Introduction to John Coonrad and His PCB Industry Insights
John Coonrad is a leading expert in the printed circuit board (PCB) industry, with over 30 years of experience in PCB design, fabrication, and materials. He regularly shares his insights and expertise through various industry publications, conferences, and webinars.
In this weekly PCB digest, we’ll explore some of John Coonrad’s latest observations and advice for professionals in the PCB industry. We’ll cover topics such as:
- PCB material selection and properties
- High-speed PCB design considerations
- PCB manufacturing process improvements
- Industry trends and challenges
Whether you’re a seasoned PCB designer or just starting in the industry, John Coonrad’s expertise can help you stay informed and make better decisions in your work.
H2: The Importance of PCB Material Selection
One of the key areas where John Coonrad provides valuable insights is in the selection of PCB materials. The choice of laminate material can have a significant impact on the performance, reliability, and cost of a PCB design.
H3: Factors to Consider When Choosing PCB Materials
When selecting a PCB material, there are several important factors to consider:
- Dielectric constant (Dk) and dissipation factor (Df)
- Thermal conductivity and coefficient of thermal expansion (CTE)
- Mechanical properties, such as strength and flexibility
- Cost and availability
- Compatibility with the intended manufacturing process
Coonrad emphasizes the importance of understanding the specific requirements of your application and choosing a material that balances performance, reliability, and cost.
H3: Comparison of Common PCB Materials
Some of the most commonly used PCB materials include:
Material | Dk | Df | Thermal Conductivity (W/mK) | CTE (ppm/°C) | Typical Applications |
---|---|---|---|---|---|
FR-4 | 4.3 | 0.02 | 0.3 | 15 | General-purpose, low-cost PCBs |
Rogers 4003C | 3.38 | 0.0027 | 0.71 | 11 | High-frequency, low-loss applications |
Isola I-Tera | 3.45 | 0.0031 | 0.41 | 12 | High-speed digital and RF applications |
Nelco N4000-13 | 3.7 | 0.009 | 0.4 | 12 | Aerospace and defense, high-reliability designs |
Coonrad advises designers to work closely with their PCB fabricators and material suppliers to select the best material for their specific application and manufacturing process.
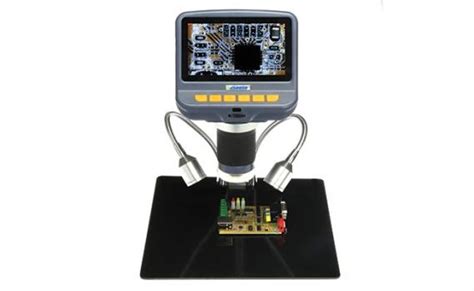
H2: High-Speed PCB Design Considerations
As digital systems continue to push for higher speeds and greater bandwidths, PCB designers face new challenges in ensuring signal integrity and minimizing electromagnetic interference (EMI).
H3: Impedance Control and Matching
One of the key aspects of high-speed PCB design is maintaining proper impedance control and matching. Coonrad stresses the importance of:
- Designing traces with consistent characteristic impedance
- Matching the impedance of traces to the source and load
- Using appropriate termination techniques to minimize reflections
He also recommends using simulation tools to model and optimize the impedance of critical traces before finalizing the PCB layout.
H3: Managing Crosstalk and EMI
Another challenge in high-speed PCB design is minimizing crosstalk and EMI. Coonrad suggests several strategies for mitigating these issues:
- Providing adequate spacing between adjacent traces
- Using guard traces or ground planes to isolate sensitive signals
- Implementing differential pair routing for high-speed signals
- Applying appropriate filtering and shielding techniques
By carefully managing the layout and routing of high-speed traces, designers can help ensure reliable performance and compliance with EMI regulations.
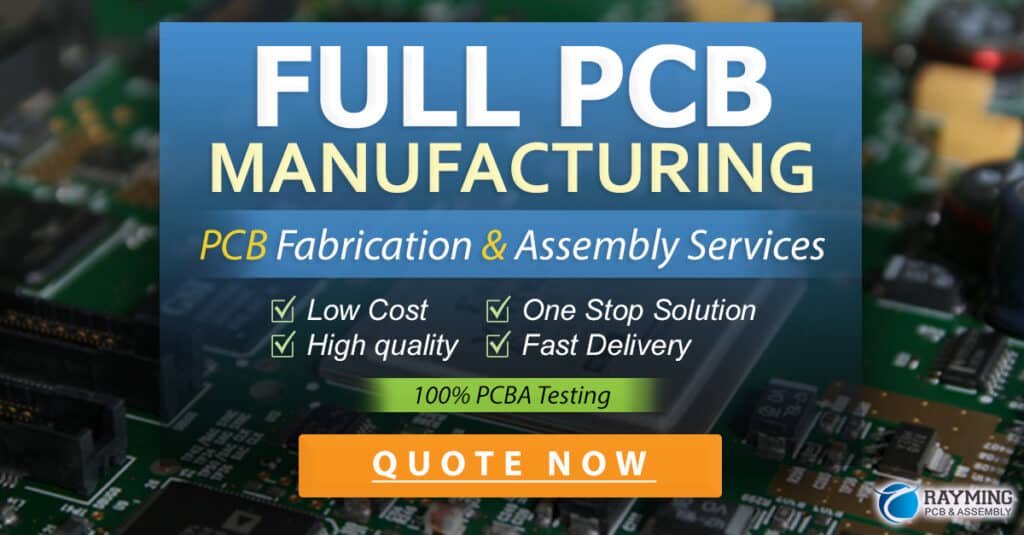
H2: PCB Manufacturing Process Improvements
In addition to design considerations, John Coonrad also shares insights on optimizing the PCB manufacturing process for better quality, reliability, and efficiency.
H3: Advances in PCB Fabrication Techniques
Coonrad highlights several recent advances in PCB fabrication that can help improve the quality and consistency of manufactured boards:
- High-density interconnect (HDI) technology for finer pitch and smaller vias
- Embedded component technology for increased miniaturization and reliability
- Improved lamination processes for better layer registration and bonding
- Automated optical inspection (AOI) and X-ray inspection for detecting manufacturing defects
By staying informed about these advances, PCB designers can take advantage of new capabilities and ensure their designs are manufacturable and reliable.
H3: Design for Manufacturing (DFM) Best Practices
To help ensure a smooth transition from design to manufacturing, Coonrad emphasizes the importance of following design for manufacturing (DFM) best practices. Some key DFM considerations include:
- Adhering to the fabricator’s design rules and guidelines
- Providing clear and complete documentation, including bill of materials and assembly drawings
- Communicating early and often with the fabricator to resolve any issues or questions
- Performing thorough design reviews and simulations to catch potential problems before manufacturing
By working closely with their PCB fabricators and following DFM principles, designers can help minimize manufacturing issues and improve the overall quality and reliability of their products.
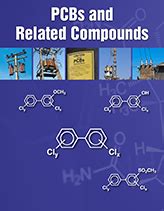
H2: PCB Industry Trends and Challenges
Finally, John Coonrad often shares his perspective on the broader trends and challenges facing the PCB industry.
H3: The Impact of 5G and IoT on PCB Design and Manufacturing
One major trend that Coonrad sees shaping the future of the PCB industry is the rise of 5G and the Internet of Things (IoT). These technologies are driving demand for:
- Higher-frequency PCB materials and designs for mmWave applications
- More complex and miniaturized PCB assemblies for IoT devices
- Increased production volumes and shorter lead times to meet market demands
Coonrad advises PCB professionals to stay informed about these trends and adapt their skills and processes accordingly.
H3: Supply Chain Disruptions and Risk Mitigation
Another challenge facing the PCB industry is the potential for supply chain disruptions, such as those caused by global events like the COVID-19 pandemic. Coonrad recommends several strategies for mitigating supply chain risks:
- Diversifying suppliers and maintaining multiple sources for critical components
- Establishing strong relationships and communication with suppliers
- Monitoring market conditions and anticipating potential disruptions
- Implementing robust inventory management and forecasting practices
By proactively managing supply chain risks, PCB professionals can help ensure continuity of operations and minimize the impact of disruptions on their businesses.
H2: Conclusion
John Coonrad’s insights and expertise provide valuable guidance for professionals throughout the PCB industry. By staying informed about the latest trends, technologies, and best practices, PCB designers and manufacturers can improve the performance, reliability, and efficiency of their products and processes.
As the industry continues to evolve, Coonrad’s weekly digests serve as an essential resource for staying ahead of the curve and navigating the challenges and opportunities ahead.
H2: Frequently Asked Questions (FAQ)
Q1: How can I stay informed about John Coonrad’s latest insights and advice?
A1: You can follow John Coonrad’s work through various industry publications, such as PCB Design Magazine, and by attending his webinars and conference presentations. Additionally, you can subscribe to his weekly PCB digest to receive regular updates on his latest insights and advice.
Q2: What are some of the most important factors to consider when selecting a PCB material?
A2: When selecting a PCB material, you should consider factors such as the dielectric constant (Dk) and dissipation factor (Df), thermal conductivity and coefficient of thermal expansion (CTE), mechanical properties, cost and availability, and compatibility with the intended manufacturing process. It’s essential to balance these factors based on the specific requirements of your application.
Q3: How can I ensure good signal integrity in high-speed PCB designs?
A3: To ensure good signal integrity in high-speed PCB designs, you should focus on maintaining proper impedance control and matching, minimizing crosstalk and EMI, and implementing appropriate routing and termination techniques. Using simulation tools to model and optimize critical traces can also help ensure reliable performance.
Q4: What are some best practices for working with PCB fabricators?
A4: To work effectively with PCB fabricators, you should adhere to their design rules and guidelines, provide clear and complete documentation, communicate early and often to resolve any issues, and perform thorough design reviews and simulations to catch potential problems before manufacturing. Following design for manufacturing (DFM) principles can also help ensure a smooth transition from design to production.
Q5: How can PCB professionals stay ahead of industry trends and challenges?
A5: PCB professionals can stay ahead of industry trends and challenges by staying informed about the latest technologies and market developments, such as the rise of 5G and IoT, and by adapting their skills and processes accordingly. They should also proactively manage supply chain risks by diversifying suppliers, establishing strong relationships, and implementing robust inventory management practices. Regularly engaging with industry experts like John Coonrad can provide valuable insights and guidance for navigating the evolving PCB landscape.
No responses yet