Introduction to COB LED Manufacturing
COB (Chip-on-Board) LED manufacturing is an advanced technique for producing high-power, high-efficiency LED lighting solutions. In COB LED manufacturing, multiple LED chips are directly mounted onto a printed circuit board (PCB) or substrate, which is then encapsulated with a phosphor layer and lens for protection and light diffusion. This process results in a compact, powerful, and efficient LED package that offers several advantages over traditional SMD (Surface-Mounted Device) LEDs.
Advantages of COB LEDs
- High lumen output per unit area
- Improved thermal management
- Better color consistency
- Wider beam angles
- Reduced production costs
COB LED Manufacturing Process
The COB LED manufacturing process involves several key steps, which are outlined below:
Step 1: Substrate Preparation
The first step in COB LED manufacturing is to prepare the substrate or PCB on which the LED chips will be mounted. The substrate material is typically aluminum, which offers excellent thermal conductivity and helps dissipate heat generated by the LED chips. The substrate is cleaned and treated to ensure proper adhesion of the LED chips.
Step 2: Die Bonding
The LED chips, or dies, are then bonded to the substrate using a die bonding machine. This machine precisely places the LED chips onto the substrate and secures them in place using a conductive adhesive or eutectic bonding process. The die bonding process is critical for ensuring proper electrical and thermal contact between the LED chips and the substrate.
Die Bonding Method | Description |
---|---|
Conductive Adhesive | A conductive epoxy is used to bond the LED chips to the substrate. |
Eutectic Bonding | A gold-tin alloy is used to create a metallic bond between the LED chips and the substrate. |
Step 3: Wire Bonding
After die bonding, the LED chips are connected to the substrate’s electrical contacts using a wire bonding process. This involves using ultra-thin gold or aluminum wires to create electrical connections between the LED chips and the substrate. Wire bonding is typically done using a thermosonic or ultrasonic bonding machine.
Step 4: Phosphor Coating
To achieve the desired color temperature and color rendering index (CRI), a phosphor layer is applied over the LED chips. The phosphor material is mixed with a silicone encapsulant and dispensed onto the LED chips using a dispensing machine. The phosphor layer converts some of the blue light emitted by the LED chips into yellow light, resulting in a white light output.
Phosphor Type | Color Temperature Range | CRI Range |
---|---|---|
YAG:Ce | 2700K – 6500K | 70 – 90 |
Nitride | 2700K – 6500K | 80 – 95 |
Silicate | 2700K – 4000K | 90 – 98 |
Step 5: Lens Molding
To protect the LED chips and phosphor layer and to shape the light output, a lens is molded over the COB assembly. The lens material is typically silicone or epoxy, which offers high transparency, durability, and resistance to UV radiation and high temperatures. The lens molding process is done using a high-precision molding machine.
Step 6: Curing and Singulation
After lens molding, the COB assembly undergoes a curing process to ensure the proper hardening of the silicone or epoxy lens. This is typically done in a curing oven at a controlled temperature and duration. Once cured, the COB assembly is singulated, or cut, into individual COB LED units using a dicing saw or laser cutting machine.
Step 7: Testing and Binning
The final step in COB LED manufacturing is testing and binning. Each COB LED unit is tested for electrical, optical, and thermal characteristics to ensure compliance with specified performance parameters. The COB LEDs are then sorted, or binned, based on their luminous flux, color temperature, and forward voltage to ensure consistency within each batch.
Quality Control in COB LED Manufacturing
Ensuring high quality and consistency in COB LED manufacturing requires strict quality control measures throughout the production process. Some key quality control steps include:
- Incoming material inspection
- Process parameter monitoring
- In-line testing and inspection
- Final product testing and certification
Incoming Material Inspection
All raw materials used in COB LED manufacturing, including LED chips, substrates, phosphors, and encapsulants, must undergo thorough incoming inspection to ensure they meet the required specifications. This includes visual inspection, dimensional checks, and material property testing.
Process Parameter Monitoring
During the COB LED manufacturing process, key process parameters such as die bonding temperature, wire bonding force, phosphor dispensing volume, and lens molding pressure must be continuously monitored and controlled to ensure consistency and minimize process variations.
In-line Testing and Inspection
In-line testing and inspection are performed at various stages of the COB LED manufacturing process to identify and correct any defects or deviations from specifications. This includes visual inspection, electrical testing, and optical testing using automated inspection systems.
Final Product Testing and Certification
Before packaging and shipping, each COB LED unit undergoes final testing to ensure compliance with customer specifications and industry standards. This includes measurements of luminous flux, color temperature, CRI, forward voltage, and thermal resistance. COB LEDs that pass final testing are then certified and labeled accordingly.
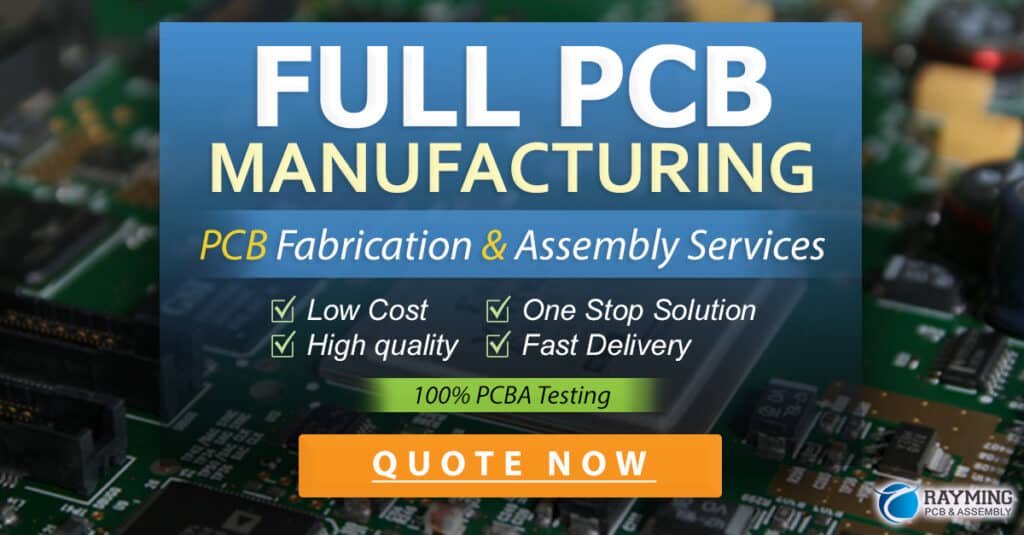
Applications of COB LEDs
COB LEDs offer numerous advantages over traditional lighting technologies, making them suitable for a wide range of applications, including:
- General lighting
- Automotive lighting
- Industrial lighting
- Outdoor lighting
- Horticulture lighting
General Lighting
COB LEDs are increasingly used in general lighting applications, such as residential and commercial indoor lighting, due to their high efficiency, excellent color rendering, and compact form factor. COB LED downlights, track lights, and panel lights are popular choices for energy-efficient and high-quality lighting solutions.
Automotive Lighting
COB LEDs are used in various automotive lighting applications, including headlights, fog lights, and daytime running lights. Their high lumen output, compact size, and durability make them ideal for demanding automotive environments.
Industrial Lighting
In industrial settings, COB LEDs provide high-intensity, uniform lighting for tasks such as inspection, assembly, and material handling. Their high efficiency and long lifespan help reduce energy costs and maintenance requirements in industrial facilities.
Outdoor Lighting
COB LEDs are well-suited for outdoor lighting applications, such as street lighting, parking lot lighting, and stadium lighting, due to their high lumen output, wide beam angles, and resistance to harsh environmental conditions.
Horticulture Lighting
COB LEDs are increasingly used in horticulture lighting applications, such as greenhouse and vertical farming, due to their ability to provide high-intensity, targeted light for plant growth. COB LEDs can be customized to emit specific wavelengths of light that optimize photosynthesis and plant development.
Future Trends in COB LED Manufacturing
As the demand for high-performance, energy-efficient lighting solutions continues to grow, COB LED manufacturing is expected to evolve and innovate in several key areas:
- Higher efficiency and lumen output
- Improved color rendering and consistency
- Advanced thermal management solutions
- Integration of smart features and controls
Higher Efficiency and Lumen Output
COB LED manufacturers are continuously working to improve the efficiency and lumen output of their products by optimizing LED chip design, phosphor composition, and optical design. Advances in materials science and manufacturing processes are expected to drive further gains in COB LED performance.
Improved Color Rendering and Consistency
As the demand for high-quality lighting in applications such as retail, healthcare, and hospitality grows, COB LED manufacturers are focusing on improving color rendering and consistency. This involves the development of advanced phosphor materials and precise color binning techniques to ensure accurate and stable color reproduction.
Advanced Thermal Management Solutions
Effective thermal management is critical for maintaining the performance and longevity of COB LEDs. Manufacturers are developing advanced thermal management solutions, such as high-conductivity substrates, heat pipes, and active cooling systems, to dissipate heat more efficiently and enable higher-power COB LED designs.
Integration of Smart Features and Controls
The integration of smart features and controls into COB LED lighting systems is becoming increasingly popular. This includes the incorporation of sensors, wireless connectivity, and programmable drivers to enable adaptive lighting, energy monitoring, and remote control capabilities. COB LED manufacturers are partnering with technology companies to develop innovative smart lighting solutions.
Frequently Asked Questions (FAQ)
1. What is the difference between COB LEDs and SMD LEDs?
COB LEDs differ from SMD LEDs in their packaging and performance characteristics. In COB LEDs, multiple LED chips are directly mounted onto a substrate and encapsulated with a phosphor layer and lens, resulting in a compact, high-power LED package. SMD LEDs, on the other hand, consist of individual LED chips packaged in a surface-mount device format. COB LEDs generally offer higher lumen output per unit area, better thermal management, and wider beam angles compared to SMD LEDs.
2. What are the advantages of using COB LEDs in lighting applications?
COB LEDs offer several advantages in lighting applications, including:
- High lumen output per unit area, enabling compact and powerful lighting designs
- Improved thermal management, resulting in better performance and longer lifespan
- Better color consistency and rendering, providing high-quality illumination
- Wider beam angles, allowing for more uniform light distribution
- Reduced production costs compared to traditional LED packaging methods
3. How do COB LEDs achieve different color temperatures and CRI values?
COB LEDs achieve different color temperatures and CRI values through the use of phosphor materials. The LED chips emit blue light, which is then partially converted into yellow light by the phosphor layer. The ratio and composition of the phosphor materials determine the resulting color temperature and CRI of the COB LED. Different phosphor types, such as YAG:Ce, nitride, and silicate, are used to achieve specific color characteristics.
4. What are the key quality control measures in COB LED manufacturing?
Key quality control measures in COB LED manufacturing include:
- Incoming material inspection to ensure raw materials meet required specifications
- Process parameter monitoring to maintain consistency and minimize variations
- In-line testing and inspection to identify and correct defects or deviations
- Final product testing and certification to ensure compliance with customer specifications and industry standards
These measures help ensure high quality and consistency in the manufactured COB LED products.
5. What are some of the future trends in COB LED manufacturing?
Future trends in COB LED manufacturing include:
- Continued improvements in efficiency and lumen output through advances in materials and manufacturing processes
- Enhanced color rendering and consistency using advanced phosphor materials and precise color binning techniques
- Development of advanced thermal management solutions to enable higher-power COB LED designs
- Integration of smart features and controls, such as sensors, wireless connectivity, and programmable drivers, to enable adaptive lighting and energy monitoring capabilities
These trends are driven by the growing demand for high-performance, energy-efficient, and intelligent lighting solutions across various applications.
Conclusion
COB LED manufacturing is a cutting-edge technology that offers numerous advantages over traditional LED packaging methods. By directly mounting multiple LED chips onto a substrate and encapsulating them with a phosphor layer and lens, COB LEDs achieve high lumen output, excellent thermal management, and superior color consistency. The COB LED manufacturing process involves several key steps, including substrate preparation, die bonding, wire bonding, phosphor coating, lens molding, curing and singulation, and final testing and binning.
To ensure high quality and consistency, COB LED manufacturers implement strict quality control measures throughout the production process, such as incoming material inspection, process parameter monitoring, in-line testing and inspection, and final product testing and certification.
COB LEDs find applications in a wide range of industries, including general lighting, automotive lighting, industrial lighting, outdoor lighting, and horticulture lighting. As the demand for energy-efficient and high-performance lighting solutions continues to grow, COB LED manufacturing is expected to evolve and innovate, with future trends focusing on higher efficiency and lumen output, improved color rendering and consistency, advanced thermal management solutions, and the integration of smart features and controls.
By understanding the COB LED manufacturing process, its advantages, applications, and future trends, lighting designers, engineers, and end-users can make informed decisions when selecting and implementing COB LED lighting solutions for their specific needs.
No responses yet