Air Core Inductors
Air core inductors are the simplest type, consisting of a coil of wire with no core material. The coil itself is the inductor, with air in between the turns. Advantages of air core inductors include:
- No core losses
- Handles high peak currents
- High Q factor
- Stable with temperature changes
- Low cost
However, air core inductors also have some drawbacks:
- Require more turns for a given inductance
- Larger size compared to inductors with cores
- Susceptible to electromagnetic interference (EMI)
- Lower maximum inductance than types with cores
Typical applications for air core inductors include high frequency circuits above 30 MHz, such as RF transmitters, receivers and oscillators. They are also used for energy storage in pulsed power applications.
Ferrite Core Inductors
Ferrite core inductors have a ceramic core made of ferrite magnetic material, with the coil wound around or inside the core. Advantages of ferrite cores include:
- High inductance with fewer coil turns
- Smaller size than air core
- High Q factor
- Low core losses at high frequencies
- Good temperature stability
- Contain EMI
Disadvantages of ferrite core inductors include:
- Lower saturation current than air core
- Core losses increase with flux density
- More expensive than air core
Ferrite core inductors are very popular and have a wide range of applications, including:
- EMI suppression
- Power convertors and voltage regulators
- Filters for switching power supplies
- Tuned circuits and transformers
- RFID antennas
Ferrite cores come in various materials optimized for different frequency ranges and applications. Some common ferrite materials include:
Material | Permeability | Frequency Range | Applications |
---|---|---|---|
MnZn | High | < 5 MHz | Power convertors, EMI filters |
NiZn | Medium | 1 – 500 MHz | Wideband transformers, antennas |
Iron powder | Low | 1 – 100 MHz | High Q tuned circuits, filters |
Iron Core Inductors
Iron core inductors have a core made of laminated iron or powdered iron materials. Advantages include:
- Very high inductance
- Handles high currents
- Low cost
- Tunes out EMI
Disadvantages of iron cores include:
- High core losses and low Q at high frequencies
- Large size and weight
- Susceptible to saturation
Iron core inductors are used mainly at low frequencies (< 100 kHz) and high current applications such as:
- Switching power supplies
- Power factor correction
- DC/DC convertors
- EMI filters
- Chokes and transformers
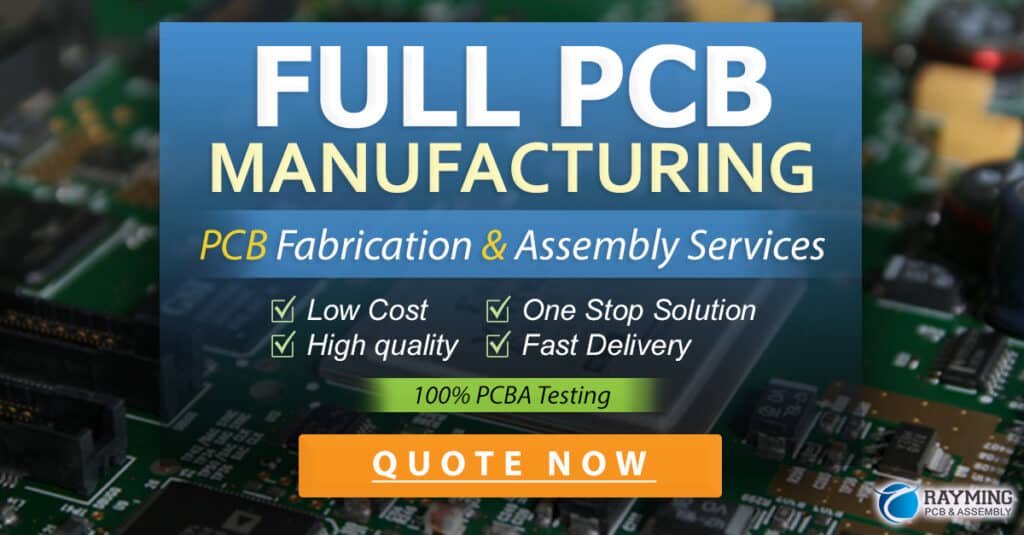
Toroidal Core Inductors
Toroidal inductors are wound around a donut-shaped core, usually ferrite or powdered iron. This closed-loop core shape has several advantages:
- High inductance with compact size
- Very low EMI radiation
- High Q factor
- Low sensitivity to external fields
- High efficiency and minimal losses
However, toroidal inductors also have some drawbacks:
- More complex to wind the coil
- Higher cost than other core shapes
- Difficult to adjust or tune inductance
Applications for toroidal core inductors include:
- High-efficiency power supplies
- Precision filters and oscillators
- EMI suppressors
- Isolation transformers
- Current sensors
Surface Mount (SMD) Inductors
Surface mount inductors are miniature inductors without leads designed to be soldered directly onto a printed circuit board (PCB). They come in various standard sizes and packaging. Advantages of SMD inductors include:
- Very small footprint on the PCB
- Minimal radiation of EMI
- High Q factor
- Suitable for automated assembly
- Lower cost in high volumes
Disadvantages include:
- Fixed inductance values
- Limited heat dissipation
- Peak current and power handling constrained by size
SMD inductors are widely used in high-density applications such as:
- Mobile devices
- Wearables
- Internet of Things (IoT) devices
- Automotive electronics
- LED drivers
Common SMD inductor packages and their sizes include:
Package | Length (mm) | Width (mm) | Height (mm) |
---|---|---|---|
0201 | 0.6 | 0.3 | 0.3 |
0402 | 1.0 | 0.5 | 0.5 |
0603 | 1.6 | 0.8 | 0.8 |
0805 | 2.0 | 1.2 | 0.5-1.0 |
1206 | 3.2 | 1.6 | 0.5-1.0 |
Variable Inductors
Variable inductors allow the inductance to be adjusted, usually by moving the core or changing the effective permeability. They are used in circuits that require tuning or variable filtering. The two main types are:
-
Slug-tuned inductors – A threaded slug made of ferrite or brass screws in and out of the coil, changing the permeability and inductance. Advantages include simple tuning and high Q. Disadvantages are a narrow tuning range and the slug can vibrate loose.
-
Permeability-tuned inductors – The core permeability is varied by an external magnetic field from a control current. This allows electronic tuning. Advantages are a wider tuning range and being more rugged than slug-tuned. Disadvantages include greater complexity and lower Q than slug-tuned.
Variable inductors are essential in applications such as:
- Antenna tuners
- Variable filters
- Resonant circuits
- Impedance matching networks
- Voltage-controlled oscillators (VCOs)
Coupled Inductors
Coupled inductors have two or more windings on the same core that are magnetically coupled. This allows energy to be transferred between the windings. The amount of coupling depends on the turns ratio, distance between windings, and core material.
There are two main types of coupled inductors:
-
Transformers – The windings are strongly coupled for maximum energy transfer. They are used to change voltage and current levels and provide isolation.
-
Inductors with auxiliary winding – A main inductor with a second winding for sensing current or injecting a signal. The auxiliary winding is loosely coupled. Common applications include current sensing and feeding forward the inductor current to improve regulation.
Advantages of coupled inductors include:
- Efficient energy transfer
- Impedance transformation
- Electrical isolation
- Feedback and sensing
Disadvantages include:
- Increased size compared to a single inductor
- Potential for unwanted coupling and noise
Molded Inductors
Molded inductors have the coil encapsulated in plastic or epoxy, with just the leads exposed. Advantages of molded construction include:
- Protection from environment and damage
- Reduced EMI pickup or radiation
- Easier PCB Cleaning
- Marked with value for identification
- Can be color-coded
Disadvantages include:
- Reduced cooling and heat dissipation
- Fixed inductance value
- Outgassing of encapsulant can affect sensitive circuits
Molded inductors are commonly used in through-hole PCB assemblies for applications such as:
- Power supplies
- Automotive electronics
- Telecom infrastructure
- Industrial controls
- LED lighting
FAQ
What is inductance and how is it measured?
Inductance is the ability of an inductor to store energy in a magnetic field. It is measured in units of henries (H). One henry is the inductance that produces a voltage of one volt when the current is changing at one ampere per second. Typical inductance values range from nanohenries (nH) to millihenries (mH).
How do I select the right type of inductor for my application?
To select the best inductor, consider the following factors:
- Inductance value required
- Operating frequency range
- Peak and RMS current
- Size and weight constraints
- Required Q factor
- EMI requirements
- Environmental factors such as temperature, humidity, and vibration
- Cost target
Refer to the inductor type characteristics in this guide to narrow down the suitable options. Consult with inductor suppliers or use online selection tools to find parts that meet your specific requirements.
What is Q factor and why is it important?
Q factor is a dimensionless parameter that indicates how much energy is lost in an inductor relative to the amount of energy stored. It is defined as:
Q = 2π * (Energy Stored / Energy Lost per Cycle)
A higher Q indicates a more ideal, low-loss inductor. High Q is desirable for resonant circuits, filters, and oscillators to enable frequency selectivity and efficiency. However, high Q also means the inductor will saturate at a lower current.
The Q factor depends on the operating frequency, inductor design, and core material. It is typically specified in the inductor datasheet at the test frequency.
Can I use an inductor for EMI suppression?
Yes, inductors are very effective for reducing electromagnetic interference (EMI). They are used in EMI filters to attenuate high frequency noise. The inductance opposes changes in current, smoothing out the signal.
The best EMI suppression is provided by ferrite core, iron powder core, and toroidal inductors. These contain the magnetic field within the core, minimizing radiation. The core material is chosen based on the frequency range of the noise to be filtered.
What happens when an inductor saturates?
Inductor saturation occurs when the magnetic flux density in the core exceeds the maximum level the core material can support. The permeability of the core decreases drastically, reducing the inductance.
When an inductor saturates, the current increases sharply and the inductor begins to look like a short circuit. This can cause overheating and damage to the inductor and associated circuits.
To avoid saturation, select an inductor with a sufficient saturation current rating for your application. Oversizing the inductor and using a core material with a higher saturation flux density can help. Current limiting and soft start circuits can also protect against saturation.
In summary, there is a wide range of Inductor Types available, each with unique advantages and suitability for different applications. Understanding the characteristics of each type is essential for making the optimum selection. Consider factors such as inductance, operating frequency, current ratings, Q factor, EMI, and saturation when choosing inductors. By following this ultimate guide and working with inductor suppliers, you can confidently select the right inductor for your design.
No responses yet