Introduction to PCB+Electrical+Tests”>PCB Electrical Tests
Printed Circuit Boards (PCBs) are the backbone of modern electronic devices. They are used in a wide range of applications, from simple consumer electronics to complex aerospace systems. To ensure that PCBs function as intended and meet the required quality standards, they must undergo various electrical tests. These tests are crucial for detecting defects, ensuring proper functionality, and guaranteeing the reliability of the final product.
In this article, we will explore the different types of electrical tests performed on PCBs, their importance, and the techniques used to conduct these tests.
The Importance of PCB Electrical Tests
PCB electrical tests are essential for several reasons:
-
Quality Assurance: Electrical tests help identify manufacturing defects, such as short circuits, open circuits, and incorrect component placement. By detecting these issues early in the production process, manufacturers can ensure that only high-quality PCBs are delivered to customers.
-
Functionality Verification: Electrical tests confirm that the PCB functions as designed. These tests verify that the board meets the specified electrical characteristics, such as voltage levels, current ratings, and Signal Integrity.
-
Reliability: Thorough electrical testing helps identify potential reliability issues that may arise during the PCB’s lifecycle. By subjecting the board to various stress tests, manufacturers can predict its performance under different environmental conditions and make necessary improvements.
-
Cost Savings: Detecting and fixing issues early in the production process can significantly reduce costs associated with rework, repairs, and product recalls.
Types of PCB Electrical Tests
There are several types of electrical tests performed on PCBs, each designed to assess specific aspects of the board’s functionality and reliability. Some of the most common tests include:
1. Continuity Test
Continuity testing is a basic electrical test that verifies the connectivity between two points on a PCB. It ensures that there are no open circuits or broken connections that could prevent the board from functioning correctly. Continuity tests are typically performed using a multimeter or a dedicated Continuity Tester.
Continuity Test Techniques
Technique | Description |
---|---|
Manual Testing | An operator manually probes the test points using a multimeter or continuity tester. |
Flying Probe Testing | Automated test equipment with movable probes checks the continuity between test points. |
Bed of Nails Testing | A custom-designed fixture with spring-loaded pins contacts the test points simultaneously. |
2. Short Circuit Test
Short circuit testing is performed to identify unintended connections between two or more points on a PCB. Short circuits can cause damage to components, lead to excessive current draw, and potentially result in device failure. Short circuit tests are often conducted in conjunction with continuity tests.
Short Circuit Test Methods
Method | Description |
---|---|
Resistance Measurement | Measuring the resistance between test points to detect low-resistance shorts. |
Current Limit Testing | Applying a limited current and monitoring the voltage drop to identify shorts. |
Thermal Imaging | Using infrared cameras to detect hot spots caused by short circuits. |
3. Insulation Resistance Test
Insulation resistance (IR) testing measures the resistance between two isolated conductors on a PCB. It verifies that the insulation between these conductors is sufficient to prevent leakage currents and ensure proper board functionality. IR tests are typically performed using a high-voltage insulation resistance tester.
Insulation Resistance Test Factors
Factor | Description |
---|---|
Test Voltage | The voltage applied during the test, typically ranging from 100V to 1000V. |
Minimum Resistance | The minimum acceptable resistance value, usually in the range of megaohms or gigaohms. |
Test Duration | The time for which the test voltage is applied, typically 1-5 minutes. |
4. Dielectric Withstand Test
Dielectric withstand testing, also known as high potential (HiPot) testing, is used to verify the insulation integrity of a PCB. It involves applying a high voltage between the conductors and the ground plane to ensure that the insulation can withstand the specified voltage without breakdown. HiPot tests are performed using a dielectric withstand tester.
Dielectric Withstand Test Parameters
Parameter | Description |
---|---|
Test Voltage | The high voltage applied during the test, typically 1.5-2 times the working voltage. |
Leakage Current Limit | The maximum allowable leakage current, usually in the range of microamps. |
Ramp Time | The time taken to gradually increase the voltage to the test level. |
Dwell Time | The duration for which the test voltage is maintained. |
5. In-Circuit Test
In-circuit testing (ICT) is a comprehensive test method that verifies the functionality of individual components on a PCB. It involves using a bed of nails fixture to access the component leads and perform various tests, such as resistance, capacitance, and semiconductor tests. ICT helps identify faulty components, incorrect component values, and assembly defects.
In-Circuit Test Advantages
- Comprehensive testing of individual components
- High fault coverage
- Automated testing process
- Early detection of component-level faults
6. Functional Test
Functional testing is performed to verify that the PCB functions as intended in its final application. It involves applying input signals to the board and measuring the output response to ensure that it meets the design specifications. Functional tests are typically conducted using specialized test equipment or custom-designed test jigs.
Functional Test Types
Type | Description |
---|---|
Boundary Scan Test | Utilizes built-in test circuitry (JTAG) to test the interconnections and functionality of digital components. |
Flying Probe Test | Employs movable probes to access test points and perform functional tests. |
Automated Optical Inspection (AOI) | Uses computer vision to inspect the PCB for correct component placement and soldering quality. |
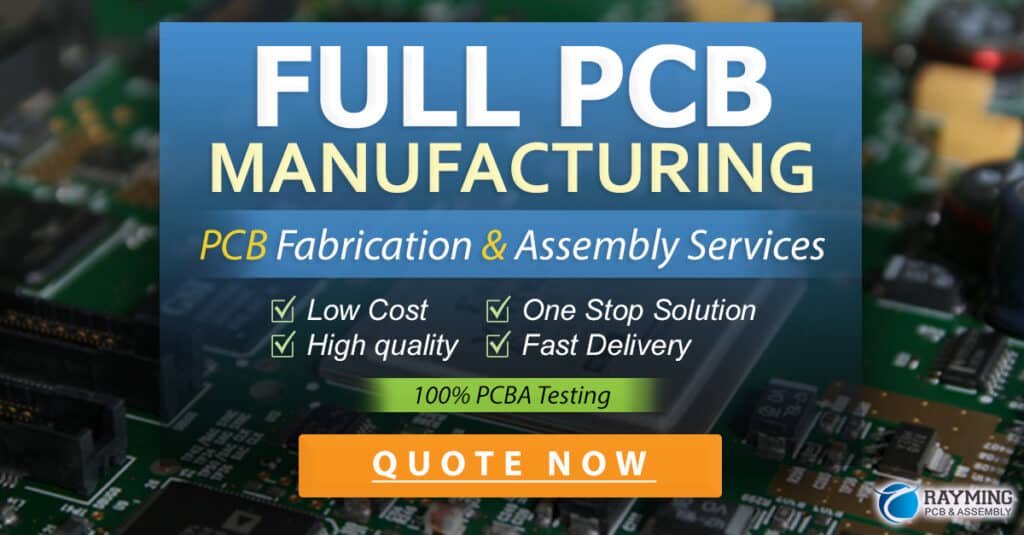
Best Practices for PCB Electrical Testing
To ensure the effectiveness and reliability of PCB electrical tests, consider the following best practices:
-
Develop a Comprehensive Test Plan: Create a detailed test plan that covers all the necessary electrical tests based on the PCB’s design, application, and quality requirements.
-
Use Appropriate Test Equipment: Select test equipment that is suitable for the specific type of test being performed. Ensure that the equipment is calibrated and maintained regularly.
-
Establish Test Criteria: Define clear pass/fail criteria for each electrical test based on industry standards, customer requirements, and design specifications.
-
Implement Statistical Process Control: Monitor test results using statistical process control techniques to identify trends, detect anomalies, and continuously improve the testing process.
-
Document Test Results: Maintain detailed records of test results, including test parameters, pass/fail status, and any observed issues. This documentation is essential for traceability and quality control purposes.
FAQ
-
What is the purpose of continuity testing on a PCB?
Continuity testing verifies that there are no open circuits or broken connections between two points on a PCB. It ensures that the electrical pathways are intact and the board can function as intended. -
How does short circuit testing differ from continuity testing?
While continuity testing checks for open circuits, short circuit testing identifies unintended connections between two or more points on a PCB. Short circuits can cause damage to components and lead to device failure. -
What is the significance of insulation resistance testing?
Insulation resistance testing measures the resistance between two isolated conductors on a PCB. It verifies that the insulation between these conductors is sufficient to prevent leakage currents and ensure proper board functionality. -
Why is dielectric withstand testing important for PCBs?
Dielectric withstand testing, also known as HiPot testing, is used to verify the insulation integrity of a PCB. It ensures that the insulation can withstand the specified high voltage without breakdown, preventing potential safety hazards and device failures. -
What are the advantages of in-circuit testing (ICT) for PCBs?
In-circuit testing provides comprehensive testing of individual components on a PCB. It offers high fault coverage, automated testing processes, and early detection of component-level faults, ensuring the overall quality and functionality of the PCB.
Conclusion
Electrical testing is a critical aspect of PCB manufacturing and quality assurance. By performing various tests, such as continuity, short circuit, insulation resistance, dielectric withstand, in-circuit, and functional tests, manufacturers can identify defects, verify functionality, and ensure the reliability of PCBs.
Implementing best practices, such as developing a comprehensive test plan, using appropriate test equipment, establishing clear test criteria, implementing statistical process control, and documenting test results, can further enhance the effectiveness of PCB electrical testing.
By investing in thorough electrical testing, manufacturers can deliver high-quality PCBs that meet customer requirements and perform reliably in their intended applications.
No responses yet