peelable soldermask supplier or manufacturer for guidance on selecting the optimal thickness for your specific application.
Conclusion
Peelable soldermask is a valuable tool in PCB manufacturing, providing temporary protection for copper traces and pads during the soldering process. By understanding the types, applications, and proper use of peelable soldermask, PCB Manufacturers can improve the quality and reliability of their soldering operations while minimizing the risk of defects and damage to the board.
When selecting and using peelable soldermask, it is essential to consider factors such as compatibility, ease of removal, thermal stability, thickness, and cost. By following best practices for application, curing, and removal, and troubleshooting any issues that may arise, PCB manufacturers can effectively incorporate peelable soldermask into their processes and achieve optimal results.
No responses yet