Introduction to Aluminum PCBs
An aluminum PCB, or printed circuit board, is a specialized type of PCB that uses aluminum as the base material instead of the more commonly used FR-4 fiberglass. Aluminum PCBs offer several unique advantages over traditional PCBs, making them ideal for certain applications.
Aluminum PCBs should not be confused with flexible printed circuits (FPCs), which are thin, flexible circuits made from polyimide or other flexible substrates. While both aluminum PCBs and FPCs offer flexibility, they are distinct technologies with different characteristics and use cases.
Advantages of Aluminum PCBs
Excellent Heat Dissipation
One of the primary advantages of aluminum PCBs is their excellent heat dissipation properties. Aluminum has a thermal conductivity of about 205 W/(m·K), which is significantly higher than the thermal conductivity of FR-4, which is around 0.3 W/(m·K). This means that aluminum PCBs can efficiently transfer heat away from components, helping to prevent overheating and improve reliability.
Lightweight and Durable
Aluminum PCBs are also lightweight and durable compared to traditional PCBs. Aluminum has a density of about 2.7 g/cm³, while FR-4 has a density of about 1.85 g/cm³. Despite being lighter, aluminum is a strong and resilient material that can withstand shocks, vibrations, and other mechanical stresses.
Flexible and Conformable
Another advantage of aluminum PCBs is their flexibility and conformability. While not as flexible as FPCs, aluminum PCBs can be bent and shaped to fit into tight spaces or conform to irregular surfaces. This makes them well-suited for applications where space is limited or where the PCB needs to be mounted on a curved or angled surface.
Cost-effective for High-power Applications
For high-power applications that require efficient heat dissipation, aluminum PCBs can be a cost-effective solution compared to other heat management methods, such as heat sinks or fans. By using an aluminum PCB, designers can often eliminate the need for additional cooling components, reducing overall system cost and complexity.
Applications of Aluminum PCBs
LED Lighting
Aluminum PCBs are commonly used in LED lighting applications, where efficient heat dissipation is critical for ensuring long-term reliability and performance. LEDs generate a significant amount of heat, and if this heat is not effectively removed, it can cause the LEDs to degrade or fail prematurely. By using an aluminum PCB, designers can help ensure that the heat generated by the LEDs is quickly and efficiently transferred away from the components.
Automotive Electronics
In the automotive industry, aluminum PCBs are used in a variety of applications, including engine control units, power inverters, and battery management systems. These applications often require PCBs that can withstand high temperatures, vibrations, and other harsh environmental conditions. Aluminum PCBs are well-suited for these challenges due to their excellent heat dissipation properties and durability.
Power Electronics
Power electronics applications, such as motor drives, power supplies, and solar inverters, also benefit from the use of aluminum PCBs. These applications often involve high currents and voltages, which can generate significant amounts of heat. By using an aluminum PCB, designers can help ensure that this heat is effectively dissipated, improving system reliability and performance.
Aerospace and Defense
In the aerospace and defense industries, aluminum PCBs are used in a range of applications, including avionics, radar systems, and satellite communications. These applications often require PCBs that are lightweight, durable, and able to withstand extreme environmental conditions. Aluminum PCBs are well-suited for these requirements due to their unique properties and characteristics.
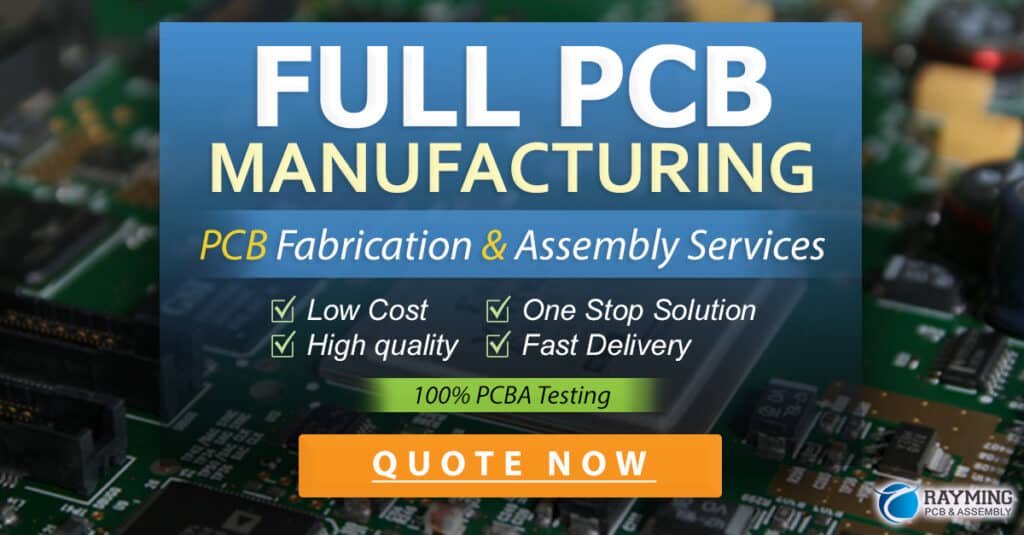
Designing with Aluminum PCBs
Thermal Management Considerations
When designing with aluminum PCBs, thermal management is a key consideration. While aluminum PCBs offer excellent heat dissipation properties, designers must still carefully consider the thermal requirements of their application and design the PCB accordingly.
One important factor to consider is the thickness of the aluminum base layer. A thicker aluminum layer will provide better heat dissipation but may also increase the overall thickness and weight of the PCB. Designers must balance these factors based on the specific requirements of their application.
Another consideration is the placement and layout of components on the PCB. High-power components that generate significant amounts of heat should be placed in areas of the PCB where they can be effectively cooled, such as near the edges of the board or in areas with good airflow.
Electrical Insulation
Another important consideration when designing with aluminum PCBs is electrical insulation. While aluminum is an excellent conductor of heat, it is also an electrical conductor. To prevent short circuits and other electrical issues, the aluminum base layer must be electrically isolated from the copper traces and components on the PCB.
This is typically achieved by applying a thin layer of dielectric material, such as polyimide or epoxy, between the aluminum and copper layers. The thickness and type of dielectric material used will depend on the specific requirements of the application, such as the operating voltage and temperature range.
Mechanical Design Considerations
When designing aluminum PCBs, mechanical design considerations are also important. While aluminum PCBs are flexible and conformable, they are not as flexible as FPCs and can be prone to cracking or breaking if bent too far or too frequently.
Designers must carefully consider the mechanical requirements of their application and design the PCB accordingly. This may involve adding additional support structures, such as stiffeners or reinforcement ribs, to areas of the PCB that will be subjected to mechanical stress.
Manufacturing Process
The manufacturing process for aluminum PCBs is similar to that of traditional PCBs, with a few key differences. The first step is to create the aluminum base layer, which is typically done by cutting a sheet of aluminum to the desired size and shape.
Next, a layer of dielectric material is applied to one or both sides of the aluminum base layer. This is typically done using a lamination process, where the dielectric material is heated and pressed onto the aluminum surface.
Once the dielectric layer is in place, the copper traces and components are added using standard PCB manufacturing processes, such as etching, plating, and soldering.
Frequently Asked Questions (FAQ)
What is the difference between an aluminum PCB and a standard PCB?
The main difference between an aluminum PCB and a standard PCB is the base material. Aluminum PCBs use an aluminum base layer, while standard PCBs use an FR-4 fiberglass base layer. Aluminum PCBs offer several advantages over standard PCBs, including better heat dissipation, lighter weight, and greater durability.
Can aluminum PCBs be used for all applications?
No, aluminum PCBs are not suitable for all applications. They are best suited for applications that require efficient heat dissipation, lightweight construction, or flexibility. For applications that do not have these requirements, standard PCBs may be a more cost-effective solution.
How much does an aluminum PCB cost compared to a standard PCB?
The cost of an aluminum PCB compared to a standard PCB can vary depending on the specific requirements of the application. In general, aluminum PCBs tend to be more expensive than standard PCBs due to the higher cost of the aluminum base material and the additional manufacturing steps required. However, for applications that require efficient heat dissipation or other unique properties, the added cost of an aluminum PCB may be justified by improved system performance and reliability.
Can aluminum PCBs be used in high-voltage applications?
Yes, aluminum PCBs can be used in high-voltage applications, but special considerations must be taken to ensure proper electrical insulation between the aluminum base layer and the copper traces and components. This typically involves using a thicker or higher-quality dielectric material, as well as additional design and manufacturing techniques to prevent electrical breakdown or arcing.
Are aluminum PCBs environmentally friendly?
Aluminum PCBs can be considered more environmentally friendly than standard PCBs in some respects. Aluminum is a readily recyclable material, and the use of aluminum PCBs can help reduce the overall weight and size of electronic devices, which can reduce transportation costs and energy consumption. However, the manufacturing process for aluminum PCBs does involve the use of chemicals and energy, so the overall environmental impact must be carefully considered.
Conclusion
Aluminum PCBs offer a unique set of advantages over traditional PCBs, including excellent heat dissipation, lightweight construction, and flexibility. These properties make them well-suited for a range of applications, including LED lighting, automotive electronics, power electronics, and aerospace and defense.
When designing with aluminum PCBs, careful consideration must be given to thermal management, electrical insulation, and mechanical design. The manufacturing process for aluminum PCBs is similar to that of standard PCBs, with the added steps of creating the aluminum base layer and applying a dielectric material.
While aluminum PCBs are not suitable for all applications, they can provide significant benefits in terms of performance, reliability, and cost for certain types of projects. As the demand for high-performance, lightweight, and durable electronic devices continues to grow, aluminum PCBs are likely to play an increasingly important role in the electronics industry.
No responses yet