Introduction to Burn Testing
Burn-testing, also known as burn-in testing, is a critical process in the electronics industry that involves subjecting electronic components, devices, or systems to a period of operation under controlled conditions. The primary objective of burn testing is to identify and eliminate early-life failures, ensuring that the product meets the required quality standards and reliability expectations before being released to the market.
What is Burn Testing?
Burn testing is a type of stress testing that involves operating an electronic device or component at elevated temperatures, voltages, or currents for a specified duration. This process accelerates the aging of the device, allowing manufacturers to detect and address potential issues that may arise during the early stages of the product’s life cycle.
Why is Burn Testing Important?
Burn testing is essential for several reasons:
-
Early Failure Detection: Burn testing helps identify defects and weaknesses in electronic components that may lead to premature failure. By detecting these issues early, manufacturers can take corrective actions before the product reaches the end-user.
-
Improved Reliability: By eliminating early-life failures, burn testing enhances the overall reliability of the electronic device or system. This translates to fewer field failures, reduced warranty claims, and improved customer satisfaction.
-
Cost Savings: Identifying and resolving issues during the manufacturing process is more cost-effective than addressing them after the product has been released. Burn testing helps minimize the costs associated with product recalls, repairs, and replacements.
-
Compliance with Standards: Many industries have specific standards and regulations that require burn testing as part of the quality assurance process. Adhering to these standards ensures that the product meets the necessary safety and performance criteria.
Types of Burn Testing
There are several types of burn testing employed in the electronics industry, each with its specific purpose and methodology.
High-Temperature Operating Life (HTOL) Testing
HTOL testing involves operating the electronic device or component at an elevated temperature, typically above its maximum rated operating temperature, for an extended period. This test accelerates the aging process and helps identify temperature-related failures.
Parameter | Typical Value |
---|---|
Temperature | 125°C to 150°C |
Duration | 500 to 1000 hours |
Voltage | Nominal or slightly elevated |
Highly Accelerated Stress Test (HAST)
HAST is a type of burn testing that combines high temperature and high humidity to accelerate the aging process. This test is particularly useful for identifying moisture-related failures in electronic components.
Parameter | Typical Value |
---|---|
Temperature | 130°C to 110°C |
Relative Humidity | 85% RH |
Pressure | 2 to 3 atm |
Duration | 96 to 264 hours |
Burn-In Testing
Burn-in testing involves operating the electronic device or component at its maximum rated conditions (temperature, voltage, and current) for a specified duration. This test helps identify infant mortality failures and stabilize the device’s performance.
Parameter | Typical Value |
---|---|
Temperature | Maximum rated operating temperature |
Voltage | Maximum rated voltage |
Current | Maximum rated current |
Duration | 24 to 168 hours |
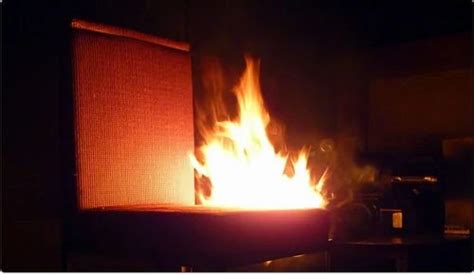
Burn Testing Methodology
The burn testing methodology involves several steps to ensure that the process is carried out effectively and yields reliable results.
1. Define Test Conditions
The first step in burn testing is to define the test conditions based on the device’s specifications, industry standards, and the type of failure modes being targeted. This includes determining the temperature, voltage, current, humidity, and duration of the test.
2. Set Up Test Equipment
Next, the test equipment must be set up according to the defined test conditions. This may involve using environmental chambers, power supplies, test fixtures, and monitoring systems to control and measure the device’s performance during the test.
3. Perform Pre-Test Characterization
Before subjecting the device to burn testing, it is essential to perform a pre-test characterization to establish a baseline for its performance. This typically involves measuring key parameters such as functionality, electrical characteristics, and physical attributes.
4. Conduct Burn Testing
Once the test setup is complete and the pre-test characterization is done, the actual burn testing can begin. The device is subjected to the defined test conditions for the specified duration, with continuous monitoring to detect any anomalies or failures.
5. Perform Post-Test Characterization
After the burn testing is complete, a post-test characterization is performed to assess the device’s performance and compare it with the pre-test results. This helps identify any degradation or changes in the device’s characteristics due to the burn testing.
6. Analyze Results and Take Corrective Actions
Finally, the test results are analyzed to determine the device’s reliability and identify any potential issues. If failures or anomalies are detected, root cause analysis is performed, and corrective actions are taken to improve the device’s design, manufacturing process, or material selection.
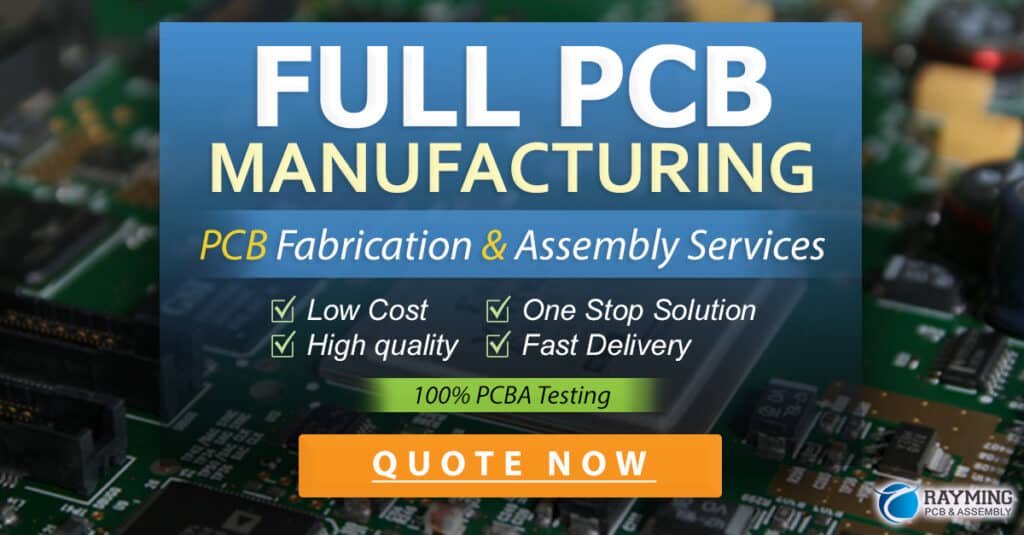
Benefits of Burn Testing
Implementing burn testing in the electronics manufacturing process offers several benefits:
-
Improved Product Quality: By identifying and eliminating early-life failures, burn testing helps improve the overall quality of the electronic device or component. This results in fewer defects and a more reliable product.
-
Reduced Field Failures: Burn testing helps minimize the occurrence of field failures, as devices that pass the test are less likely to experience premature failure during normal operation. This leads to improved customer satisfaction and reduced warranty claims.
-
Enhanced Reliability: By subjecting devices to accelerated aging conditions, burn testing provides valuable insights into their long-term reliability. This information can be used to make design improvements and optimize the manufacturing process.
-
Compliance with Standards: Burn testing helps ensure that electronic devices meet the necessary industry standards and regulations for safety, performance, and reliability. This is particularly important for products used in critical applications such as aerospace, automotive, and medical devices.
-
Cost Savings: Identifying and resolving issues during the manufacturing process through burn testing is more cost-effective than addressing them after the product has been released. This helps minimize the costs associated with product recalls, repairs, and replacements.
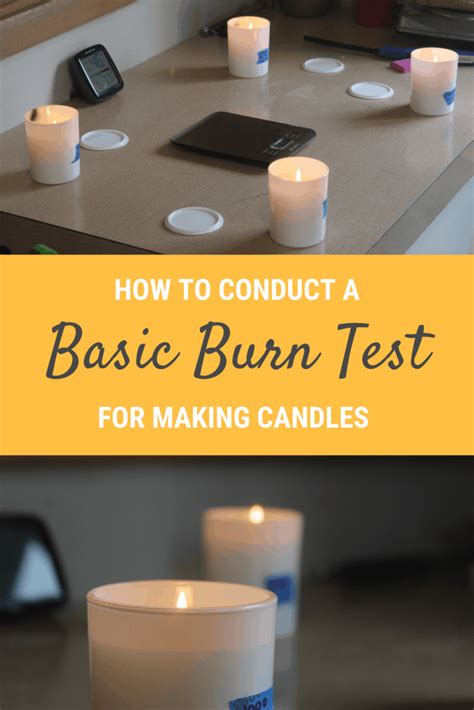
Challenges and Considerations
While burn testing offers numerous benefits, there are also some challenges and considerations to keep in mind:
-
Test Duration: Burn testing can be time-consuming, particularly for tests that require extended durations such as HTOL testing. This can impact production schedules and time-to-market.
-
Test Coverage: Ensuring adequate test coverage can be challenging, as it requires selecting the appropriate test conditions and sample sizes to represent the entire population of devices. Insufficient test coverage may lead to undetected failures.
-
Test Correlation: Correlating burn test results with actual field performance can be difficult, as the test conditions may not fully represent the real-world operating environment. This can lead to false positives or false negatives.
-
Cost: Implementing burn testing can be costly, as it requires specialized equipment, facilities, and trained personnel. The cost of testing must be balanced against the potential benefits in terms of improved reliability and reduced field failures.
Best Practices for Burn Testing
To ensure the effectiveness of burn testing and maximize its benefits, consider the following best practices:
-
Define Clear Objectives: Establish clear objectives for the burn testing process, including the types of failures being targeted, the desired level of reliability, and the acceptance criteria.
-
Select Appropriate Test Conditions: Choose test conditions that are representative of the device’s intended operating environment and are sufficient to accelerate the aging process without introducing unrealistic failures.
-
Use Statistical Sampling: Employ statistical sampling techniques to select a representative sample of devices for testing. This helps ensure that the test results are valid and can be extrapolated to the entire population.
-
Monitor Test Progress: Continuously monitor the burn testing process to detect any anomalies or failures in real-time. This allows for prompt root cause analysis and corrective actions.
-
Document and Analyze Results: Maintain detailed documentation of the test setup, conditions, and results. Analyze the data to identify trends, failure modes, and areas for improvement.
-
Incorporate Feedback: Use the insights gained from burn testing to make design improvements, optimize manufacturing processes, and enhance the overall reliability of the electronic device or component.
Frequently Asked Questions (FAQ)
-
Q: How long does burn testing typically take?
A: The duration of burn testing depends on the type of test and the specific requirements of the electronic device or component. HTOL testing can range from 500 to 1000 hours, while burn-in testing may last anywhere from 24 to 168 hours. -
Q: Is burn testing required for all electronic devices?
A: While burn testing is highly recommended for most electronic devices, the specific requirements may vary depending on the industry, application, and relevant standards. Some industries, such as aerospace and automotive, have stringent burn testing requirements to ensure the reliability and safety of the devices. -
Q: Can burn testing guarantee zero field failures?
A: While burn testing can significantly reduce the occurrence of field failures, it cannot guarantee zero failures. The effectiveness of burn testing depends on factors such as test coverage, test conditions, and the representativeness of the sample. Additionally, some failures may occur due to factors not addressed by burn testing, such as user misuse or environmental factors. -
Q: How much does burn testing cost?
A: The cost of burn testing varies depending on factors such as the type of test, the duration, the equipment required, and the number of devices being tested. It is important to consider the cost of testing in relation to the potential benefits, such as improved reliability and reduced field failures. -
Q: Can burn testing be performed in-house or is it typically outsourced?
A: Burn testing can be performed either in-house or outsourced to specialized testing facilities. The decision to perform burn testing in-house or outsource it depends on factors such as the availability of equipment, expertise, and resources. Outsourcing burn testing can be advantageous for companies that lack the necessary infrastructure or expertise, while in-house testing allows for greater control and flexibility.
Conclusion
Burn testing is a critical process in the electronics industry that helps identify and eliminate early-life failures, ensuring the reliability and quality of electronic devices and components. By subjecting devices to accelerated aging conditions, burn testing provides valuable insights into their long-term performance and helps manufacturers make informed decisions regarding design, manufacturing, and material selection.
Implementing burn testing offers numerous benefits, including improved product quality, reduced field failures, enhanced reliability, compliance with standards, and cost savings. However, it is important to consider the challenges and best practices associated with burn testing to ensure its effectiveness and maximize its benefits.
By incorporating burn testing into their quality assurance processes, electronics manufacturers can deliver high-quality, reliable products that meet the expectations of their customers and comply with the necessary industry standards and regulations.
No responses yet