What are Vibration Sensors?
Vibration sensors are devices that convert mechanical vibrations into electrical signals. These sensors are designed to detect and measure the frequency, amplitude, and acceleration of vibrations in a given system. The electrical signals generated by the sensors can be analyzed to determine the condition of the system and identify potential issues before they lead to failures or breakdowns.
Types of Vibration Sensors
There are several types of vibration sensors available in the market, each with its own unique characteristics and applications. Here are the most common types of vibration sensors:
1. Piezoelectric Vibration Sensors
Piezoelectric vibration sensors are the most widely used type of vibration sensors. They utilize piezoelectric materials, such as quartz or ceramics, which generate an electrical charge when subjected to mechanical stress or strain. The piezoelectric effect allows these sensors to convert vibrations into electrical signals accurately.
Advantages of Piezoelectric Vibration Sensors
- High sensitivity
- Wide frequency range
- Excellent linearity
- Robust and durable construction
- Suitable for harsh environments
Applications of Piezoelectric Vibration Sensors
- Machine condition monitoring
- Structural health monitoring
- Automotive testing
- Aerospace and defense
- Consumer electronics
2. MEMS Vibration Sensors
MEMS (Micro-Electro-Mechanical Systems) vibration sensors are miniaturized sensors that utilize advanced microfabrication techniques. These sensors consist of a small, integrated circuit with a mechanical sensing element, such as a cantilever beam or a proof mass. MEMS vibration sensors are known for their low power consumption, small size, and cost-effectiveness.
Advantages of MEMS Vibration Sensors
- Compact and lightweight
- Low power consumption
- Cost-effective
- High sensitivity
- Integration with electronics
Applications of MEMS Vibration Sensors
- Smartphone and wearable devices
- Automotive applications (e.g., airbag deployment, electronic stability control)
- Consumer electronics (e.g., gaming controllers, virtual reality devices)
- Industrial automation and robotics
3. Capacitive Vibration Sensors
Capacitive vibration sensors work on the principle of capacitance change. They consist of two conductive plates separated by a dielectric material. When subjected to vibrations, the distance between the plates changes, resulting in a change in capacitance. This change in capacitance is then converted into an electrical signal proportional to the vibration amplitude.
Advantages of Capacitive Vibration Sensors
- High sensitivity
- Low power consumption
- Wide dynamic range
- Suitable for low-frequency vibrations
Applications of Capacitive Vibration Sensors
- Structural health monitoring
- Seismic monitoring
- Automotive applications (e.g., suspension systems)
- Consumer electronics (e.g., touch screens, Proximity Sensors)
4. Piezoresistive Vibration Sensors
Piezoresistive vibration sensors utilize materials whose electrical resistance changes when subjected to mechanical stress or strain. These sensors typically consist of a piezoresistive element, such as a silicon strain gauge, bonded to a flexible substrate. When vibrations occur, the piezoresistive element experiences a change in resistance, which is then converted into an electrical signal.
Advantages of Piezoresistive Vibration Sensors
- High sensitivity
- Wide bandwidth
- Good temperature stability
- Suitable for low-frequency vibrations
Applications of Piezoresistive Vibration Sensors
- Automotive testing (e.g., crash testing, road load data acquisition)
- Structural health monitoring
- Aerospace and defense
- Industrial automation and robotics
5. Optical Vibration Sensors
Optical vibration sensors use light to detect and measure vibrations. These sensors typically consist of a light source, such as a laser or an LED, and a photodetector. The light source is directed towards a reflective surface attached to the vibrating object, and the reflected light is captured by the photodetector. The variations in the reflected light intensity are then analyzed to determine the vibration characteristics.
Advantages of Optical Vibration Sensors
- Non-contact measurement
- High sensitivity
- Wide frequency range
- Immune to electromagnetic interference
Applications of Optical Vibration Sensors
- Structural health monitoring
- Aerospace and defense
- Industrial automation and robotics
- Research and development
Comparison of Vibration Sensor Types
The following table provides a comparison of the different types of vibration sensors based on their key characteristics:
Sensor Type | Sensitivity | Frequency Range | Size | Cost | Applications |
---|---|---|---|---|---|
Piezoelectric | High | Wide | Small to Large | Moderate | Industrial, Automotive, Aerospace |
MEMS | High | Wide | Very Small | Low | Consumer Electronics, Automotive |
Capacitive | High | Low to Medium | Small to Medium | Moderate | Structural Monitoring, Automotive |
Piezoresistive | High | Low to Medium | Small to Medium | Moderate | Automotive, Structural Monitoring |
Optical | High | Wide | Small to Large | High | Structural Monitoring, Aerospace |
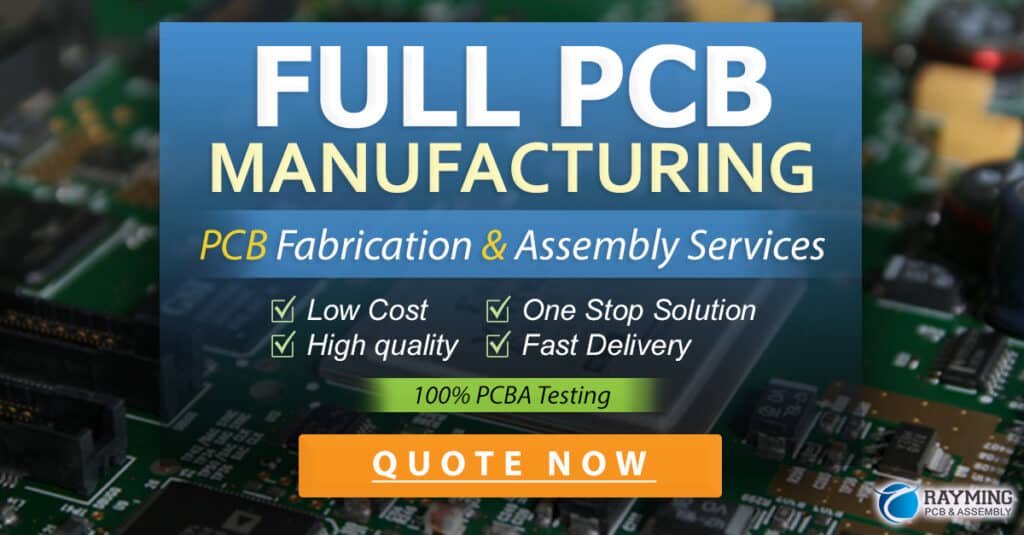
Frequently Asked Questions (FAQ)
-
What is the most suitable vibration sensor for machine condition monitoring?
Piezoelectric vibration sensors are widely used for machine condition monitoring due to their high sensitivity, wide frequency range, and robustness. They can effectively detect and measure vibrations in industrial machinery, enabling early fault detection and predictive maintenance. -
Can MEMS vibration sensors be used in harsh environments?
MEMS vibration sensors are generally not suitable for harsh environments due to their small size and sensitivity to temperature and humidity. For applications in harsh environments, piezoelectric or optical vibration sensors are more appropriate. -
How do I select the right vibration sensor for my application?
When selecting a vibration sensor, consider factors such as the frequency range of interest, required sensitivity, environmental conditions, size constraints, and budget. Consult the sensor manufacturer’s specifications and application notes to determine the most suitable sensor for your specific requirements. -
What is the difference between accelerometers and vibration sensors?
Accelerometers are a type of vibration sensor that specifically measure acceleration. While all accelerometers can be considered vibration sensors, not all vibration sensors are accelerometers. Vibration sensors encompass a wider range of devices that can measure various vibration parameters, such as displacement, velocity, and acceleration. -
How do I interpret the data from a vibration sensor?
Interpreting vibration sensor data requires knowledge of signal processing techniques and an understanding of the system being monitored. The raw vibration data is typically analyzed using techniques such as Fourier analysis, time-frequency analysis, and statistical methods to extract meaningful information about the system’s health and performance. It is recommended to consult with vibration analysis experts or use specialized software tools for accurate interpretation of vibration data.
Conclusion
Vibration sensors play a crucial role in various industries, enabling the monitoring and analysis of vibrations in machines, structures, and devices. By understanding the different types of vibration sensors, their working principles, and their applications, engineers and technicians can select the most suitable sensor for their specific needs. Whether it’s for machine condition monitoring, structural health monitoring, or consumer electronics, vibration sensors provide valuable insights into the dynamic behavior of systems, contributing to improved safety, reliability, and performance.
No responses yet