What is Wave Soldering?
Wave soldering is a fast and efficient soldering process that involves passing a PCB over a molten solder wave. The process begins by applying a layer of flux to the bottom side of the PCB, which helps to remove oxides and improve solder wettability. The PCB is then placed on a conveyor belt that carries it over a tank of molten solder. As the PCB passes over the solder wave, the molten solder adheres to the exposed metal surfaces, creating electrical connections between the components and the PCB.
Advantages of Wave Soldering
- High throughput: Wave soldering is a fast process that can handle large volumes of PCBs, making it ideal for high-volume production runs.
- Cost-effective: Due to its speed and efficiency, wave soldering is generally more cost-effective than other soldering methods, especially for large-scale production.
- Versatility: Wave soldering can accommodate a wide range of component types, including through-hole components and some surface mount devices (SMDs).
- Consistent results: When properly set up and maintained, wave soldering machines can produce consistent and reliable solder joints.
Disadvantages of Wave Soldering
- Limited component compatibility: Wave soldering is not suitable for all types of SMDs, particularly those with fine pitch or small sizes.
- Thermal stress: The high temperature of the molten solder can cause thermal stress on sensitive components, potentially leading to damage or reduced lifespan.
- Solder bridging: If not properly controlled, wave soldering can result in solder bridging between closely spaced components or pins.
- Flux residue: The use of flux in wave soldering can leave residue on the PCB, which may require additional cleaning steps.
What is Reflow Soldering?
Reflow soldering is a process that involves applying solder paste to the PCB pads, placing components onto the solder paste, and then heating the entire assembly in a reflow oven. The solder paste, which consists of tiny solder spheres suspended in a flux medium, melts during the reflow process, forming electrical connections between the components and the PCB. Reflow soldering is commonly used for surface mount technology (SMT) assembly.
Advantages of Reflow Soldering
- SMD compatibility: Reflow soldering is well-suited for SMDs, including those with fine pitch and small sizes.
- Automated process: Reflow soldering is highly automated, with pick-and-place machines and reflow ovens handling the majority of the process, resulting in consistent and precise component placement and soldering.
- Minimal thermal stress: The controlled heating profile in reflow soldering minimizes thermal stress on components compared to wave soldering.
- Reduced solder bridging: Reflow soldering’s precise solder paste application and controlled heating reduce the likelihood of solder bridging.
Disadvantages of Reflow Soldering
- Higher initial investment: Reflow soldering requires specialized equipment, such as pick-and-place machines and reflow ovens, which can be more expensive than wave soldering equipment.
- Limited through-hole compatibility: While reflow soldering can accommodate some through-hole components, it is primarily designed for SMDs.
- Solder paste shelf life: Solder paste has a limited shelf life and must be stored and handled properly to maintain its quality.
- Stencil and pad design: Reflow soldering requires precise stencil and pad designs to ensure proper solder paste application and component placement.
Comparing Wave Soldering and Reflow Soldering
To better understand the differences between wave soldering and reflow soldering, let’s compare them side-by-side:
Factor | Wave Soldering | Reflow Soldering |
---|---|---|
Soldering Process | PCB passes over a molten solder wave | Solder paste is applied to PCB pads, components are placed, and the assembly is heated in a reflow oven |
Component Compatibility | Suitable for through-hole components and some SMDs | Primarily designed for SMDs, with limited through-hole compatibility |
Production Volume | Ideal for high-volume production runs | Suitable for both high-volume and low-volume production |
Cost-Effectiveness | More cost-effective for large-scale production | Higher initial investment in equipment, but cost-effective for SMD-heavy assemblies |
Thermal Stress | Higher thermal stress on components | Lower thermal stress due to controlled heating profile |
Solder Bridging | Higher risk of solder bridging if not properly controlled | Reduced risk of solder bridging due to precise solder paste application |
Flux Residue | Can leave flux residue on the PCB, requiring additional cleaning | Minimal flux residue due to the use of no-clean solder paste |
Process Automation | Less automated than reflow soldering | Highly automated, with pick-and-place machines and reflow ovens |
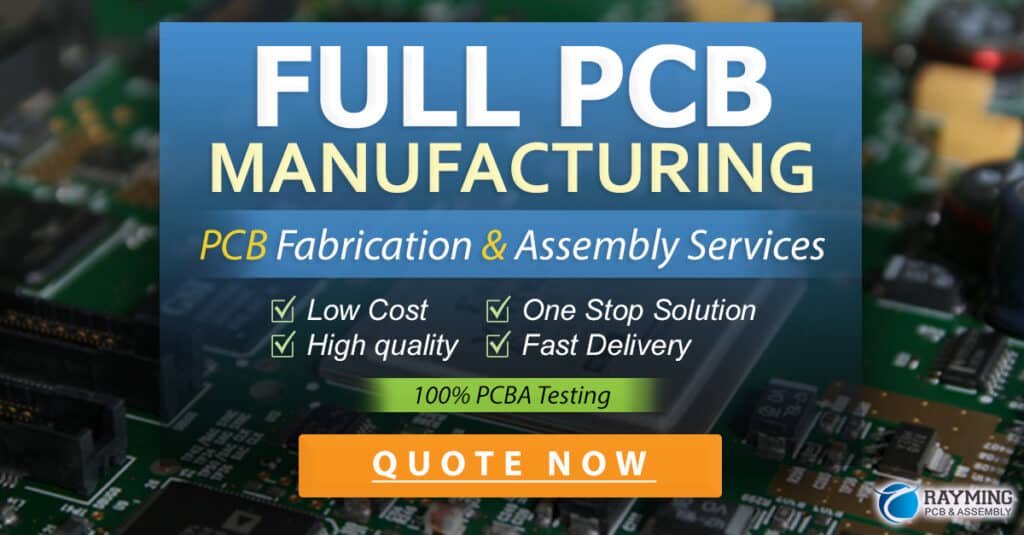
Choosing Between Wave Soldering and Reflow Soldering
When deciding between wave soldering and reflow soldering for your PCB assembly, consider the following factors:
- Component types: If your PCB primarily consists of through-hole components, wave soldering may be the better choice. If your PCB is dominated by SMDs, especially those with fine pitch or small sizes, reflow soldering is the preferred method.
- Production volume: For high-volume production runs, wave soldering is generally more cost-effective. However, if your PCB has a high number of SMDs, reflow soldering may be more efficient, even for large-scale production.
- PCB complexity: Complex PCBs with a mix of through-hole and surface mount components may require a combination of both wave soldering and reflow soldering techniques.
- Budget and equipment: Consider your available budget and existing equipment when choosing between wave soldering and reflow soldering. Reflow soldering requires a higher initial investment in equipment, such as pick-and-place machines and reflow ovens.
- Quality requirements: If your PCB assembly requires highly precise and consistent solder joints, reflow soldering may be the better choice due to its automated process and controlled heating profile.
Frequently Asked Questions (FAQ)
-
Can wave soldering and reflow soldering be used together on the same PCB?
Yes, it is possible to use both wave soldering and reflow soldering on the same PCB. This is often done for PCBs with a mix of through-hole and surface mount components. In this case, the SMDs are typically reflow soldered first, followed by wave soldering for the through-hole components. -
Is wave soldering only suitable for through-hole components?
While wave soldering is primarily used for through-hole components, it can also accommodate some types of SMDs. However, wave soldering is not suitable for all SMDs, particularly those with fine pitch or small sizes, as the molten solder wave may cause bridging or damage to the components. -
Can reflow soldering be used for double-sided PCBs?
Yes, reflow soldering can be used for double-sided PCBs. In this case, the process is typically done in two stages. First, solder paste is applied to one side of the PCB, and components are placed. The assembly is then run through the reflow oven. After the first side is soldered, the process is repeated for the other side of the PCB. -
What is selective soldering, and how does it differ from wave soldering and reflow soldering?
Selective soldering is a soldering process that targets specific areas of a PCB, rather than soldering the entire board. This method is often used for PCBs with a mix of through-hole and surface mount components, or for boards with components that are sensitive to heat. Selective soldering uses a localized solder fountain or mini-wave to solder specific components, minimizing thermal stress on the rest of the PCB. -
How does the choice between wave soldering and reflow soldering affect the PCB design process?
The choice between wave soldering and reflow soldering can significantly impact the PCB design process. For wave soldering, the PCB layout must account for the direction of the solder wave and ensure that components are properly oriented and spaced to prevent shadowing or bridging. Reflow soldering requires precise stencil and pad designs to ensure proper solder paste application and component placement. Additionally, the choice of soldering method may influence the selection of components and their packaging types.
Conclusion
Wave soldering and reflow soldering are two distinct soldering techniques used in PCB assembly, each with its own advantages, disadvantages, and applications. Wave soldering is ideal for high-volume production of PCBs with primarily through-hole components, offering a fast and cost-effective solution. Reflow soldering, on the other hand, is better suited for SMD-heavy assemblies, providing precise and consistent solder joints with minimal thermal stress on components.
When choosing between wave soldering and reflow soldering, consider factors such as component types, production volume, PCB complexity, budget, equipment, and quality requirements. In some cases, a combination of both techniques may be necessary to achieve the best results.
By understanding the differences between wave soldering and reflow soldering, you can make informed decisions when planning your PCB assembly process, ensuring that your products are manufactured efficiently, cost-effectively, and to the highest quality standards.
No responses yet