What are Annular rings?
Annular rings, also known as PCB annular rings, refer to the copper-plated holes or vias that allow electrical connections between different layers of a printed circuit board (PCB). These rings are critical components in PCB Design and manufacturing, as they ensure reliable electrical connectivity and signal integrity throughout the board.
Key Characteristics of Annular Rings
Annular rings have several key characteristics that make them essential for PCB functionality:
-
Conductivity: Annular rings are made of copper, which is an excellent conductor of electricity. This ensures that signals can travel efficiently between layers of the PCB.
-
Mechanical strength: The copper plating around the holes provides mechanical strength to the PCB, preventing the holes from deforming or breaking during the manufacturing process or when the board is subjected to stress.
-
Thermal management: Annular rings can also help with thermal management by providing a path for heat to dissipate from the PCB.
The Importance of Annular Rings in PCB Design
Signal Integrity
One of the primary reasons annular rings are crucial in PCB design is their role in maintaining signal integrity. As electronic devices become more complex and operate at higher frequencies, the demand for reliable signal transmission increases. Annular rings help to minimize signal loss and ensure that signals travel efficiently between layers of the PCB.
Manufacturability
Annular rings also play a significant role in the manufacturability of PCBs. The size and placement of annular rings can affect the ease with which a PCB can be manufactured. For example, if the annular rings are too small or too close together, it may be difficult to drill the holes accurately, leading to manufacturing defects.
Reliability
The reliability of a PCB is directly related to the quality of its annular rings. Poor quality annular rings can lead to electrical failures, such as open circuits or short circuits, which can cause the PCB to malfunction or fail entirely. Ensuring that annular rings are properly designed and manufactured is essential for creating reliable PCBs.
Annular Ring Design Considerations
When designing annular rings for a PCB, several factors must be considered to ensure optimal performance and manufacturability.
Annular Ring Size
The size of the annular ring is one of the most critical design considerations. The annular ring must be large enough to provide a reliable electrical connection and mechanical strength, but not so large that it takes up too much space on the PCB.
The minimum annular ring size is typically determined by the PCB Manufacturer and is based on the capabilities of their manufacturing process. The following table provides general guidelines for minimum annular ring sizes based on the hole size:
Hole Size (mm) | Minimum Annular Ring (mm) |
---|---|
0.2 – 0.4 | 0.125 |
0.4 – 0.6 | 0.150 |
0.6 – 1.0 | 0.200 |
1.0 – 2.0 | 0.250 |
Annular Ring Placement
The placement of annular rings on a PCB is also a critical design consideration. Annular rings should be placed in a way that minimizes the risk of manufacturing defects and ensures reliable electrical connections.
Some key guidelines for annular ring placement include:
-
Clearance: Ensure that there is sufficient clearance between annular rings and other components on the PCB to prevent short circuits and other manufacturing defects.
-
Symmetry: Place annular rings symmetrically around the hole to ensure even distribution of mechanical stress and prevent deformation during the manufacturing process.
-
Spacing: Maintain appropriate spacing between annular rings to prevent electrical interference and ensure reliable signal transmission.
Material Selection
The material used for the PCB substrate and the copper plating can also affect the performance and reliability of annular rings. The most common PCB substrate materials are:
-
FR-4: A glass-reinforced epoxy laminate that is widely used in PCB manufacturing due to its good mechanical and electrical properties.
-
High-Tg FR-4: A variant of FR-4 with improved thermal stability, making it suitable for high-temperature applications.
-
Polyimide: A high-performance polymer that offers excellent thermal stability and mechanical strength, making it ideal for demanding applications such as aerospace and military electronics.
The choice of copper plating also influences the performance of annular rings. Some common copper plating options include:
-
Electroless Copper (ENIG): A thin layer of gold over a nickel-plated copper surface, providing good solderability and corrosion resistance.
-
Immersion Silver (IAg): A thin layer of silver over the copper surface, offering good solderability and electrical conductivity.
-
Immersion Tin (ISn): A thin layer of tin over the copper surface, providing good solderability and oxidation resistance.
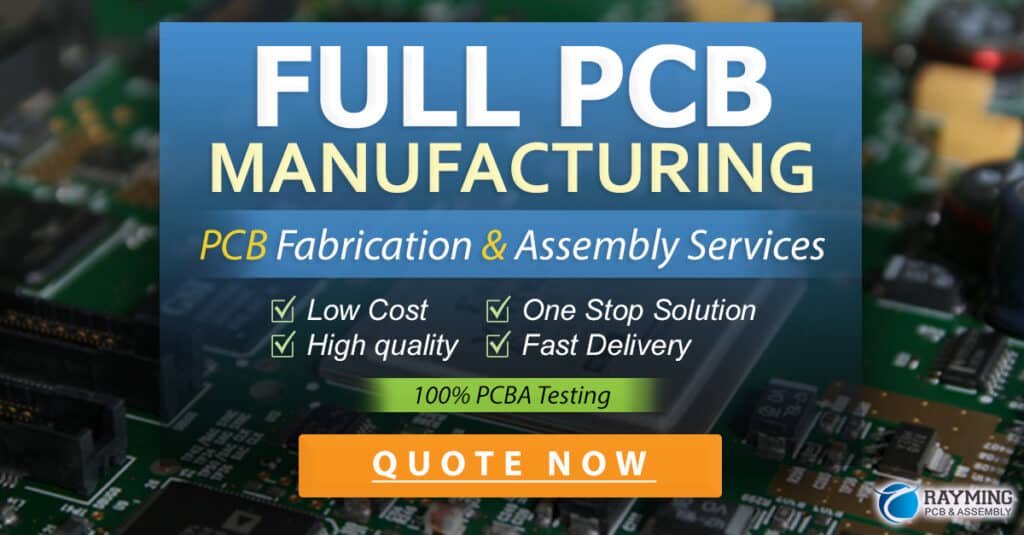
Annular Ring Manufacturing Process
The manufacturing process for annular rings involves several key steps to ensure the quality and reliability of the final product.
Drilling
The first step in creating annular rings is drilling the holes in the PCB substrate. This is typically done using a computer-controlled drilling machine that ensures precise hole placement and size.
Desmearing
After drilling, the holes are cleaned using a process called desmearing, which removes any debris or resin smearing that may have occurred during drilling. This ensures that the copper plating can adhere properly to the hole walls.
Copper Plating
Once the holes are cleaned, they are plated with copper to create the annular rings. This is typically done using an electroplating process, where the PCB is immersed in a copper solution and an electric current is applied to deposit the copper onto the hole walls.
Inspection
After copper plating, the PCB undergoes a thorough inspection to ensure that the annular rings meet the required specifications for size, placement, and quality. This may involve visual inspection, electrical testing, and cross-sectional analysis.
Common Annular Ring Defects and How to Prevent Them
Despite careful design and manufacturing processes, annular rings can still be subject to various defects that can affect the performance and reliability of the PCB.
Insufficient Annular Ring
An insufficient annular ring occurs when the copper plating around the hole is too thin or uneven, resulting in a weak electrical connection and reduced mechanical strength. This can be caused by improper plating processes or incorrect hole sizing.
To prevent insufficient annular rings, ensure that:
- The hole size is appropriate for the desired annular ring size.
- The plating process is properly controlled and monitored.
- The PCB substrate is clean and free of contaminants that may interfere with plating adhesion.
Annular Ring Breakout
Annular ring breakout occurs when the copper plating separates from the hole wall, creating an open circuit or weak connection. This can be caused by mechanical stress during the manufacturing process or thermal stress during operation.
To prevent annular ring breakout, ensure that:
- The annular ring size is sufficiently large to provide mechanical strength.
- The PCB substrate material is appropriate for the intended application and operating conditions.
- The PCB is handled and stored properly to minimize mechanical stress.
Annular Ring Short
An annular ring short occurs when the copper plating bridges the gap between adjacent annular rings, creating an unintended electrical connection. This can be caused by improper annular ring placement or overplating.
To prevent annular ring shorts, ensure that:
- The annular rings are placed with sufficient clearance between them.
- The plating process is properly controlled to prevent excessive copper deposition.
- The PCB design is reviewed and optimized to minimize the risk of shorts.
FAQ
- What is the purpose of annular rings in PCBs?
Annular rings provide electrical connectivity between different layers of a PCB and ensure signal integrity and mechanical strength.
- How does the size of annular rings affect PCB performance?
The size of annular rings affects both the electrical and mechanical properties of the PCB. Larger annular rings provide better mechanical strength and electrical connectivity, but take up more space on the board.
- What materials are commonly used for PCB substrates and copper plating?
Common PCB substrate materials include FR-4, High-Tg FR-4, and polyimide. Copper plating options include electroless nickel immersion gold (ENIG), immersion silver (IAg), and immersion tin (ISn).
- What are some common defects that can occur in annular rings?
Common annular ring defects include insufficient annular rings, annular ring breakout, and annular ring shorts. These defects can be caused by improper design, manufacturing processes, or handling.
- How can annular ring defects be prevented?
Annular ring defects can be prevented by ensuring proper design (e.g., appropriate annular ring size and placement), controlling manufacturing processes (e.g., plating and drilling), and handling the PCB with care to minimize mechanical stress.
Conclusion
Annular rings are essential components in PCB design and manufacturing, providing reliable electrical connectivity and mechanical strength. By understanding the key characteristics, design considerations, and manufacturing processes involved in creating annular rings, PCB designers and manufacturers can ensure the production of high-quality, reliable PCBs.
Proper design, material selection, and process control are critical for preventing common annular ring defects and ensuring optimal PCB performance. As electronic devices continue to advance and become more complex, the importance of well-designed and manufactured annular rings will only continue to grow.
No responses yet