What Are Flexible and flex-rigid PCBs?
Flexible PCBs, also known as flex circuits, are thin, lightweight, and bendable circuit boards made from flexible plastic substrates, such as polyimide or polyester. These boards can be easily bent, twisted, or folded without damaging the electrical connections or components. Flex-rigid PCBs, on the other hand, combine both flexible and rigid sections in a single board, allowing for even greater design versatility and functionality.
Advantages of Flexible and Flex-Rigid PCBs
- Increased Flexibility: The ability to bend and fold allows for more compact and space-saving designs.
- Improved Durability: Flexible materials can withstand vibrations, shocks, and extreme temperatures better than rigid boards.
- Enhanced Design Freedom: Flexible and flex-rigid PCBs enable engineers to create complex, three-dimensional shapes and configurations.
- Reduced Weight and Size: The thin, lightweight nature of these boards helps minimize the overall weight and size of electronic devices.
- Improved Signal Integrity: Shorter signal paths and reduced EMI/RFI interference lead to better signal integrity and performance.
Flexible PCB Applications
Flexible and flex-rigid PCBs find applications in a wide range of industries, including:
- Consumer Electronics
- Medical Devices
- Automotive Industry
- Aerospace and Defense
- Industrial Automation
- Wearable Technology
Consumer Electronics
In the consumer electronics sector, flexible and flex-rigid PCBs are used in various devices, such as:
- Smartphones and tablets
- Laptops and computers
- Cameras and camcorders
- Gaming consoles and controllers
- Smart watches and fitness trackers
These PCBs enable manufacturers to create sleek, compact, and lightweight devices with improved functionality and durability. For example, in smartphones, flex circuits are used to connect the display, camera, and other components to the main board, allowing for thinner and more flexible designs.
Medical Devices
Flexible and flex-rigid PCBs play a crucial role in the development of advanced medical devices, such as:
- Implantable devices (pacemakers, defibrillators, neurostimulators)
- Wearable monitoring devices (ECG, EEG, blood pressure monitors)
- Diagnostic imaging equipment (X-ray, MRI, CT scanners)
- Surgical instruments and robotics
The flexibility and durability of these PCBs make them ideal for use in medical applications, where reliability and long-term performance are critical. Implantable devices, for instance, rely on flex circuits to provide a compact and biocompatible solution that can withstand the harsh environment inside the human body.
Automotive Industry
In the automotive industry, flexible and flex-rigid PCBs are used in various systems and components, such as:
- Infotainment systems and displays
- Driver assistance systems (ADAS)
- Engine control units (ECUs)
- Lighting and sensors
- Electric vehicles and hybrid powertrains
The ability of these PCBs to withstand vibrations, extreme temperatures, and harsh environmental conditions makes them well-suited for automotive applications. Flex-rigid PCBs, in particular, are commonly used in automotive electronics due to their ability to combine the benefits of both flexible and rigid sections, enabling more complex and integrated designs.
Aerospace and Defense
Flexible and flex-rigid PCBs are extensively used in the aerospace and defense industries for applications such as:
- Avionics systems
- Satellite communication
- Military radar and surveillance
- Unmanned aerial vehicles (UAVs)
- Soldier-worn electronics
The lightweight, compact, and durable nature of these PCBs makes them ideal for use in aerospace and defense applications, where space and weight constraints are critical. Flex circuits, for example, are used in satellite solar arrays to provide a lightweight and flexible solution for power generation in space.
Industrial Automation
In industrial automation, flexible and flex-rigid PCBs are used in various applications, such as:
- Robotics and motion control
- Machine vision systems
- Sensors and actuators
- Industrial networking and communication
- Process control and monitoring
The ability of these PCBs to withstand harsh industrial environments, including vibrations, shocks, and extreme temperatures, makes them well-suited for use in industrial automation. Flex-rigid PCBs, in particular, are commonly used in robotics and motion control applications, where they provide a reliable and flexible solution for connecting various components and subsystems.
Wearable Technology
Flexible and flex-rigid PCBs are essential components in the rapidly growing field of wearable technology, which includes devices such as:
- Smartwatches and fitness trackers
- Smart clothing and textiles
- Virtual and augmented reality headsets
- Medical and healthcare wearables
- Personal safety and security devices
The flexibility and lightweight nature of these PCBs make them ideal for use in wearable devices, where comfort and ergonomics are crucial. Flex circuits, for instance, are used in smart clothing to provide a seamless and unobtrusive integration of electronics into fabrics.
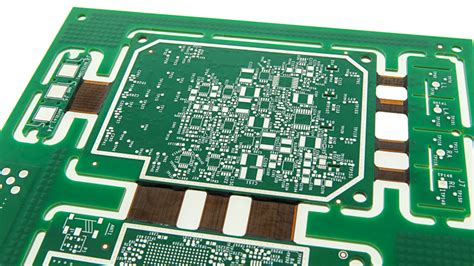
Best Practices for Designing Flexible and Flex-Rigid PCBs
To ensure optimal performance and reliability, engineers should follow best practices when designing flexible and flex-rigid PCBs:
-
Choose the right materials: Select flexible substrates and conductors that meet the specific requirements of the application, such as temperature range, chemical resistance, and mechanical properties.
-
Consider bend radius and fatigue: Design the PCB layout to minimize stress and strain on the flexible sections, and ensure that the bend radius is within the recommended range for the chosen materials.
-
Optimize component placement: Position components strategically to minimize the number of bends and folds in the flexible sections, and consider using surface mount technology (SMT) components for better compatibility with flex circuits.
-
Use appropriate connectors and strain relief: Select connectors that are specifically designed for use with flexible PCBs, and incorporate strain relief features to prevent damage to the board and components during flexing.
-
Conduct thorough testing and validation: Perform rigorous testing and validation procedures to ensure that the flexible or flex-rigid PCB meets the required performance, reliability, and durability standards for the intended application.
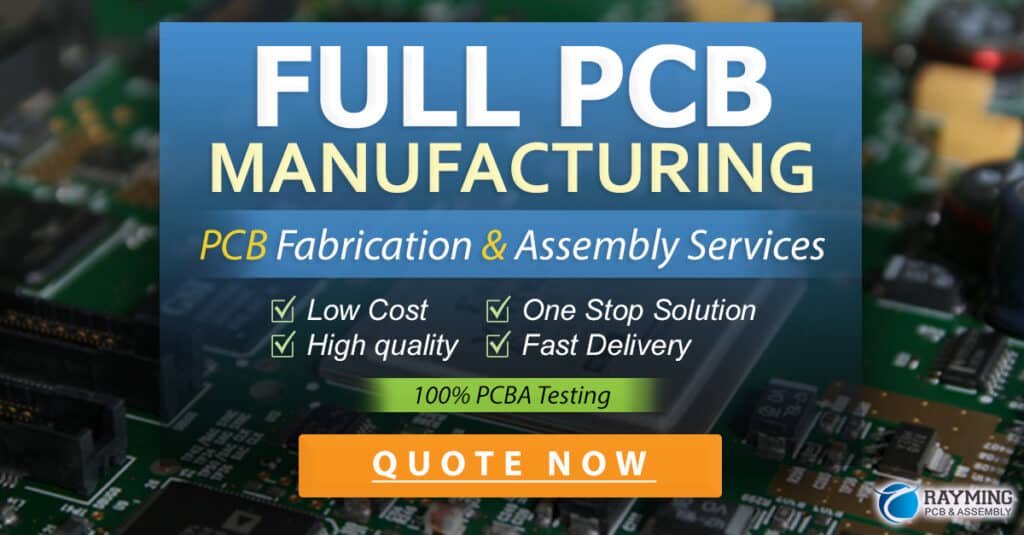
FAQ
-
Q: What is the difference between flexible and flex-rigid PCBs?
A: Flexible PCBs are entirely made from flexible materials and can be bent or folded, while flex-rigid PCBs combine both flexible and rigid sections in a single board. -
Q: What are the main advantages of using flexible and flex-rigid PCBs?
A: The main advantages include increased flexibility, improved durability, enhanced design freedom, reduced weight and size, and improved signal integrity. -
Q: In which industries are flexible and flex-rigid PCBs commonly used?
A: These PCBs are used in various industries, such as consumer electronics, medical devices, automotive, aerospace and defense, industrial automation, and wearable technology. -
Q: What are some best practices for designing flexible and flex-rigid PCBs?
A: Best practices include choosing the right materials, considering bend radius and fatigue, optimizing component placement, using appropriate connectors and strain relief, and conducting thorough testing and validation. -
Q: How do flexible and flex-rigid PCBs contribute to the development of wearable technology?
A: The flexibility and lightweight nature of these PCBs make them ideal for use in wearable devices, where comfort and ergonomics are crucial. They enable the seamless integration of electronics into fabrics and other wearable materials.
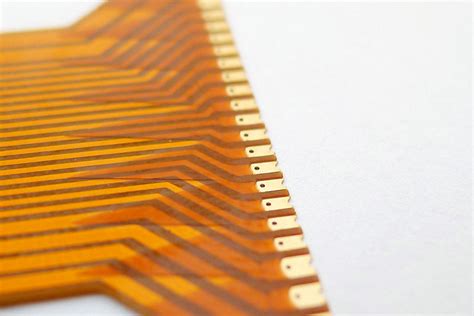
Conclusion
Flexible and flex-rigid PCBs offer numerous advantages over traditional rigid boards, making them essential components in a wide range of industries and applications. By leveraging the unique properties of these PCBs, engineers can create more compact, durable, and functionally advanced electronic devices. As technology continues to evolve, the demand for flexible and flex-rigid PCBs is expected to grow, driving further innovation and development in the electronics industry.
No responses yet