Introduction to Waterproof PCBs
Printed Circuit Boards (PCBs) are essential components in modern electronic devices. They provide a platform for electrical components to be mounted and connected, enabling the device to function as intended. However, in certain applications, PCBs may be exposed to harsh environments, including moisture, humidity, and even direct contact with water. In such cases, waterproof PCBs become crucial to ensure the reliability and longevity of the electronic device.
What is a Waterproof PCB?
A waterproof PCB is a specially designed and manufactured circuit board that can withstand exposure to water and moisture without compromising its functionality. These PCBs are coated with a protective layer that prevents water from penetrating the board and damaging the electronic components.
Why are Waterproof PCBs Important?
Waterproof PCBs are essential in various applications where electronic devices are exposed to wet or humid environments. Some common examples include:
- Outdoor electronic devices
- Marine electronics
- Automotive electronics
- Medical devices
- Industrial equipment
In these applications, the failure of an electronic device due to water damage can have severe consequences, ranging from inconvenience to safety hazards. Waterproof PCBs help mitigate these risks by providing a reliable and durable solution.
How are Waterproof PCBs Made?
The process of making a waterproof PCB involves several steps, each contributing to the overall water resistance of the board.
PCB Design Considerations
The first step in creating a waterproof PCB is to design the board with water resistance in mind. This involves several considerations:
- Choosing the right substrate material (e.g., FR-4, polyimide)
- Designing the PCB layout to minimize exposed copper traces
- Incorporating sufficient clearance between components
- Selecting components with appropriate IP ratings
Conformal Coating
Once the PCB design is finalized, the next step is to apply a conformal coating. A conformal coating is a thin, protective layer applied to the surface of the PCB, covering the components and traces. This coating acts as a barrier against moisture, dust, and other contaminants.
There are several types of conformal coatings, each with its own advantages and disadvantages:
Coating Type | Advantages | Disadvantages |
---|---|---|
Acrylic | Easy to apply, low cost | Limited chemical resistance |
Silicone | Excellent flexibility, wide temperature range | Difficult to repair |
Polyurethane | Good moisture and abrasion resistance | Can be difficult to apply evenly |
Epoxy | Excellent chemical and abrasion resistance | Brittle, difficult to remove |
The choice of conformal coating depends on the specific requirements of the application, such as the expected environmental conditions and the desired level of protection.
Encapsulation
In some cases, conformal coating alone may not provide sufficient protection against water and moisture. For such applications, encapsulation is used. Encapsulation involves completely sealing the PCB and its components in a protective material, such as epoxy or silicone.
Encapsulation provides a higher level of protection compared to conformal coating, as it creates a solid barrier around the PCB. However, it also makes the PCB more difficult to repair or modify, and can increase the overall size and weight of the device.
Potting
Potting is another method used to waterproof PCBs. It involves filling the enclosure containing the PCB with a potting compound, typically a two-part epoxy or silicone. The potting compound hardens, creating a solid, waterproof barrier around the PCB and its components.
Potting provides excellent protection against water and moisture, as well as shock and vibration. However, like encapsulation, it makes the PCB difficult to repair or modify, and can significantly increase the weight of the device.
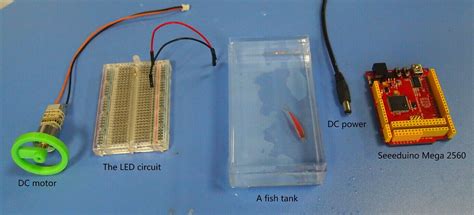
Testing and Certification
To ensure that a waterproof PCB meets the required standards of water resistance, it must undergo rigorous testing and certification.
IP Rating
The Ingress Protection (IP) rating system is used to classify the degree of protection provided by an enclosure against the intrusion of solid objects and water. The IP rating consists of two digits:
- The first digit indicates the level of protection against solid objects (e.g., dust)
- The second digit indicates the level of protection against water
For example, an IP67 rating means that the enclosure is completely dustproof (6) and can withstand immersion in water up to 1 meter deep for 30 minutes (7).
Testing Methods
There are several testing methods used to evaluate the water resistance of a PCB:
- Immersion test: The PCB is submerged in water for a specified duration and depth
- Spray test: The PCB is subjected to a high-pressure water spray from various angles
- Humidity test: The PCB is exposed to high humidity levels for an extended period
The specific testing requirements depend on the application and the desired level of water resistance.
Certification
After successful testing, a waterproof PCB can be certified by a recognized authority, such as Underwriters Laboratories (UL) or the International Electrotechnical Commission (IEC). Certification ensures that the PCB meets the required standards and provides peace of mind for manufacturers and end-users alike.
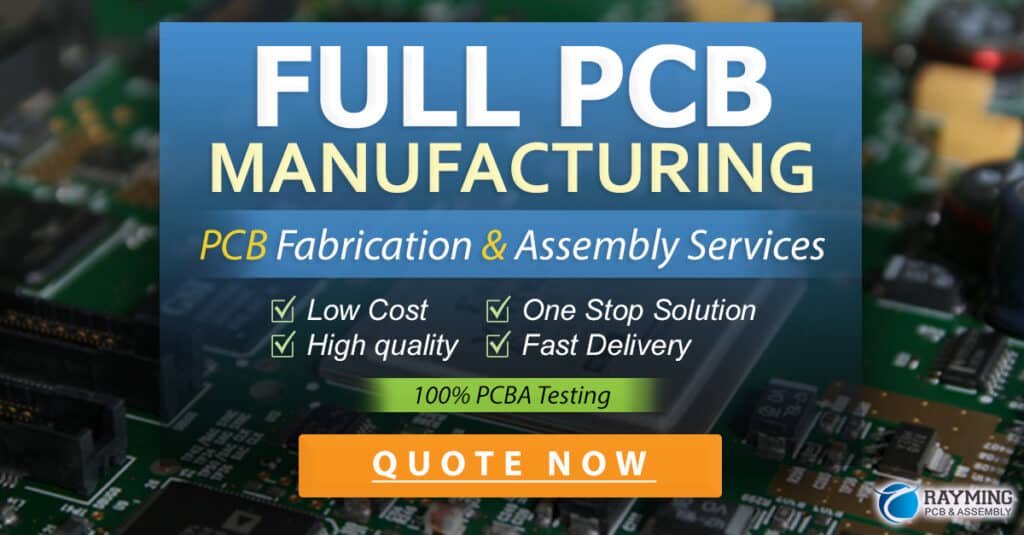
Applications of Waterproof PCBs
Waterproof PCBs find applications in various industries and devices. Some common examples include:
Outdoor Electronic Devices
Outdoor electronic devices, such as security cameras, lighting systems, and communication equipment, are exposed to the elements and require robust protection against water and moisture. Waterproof PCBs ensure that these devices can function reliably in all weather conditions.
Marine Electronics
Marine electronics, including navigation systems, fish finders, and communication devices, operate in a harsh environment with constant exposure to water and humidity. Waterproof PCBs are essential to ensure the reliability and longevity of these devices.
Automotive Electronics
Modern vehicles incorporate numerous electronic systems, many of which are exposed to moisture and humidity. Waterproof PCBs are used in applications such as engine control units, sensors, and infotainment systems to ensure their proper functioning.
Medical Devices
Medical devices, particularly those used in diagnostic and therapeutic procedures, must be able to withstand exposure to liquids and bodily fluids. Waterproof PCBs are crucial in ensuring the safety and reliability of these devices.
Industrial Equipment
Industrial equipment, such as sensors, controllers, and automation systems, often operates in harsh environments with exposure to moisture, chemicals, and other contaminants. Waterproof PCBs help ensure the reliable operation of these systems, minimizing downtime and maintenance costs.
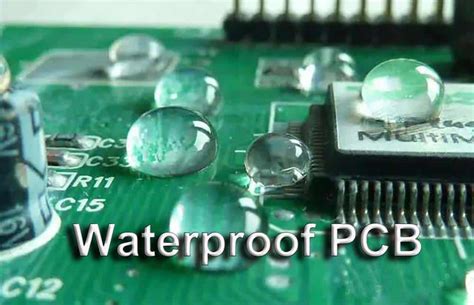
Advantages of Waterproof PCBs
Waterproof PCBs offer several advantages over traditional PCBs:
- Increased reliability: Waterproof PCBs are more resistant to moisture and water damage, ensuring the reliable operation of electronic devices in harsh environments.
- Extended lifespan: By protecting the electronic components from water and moisture, waterproof PCBs can significantly extend the lifespan of the device.
- Reduced maintenance: Waterproof PCBs require less maintenance compared to traditional PCBs, as they are less susceptible to corrosion and other water-related issues.
- Enhanced safety: In applications where water damage can pose a safety hazard, such as medical devices or automotive electronics, waterproof PCBs help mitigate these risks.
Challenges and Considerations
While waterproof PCBs offer numerous benefits, there are also some challenges and considerations to keep in mind:
- Increased cost: The additional processing steps and materials required to make a PCB waterproof can increase its overall cost compared to a traditional PCB.
- Design limitations: Waterproofing a PCB may impose certain design limitations, such as the need for larger component spacing or the use of specific substrate materials.
- Repair and modification: Waterproof PCBs, particularly those that are encapsulated or potted, can be difficult to repair or modify, which may impact the serviceability of the device.
- Environmental impact: Some waterproofing materials, such as certain conformal coatings, may have an environmental impact that needs to be considered.
Future Trends in Waterproof PCBs
As electronic devices continue to evolve and find new applications, the demand for waterproof PCBs is expected to grow. Some future trends in waterproof PCB technology include:
- Advanced materials: The development of new, high-performance waterproofing materials, such as nanocoatings, may offer improved protection and durability.
- 3D printing: The use of 3D printing technology in PCB manufacturing may enable the creation of complex, waterproof structures and enclosures.
- Embedded electronics: The integration of electronic components directly into the PCB substrate, known as embedded electronics, may provide inherent water resistance.
- Self-healing materials: The development of self-healing materials that can automatically repair minor damage caused by water or moisture may further enhance the reliability of waterproof PCBs.
Frequently Asked Questions (FAQ)
-
What is the difference between conformal coating and encapsulation?
Conformal coating is a thin, protective layer applied to the surface of the PCB, while encapsulation involves completely sealing the PCB and its components in a protective material. -
Can a waterproof PCB be repaired if damaged?
The ability to repair a waterproof PCB depends on the waterproofing method used. PCBs with conformal coating can often be repaired, while those that are encapsulated or potted are more difficult to repair. -
What is the IP rating system, and how does it relate to waterproof PCBs?
The IP rating system classifies the degree of protection provided by an enclosure against the intrusion of solid objects and water. It consists of two digits, with the second digit indicating the level of protection against water. -
Are waterproof PCBs more expensive than traditional PCBs?
Yes, waterproof PCBs are generally more expensive than traditional PCBs due to the additional processing steps and materials required for waterproofing. -
What industries commonly use waterproof PCBs?
Waterproof PCBs are commonly used in industries such as outdoor electronics, marine electronics, automotive electronics, medical devices, and industrial equipment.
Conclusion
Waterproof PCBs are essential components in electronic devices that are exposed to wet or humid environments. By providing a reliable and durable solution against water and moisture, waterproof PCBs ensure the proper functioning and longevity of these devices.
The process of making a waterproof PCB involves several steps, including design considerations, conformal coating, encapsulation, and potting. Rigorous testing and certification ensure that the PCB meets the required standards of water resistance.
As electronic devices continue to find new applications in various industries, the demand for waterproof PCBs is expected to grow. Advances in materials, manufacturing techniques, and self-healing technologies may further enhance the performance and reliability of waterproof PCBs in the future.
No responses yet