Introduction to Varistors
A varistor, also known as a voltage-dependent resistor (VDR), is an electronic component that provides protection against voltage spikes in electrical circuits. Its resistance varies with the applied voltage, making it an ideal choice for Overvoltage Protection applications. When exposed to high voltage transients, the varistor’s resistance dramatically decreases, allowing it to absorb and dissipate the excess energy, thereby protecting sensitive electronic components from damage.
Varistors are widely used in various industries, including telecommunications, automotive, consumer electronics, and power systems. They offer a cost-effective and reliable solution for safeguarding electronic circuits against voltage surges caused by lightning strikes, switching transients, and electrostatic discharges.
Varistor Symbols and Their Meanings
To effectively use varistors in circuit designs, it is essential to understand the symbols used to represent them in schematic diagrams. The following table shows the most common varistor symbols and their meanings:
Symbol | Meaning |
---|---|
Basic varistor symbol | |
Bidirectional varistor symbol | |
Unidirectional varistor symbol | |
Varistor with a third terminal (ground) |
The basic varistor symbol consists of two parallel lines with a curved arrow between them, indicating its voltage-dependent behavior. The bidirectional varistor symbol has arrows pointing in both directions, suggesting that it can handle voltage spikes of either polarity. The unidirectional varistor symbol has an arrow pointing in only one direction, indicating that it is designed to protect against voltage spikes of a specific polarity. Lastly, the varistor symbol with a third terminal represents a device with an additional ground connection for enhanced protection.
Varistor Working Principle
Varistors are essentially ceramic semiconductor devices that exhibit a nonlinear current-voltage (I-V) characteristic. They are composed of a ceramic material, typically zinc oxide (ZnO), sandwiched between two metal electrodes. The ZnO grains are separated by thin insulating layers, forming a network of grain boundaries.
Under normal operating conditions, the varistor acts as a high-resistance device, allowing only a small leakage current to flow through it. However, when the applied voltage exceeds a specific threshold value, known as the varistor voltage, the device’s resistance drastically decreases, and it begins to conduct a large current. This sudden change in resistance is due to the breakdown of the insulating layers at the grain boundaries, allowing current to flow through the ZnO grains.
As the varistor conducts, it absorbs and dissipates the excess energy associated with the voltage spike, effectively clamping the voltage across its terminals to a safe level. Once the transient voltage subsides, the varistor returns to its high-resistance state, ready to protect against future voltage spikes.
Varistor Equivalent Circuit
To better understand the behavior of a varistor, it is helpful to consider its equivalent circuit model. The following figure shows a simplified equivalent circuit of a varistor:
The equivalent circuit consists of three main components:
- Variable Resistor (RV): Represents the nonlinear resistance of the varistor, which changes with the applied voltage.
- Capacitor (C): Represents the parasitic capacitance of the varistor, which is typically in the range of a few hundred picofarads to a few nanofarads.
- Inductor (L): Represents the parasitic inductance of the varistor, which is usually negligible in most applications.
The variable resistor (RV) is the key component that determines the varistor’s voltage-clamping behavior. As the applied voltage increases, the resistance of RV decreases, allowing more current to flow through the device. The capacitor (C) and inductor (L) contribute to the varistor’s high-frequency response and may affect its performance in certain applications.
Varistor Characteristics
To effectively select and use varistors in circuit protection applications, it is essential to understand their key characteristics. The following table summarizes the primary characteristics of varistors:
Characteristic | Description |
---|---|
Varistor Voltage (VV) | The voltage at which the varistor begins to conduct significantly, typically defined as the voltage at which the device conducts 1 mA of current. |
Maximum Continuous Operating Voltage (MCOV) | The maximum voltage that can be continuously applied to the varistor without causing degradation or damage. |
Clamping Voltage (VC) | The peak voltage that appears across the varistor terminals when subjected to a specified transient current. |
Energy Absorption Capacity | The maximum amount of energy the varistor can absorb without being damaged, typically expressed in joules (J). |
Response Time | The time required for the varistor to react to a voltage transient and clamp the voltage to a safe level, typically in the range of nanoseconds. |
Capacitance | The parasitic capacitance of the varistor, which may affect its high-frequency performance. |
Leakage Current | The small current that flows through the varistor when the applied voltage is below the varistor voltage. |
When selecting a varistor for a specific application, it is crucial to consider these characteristics and ensure that the chosen device can effectively protect the circuit under the expected operating conditions.
Varistor Applications
Varistors find widespread use in various industries and applications where overvoltage protection is critical. Some of the most common applications include:
Power Supply Protection
Varistors are commonly used to protect power supplies from voltage transients that may occur due to lightning strikes, switching events, or other disturbances on the power line. By placing a varistor across the input terminals of a power supply, any voltage spikes that exceed the varistor voltage will be clamped, protecting the sensitive electronic components inside the power supply.
Telecommunication Equipment Protection
In telecommunication systems, varistors are used to protect equipment from voltage surges that may propagate through the communication lines. These surges can be caused by lightning strikes, electromagnetic interference, or cross-talk between adjacent lines. By installing varistors at the input stages of telecommunication equipment, such as modems, routers, and switches, the devices can be safeguarded against damage caused by transient overvoltages.
Automotive Electronics Protection
Modern automobiles rely heavily on electronic systems for various functions, including engine control, infotainment, and safety features. Varistors play a crucial role in protecting these electronic components from voltage spikes that may occur due to load dump events, alternator transients, or other electrical disturbances in the vehicle’s electrical system. By strategically placing varistors in the automotive electronic circuits, designers can ensure the reliable operation of these systems even under harsh electrical conditions.
Industrial Control Systems Protection
Industrial control systems, such as programmable logic controllers (PLCs), sensors, and actuators, are often exposed to harsh electrical environments where voltage transients are common. Varistors are used to protect these systems from overvoltage events that may cause damage or malfunction. By incorporating varistors into the design of industrial control panels and equipment, engineers can improve the reliability and longevity of these systems.
Consumer Electronics Protection
Varistors are widely used in consumer electronic devices, such as televisions, computers, and home appliances, to protect them from voltage surges that may enter the device through the power cord or other input/output ports. By placing varistors at the input stage of these devices, any incoming voltage spikes can be effectively clamped, preventing damage to the internal electronic components.
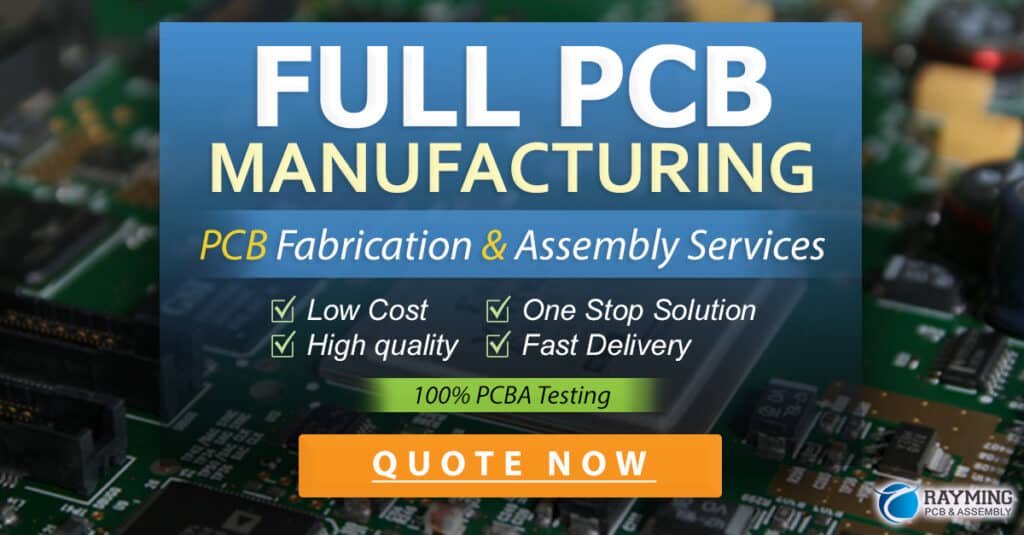
Varistor Selection Considerations
When selecting a varistor for a specific application, several factors must be considered to ensure optimal performance and protection. These factors include:
-
Varistor Voltage (VV): The varistor voltage should be selected based on the maximum continuous operating voltage (MCOV) of the protected circuit. The VV should be higher than the MCOV to avoid continuous conduction and overheating of the varistor.
-
Energy Absorption Capacity: The varistor’s energy absorption capacity should be sufficient to handle the expected energy of the voltage transients in the application. This can be determined by considering the transient voltage waveform, source impedance, and the desired clamping voltage.
-
Clamping Voltage (VC): The clamping voltage should be low enough to protect the sensitive electronic components in the circuit but high enough to avoid excessive current flow through the varistor during a transient event.
-
Response Time: The varistor’s response time should be fast enough to effectively clamp the voltage transient before it can cause damage to the protected components. For most applications, varistors with response times in the nanosecond range are suitable.
-
Operating Temperature Range: The varistor should be selected to operate reliably over the expected temperature range of the application. High temperatures can cause a decrease in the varistor voltage and an increase in leakage current, which may affect the device’s performance and reliability.
-
Mechanical Considerations: The varistor’s package size and mounting type should be compatible with the circuit board layout and assembly process. Surface-mount varistors are commonly used in modern electronic designs due to their compact size and ease of assembly.
By carefully considering these factors and consulting the varistor manufacturer’s data sheets, designers can select the most appropriate varistor for their specific application, ensuring optimal protection against voltage transients.
Varistor Protection Circuit Design
When incorporating varistors into a circuit for overvoltage protection, several design considerations must be taken into account to ensure effective and reliable protection. The following guidelines can help in designing varistor protection circuits:
-
Varistor Placement: The varistor should be placed as close as possible to the input terminals of the protected circuit or device. This minimizes the inductance between the varistor and the protected components, ensuring fast response times and effective clamping of voltage transients.
-
Parallel Connection: Varistors are typically connected in parallel with the protected circuit or device. This allows the varistor to clamp the voltage across its terminals and shunt the excess current away from the sensitive components during a transient event.
-
Series Impedance: In some cases, it may be necessary to include a small series impedance, such as a resistor or an inductor, between the varistor and the protected circuit. This can help limit the peak current through the varistor during a transient event and improve the overall clamping performance.
-
Thermal Management: Varistors can generate significant heat during a transient event, especially if the energy absorption capacity is exceeded. To prevent thermal damage, it is essential to consider the varistor’s power dissipation capabilities and provide adequate heat sinking or cooling if necessary.
-
Failsafe Design: In critical applications, it is recommended to use a failsafe design approach, which ensures that the protected circuit remains safe even if the varistor fails. This can be achieved by using multiple varistors in parallel, implementing thermal fuses, or incorporating other redundant protection mechanisms.
-
Coordination with Other Protection Devices: Varistors can be used in conjunction with other overvoltage protection devices, such as gas discharge tubes (GDTs) or transient voltage suppression (TVS) diodes, to achieve optimal protection performance. When using multiple protection devices, it is essential to ensure proper coordination between them to avoid interference or unintended interactions.
By following these design guidelines and carefully selecting the appropriate varistor based on the application requirements, designers can create robust and reliable overvoltage protection circuits that effectively safeguard sensitive electronic components from voltage transients.
Frequently Asked Questions (FAQ)
-
What is the difference between a varistor and a surge suppressor?
A varistor is a single component that provides overvoltage protection by clamping voltage spikes to a safe level. A surge suppressor, on the other hand, is a complete device that typically incorporates varistors along with other components, such as gas discharge tubes and capacitors, to provide comprehensive protection against voltage transients. -
Can varistors be used for AC and DC applications?
Yes, varistors can be used for both AC and DC applications. However, it is essential to select the appropriate varistor based on the specific requirements of the application, such as the maximum continuous operating voltage, transient energy absorption capacity, and clamping voltage. -
How do varistors fail, and what are the consequences?
Varistors can fail due to various reasons, including excessive energy absorption, high temperature, or aging. When a varistor fails, it typically enters a short-circuit state, which can lead to increased current flow and potential damage to the protected circuit. In some cases, a failed varistor may enter an open-circuit state, leaving the protected circuit vulnerable to future voltage transients. -
Can varistors be connected in series or parallel for improved protection?
Varistors can be connected in parallel to increase the current handling capacity and energy absorption capability of the protection circuit. However, connecting varistors in series is generally not recommended, as it can lead to uneven voltage distribution and potential failure of the individual varistors. -
How do I select the right varistor for my application?
To select the right varistor for your application, consider factors such as the maximum continuous operating voltage, transient energy absorption capacity, clamping voltage, response time, and operating temperature range. Consult the varistor manufacturer’s data sheets and application notes to determine the most suitable device for your specific requirements. It is also recommended to seek the advice of experienced engineers or protection specialists when designing critical overvoltage protection circuits.
Conclusion
Varistors are essential components in overvoltage protection circuits, offering a reliable and cost-effective solution for safeguarding sensitive electronic devices from voltage transients. By understanding varistor symbols, working principles, characteristics, and applications, designers can effectively incorporate these devices into their circuit designs.
When selecting varistors and designing protection circuits, it is crucial to consider factors such as varistor voltage, energy absorption capacity, clamping voltage, response time, and operating temperature range. Following best practices in varistor placement, parallel connection, thermal management, and failsafe design can help ensure optimal protection performance and reliability.
As electronic systems continue to advance and become more complex, the importance of robust overvoltage protection solutions, such as varistors, will only continue to grow. By staying informed about the latest developments in varistor technology and protection circuit design techniques, engineers can create safer, more reliable, and more resilient electronic products that can withstand the challenges of today’s demanding electrical environments.
No responses yet