What is Obsolescence Management Software?
Obsolescence management software is a type of application designed to help companies proactively identify, assess, and mitigate risks related to obsolete or soon-to-be obsolete parts and components. These platforms centralize and analyze data from various sources to provide visibility into the lifecycle status of parts.
Key features and capabilities of obsolescence management software include:
- Bill of Materials (BOM) monitoring
- Part lifecycle and risk analysis
- Supply chain management
- Notifications and alerts
- Reporting and analytics
By leveraging these tools, companies can take a systematic approach to obsolescence management, making data-driven decisions to avoid shortages, redesigns, and other obsolescence-related disruptions.
The High Costs of Obsolete Parts
Obsolete parts may seem like a minor annoyance, but they can have major consequences across an organization. Some of the potential impacts include:
Impact | Description |
---|---|
Production delays | Inability to source obsolete parts can halt production lines |
Increased costs | Last-time buys, redesigns, and rush orders drive up expenses |
Excess inventory | Overbuying parts to avoid shortages ties up working capital |
Customer dissatisfaction | Delays and quality issues damage customer relationships |
Competitive disadvantage | Nimbler competitors avoid obsolescence issues and win market share |
A 2021 survey found that 84% of supply chain leaders had experienced increased costs due to obsolescence, with 56% facing production downtime and 32% reporting customer satisfaction issues. The average cost of obsolescence per company was $66 million annually.
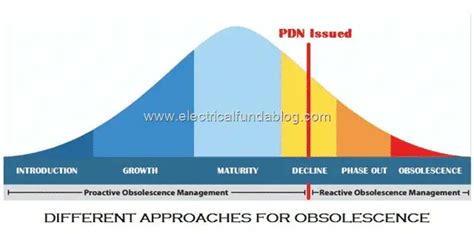
Proactive Obsolescence Management With Software
Obsolescence management software enables companies to shift from a reactive approach, scrambling to address obsolescence issues after they occur, to a proactive strategy focused on prevention and early detection.
Centralized Data Management
One of the key benefits of obsolescence management software is that it provides a centralized platform for managing data related to parts and components. This includes:
- Part numbers and descriptions
- Manufacturer and supplier information
- Lifecycle status and risk level
- Inventory levels and usage data
- Alternative and substitute parts
By aggregating data from disparate systems like enterprise resource planning (ERP), product lifecycle management (PLM), and supplier portals, obsolescence management software creates a “single source of truth.” This makes it easier for teams across the organization to access up-to-date, accurate information about parts.
BOM Monitoring and Analysis
Bills of materials (BOMs) are a critical data source for obsolescence management, as they list all the components, parts, and subassemblies required to manufacture a product. Obsolescence management software can ingest BOMs and continuously monitor the lifecycle status and risk of each part.
Some key BOM analysis capabilities include:
- Identifying parts nearing end-of-life
- Flagging parts with limited or declining supply availability
- Highlighting parts with single-source or high-risk suppliers
- Comparing BOMs across products to identify common at-risk parts
- Generating risk scores to prioritize parts for mitigation actions
With automated BOM monitoring, companies can identify obsolescence risks early in the product lifecycle and take action before issues impact production.
Supply Chain Collaboration
Obsolescence management often requires close collaboration with suppliers to gather information about part lifecycles, identify alternative parts, and develop mitigation strategies. Obsolescence management software can facilitate this collaboration by providing portals for suppliers to share data and communicate with internal teams.
Some ways software enhances supply chain collaboration include:
- Allowing suppliers to upload part datasheets, lifecycle notices, and other relevant documents
- Enabling suppliers to propose alternative parts and substitutes
- Providing a platform for suppliers and internal teams to discuss obsolescence issues and mitigation plans
- Automating data sharing between supplier systems and the obsolescence management platform
By fostering closer collaboration with suppliers, companies can gain better visibility into upcoming obsolescence risks and work proactively with suppliers to address them.
Automated Alerts and Notifications
One of the challenges of obsolescence management is keeping track of the constant deluge of product change notices (PCNs) and end-of-life (EOL) notices from suppliers. These documents inform customers of upcoming changes to parts, including obsolescence, but they can be easy to miss or overlook.
Obsolescence management software can automate the processing of PCNs and EOL notices, extracting key information and matching it to the parts in a company’s BOMs. The software can then generate alerts and notifications to the appropriate teams, ensuring that obsolescence risks are promptly identified and addressed.
Automated alerts can be triggered by various events, such as:
- Receipt of a PCN or EOL notice for a part in a BOM
- A part reaching a certain lifecycle stage (e.g. “obsolete”)
- Inventory levels of a part falling below a certain threshold
- A single-source supplier discontinuing a part
By automating notifications, obsolescence management software helps ensure that the right people are informed of obsolescence risks at the right time, reducing the chances of issues slipping through the cracks.
Mitigation Strategy Development
Once obsolescence risks have been identified, the next step is to develop and execute mitigation strategies. Obsolescence management software can support this process by providing tools for evaluating different mitigation options and tracking the implementation of mitigation plans.
Common obsolescence mitigation strategies include:
Strategy | Description |
---|---|
Last-time buy | Purchasing enough parts to support production until a redesign is completed |
Alternate part substitution | Identifying and qualifying a different part that can be used in place of the obsolete one |
Redesign | Modifying the product design to eliminate the need for the obsolete part |
Aftermarket sourcing | Purchasing parts from brokers or other secondary market sources |
Obsolescence management software can help companies evaluate the feasibility, cost, and risk of each mitigation option, taking into account factors like:
- Availability and cost of alternate parts
- Inventory levels and projected usage rates
- Time and cost required for redesigns
- Reliability and quality risks of aftermarket parts
The software can also provide workflow tools for assigning tasks, tracking progress, and documenting decisions related to mitigation plans.
Analytics and Reporting
Finally, obsolescence management software can provide analytics and reporting capabilities to help companies monitor the effectiveness of their obsolescence management programs and identify areas for improvement.
Key metrics and reports might include:
- Number of parts at each lifecycle stage
- Percentage of BOMs with high-risk parts
- Average time to identify and mitigate obsolescence risks
- Cost avoidance from proactive obsolescence management
- Supplier performance metrics (e.g. responsiveness to obsolescence inquiries, number of obsolete parts)
By regularly reviewing these metrics and reports, companies can continuously improve their obsolescence management processes and demonstrate the value of their obsolescence management investments to stakeholders.
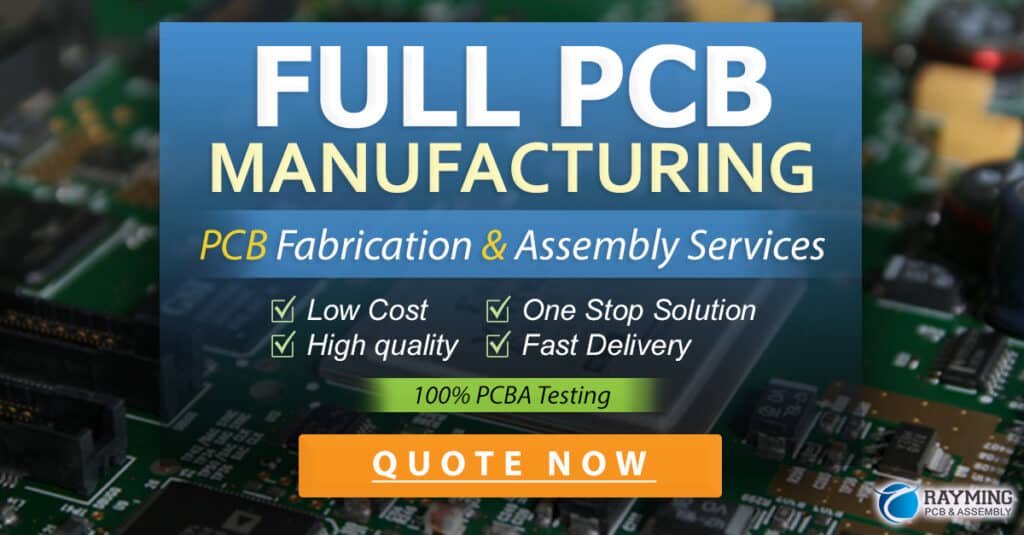
Implementing Obsolescence Management Software
While obsolescence management software can provide significant benefits, implementing it successfully requires careful planning and change management. Some best practices for implementation include:
-
Clearly define goals and requirements for the software, focusing on the most critical obsolescence management pain points and opportunities.
-
Evaluate multiple software options and select one that aligns with the company’s specific needs and existing systems and processes.
-
Develop a data migration and integration plan to ensure that all relevant data is accurately loaded into the new system and kept up-to-date.
-
Provide training and support to help users adapt to the new software and processes, emphasizing the benefits and value of proactive obsolescence management.
-
Establish clear roles and responsibilities for obsolescence management activities, including data maintenance, risk assessment, and mitigation planning.
-
Continuously monitor and optimize the obsolescence management process, using data and feedback from the software to identify areas for improvement.
By following these best practices, companies can realize the full potential of obsolescence management software and create a culture of proactive, data-driven obsolescence management.
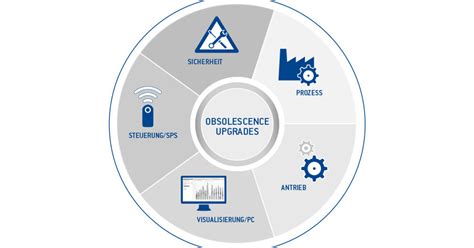
Frequently Asked Questions
What types of companies can benefit from obsolescence management software?
Any company that relies on electronic components, mechanical parts, or other materials with limited lifecycles can benefit from obsolescence management software. This includes companies in industries like aerospace, defense, automotive, medical devices, and industrial equipment.
How does obsolescence management software integrate with other business systems?
Obsolescence management software typically integrates with other systems like ERP, PLM, and supply chain management platforms to exchange data about parts, BOMs, and supplier information. Integration can be achieved through APIs, file transfers, or direct database connections.
How much does obsolescence management software cost?
Costs for obsolescence management software vary depending on factors like the size of the organization, the number of users, and the specific features and capabilities required. Some software is priced based on a per-user or per-part model, while others charge a flat annual fee. Implementation and training costs may also need to be considered.
How long does it take to implement obsolescence management software?
Implementation timelines can range from a few weeks to several months, depending on the complexity of the software and the amount of data that needs to be migrated. A typical implementation might include phases for data preparation, software configuration, testing, and user training.
What are the key success factors for an obsolescence management program?
Some of the key success factors for obsolescence management include:
- Executive sponsorship and cross-functional alignment
- Clearly defined processes and metrics
- Accurate and up-to-date data about parts and BOMs
- Close collaboration with suppliers and internal stakeholders
- Continuous monitoring and improvement of the obsolescence management process
By addressing these factors and leveraging the capabilities of obsolescence management software, companies can create a robust and effective obsolescence management program.
Conclusion
In today’s fast-paced, constantly evolving business environment, obsolescence is a fact of life for many companies. But with the right tools and strategies, it doesn’t have to be a constant source of surprises and disruptions.
By implementing obsolescence management software, companies can gain the visibility, insights, and collaboration capabilities they need to proactively identify and mitigate obsolescence risks. From automated BOM monitoring and risk assessment to streamlined mitigation planning and execution, these platforms provide a comprehensive toolkit for managing obsolescence across the product lifecycle.
Of course, software alone is not a silver bullet. To truly master obsolescence management, companies must also foster a culture of proactive risk management, build strong relationships with suppliers, and continuously monitor and optimize their processes.
But with the right combination of tools, processes, and people, companies can turn obsolescence management from a reactive fire drill into a strategic advantage. By staying ahead of obsolescence risks and minimizing disruptions, they can reduce costs, improve customer satisfaction, and focus on what matters most: innovating and delivering value to their customers.
No responses yet