Introduction to Flexible and Flex-Rigid PCBs
Flexible and Flex-Rigid PCBs are becoming increasingly popular in the electronics industry due to their unique properties and versatile applications. These types of PCBs offer several advantages over traditional rigid PCBs, such as improved reliability, increased design flexibility, and reduced weight and size. In this article, we will explore the best ways to use Flexible and Flex-Rigid PCBs in various industries and applications.
What are Flexible PCBs?
Flexible PCBs, also known as flex circuits, are printed circuit boards made from flexible materials such as polyimide or polyester. They consist of a thin, flexible substrate with conductive traces and components mounted on one or both sides. Flexible PCBs can bend, twist, and fold without damaging the circuitry, making them ideal for applications that require movement or tight spaces.
What are Flex-Rigid PCBs?
Flex-Rigid PCBs are a combination of flexible and rigid PCBs, combining the best features of both types. They consist of one or more flexible layers bonded to one or more rigid layers, creating a single, integrated circuit board. Flex-Rigid PCBs offer the flexibility of flex circuits while providing the stability and durability of rigid PCBs in areas that require more support.
Advantages of Flexible and Flex-Rigid PCBs
Flexible and Flex-Rigid PCBs offer several advantages over traditional rigid PCBs, making them suitable for a wide range of applications. Some of the key benefits include:
-
Improved reliability: Flexible and Flex-Rigid PCBs can withstand vibrations, shocks, and thermal stresses better than rigid PCBs, reducing the risk of failure and increasing the overall reliability of the electronic device.
-
Increased design flexibility: The ability to bend, twist, and fold allows designers to create more complex and compact designs, saving space and reducing the overall size of the device.
-
Reduced weight: Flexible and Flex-Rigid PCBs are lighter than their rigid counterparts, making them ideal for applications where weight is a critical factor, such as aerospace and wearable electronics.
-
Enhanced signal integrity: The shorter trace lengths and reduced parasitic capacitance in Flexible and Flex-Rigid PCBs can improve signal integrity and reduce electromagnetic interference (EMI).
-
Cost-effective: Although the initial cost of Flexible and Flex-Rigid PCBs may be higher than rigid PCBs, they can reduce the overall cost of the device by eliminating the need for connectors, cables, and other components.
Applications of Flexible and Flex-Rigid PCBs
Flexible and Flex-Rigid PCBs are used in a wide range of industries and applications, including:
Consumer Electronics
Flexible and Flex-Rigid PCBs are commonly used in consumer electronics, such as smartphones, tablets, and wearable devices. They enable manufacturers to create thinner, lighter, and more compact designs while improving the overall reliability and functionality of the device.
Example: Smartwatches
Smartwatches require a compact, lightweight design that can withstand daily wear and tear. Flexible PCBs allow designers to create a slim, curved design that fits comfortably on the wrist while providing the necessary functionality and connectivity.
Medical Devices
Flexible and Flex-Rigid PCBs are increasingly used in medical devices, such as implantable sensors, medical wearables, and diagnostic equipment. They offer several advantages, including improved patient comfort, increased reliability, and reduced size and weight.
Example: Implantable Sensors
Implantable sensors, such as glucose monitors and pacemakers, require a compact, biocompatible design that can function reliably inside the human body. Flex-Rigid PCBs allow designers to create a small, flexible device that can conform to the body’s shape while providing the necessary support and protection for the electronic components.
Automotive Electronics
Flexible and Flex-Rigid PCBs are used in various automotive applications, such as dashboard displays, lighting systems, and sensors. They offer improved reliability, reduced weight, and increased design flexibility, making them ideal for the harsh operating conditions in vehicles.
Example: Dashboard Displays
Modern dashboard displays require a compact, flexible design that can fit into the limited space available in the vehicle. Flex-Rigid PCBs allow designers to create a thin, curved display that integrates seamlessly with the dashboard while providing the necessary support and connectivity for the electronic components.
Aerospace and Defense
Flexible and Flex-Rigid PCBs are used in aerospace and defense applications, such as satellites, aircraft, and military equipment. They offer several advantages, including reduced weight, increased reliability, and improved thermal management.
Example: Satellite Electronics
Satellites require lightweight, compact electronics that can withstand the harsh conditions of space, including extreme temperatures, radiation, and vibrations. Flexible PCBs allow designers to create a lightweight, compact design that can conform to the limited space available in the satellite while providing the necessary functionality and reliability.
Industrial Electronics
Flexible and Flex-Rigid PCBs are used in various industrial applications, such as robotics, automation, and process control. They offer improved reliability, increased design flexibility, and reduced size and weight, making them suitable for the demanding operating conditions in industrial environments.
Example: Robotic Arms
Robotic arms require a compact, flexible design that can withstand the repetitive movements and high accelerations involved in industrial processes. Flex-Rigid PCBs allow designers to create a lightweight, durable design that can fit into the limited space available in the robotic arm while providing the necessary connectivity and functionality.
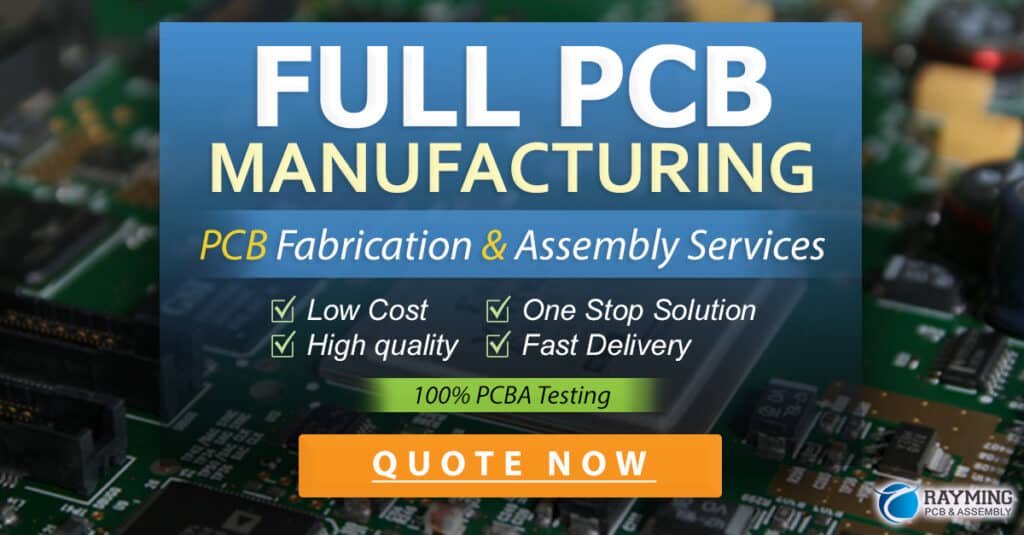
Best Practices for Designing Flexible and Flex-Rigid PCBs
Designing Flexible and Flex-Rigid PCBs requires a different approach than traditional rigid PCBs. Some best practices to keep in mind include:
-
Consider the bend radius: When designing a Flexible or Flex-Rigid PCB, it’s essential to consider the minimum bend radius required for the application. This will help ensure that the PCB can withstand the necessary flexing without damaging the circuitry.
-
Use appropriate materials: Choosing the right materials for your Flexible or Flex-Rigid PCB is crucial for ensuring reliability and durability. Common materials include polyimide, polyester, and FR-4.
-
Optimize trace routing: When routing traces on a Flexible or Flex-Rigid PCB, it’s important to minimize the number of bends and keep the traces as short as possible to reduce stress on the circuitry.
-
Consider the assembly process: Assembling Flexible and Flex-Rigid PCBs can be more challenging than rigid PCBs due to the flexing involved. It’s important to consider the assembly process during the design phase to ensure that the PCB can be manufactured and assembled efficiently.
-
Test and validate the design: Before mass production, it’s crucial to test and validate the design of your Flexible or Flex-Rigid PCB to ensure that it meets the required specifications and can withstand the intended operating conditions.
Future Trends in Flexible and Flex-Rigid PCBs
As technology continues to advance, the demand for Flexible and Flex-Rigid PCBs is expected to grow. Some future trends to watch out for include:
-
Increased adoption in wearable electronics: With the growing popularity of wearable devices, such as smartwatches and fitness trackers, the demand for Flexible and Flex-Rigid PCBs in this sector is expected to increase.
-
Advancements in materials: New materials, such as stretchable conductors and self-healing polymers, are being developed to enhance the performance and durability of Flexible and Flex-Rigid PCBs.
-
Integration of sensors and antennas: Flexible and Flex-Rigid PCBs are increasingly being used to integrate sensors and antennas directly into the PCB, enabling new applications in the Internet of Things (IoT) and wireless communication.
-
Miniaturization: As electronic devices continue to shrink in size, the demand for smaller, more compact Flexible and Flex-Rigid PCBs is expected to grow.
-
Sustainable manufacturing: With the increasing focus on sustainability, manufacturers are exploring eco-friendly materials and processes for producing Flexible and Flex-Rigid PCBs.
FAQ
-
Q: What is the difference between Flexible and Flex-Rigid PCBs?
A: Flexible PCBs are made entirely from flexible materials, while Flex-Rigid PCBs combine flexible and rigid layers into a single, integrated circuit board. -
Q: What are the main advantages of using Flexible and Flex-Rigid PCBs?
A: The main advantages include improved reliability, increased design flexibility, reduced weight and size, enhanced signal integrity, and cost-effectiveness. -
Q: In which industries are Flexible and Flex-Rigid PCBs commonly used?
A: Flexible and Flex-Rigid PCBs are used in various industries, including consumer electronics, medical devices, automotive electronics, aerospace and defense, and industrial electronics. -
Q: What are some best practices for designing Flexible and Flex-Rigid PCBs?
A: Some best practices include considering the bend radius, using appropriate materials, optimizing trace routing, considering the assembly process, and testing and validating the design. -
Q: What are some future trends in Flexible and Flex-Rigid PCBs?
A: Future trends include increased adoption in wearable electronics, advancements in materials, integration of sensors and antennas, miniaturization, and sustainable manufacturing.
Conclusion
Flexible and Flex-Rigid PCBs offer numerous advantages over traditional rigid PCBs, making them suitable for a wide range of applications and industries. By understanding the best ways to use these types of PCBs and following best practices for design and manufacturing, engineers and designers can create more reliable, compact, and cost-effective electronic devices. As technology continues to advance, the demand for Flexible and Flex-Rigid PCBs is expected to grow, driven by trends such as wearable electronics, miniaturization, and sustainable manufacturing.
No responses yet