What is an Ultrasonic Sensor?
An ultrasonic sensor is a type of electronic device that measures the distance to an object using ultrasonic sound waves. It works by emitting high-frequency sound waves and measuring the time it takes for the waves to bounce back after hitting an object. The sensor then calculates the distance based on the speed of sound and the time taken for the echo to return.
Ultrasonic sensors are widely used in various applications, such as:
- Object detection and avoidance in robotics
- Liquid level measurement in tanks
- Parking sensors in automobiles
- Proximity sensing in security systems
- Medical imaging and diagnostics
Components of an Ultrasonic Sensor
A typical ultrasonic sensor consists of the following components:
-
Transmitter: The transmitter is responsible for emitting the ultrasonic sound waves. It usually consists of a piezoelectric crystal that vibrates at a specific frequency when an electrical signal is applied to it.
-
Receiver: The receiver is a microphone that detects the reflected sound waves. It converts the received acoustic energy into electrical signals for further processing.
-
Control and Processing Unit: This unit generates the electrical signals for the transmitter and processes the received signals from the receiver. It calculates the distance based on the time difference between the transmitted and received signals.
-
Transducer Housing: The transducer housing encapsulates the transmitter and receiver, protecting them from external factors such as dust, moisture, and mechanical damage.
How Does an Ultrasonic Sensor Work?
The working principle of an ultrasonic sensor is based on the time-of-flight (TOF) method. Here’s a step-by-step explanation of how an ultrasonic sensor operates:
-
The control unit generates a short electrical pulse, typically lasting a few microseconds, which is applied to the transmitter.
-
The transmitter converts the electrical pulse into an ultrasonic sound wave, usually at a frequency of 40 kHz or higher. The sound wave propagates through the medium (usually air) at the speed of sound.
-
When the sound wave encounters an object, it reflects off the object’s surface and travels back towards the sensor.
-
The reflected sound wave, or echo, is detected by the receiver, which converts it into an electrical signal.
-
The control unit measures the time interval between the transmission of the sound wave and the reception of the echo. This time interval is called the time-of-flight (TOF).
-
Knowing the speed of sound in the medium (approximately 343 m/s in air at room temperature), the distance to the object can be calculated using the following formula:
Distance = (Speed of Sound × Time-of-Flight) / 2
The division by 2 accounts for the fact that the sound wave travels twice the distance between the sensor and the object (forward and backward).
Strengths of Ultrasonic Sensors
Ultrasonic sensors offer several advantages that make them suitable for a wide range of applications:
-
Non-contact Sensing: Ultrasonic sensors can measure distances without physical contact with the target object. This makes them suitable for applications where contact is not possible or desirable, such as liquid level measurement or object detection in harsh environments.
-
Accurate and Reliable: Ultrasonic sensors provide accurate distance measurements with a typical accuracy of ±1% of the measured distance. They are also highly reliable and can operate consistently over long periods.
-
Wide Detection Range: Ultrasonic sensors can detect objects at distances ranging from a few centimeters to several meters, depending on the sensor’s specifications and the operating environment.
-
Insensitive to Color and Transparency: Unlike optical sensors, ultrasonic sensors are not affected by the color, transparency, or reflectivity of the target object. They can detect objects made of various materials, including plastics, metals, liquids, and even transparent objects.
-
Immune to Electromagnetic Interference: Ultrasonic sensors are not affected by electromagnetic interference (EMI) from other electronic devices or sources. This makes them suitable for use in environments with high levels of EMI, such as industrial settings.
-
Cost-effective: Ultrasonic sensors are relatively inexpensive compared to other sensing technologies, such as laser rangefinders or radar sensors. This makes them an attractive option for cost-sensitive applications.
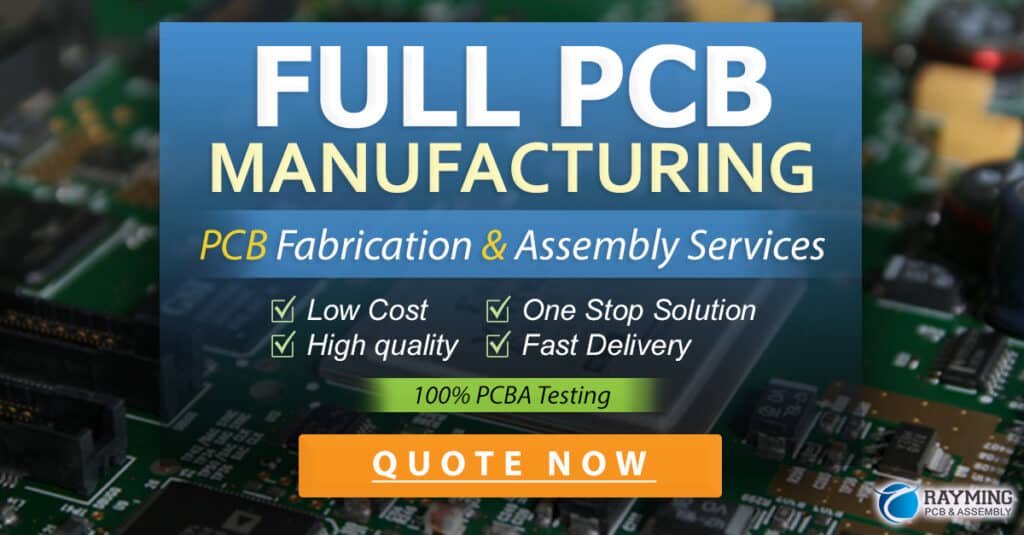
Weaknesses of Ultrasonic Sensors
Despite their numerous advantages, ultrasonic sensors also have some limitations and drawbacks:
-
Limited Angular Resolution: Ultrasonic sensors have a relatively wide beam angle, typically ranging from 15 to 30 degrees. This means that they cannot distinguish between objects that are close to each other within the beam width. This limitation can be overcome by using multiple sensors or by employing more advanced signal processing techniques.
-
Sensitivity to Temperature and Humidity: The speed of sound in air varies with temperature and humidity. As a result, the accuracy of ultrasonic sensors can be affected by changes in environmental conditions. To maintain accuracy, the sensor may need to be calibrated or compensated for temperature and humidity variations.
-
Susceptibility to Acoustic Noise: Ultrasonic sensors can be affected by external acoustic noise sources, such as machinery, air turbulence, or other ultrasonic devices operating in the same frequency range. This can lead to false readings or reduced accuracy.
-
Reduced Performance on Soft or Angled Surfaces: Ultrasonic sensors may have difficulty detecting soft, porous, or angled surfaces. Soft materials, such as foam or fabric, can absorb the sound waves, while angled surfaces can deflect the waves away from the sensor, resulting in weak or no echoes.
-
Minimum Detection Distance: Ultrasonic sensors have a minimum detection distance, typically a few centimeters, due to the time required for the transducer to settle after transmitting the sound wave. Objects closer than this minimum distance cannot be accurately detected.
Applications of Ultrasonic Sensors
Ultrasonic sensors find applications in various fields, thanks to their non-contact sensing, accuracy, and reliability. Some common applications include:
-
Robotics and Automation: Ultrasonic sensors are used in robots for object detection, collision avoidance, and navigation. They help robots sense and navigate their surroundings, enabling tasks such as obstacle avoidance, mapping, and autonomous navigation.
-
Liquid Level Measurement: Ultrasonic sensors are widely used in liquid level measurement systems for tanks, reservoirs, and containers. They provide non-contact, continuous level measurement, even in harsh or corrosive environments.
-
Automotive Industry: Ultrasonic sensors are used in parking assist systems, blind-spot detection, and collision avoidance systems in vehicles. They help drivers maneuver and park safely by detecting nearby objects and providing alerts or automatic braking.
-
Industrial Automation: Ultrasonic sensors are used in various industrial applications, such as material handling, conveyor systems, and packaging machines. They help detect and position objects, measure distances, and control automated processes.
-
Medical and Healthcare: Ultrasonic sensors are used in medical imaging and diagnostic devices, such as ultrasound machines. They enable non-invasive imaging of internal body structures, aiding in the diagnosis and monitoring of various medical conditions.
-
Security and Surveillance: Ultrasonic sensors are used in intrusion detection systems and motion sensors for security applications. They can detect the presence of objects or people in a monitored area and trigger alarms or activate cameras.
Choosing the Right Ultrasonic Sensor
When selecting an ultrasonic sensor for a specific application, several factors should be considered:
-
Range: The sensing range of the ultrasonic sensor should match the requirements of the application. Consider the minimum and maximum distances at which the sensor needs to detect objects.
-
Beam Angle: The beam angle determines the sensor’s field of view. A wider beam angle covers a larger area but may have lower angular resolution. A narrower beam angle provides better resolution but covers a smaller area.
-
Frequency: Ultrasonic sensors operate at different frequencies, typically ranging from 40 kHz to 1 MHz. Higher frequencies offer better resolution and smaller minimum detection distances but have shorter sensing ranges. Lower frequencies have longer ranges but lower resolution.
-
Accuracy and Resolution: Consider the required accuracy and resolution of the distance measurements. Some applications may demand high precision, while others may tolerate a certain level of error.
-
Environmental Conditions: Take into account the environmental conditions in which the sensor will operate. Factors such as temperature, humidity, dust, and vibrations can affect the sensor’s performance and durability.
-
Interface and Communication: Consider how the sensor will interface with the rest of the system. Common interfaces include analog voltage output, digital I2C or SPI communication, and serial communication (e.g., UART).
-
Cost and Availability: Evaluate the cost and availability of the sensor, especially for large-scale or cost-sensitive applications. Consider factors such as the sensor’s price, lead time, and long-term availability from the manufacturer.
Table: Comparison of Ultrasonic Sensor Specifications
Specification | Sensor A | Sensor B | Sensor C |
---|---|---|---|
Range | 2-400 cm | 3-500 cm | 1-200 cm |
Beam Angle | 15° | 20° | 10° |
Frequency | 40 kHz | 50 kHz | 80 kHz |
Accuracy | ±1% | ±0.5% | ±2% |
Resolution | 1 mm | 0.5 mm | 2 mm |
Operating Voltage | 5 V | 3.3 V | 5 V |
Communication | Analog | I2C | UART |
Dimensions (L×W×H) | 45×20×15 mm | 60×20×20 mm | 30×15×10 mm |
Price | $10 | $25 | $8 |
Frequently Asked Questions (FAQ)
-
Q: What is the maximum range of an ultrasonic sensor?
A: The maximum range of an ultrasonic sensor varies depending on the specific model and its operating frequency. Typical ranges can be from a few centimeters up to several meters. High-end ultrasonic sensors can even reach distances of 10 meters or more. -
Q: Can ultrasonic sensors detect transparent objects?
A: Yes, ultrasonic sensors can detect transparent objects because they rely on sound waves rather than visual cues. The sensor emits sound waves that reflect off the surface of the object, regardless of its transparency. -
Q: Are ultrasonic sensors affected by lighting conditions?
A: No, ultrasonic sensors are not affected by lighting conditions. They operate based on the propagation and reflection of sound waves, which are independent of ambient light levels. This makes them suitable for use in dark or poorly lit environments. -
Q: How do ultrasonic sensors handle multiple objects within their field of view?
A: Ultrasonic sensors typically detect the closest object within their field of view. If there are multiple objects at different distances, the sensor will report the distance to the nearest object. Some advanced ultrasonic sensors can provide information about multiple objects by using more sophisticated signal processing techniques. -
Q: Can ultrasonic sensors be used underwater?
A: Yes, ultrasonic sensors can be used underwater, as sound waves propagate well in liquids. However, specialized underwater ultrasonic sensors are required, as they are designed to withstand the pressure and corrosive nature of underwater environments. The sensing range and performance may differ compared to air-based ultrasonic sensors due to the different properties of sound propagation in water.
Conclusion
Ultrasonic sensors are versatile and reliable devices that use sound waves to measure distances and detect objects. They offer numerous advantages, such as non-contact sensing, accuracy, wide detection ranges, and immunity to color and transparency. However, they also have some limitations, including limited angular resolution, sensitivity to temperature and humidity, and reduced performance on soft or angled surfaces.
Ultrasonic sensors find applications in various fields, including robotics, liquid level measurement, automotive industry, industrial automation, medical imaging, and security systems. When choosing an ultrasonic sensor, factors such as range, beam angle, frequency, accuracy, environmental conditions, interface, and cost should be considered to ensure optimal performance for the specific application.
As technology advances, ultrasonic sensors continue to evolve, with improvements in range, resolution, and signal processing capabilities. Researchers and engineers are developing new techniques and algorithms to enhance the performance and overcome the limitations of ultrasonic sensors, expanding their potential applications in the future.
No responses yet