What is a Chamfer?
A chamfer is a beveled edge or corner that is created by cutting away material at an angle, typically 45 degrees, to the surface or edge of a workpiece. Chamfers can be found on both exterior and interior edges of components, and they are used for various functional and aesthetic purposes.
Types of Chamfers
There are several types of chamfers, each with its own specific characteristics and applications:
- Flat Chamfer: A flat chamfer is a simple, straight cut at a 45-degree angle to the surface or edge of the workpiece. This is the most common type of chamfer and is often used for deburring, facilitating assembly, and improving aesthetics.
- Radius Chamfer: A radius chamfer, also known as a rounded chamfer, is created by cutting a curved or rounded edge instead of a straight one. This type of chamfer is often used to reduce stress concentrations and improve the overall appearance of the component.
- Angle Chamfer: An angle chamfer is created by cutting the edge at an angle other than 45 degrees. The specific angle used depends on the application and the desired outcome, such as improved clearance or a specific aesthetic appearance.
Chamfer Dimensions
Chamfer dimensions are typically specified using two measurements: the chamfer length and the chamfer angle. The chamfer length is the distance from the edge of the workpiece to the point where the chamfer meets the surface, while the chamfer angle is the angle between the chamfer and the surface.
Chamfer Type | Typical Angle | Common Applications |
---|---|---|
Flat Chamfer | 45 degrees | Deburring, assembly, aesthetics |
Radius Chamfer | N/A (curved) | Stress reduction, aesthetics |
Angle Chamfer | Varies (e.g., 30°, 60°) | Clearance, specific aesthetics |
Chamfered holes
Chamfered holes are a specific application of chamfers in mechanical components. These holes feature a chamfered edge at the top of the hole, which provides several benefits and serves various purposes.
Benefits of Chamfered Holes
- Easier Assembly: Chamfered holes facilitate the insertion of mating components, such as screws, bolts, or pins, by providing a guided entry. The chamfered edge helps align the mating component with the hole, reducing the risk of misalignment and damage during assembly.
- Reduced Stress Concentrations: Sharp edges and corners in holes can act as stress concentration points, leading to increased stress levels and potential failure. Chamfered holes help reduce these stress concentrations by providing a smooth transition between the surface and the hole, distributing the stress more evenly.
- Improved Aesthetics: Chamfered holes can enhance the overall appearance of a component by creating a clean, finished look. The chamfered edge provides a visually appealing transition between the surface and the hole, making the component look more professional and well-designed.
- Burr Removal: The process of creating chamfered holes can also help remove burrs that may form during drilling or machining operations. Burrs can interfere with assembly and cause damage to mating components, so removing them is essential for proper functionality and longevity.
Applications of Chamfered Holes
Chamfered holes are used in a wide range of industries and applications, including:
- Automotive: Chamfered holes are commonly found in automotive components, such as engine blocks, transmission cases, and suspension parts. They facilitate assembly, reduce stress concentrations, and improve the overall appearance of the vehicle.
- Aerospace: In the aerospace industry, chamfered holes are used in various components, such as airframe structures, landing gear, and engine parts. They help ensure proper assembly, reduce stress concentrations, and maintain the high-quality standards required in the industry.
- Medical Devices: Chamfered holes are used in medical device components, such as implants, surgical instruments, and diagnostic equipment. They facilitate assembly, reduce stress concentrations, and improve the overall appearance and functionality of the devices.
- Consumer Products: Many consumer products, such as electronics, appliances, and furniture, incorporate chamfered holes in their design. These holes serve both functional and aesthetic purposes, making the products easier to assemble and more visually appealing.
Manufacturing Chamfered Holes
There are several methods for creating chamfered holes in mechanical components, each with its own advantages and limitations. The choice of method depends on factors such as the material being machined, the required precision, and the production volume.
Drilling and Chamfering
One common method for creating chamfered holes is to drill the hole first and then create the chamfer using a separate tool, such as a chamfering bit or a countersink. This two-step process allows for greater flexibility in the choice of chamfer angle and depth, but it may be more time-consuming than other methods.
Spot Drilling
Spot drilling is a method that combines drilling and chamfering into a single operation. A spot drill, also known as a centering drill, has a 90-degree point angle and a chamfered tip. This tool creates a small pilot hole with a chamfered edge, which can then be followed by a standard drill bit to create the final hole. Spot drilling helps ensure accurate hole placement and reduces the risk of drill bit wandering.
Counterboring
Counterboring is a process that creates a stepped hole with a larger diameter at the top and a smaller diameter at the bottom. The larger diameter portion of the hole is typically chamfered to facilitate assembly and reduce stress concentrations. Counterboring is often used when a screw or bolt head needs to be flush with or below the surface of the component.
Punching
Punching is a high-speed, high-volume method for creating holes in sheet metal components. Chamfered holes can be created using punching by incorporating a chamfered profile into the punch and die set. This method is well-suited for large production runs but may have limitations in terms of Hole Size and chamfer angle.
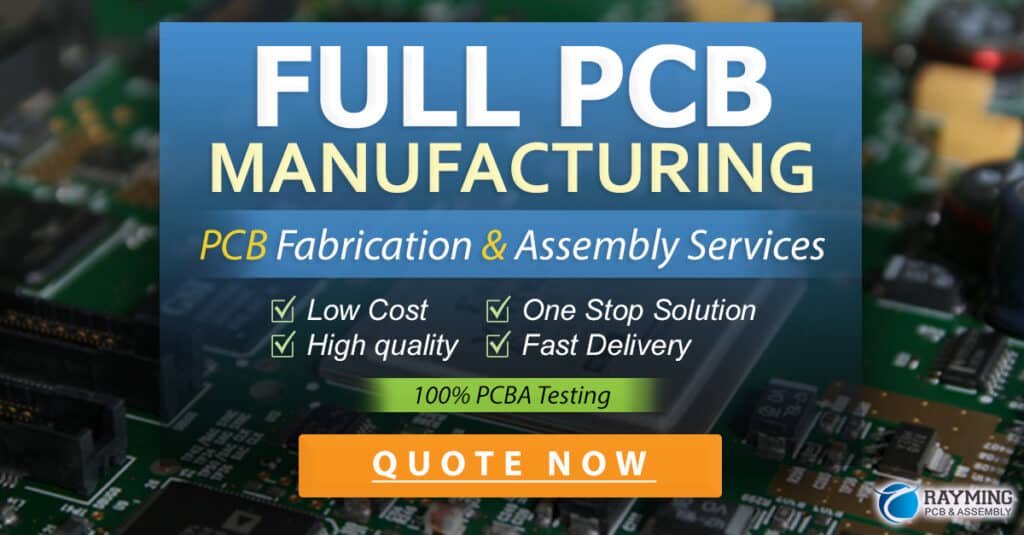
Design Considerations for Chamfered Holes
When designing components with chamfered holes, there are several factors to consider to ensure optimal functionality, manufacturability, and aesthetics.
Chamfer Angle
The choice of chamfer angle depends on the specific application and the desired outcome. A 45-degree chamfer is the most common and is suitable for most general-purpose applications. However, other angles, such as 30 or 60 degrees, may be used for specific purposes, such as improved clearance or a particular aesthetic appearance.
Chamfer Depth
The depth of the chamfer is another essential consideration. A chamfer that is too shallow may not provide sufficient clearance or stress reduction, while a chamfer that is too deep may weaken the component or interfere with mating parts. The chamfer depth should be selected based on the material properties, the hole size, and the specific application requirements.
Material Properties
The material properties of the component play a significant role in the design of chamfered holes. Harder materials, such as steels and titanium alloys, may require different chamfer angles and depths compared to softer materials, such as plastics and aluminum alloys. The design should take into account the material’s strength, ductility, and machinability to ensure optimal performance and manufacturability.
Hole Size and Position
The size and position of the chamfered holes should be carefully considered in the context of the overall component design. The hole size should be selected based on the mating component requirements, such as screw or bolt sizes, while the hole position should be optimized for strength, functionality, and manufacturability. Proper hole placement can help reduce stress concentrations, improve assembly efficiency, and minimize material waste.
Frequently Asked Questions (FAQ)
- What is the purpose of a chamfered hole?
Chamfered holes serve several purposes, including facilitating assembly, reducing stress concentrations, and improving the overall appearance of the component. The chamfered edge provides a guided entry for mating components, helps distribute stress more evenly, and creates a clean, finished look. - What is the most common chamfer angle for holes?
The most common chamfer angle for holes is 45 degrees. This angle provides a good balance between clearance, stress reduction, and manufacturability for most general-purpose applications. - Can chamfered holes be created in any material?
Chamfered holes can be created in most machinable materials, including metals, plastics, and composites. However, the specific design and manufacturing process may need to be adapted based on the material properties, such as hardness, ductility, and machinability. - How does the depth of the chamfer affect the hole’s performance?
The depth of the chamfer can influence the hole’s performance in several ways. A chamfer that is too shallow may not provide sufficient clearance or stress reduction, while a chamfer that is too deep may weaken the component or interfere with mating parts. The optimal chamfer depth depends on factors such as the material properties, hole size, and specific application requirements. - What are the advantages of spot drilling for creating chamfered holes?
Spot drilling combines drilling and chamfering into a single operation, which can save time and improve accuracy compared to a two-step process. The spot drill creates a small pilot hole with a chamfered edge, helping to ensure accurate hole placement and reducing the risk of drill bit wandering. This method is particularly useful for creating precise, consistent chamfered holes in large quantities.
No responses yet