Introduction to Signal Return Path
In the world of high-performance mixed-signal printed circuit board (PCB) design, understanding the concept of signal return path is crucial for ensuring the integrity and reliability of the system. The signal return path is the route that electrical currents take to complete a circuit, and it plays a vital role in managing noise, crosstalk, and electromagnetic interference (EMI) in mixed-signal PCBs.
What is a Mixed-Signal PCB?
A mixed-signal PCB is a circuit board that incorporates both analog and digital signals on the same board. These boards are commonly used in applications such as:
- Telecommunications equipment
- Automotive electronics
- Medical devices
- Industrial control systems
Designing mixed-signal PCBs presents unique challenges due to the coexistence of sensitive analog circuits and high-speed digital circuits on the same board. One of the most critical aspects of mixed-signal PCB design is managing the signal return path effectively.
The Importance of Signal Return Path
The signal return path is essential for several reasons:
-
Circuit Completion: Electrical currents always flow in closed loops, and the signal return path provides the necessary route for the current to return to its source, completing the circuit.
-
Noise Reduction: A well-designed signal return path helps minimize noise coupling between different parts of the circuit by providing a low-impedance path for return currents.
-
EMI Mitigation: Properly managing the signal return path can help reduce electromagnetic interference (EMI) by minimizing the loop area between the signal trace and its return path.
-
Signal Integrity: A clean and uninterrupted signal return path ensures that signals maintain their integrity as they propagate through the PCB, reducing distortion and ensuring reliable operation.
AC vs. DC Return Path
In mixed-signal PCBs, it is essential to understand the difference between AC and DC return paths and how they impact the overall performance of the system.
DC Return Path
The DC return path is the route taken by low-frequency currents, typically below 1 kHz, to return to their source. These currents are primarily associated with power supply and biasing circuits. In a mixed-signal PCB, the DC return path is usually provided by a ground plane or a combination of ground planes and traces.
Design Considerations for DC Return Path
-
Ground Plane: Use a continuous ground plane whenever possible to provide a low-impedance return path for DC currents. This helps minimize voltage drops and ensures stable reference voltages throughout the PCB.
-
Partitioning: Partition the ground plane into separate sections for analog and digital circuits to minimize noise coupling between them. Use a single point of connection, often called a “star ground,” to join the analog and digital ground planes.
-
Trace Routing: When routing DC power traces, keep them as short and wide as possible to minimize resistance and voltage drop. Avoid routing power traces near sensitive analog circuits to reduce the risk of noise coupling.
AC Return Path
The AC return path is the route taken by high-frequency currents, typically above 1 MHz, to return to their source. These currents are primarily associated with high-speed digital signals and RF circuits. In a mixed-signal PCB, the AC return path is usually provided by a ground plane located directly beneath the signal trace.
Design Considerations for AC Return Path
-
Ground Plane Proximity: Route high-speed digital signals and RF traces as close to the ground plane as possible to minimize loop area and reduce inductance. This helps maintain signal integrity and minimizes EMI.
-
Trace Geometry: Keep high-speed digital traces as short and straight as possible to minimize reflections and signal distortion. Avoid sharp bends or discontinuities that can cause impedance mismatches.
-
Via Placement: Place vias strategically to provide a low-impedance connection between the signal trace and the ground plane. Minimize the distance between the signal via and its corresponding ground via to reduce loop area and inductance.
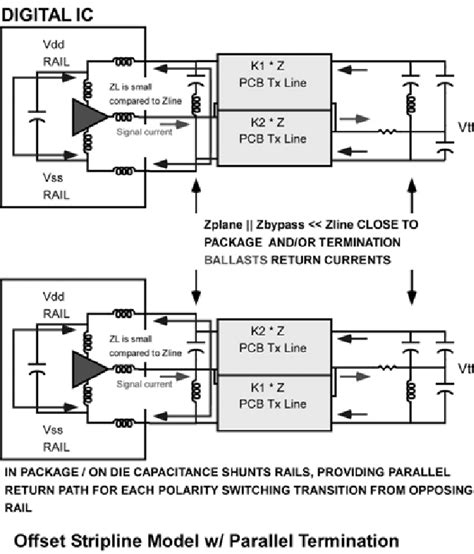
Signal Return Path Management Techniques
Effective management of the signal return path in mixed-signal PCBs involves several techniques and best practices. Some of the most important ones are:
Ground Plane Design
A well-designed ground plane is the foundation of a robust signal return path. Consider the following guidelines when designing ground planes for mixed-signal PCBs:
-
Uninterrupted Ground Plane: Maintain a continuous ground plane throughout the PCB whenever possible. Avoid splitting the ground plane or creating large gaps, as this can disrupt the return path and cause EMI issues.
-
Ground Plane Thickness: Use a sufficiently thick ground plane to minimize resistance and provide a low-impedance return path. A typical thickness for a ground plane in a mixed-signal PCB is 1 oz. copper (35 µm).
-
Ground Plane Partitioning: Partition the ground plane into separate sections for analog and digital circuits to minimize noise coupling. Use a single point of connection, such as a star ground, to join the analog and digital ground planes.
Trace Routing and Geometry
Proper trace routing and geometry are crucial for maintaining signal integrity and minimizing EMI in mixed-signal PCBs. Consider the following guidelines:
-
Trace Width: Use appropriate trace widths based on the current carrying requirements and the desired characteristic impedance. Wider traces have lower resistance and can carry more current, but they also have higher capacitance and may require more space on the PCB.
-
Trace Spacing: Maintain adequate spacing between traces to minimize crosstalk and coupling. The spacing required depends on factors such as the signal frequency, trace geometry, and the dielectric constant of the PCB material.
-
Trace Length Matching: Match the lengths of critical signal traces, such as differential pairs or clock signals, to ensure proper timing and minimize skew. Use serpentine routing or delay lines to adjust trace lengths when necessary.
Via Design and Placement
Vias are essential for connecting signal traces to ground planes and other layers in a multi-layer PCB. Proper via design and placement are crucial for maintaining signal integrity and minimizing EMI. Consider the following guidelines:
-
Via Size: Use appropriately sized vias based on the current carrying requirements and the desired impedance. Larger vias have lower resistance and inductance but may require more space on the PCB.
-
Via Placement: Place vias strategically to provide a low-impedance connection between the signal trace and the ground plane. Minimize the distance between the signal via and its corresponding ground via to reduce loop area and inductance.
-
Via Stitching: Use via stitching techniques to create a low-impedance connection between ground planes on different layers. This helps maintain a continuous return path and minimizes EMI.
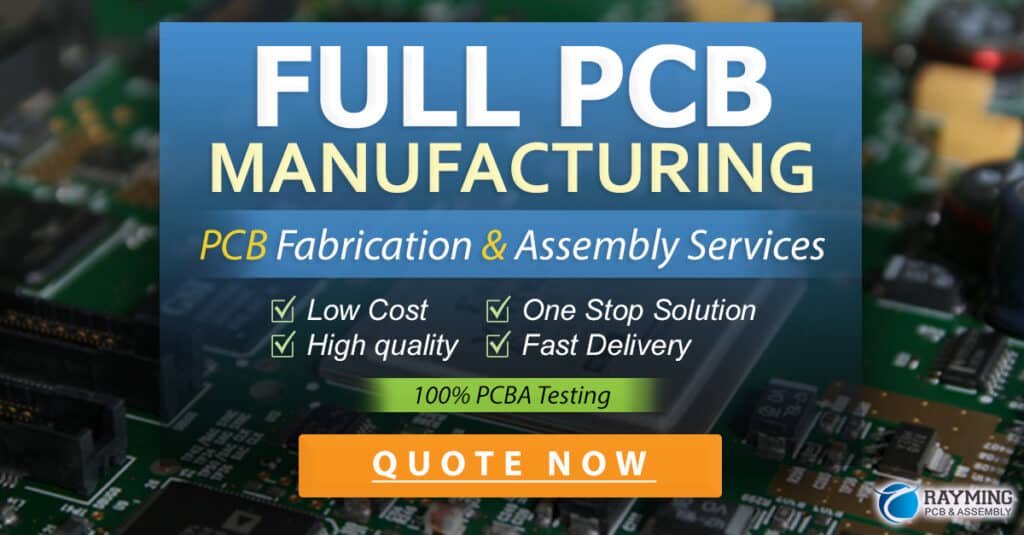
PCB Layer Stackup Design
The layer stackup of a mixed-signal PCB plays a crucial role in managing the signal return path and ensuring overall system performance. Consider the following guidelines when designing the layer stackup:
-
Signal Layers: Arrange signal layers to minimize crosstalk and coupling between different signal types. Place high-speed digital signals on layers adjacent to ground planes to minimize loop area and reduce EMI.
-
Ground Layers: Use dedicated ground layers to provide a low-impedance return path for signals. Place ground layers strategically to minimize the distance between signal traces and their corresponding return paths.
-
Power Layers: Use dedicated power layers to distribute power to different parts of the circuit. Place power layers close to the ground layers to minimize inductance and provide a low-impedance return path for power supply currents.
Layer | Type | Description |
---|---|---|
1 | Signal | Top layer for high-speed digital and analog signals |
2 | Ground | Ground plane for high-speed digital signals |
3 | Signal | Inner layer for low-speed digital and analog signals |
4 | Power | Power plane for analog and digital circuits |
5 | Signal | Inner layer for low-speed digital and analog signals |
6 | Ground | Ground plane for low-speed digital and analog signals |
7 | Signal | Bottom layer for high-speed digital and analog signals |
Table 1: Example of a 7-layer mixed-signal PCB stackup
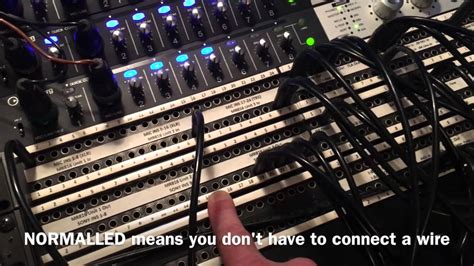
Simulation and Analysis
To ensure the effectiveness of the signal return path design, it is essential to perform simulations and analyses before finalizing the PCB layout. Some of the key simulations and analyses include:
-
Electromagnetic Simulation: Use electromagnetic simulation tools to analyze the behavior of high-speed signals and identify potential issues such as impedance mismatches, reflections, and crosstalk.
-
Power Integrity Analysis: Perform power integrity analysis to ensure that the power distribution network provides a stable and clean supply voltage to all parts of the circuit. Analyze voltage drops, current densities, and decoupling capacitor placement to optimize the power delivery system.
-
Signal Integrity Analysis: Perform signal integrity analysis to ensure that critical signals maintain their integrity as they propagate through the PCB. Analyze factors such as rise time, overshoot, undershoot, and jitter to identify potential signal quality issues.
Real-World Examples
To illustrate the importance of signal return path management in mixed-signal PCBs, let’s look at a few real-world examples:
Example 1: Automotive Infotainment System
An automotive infotainment system is a mixed-signal PCB that incorporates both analog audio circuits and high-speed digital video and communication interfaces. Proper management of the signal return path is crucial for ensuring the quality of the audio and video signals and minimizing EMI that could interfere with other electronic systems in the vehicle.
In this example, the PCB designer used a 10-layer stackup with dedicated ground planes for the analog and digital sections of the board. The high-speed digital signals were routed on layers adjacent to the digital ground plane, while the analog signals were routed on layers adjacent to the analog ground plane. The ground planes were connected using a star ground topology to minimize noise coupling between the analog and digital sections.
Example 2: Medical Ultrasound Imaging System
A medical ultrasound imaging system is a mixed-signal PCB that incorporates high-frequency analog transducer circuits and high-speed digital signal processing and communication interfaces. Effective management of the signal return path is essential for maintaining the integrity of the weak echo signals received by the transducers and minimizing noise that could degrade image quality.
In this example, the PCB designer used a 12-layer stackup with dedicated ground planes for the analog and digital sections of the board. The high-frequency analog signals were routed on layers adjacent to the analog ground plane, while the high-speed digital signals were routed on layers adjacent to the digital ground plane. The ground planes were connected using a multi-point ground topology to minimize ground bounce and ensure a stable reference voltage for the analog circuits.
Frequently Asked Questions (FAQ)
-
What is the difference between a ground plane and a power plane?
A ground plane is a continuous layer of copper that provides a low-impedance return path for electrical currents. A power plane, on the other hand, is a continuous layer of copper that distributes power to different parts of the circuit. Ground planes and power planes work together to create a stable reference voltage and minimize noise in the system. -
Why is it important to partition the ground plane in a mixed-signal PCB?
Partitioning the ground plane into separate sections for analog and digital circuits helps minimize noise coupling between the two domains. Analog circuits are sensitive to noise and require a clean and stable reference voltage, while digital circuits generate high-frequency noise that can interfere with analog signals. By partitioning the ground plane and using a star ground topology, the designer can effectively isolate the analog and digital sections of the board and minimize noise coupling. -
What is the purpose of via stitching in a mixed-signal PCB?
Via stitching is a technique used to create a low-impedance connection between ground planes on different layers of the PCB. By placing vias at regular intervals along the edge of the ground plane, the designer can effectively “stitch” the planes together, creating a continuous return path for electrical currents. Via stitching helps minimize EMI and ensure a stable reference voltage throughout the board. -
How can I determine the appropriate trace width and spacing for my mixed-signal PCB?
The appropriate trace width and spacing depend on several factors, including the signal frequency, current carrying requirements, and the desired characteristic impedance. There are various online calculators and design tools that can help you determine the optimal trace width and spacing based on your specific requirements. In general, wider traces have lower resistance and can carry more current, while larger spacing between traces helps minimize crosstalk and coupling. -
What are some common simulation and analysis tools used for mixed-signal PCB design?
Some common simulation and analysis tools used for mixed-signal PCB design include: - Electromagnetic simulation tools such as Ansys HFSS, Keysight ADS, and Altium Designer
- Power integrity analysis tools such as Ansys SIwave, Cadence Sigrity, and Mentor Graphics HyperLynx
- Signal integrity analysis tools such as Ansys Nexxim, Cadence Sigrity, and Mentor Graphics HyperLynx
These tools allow designers to analyze the behavior of high-speed signals, optimize power delivery systems, and ensure the overall performance and reliability of the mixed-signal PCB.
Conclusion
Understanding and effectively managing the signal return path is crucial for the successful design of high-performance mixed-signal PCBs. By carefully considering factors such as ground plane design, trace routing and geometry, via placement, and layer stackup, designers can minimize noise, crosstalk, and EMI while ensuring the integrity and reliability of the system.
Through the use of appropriate design techniques, simulation and analysis tools, and adherence to best practices, mixed-signal PCB designers can create robust and reliable systems that meet the demanding requirements of modern electronic applications.
No responses yet