Introduction to BGA PCB Soldering
Ball Grid Array (BGA) is a surface-mount packaging used for integrated circuits (ICs) that utilizes an array of solder balls to connect the IC to the printed circuit board (PCB). BGA packages offer numerous advantages, including high interconnect density, improved electrical and thermal performance, and reduced package size. However, the soldering process for BGA components is more complex compared to traditional through-hole or surface-mount components, making it prone to various soldering errors.
Importance of Proper BGA Soldering
Proper BGA soldering is crucial for ensuring the reliability and functionality of electronic devices. Soldering errors can lead to issues such as:
– Intermittent or complete failure of the device
– Reduced product lifespan
– Increased manufacturing costs due to rework or scrap
– Potential safety hazards, especially in critical applications
Understanding and identifying common BGA soldering errors is essential for implementing effective process controls and improving the overall quality of the final product.
Common BGA Soldering Error Categories
1. Bridging
Bridging is one of the most common BGA soldering errors, occurring when excess solder creates an unintended connection between two or more solder balls or pads. This error can cause short circuits, leading to device malfunction or failure.
Causes of Bridging
- Excessive solder paste application
- Incorrect solder paste stencil design or alignment
- Inadequate solder mask clearance between pads
- Improper reflow profile (e.g., insufficient peak temperature or time above liquidus)
- Component misalignment during placement
Prevention and Mitigation Strategies
- Optimize solder paste stencil design and thickness
- Ensure proper solder paste application and stencil alignment
- Maintain adequate solder mask clearance between pads
- Implement a well-controlled reflow profile
- Utilize automated component placement with vision systems for accurate alignment
2. Voiding
Voiding refers to the formation of air pockets or voids within the solder joint, which can compromise the mechanical strength and thermal conductivity of the connection. Voids can be categorized as macro-voids (larger than 100 μm) or micro-voids (smaller than 100 μm).
Causes of Voiding
- Outgassing of flux or other volatiles during the reflow process
- Inadequate solder paste volume or improper paste formulation
- Incorrect reflow profile (e.g., rapid heating or cooling rates)
- Contamination or oxidation of the solder paste or pad surfaces
- Inadequate venting of the BGA package during reflow
Prevention and Mitigation Strategies
- Select solder paste with low voiding characteristics and appropriate flux chemistry
- Optimize the reflow profile to minimize outgassing and ensure proper wetting
- Implement nitrogen reflow to reduce oxidation and improve wetting
- Utilize vacuum soldering or vapor phase soldering techniques to minimize voiding
- Ensure proper storage and handling of solder paste to prevent contamination or degradation
3. Non-Wetting and De-Wetting
Non-wetting occurs when the molten solder fails to adhere to the pad or ball surface, resulting in an incomplete or absent solder joint. De-wetting is a related issue where the solder initially wets the surface but then recedes, leaving a thin, non-uniform coating.
Causes of Non-Wetting and De-Wetting
- Contamination or oxidation of the pad or ball surfaces
- Insufficient flux activity or incorrect flux chemistry
- Inadequate preheat or peak temperature during reflow
- Rapid cooling rates that cause the solder to solidify before complete wetting
- Incompatible solder alloy or surface finish materials
Prevention and Mitigation Strategies
- Ensure proper cleaning and preparation of the pad and ball surfaces
- Select appropriate flux chemistry and activity level for the application
- Optimize the reflow profile to ensure adequate preheat and peak temperatures
- Implement a controlled cooling rate to allow sufficient time for wetting
- Verify compatibility between solder alloy, surface finish, and substrate materials
4. Head-in-Pillow (HiP)
Head-in-Pillow (HiP) is a defect that occurs when the solder ball on the component and the solder paste on the PCB pad fail to coalesce during the reflow process, resulting in a partial or incomplete connection.
Causes of Head-in-Pillow
- Oxidation of the solder ball or pad surfaces
- Insufficient flux activity or incorrect flux chemistry
- Inadequate preheat or peak temperature during reflow
- Rapid cooling rates that cause premature solidification of the solder
- Misalignment or poor contact between the ball and paste during placement
Prevention and Mitigation Strategies
- Ensure proper storage and handling of components to minimize oxidation
- Select appropriate flux chemistry and activity level for the application
- Optimize the reflow profile to ensure adequate preheat and peak temperatures
- Implement a controlled cooling rate to allow sufficient time for coalescence
- Utilize automated component placement with vision systems for accurate alignment
5. Solder Beading
Solder beading is an issue where small, discrete balls of solder form on the surface of the solder joint or adjacent areas of the PCB. These beads can cause short circuits or interfere with the function of nearby components.
Causes of Solder Beading
- Excessive solder paste volume or improper paste formulation
- Incorrect solder paste stencil design or thickness
- Inadequate solder mask clearance or coverage
- Improper reflow profile (e.g., insufficient peak temperature or time above liquidus)
- Contamination or oxidation of the solder paste or pad surfaces
Prevention and Mitigation Strategies
- Optimize solder paste stencil design and thickness
- Ensure proper solder paste application and volume
- Maintain adequate solder mask clearance and coverage
- Implement a well-controlled reflow profile
- Ensure proper storage and handling of solder paste to prevent contamination or degradation
Inspection and Quality Control Methods
Visual Inspection
Visual inspection is the most basic method for detecting BGA soldering errors. Trained operators use magnification tools, such as microscopes or digital cameras, to examine the solder joints for visible defects like bridging, beading, or incomplete wetting.
Advantages
- Quick and cost-effective
- Suitable for detecting gross defects
- Can be performed at various stages of the assembly process
Limitations
- Subjective and dependent on operator skill and experience
- Limited ability to detect internal or hidden defects (e.g., voids or HiP)
- Time-consuming for high-volume production
X-Ray Inspection
X-ray inspection is a non-destructive testing method that uses X-rays to create images of the internal structure of the solder joints. This technique is particularly useful for detecting defects that are not visible from the surface, such as voids, HiP, or missing balls.
Advantages
- Non-destructive and suitable for production use
- Provides detailed images of internal joint structure
- Automated systems can quickly scan and analyze multiple joints
Limitations
- Higher equipment costs compared to visual inspection
- Requires skilled operators to interpret X-ray images
- Limited ability to detect some surface defects (e.g., non-wetting or de-wetting)
Automated Optical Inspection (AOI)
Automated Optical Inspection (AOI) systems use high-resolution cameras and advanced image processing algorithms to automatically detect and classify soldering errors. AOI systems can be programmed to identify a wide range of defects based on pre-defined criteria.
Advantages
- Fast and consistent inspection for high-volume production
- Objective and repeatable results
- Can detect a wide range of surface defects
- Automated defect classification and reporting
Limitations
- Higher equipment costs compared to manual visual inspection
- Limited ability to detect internal or hidden defects (e.g., voids or HiP)
- May require periodic programming updates to accommodate new components or defect types
Electrical Testing
Electrical testing involves verifying the electrical continuity and resistance of the solder joints using techniques such as flying probe testing or boundary scan testing. These methods can help identify defects that may not be visually apparent but can still impact the electrical performance of the device.
Advantages
- Directly assesses the electrical functionality of the solder joints
- Can detect defects that may be missed by visual or X-ray inspection
- Suitable for both production and troubleshooting applications
Limitations
- Requires specialized equipment and fixturing
- May be time-consuming for high-volume production
- Limited ability to provide detailed information about the physical characteristics of the defects
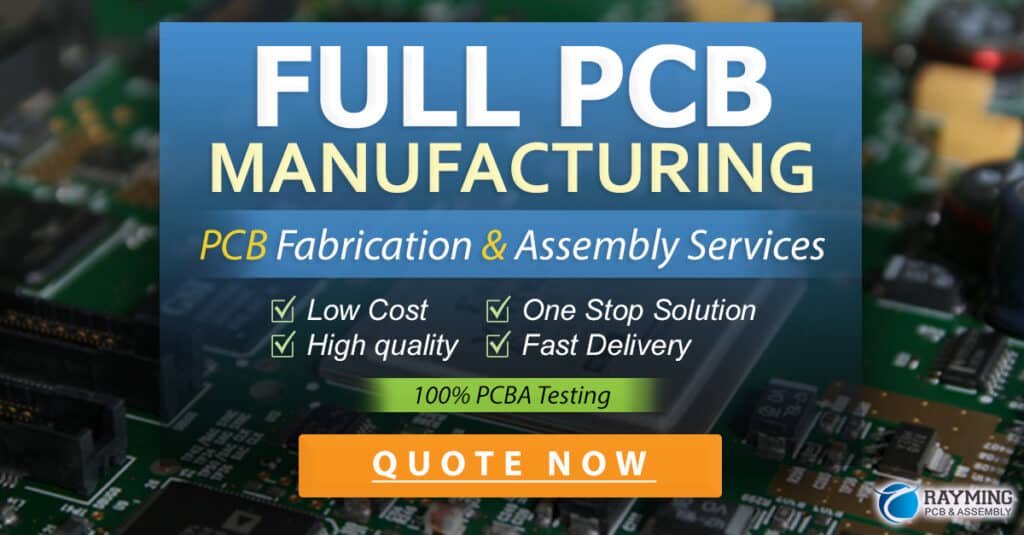
Rework and Repair Techniques
When BGA soldering errors are detected, rework or repair may be necessary to salvage the affected components or PCBs. The choice of rework technique depends on factors such as the type and severity of the defect, the component and PCB materials, and the available equipment and expertise.
Localized Heating
Localized heating involves applying focused heat to the specific area of the solder joint that requires rework. This can be accomplished using tools such as hot air pencils, soldering irons, or laser soldering systems.
Advantages
- Minimizes thermal stress on adjacent components and PCB areas
- Suitable for minor defects or single joint repairs
- Relatively low equipment costs
Limitations
- Requires skilled operators to avoid damaging the component or PCB
- Limited ability to control the heating process or temperature uniformity
- May not be suitable for larger components or multiple joint repairs
Global Heating
Global heating involves applying heat to the entire BGA component and surrounding PCB area using techniques such as hot air reflow or infrared reflow. This method is often used for more extensive repairs or for replacing entire BGA components.
Advantages
- Provides uniform heating across the component and PCB
- Suitable for larger components or multiple joint repairs
- Can be automated for consistent results
Limitations
- Higher equipment costs compared to localized heating methods
- Requires careful control of the heating profile to avoid thermal damage
- May necessitate the removal and replacement of adjacent components
Solder Paste Dispensing
Solder paste dispensing is a technique used to add or replace solder material on the PCB pads prior to rework. This can be done using manual or automated dispensing systems, depending on the application and volume.
Advantages
- Allows precise control over the amount and placement of solder paste
- Suitable for repairing defects related to insufficient solder volume
- Can be used in conjunction with other rework methods
Limitations
- Requires specialized dispensing equipment and consumables
- May require additional cleaning steps to remove flux residue
- Limited ability to address defects not related to solder volume
Best Practices for BGA Soldering
To minimize the occurrence of BGA soldering errors and improve the overall quality of the soldering process, consider implementing the following best practices:
- Design for Manufacturability (DFM)
- Optimize PCB and stencil designs for proper solder paste deposition and flow
- Ensure adequate pad size, shape, and spacing for the selected BGA components
-
Incorporate appropriate solder mask clearances and venting features
-
Process Control
- Establish and maintain a robust quality management system
- Regularly calibrate and maintain soldering equipment and tools
- Monitor and control critical process parameters (e.g., reflow temperatures, conveyor speeds)
-
Implement statistical process control (SPC) methods to track and analyze process performance
-
Material Selection and Handling
- Choose solder paste and flux formulations that are compatible with the components and PCB materials
- Ensure proper storage and handling of solder paste to maintain quality and consistency
-
Follow manufacturer recommendations for solder paste printing and reflow profile settings
-
Training and Education
- Provide comprehensive training to operators and technicians on BGA soldering techniques and defect identification
- Encourage continuous learning and skill development through ongoing education and certification programs
-
Foster a culture of quality and continuous improvement within the organization
-
Collaboration and Communication
- Promote open communication and collaboration between design, manufacturing, and quality teams
- Regularly review and discuss soldering process performance and improvement opportunities
- Engage with suppliers and industry partners to stay informed about new technologies and best practices
By adopting these best practices and continuously monitoring and improving the BGA soldering process, manufacturers can significantly reduce the occurrence of soldering errors and enhance the reliability and performance of their products.
Frequently Asked Questions (FAQ)
- What is the most common BGA soldering error?
-
Bridging is one of the most common BGA soldering errors, occurring when excess solder creates an unintended connection between two or more solder balls or pads.
-
How can voids in BGA solder joints be minimized?
-
To minimize voids, select solder paste with low voiding characteristics, optimize the reflow profile to reduce outgassing, implement nitrogen reflow, and consider using vacuum soldering or vapor phase soldering techniques.
-
What causes head-in-pillow (HiP) defects in BGA soldering?
-
HiP defects can be caused by oxidation of the solder ball or pad surfaces, insufficient flux activity, inadequate reflow temperatures, rapid cooling rates, or misalignment between the ball and paste during placement.
-
What inspection methods are used to detect BGA soldering errors?
-
Common inspection methods include visual inspection, X-ray inspection, automated optical inspection (AOI), and electrical testing. Each method has its advantages and limitations in detecting different types of defects.
-
How can BGA soldering errors be reworked or repaired?
- BGA soldering errors can be reworked using techniques such as localized heating, global heating, or solder paste dispensing. The choice of rework method depends on factors such as the type and severity of the defect, component and PCB materials, and available equipment and expertise.
Conclusion
BGA soldering is a complex process that requires careful control and attention to detail to ensure reliable and high-quality solder joints. Understanding the common error categories, their causes, and prevention strategies is crucial for manufacturers aiming to improve their soldering process and minimize defects.
By implementing a combination of robust process controls, appropriate inspection methods, and effective rework techniques, manufacturers can significantly reduce the occurrence of BGA soldering errors and enhance the overall quality and reliability of their products. Adopting best practices, such as design for manufacturability, material selection and handling, and continuous training and education, further contributes to the success of the BGA soldering process.
As technology advances and new challenges arise, it is essential for manufacturers to stay informed about the latest developments in BGA soldering and to collaborate with industry partners to share knowledge and best practices. By continuously monitoring, analyzing, and improving their soldering processes, manufacturers can position themselves to meet the ever-increasing demands for high-quality and reliable electronic products in today’s competitive market.
No responses yet