Introduction to Polyimide PCBs
Polyimide PCBs are a type of printed circuit board that utilizes polyimide as the base material. Polyimide is a high-performance polymer known for its excellent thermal stability, chemical resistance, and mechanical strength. These properties make polyimide PCBs ideal for applications that require reliability in harsh environments, such as aerospace, military, and high-temperature electronics.
Advantages of Polyimide PCBs
- High temperature resistance (up to 400°C)
- Excellent chemical resistance
- Superior mechanical strength and flexibility
- Low dielectric constant and dissipation factor
- Dimensional stability over a wide temperature range
Types of Polyimide PCBs
There are two main types of polyimide PCBs: rigid and flex.
Rigid Polyimide PCBs
Rigid polyimide PCBs are constructed using a solid polyimide substrate that provides excellent stability and durability. These boards are ideal for applications that require high reliability and performance in demanding environments.
Advantages of Rigid Polyimide PCBs
- Improved thermal management
- Enhanced mechanical strength
- Increased durability in harsh conditions
- Better signal integrity at high frequencies
Flex Polyimide PCBs
Flex polyimide PCBs are designed to be flexible, allowing them to conform to various shapes and fit into tight spaces. These boards are made by laminating thin layers of polyimide film with conductive traces, resulting in a flexible circuit that can withstand repeated bending and flexing.
Advantages of Flex Polyimide PCBs
- Increased design flexibility
- Reduced weight and space requirements
- Improved reliability in dynamic applications
- Resistance to vibration and shock
Polyimide Laminate Materials
Polyimide laminates are the foundation of polyimide PCBs. These materials are created by impregnating polyimide resin into a reinforcement material, such as glass fiber or aramid fiber, and then curing the composite under high temperature and pressure.
Common Polyimide Laminate Materials
- Kapton® (DuPont™)
- Apical® (Kaneka)
- Upilex® (UBE Industries)
- VTEC® PI (Richard Lamination)
Material | Dielectric Constant | Dissipation Factor | Tg (°C) | CTE (ppm/°C) |
---|---|---|---|---|
Kapton® | 3.5 | 0.002 | 360-410 | 20-40 |
Apical® | 3.4 | 0.003 | 280-320 | 30-60 |
Upilex® | 3.5 | 0.003 | 300-500 | 10-20 |
VTEC® PI | 3.4 | 0.002 | 260-320 | 30-50 |
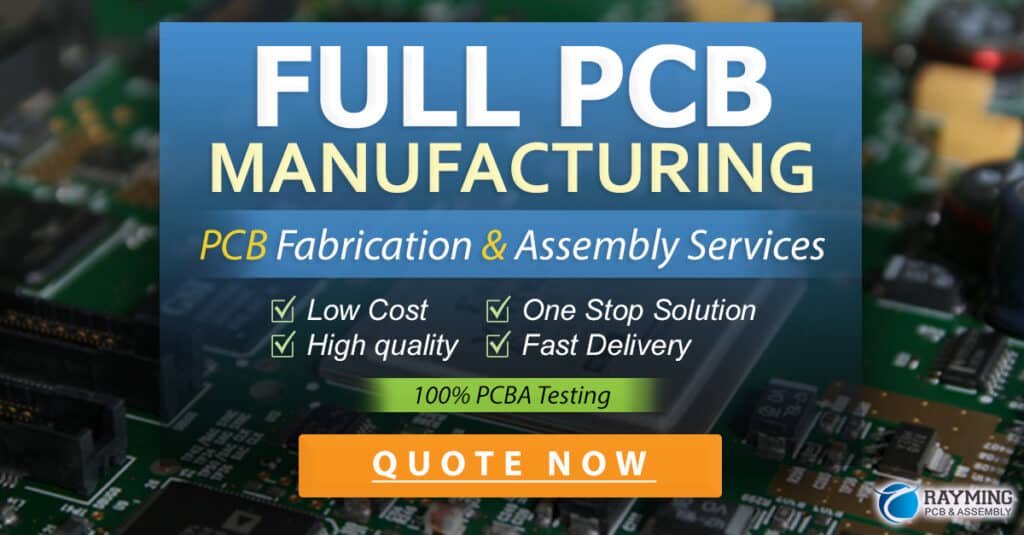
Applications of Polyimide PCBs
Polyimide PCBs find use in various industries and applications that demand high reliability and performance in challenging environments.
Aerospace and Military
- Avionics systems
- Satellite communications
- Missile guidance systems
- Radar equipment
Automotive Electronics
- Engine control units (ECUs)
- Hybrid and electric vehicle power electronics
- Sensor systems
- Infotainment systems
Industrial and Medical
- Oil and gas exploration equipment
- Power generation and distribution
- Medical implants and devices
- High-temperature sensors and actuators
Manufacturing Process of Polyimide PCBs
The manufacturing process of polyimide PCBs involves several steps to ensure the highest quality and reliability.
- Material selection and preparation
- Lamination of polyimide layers
- Drilling and hole preparation
- Copper plating and patterning
- Solder mask application and surface finishing
- Cutting and singulation
- Inspection and testing
Challenges in Polyimide PCB Manufacturing
- Higher processing temperatures compared to traditional PCB materials
- Increased material costs
- Specialized equipment and expertise required
- Longer lead times due to additional processing steps
Future Trends in Polyimide PCBs
As technology advances and applications become more demanding, polyimide PCBs are expected to play an increasingly important role in the electronics industry.
Emerging Trends
- Miniaturization and increased density
- Integration of embedded components
- Advancement in high-speed and high-frequency applications
- Adoption of additive manufacturing techniques
Frequently Asked Questions (FAQ)
-
Q: What is the main difference between rigid and flex polyimide PCBs?
A: Rigid polyimide PCBs have a solid, inflexible substrate, while flex polyimide PCBs are designed to be flexible and can conform to various shapes and fit into tight spaces. -
Q: Can polyimide PCBs withstand extreme temperatures?
A: Yes, polyimide PCBs are known for their excellent thermal stability and can withstand temperatures up to 400°C, making them suitable for high-temperature applications. -
Q: Are polyimide PCBs more expensive than traditional PCBs?
A: Yes, polyimide PCBs tend to be more expensive due to the higher material costs and specialized manufacturing processes required. -
Q: What industries commonly use polyimide PCBs?
A: Polyimide PCBs are commonly used in industries that require high reliability and performance in demanding environments, such as aerospace, military, automotive, industrial, and medical electronics. -
Q: Can polyimide PCBs be manufactured using the same equipment as traditional PCBs?
A: While some of the equipment may be similar, polyimide PCBs often require specialized equipment and expertise due to their unique properties and processing requirements.
Conclusion
Polyimide PCBs, both rigid and flex, offer superior performance and reliability in demanding applications where traditional PCB materials may fall short. With their excellent thermal stability, chemical resistance, and mechanical strength, polyimide PCBs are well-suited for industries such as aerospace, military, automotive, and industrial electronics.
As technology continues to advance and applications become more challenging, the demand for polyimide PCBs is expected to grow. Manufacturers and designers who understand the advantages and challenges associated with polyimide PCBs will be well-positioned to create innovative solutions that push the boundaries of electronic performance and reliability.
No responses yet