What is a Waterproof PCB?
A waterproof PCB, also known as a water-resistant PCB, is a printed circuit board designed to withstand exposure to water and moisture. These PCBs are specially engineered to protect the electronic components and circuitry from damage caused by water ingress. Waterproof PCBs are essential in various applications where electronic devices are exposed to harsh environments, such as outdoor installations, marine equipment, and medical devices.
Key Features of Waterproof PCBs
- Conformal Coating
- Sealed Connectors
- Waterproof Enclosures
- Moisture-Resistant Materials
- Proper PCB Design
Why Are Waterproof PCBs Important?
Waterproof PCBs play a crucial role in ensuring the reliability and longevity of electronic devices exposed to water and moisture. Here are some reasons why waterproof PCBs are important:
-
Protection against corrosion: Water and moisture can cause corrosion of the metal traces and components on a PCB, leading to short circuits and device failure. Waterproof PCBs prevent corrosion by shielding the board from water exposure.
-
Improved reliability: By protecting the PCB from water damage, waterproof PCBs enhance the overall reliability of the electronic device. This is particularly important for critical applications where device failure can have serious consequences.
-
Extended product lifespan: Waterproof PCBs help extend the lifespan of electronic devices by preventing premature failure due to water damage. This results in cost savings and reduced downtime for end-users.
-
Compliance with industry standards: Many industries, such as automotive, marine, and medical, have specific standards for water resistance. Waterproof PCBs help manufacturers meet these standards and ensure their products are suitable for use in these environments.
How Are Waterproof PCBs Made?
The manufacturing process for waterproof PCBs involves several specialized techniques and materials. Here are the key steps in making a waterproof PCB:
-
PCB Design: The first step is to design the PCB with waterproofing in mind. This involves selecting appropriate materials, determining the placement of components, and incorporating features such as sealed connectors and mounting holes.
-
Material Selection: Waterproof PCBs are typically made using moisture-resistant materials, such as polyimide or FR-4 with a higher glass transition temperature (Tg). These materials provide better resistance to water absorption and maintain their structural integrity when exposed to moisture.
-
Conformal Coating: Once the PCB is assembled, a conformal coating is applied to the board. This coating is a thin, protective layer that covers the PCB and its components, sealing them from water and moisture. Common conformal coatings include acrylic, silicone, and polyurethane.
-
Encapsulation: In some cases, critical components or the entire PCB may be encapsulated in a waterproof resin or potting compound. This provides an additional layer of protection against water ingress and helps to insulate the components from physical damage.
-
Sealing Connectors and Openings: All connectors, mounting holes, and other openings on the PCB must be properly sealed to prevent water from entering the device. This can be achieved using waterproof connectors, gaskets, or sealants.
-
Testing and Certification: After the waterproofing process is complete, the PCB undergoes rigorous testing to ensure it meets the required water resistance standards. This may include submersion tests, humidity tests, and other environmental stress tests. Once the PCB passes these tests, it can be certified as waterproof.
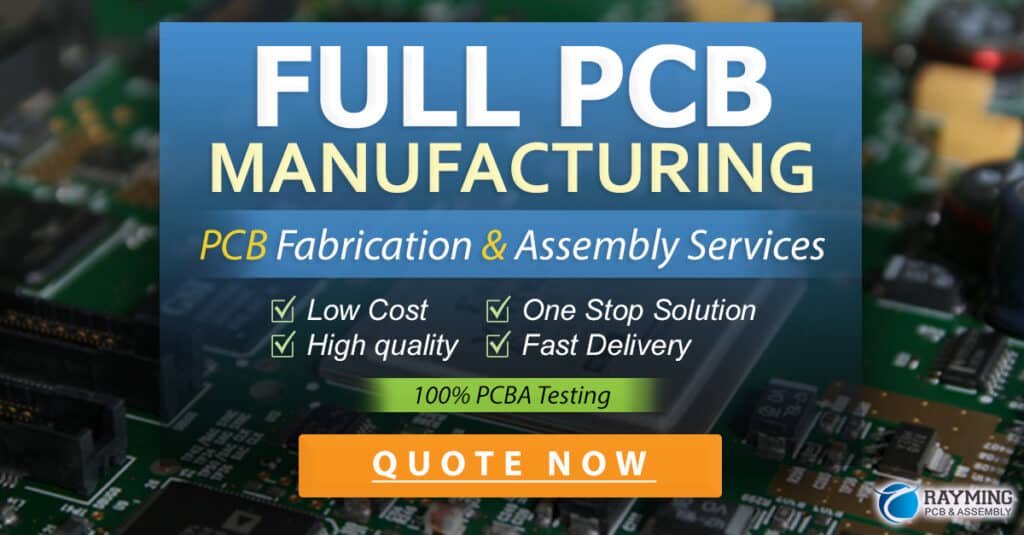
Conformal Coatings for Waterproof PCBs
Conformal coatings are a critical component in making PCBs waterproof. These coatings provide a thin, protective layer that shields the PCB and its components from water, moisture, and other environmental contaminants. Here are some common types of conformal coatings used in waterproof PCBs:
1. Acrylic Conformal Coating
Acrylic conformal coatings are popular for their ease of application, fast curing time, and good moisture resistance. They provide excellent protection against humid environments and can be easily removed for repairs or rework. However, acrylic coatings have limited resistance to solvents and may not be suitable for harsh chemical environments.
2. Silicone Conformal Coating
Silicone conformal coatings offer excellent flexibility and temperature resistance. They provide good protection against moisture and are resistant to many solvents and chemicals. Silicone coatings are also known for their high dielectric strength, making them suitable for high-voltage applications. However, they can be difficult to remove for repairs and may require specialized solvents.
3. Polyurethane Conformal Coating
Polyurethane conformal coatings provide excellent abrasion and chemical resistance. They offer good protection against moisture and can withstand exposure to a wide range of solvents and chemicals. Polyurethane coatings are also known for their durability and long-term reliability. However, they can be more difficult to apply and may require a thicker coating compared to other materials.
4. Parylene Conformal Coating
Parylene conformal coatings are applied using a vapor deposition process, resulting in a thin, uniform coating that conforms to the surface of the PCB. Parylene coatings provide excellent moisture resistance and have a low dielectric constant, making them suitable for high-frequency applications. They also offer good chemical resistance and can withstand extreme temperatures. However, the application process for Parylene coatings is more complex and requires specialized equipment.
Conformal Coating | Moisture Resistance | Chemical Resistance | Ease of Application | Repair/Rework |
---|---|---|---|---|
Acrylic | Good | Limited | Easy | Easy |
Silicone | Good | Good | Moderate | Difficult |
Polyurethane | Good | Excellent | Moderate | Moderate |
Parylene | Excellent | Good | Complex | Difficult |
Waterproof PCB Design Considerations
Designing a waterproof PCB requires careful consideration of several factors to ensure optimal performance and reliability. Here are some key design considerations for waterproof PCBs:
1. Component Selection
When designing a waterproof PCB, it’s essential to choose components that are rated for the expected environmental conditions. This includes selecting components with appropriate moisture sensitivity levels (MSL), temperature ratings, and packaging materials. It’s also important to consider the placement of components to minimize exposure to water and moisture.
2. PCB Material
The choice of PCB material is critical for waterproof applications. FR-4 is a common PCB substrate material, but for waterproof PCBs, it’s important to choose a high-quality FR-4 with a higher glass transition temperature (Tg) to ensure better resistance to moisture absorption. Other moisture-resistant materials, such as polyimide or PTFE, may be used for more demanding applications.
3. Conformal Coating
As discussed earlier, conformal coatings play a vital role in waterproofing PCBs. When designing the PCB, it’s important to consider the type of conformal coating that will be used and ensure that the board layout and component placement are compatible with the coating process. This may involve providing adequate spacing between components and ensuring that all areas of the PCB can be properly coated.
4. Sealing Connectors and Openings
All connectors, mounting holes, and other openings on the PCB must be properly sealed to prevent water ingress. This can be achieved by using waterproof connectors, gaskets, or sealants. When designing the PCB, it’s important to specify the appropriate sealing methods and ensure that the board layout accommodates these features.
5. Drainage and Ventilation
In some cases, it may be necessary to incorporate drainage and ventilation features into the PCB design to prevent the buildup of moisture within the device. This can include adding drainage holes, ventilation slots, or using breathable membranes to allow moisture to escape while preventing water ingress.
6. Testing and Validation
Designing a waterproof PCB is an iterative process that requires testing and validation at various stages. This may include conducting moisture absorption tests, thermal cycling tests, and submersion tests to ensure that the PCB meets the required water resistance standards. It’s important to plan for testing and validation early in the design process to identify and address any potential issues before finalizing the PCB layout.
Design Consideration | Importance |
---|---|
Component Selection | Choose components rated for expected environmental conditions |
PCB Material | Select moisture-resistant materials (e.g., high-Tg FR-4, polyimide) |
Conformal Coating | Ensure compatibility with coating process and provide adequate spacing |
Sealing | Specify appropriate sealing methods for connectors and openings |
Drainage & Ventilation | Incorporate features to prevent moisture buildup |
Testing & Validation | Plan for testing and validation early in the design process |
Applications of Waterproof PCBs
Waterproof PCBs find applications in various industries where electronic devices are exposed to water, moisture, and other harsh environmental conditions. Here are some common applications of waterproof PCBs:
1. Marine Electronics
Waterproof PCBs are essential for marine electronics, such as navigation systems, communication equipment, and sensor networks. These devices are exposed to saltwater, humidity, and temperature fluctuations, making water resistance crucial for their reliable operation.
2. Outdoor Equipment
Electronic devices used outdoors, such as security cameras, weather monitoring stations, and solar panel controllers, require waterproof PCBs to withstand exposure to rain, snow, and moisture. Waterproofing helps ensure the long-term reliability and performance of these devices in challenging environmental conditions.
3. Automotive Electronics
Waterproof PCBs are used in various automotive applications, particularly in safety-critical systems and sensors exposed to moisture and road debris. Examples include engine control units, brake control modules, and parking sensors. Waterproofing helps prevent corrosion and short circuits, ensuring the safe and reliable operation of these systems.
4. Medical Devices
Medical devices, such as wearable monitors, implantable sensors, and diagnostic equipment, often require waterproof PCBs to protect against exposure to bodily fluids and moisture. Waterproofing is critical in maintaining the sterility and performance of these devices, especially in applications where they come into direct contact with patients.
5. Industrial Controls
Industrial control systems, such as those used in manufacturing plants, power generation facilities, and water treatment plants, often operate in harsh environments with high humidity, chemical exposure, and water splash. Waterproof PCBs help ensure the reliable operation of these control systems, minimizing downtime and maintenance requirements.
Application | Environmental Challenges | Key Benefits of Waterproof PCBs |
---|---|---|
Marine Electronics | Saltwater, humidity, temperature fluctuations | Reliable operation in harsh marine environments |
Outdoor Equipment | Rain, snow, moisture | Long-term reliability and performance outdoors |
Automotive Electronics | Moisture, road debris | Safe and reliable operation of safety-critical systems |
Medical Devices | Bodily fluids, moisture | Maintains sterility and performance in medical applications |
Industrial Controls | High humidity, chemical exposure, water splash | Minimizes downtime and maintenance in industrial settings |
FAQs About Waterproof PCBs
1. What is the difference between waterproof and water-resistant PCBs?
Waterproof PCBs are designed to provide complete protection against water ingress, even when submerged. Water-resistant PCBs, on the other hand, offer protection against splashes and light exposure to water but may not withstand complete submersion. The level of water resistance required depends on the specific application and environmental conditions.
2. How long do waterproof PCBs last?
The lifespan of a waterproof PCB depends on various factors, such as the quality of the conformal coating, the environmental conditions, and the PCB material. With proper design, manufacturing, and maintenance, waterproof PCBs can last for several years or even decades. Regular inspections and maintenance can help extend the lifespan of waterproof PCBs.
3. Can waterproof PCBs be repaired?
Yes, waterproof PCBs can be repaired, but the process can be more challenging compared to non-waterproof PCBs. The conformal coating must be carefully removed to access the components for repair, and the coating must be reapplied after the repair is complete. Some conformal coatings, such as silicone and Parylene, can be difficult to remove and may require specialized solvents or equipment.
4. How much do waterproof PCBs cost compared to regular PCBs?
Waterproof PCBs generally cost more than regular PCBs due to the additional materials and processes involved in their manufacture. The cost difference can vary depending on the specific waterproofing methods used, the PCB complexity, and the production volume. However, the added cost of waterproofing is often justified by the improved reliability and longevity of the PCB in harsh environments.
5. Are there any limitations to waterproof PCBs?
While waterproof PCBs offer excellent protection against water and moisture, they do have some limitations. Waterproofing can add thickness and weight to the PCB, which may be a concern in some applications. Additionally, waterproof coatings can make it more difficult to access components for repair or rework. Proper design and planning can help mitigate these limitations and ensure the successful implementation of waterproof PCBs in various applications.
Conclusion
Waterproof PCBs are essential for ensuring the reliability and longevity of electronic devices exposed to water, moisture, and other harsh environmental conditions. By understanding the key features, manufacturing processes, and design considerations for waterproof PCBs, engineers and manufacturers can create robust and reliable electronic systems for a wide range of applications.
When designing a waterproof PCB, it’s important to consider factors such as component selection, PCB material, conformal coating, sealing methods, and testing and validation. By carefully addressing these design considerations and working with experienced PCB manufacturers, it’s possible to create waterproof PCBs that meet the specific requirements of the intended application.
As electronic devices continue to be used in increasingly challenging environments, the demand for waterproof PCBs will only grow. By staying up-to-date with the latest waterproofing technologies and best practices, engineers and manufacturers can ensure that their products are well-equipped to withstand the rigors of these environments and deliver reliable, long-lasting performance.
No responses yet