Introduction to Transparent PCBs
Transparent PCBs, also known as see-through circuit boards, are a revolutionary development in the world of electronic manufacturing. These innovative circuit boards offer a unique combination of electrical functionality and optical transparency, opening up a wide range of possibilities for various applications. With their high optical transmissivity, transparent PCBs allow light to pass through the board, enabling the creation of visually stunning and functionally advanced electronic devices.
What are Transparent PCBs?
Transparent PCBs are printed circuit boards that are fabricated using transparent materials, such as glass or clear polymers, instead of the traditional opaque substrates like FR-4. These transparent substrates allow light to pass through the board, while still maintaining the necessary electrical properties required for circuit functionality. The conductive traces on transparent PCBs are typically made using transparent conductive materials, such as indium tin oxide (ITO) or silver nanowires, which ensure electrical conductivity without compromising optical clarity.
Advantages of Transparent PCBs
Transparent PCBs offer several advantages over traditional opaque circuit boards:
-
Optical Transparency: The high optical transmissivity of transparent PCBs allows light to pass through the board, enabling the creation of visually appealing and interactive electronic devices. This transparency opens up new possibilities for applications such as displays, lighting, and optical sensors.
-
Design Flexibility: With transparent PCBs, designers have greater freedom to create innovative and aesthetically pleasing electronic products. The transparency of the board allows for the integration of visual elements, such as graphics or logos, directly onto the PCB, enhancing the overall appearance of the device.
-
Improved Functionality: Transparent PCBs enable the integration of optical components, such as LEDs or photodiodes, directly onto the board. This integration allows for more compact and efficient device designs, reducing the need for additional wiring and connectors.
-
Enhanced Durability: Transparent substrates, such as glass, offer excellent mechanical strength and thermal stability compared to traditional PCB materials. This durability makes transparent PCBs suitable for applications that require high reliability and resistance to environmental factors.
Manufacturing Process of Transparent PCBs
The manufacturing process of transparent PCBs differs from that of traditional opaque boards due to the unique materials and techniques involved.
Substrate Selection
The first step in manufacturing transparent PCBs is selecting the appropriate transparent substrate. Common substrate materials include:
-
Glass: Glass substrates offer excellent optical clarity, mechanical strength, and thermal stability. They are suitable for applications that require high transparency and durability.
-
Clear Polymers: Clear polymers, such as polyethylene terephthalate (PET) or polycarbonate (PC), provide good optical transparency and flexibility. They are often used in flexible transparent PCBs for wearable electronics and displays.
Conductive Trace Deposition
Once the transparent substrate is selected, the next step is depositing the conductive traces onto the board. Several methods can be used for this purpose:
-
Indium Tin Oxide (ITO) Sputtering: ITO is a transparent conductive material widely used in transparent electronics. It is deposited onto the substrate using a sputtering process, creating a thin, transparent, and conductive layer.
-
Silver Nanowire Coating: Silver nanowires are another transparent conductive material that can be used for creating traces on transparent PCBs. They are typically applied using a coating process, such as spin coating or spray coating.
-
Inkjet Printing: Conductive inks containing transparent conductive materials can be printed directly onto the transparent substrate using inkjet printing technology. This method allows for precise patterning of the conductive traces.
Patterning and Etching
After depositing the conductive traces, the desired circuit pattern is created through a patterning and etching process. Photolithography is commonly used for this purpose, involving the following steps:
- A photoresist layer is applied onto the conductive layer.
- The photoresist is exposed to UV light through a photomask containing the circuit pattern.
- The exposed photoresist is developed, leaving the desired pattern on the conductive layer.
- The uncovered conductive material is etched away using chemical or physical etching methods.
- The remaining photoresist is removed, revealing the final circuit pattern.
Component Assembly
Once the transparent PCB is patterned and etched, electronic components are assembled onto the board. Special consideration is given to the selection of components to ensure compatibility with the transparent substrate and maintain the overall optical clarity of the device. Surface mount technology (SMT) is commonly used for component assembly on transparent PCBs, as it allows for precise placement and minimizes the obstruction of light.
Applications of Transparent PCBs
Transparent PCBs find applications in various fields where optical transparency and electronic functionality are required. Some notable applications include:
Displays and Touch Screens
Transparent PCBs are widely used in the manufacturing of displays and touch screens. The transparency of the board allows for the integration of Touch Sensors, such as capacitive or resistive sensors, directly onto the display panel. This integration enables the creation of seamless and responsive touch interfaces for devices like smartphones, tablets, and interactive kiosks.
Lighting and Illumination
Transparent PCBs are ideal for lighting applications, particularly in the field of LED lighting. The transparency of the board allows for the direct mounting of LEDs onto the PCB, creating thin and uniform illumination panels. Transparent PCBs are used in applications such as backlighting for displays, decorative lighting, and automotive lighting.
Wearable Electronics
The flexibility and transparency of transparent PCBs make them suitable for wearable electronic devices. They can be used to create transparent and lightweight circuit boards for applications such as smartwatches, fitness trackers, and head-mounted displays. The transparency of the board enhances the aesthetic appeal of the device while providing the necessary electronic functionality.
Solar Cells and Photovoltaics
Transparent PCBs are finding applications in the field of solar energy harvesting. The transparency of the board allows for the integration of transparent solar cells, enabling the creation of energy-generating devices that can be seamlessly integrated into windows, building facades, or consumer electronics. Transparent PCBs provide the necessary electrical interconnections while maximizing the exposure of the solar cells to sunlight.
Medical Devices and Biosensors
Transparent PCBs are being explored for use in medical devices and biosensors. The transparency of the board allows for the integration of optical sensors, such as photodiodes or spectrometers, directly onto the PCB. This integration enables the development of compact and efficient diagnostic devices for applications like blood analysis, drug testing, and environmental monitoring.
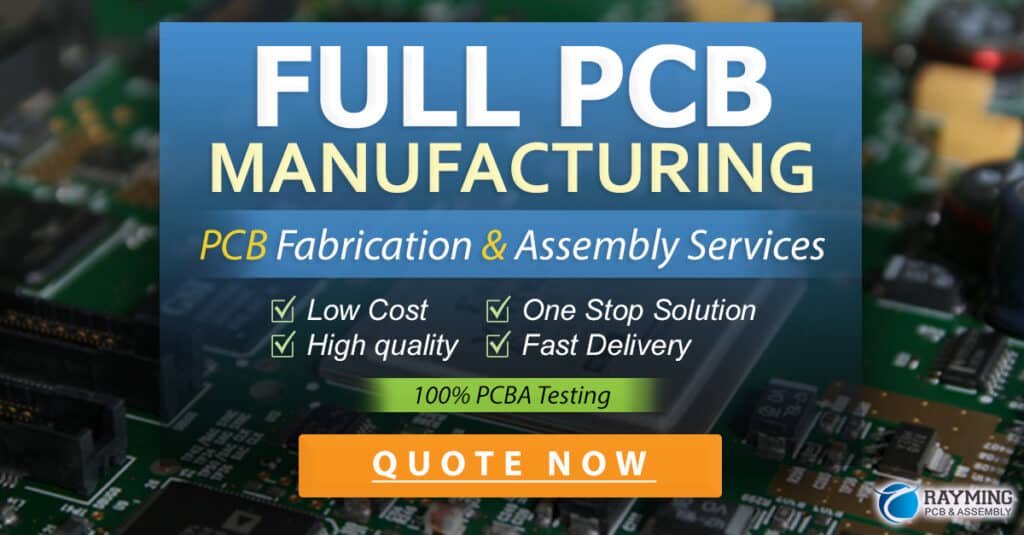
Challenges and Future Developments
While transparent PCBs offer numerous advantages and possibilities, there are still challenges to be addressed for their widespread adoption:
Material Optimization
One of the main challenges in transparent PCB manufacturing is the optimization of transparent conductive materials. Current materials, such as ITO and silver nanowires, have limitations in terms of conductivity, flexibility, and cost. Research is ongoing to develop new transparent conductive materials with improved properties and cost-effectiveness.
Process Standardization
The manufacturing process for transparent PCBs is still evolving, and there is a need for standardization to ensure consistent quality and reliability. Efforts are being made to establish guidelines and best practices for transparent PCB fabrication, including substrate selection, conductive trace deposition, and component assembly.
Integration with Conventional Electronics
Integrating transparent PCBs with conventional electronic components and systems can be challenging due to differences in materials and manufacturing processes. Efforts are being made to develop compatible interconnection technologies and assembly methods to facilitate seamless integration between transparent and conventional electronics.
Cost Reduction
Currently, the cost of manufacturing transparent PCBs is higher compared to traditional opaque boards due to the specialized materials and processes involved. As the technology matures and production volumes increase, it is expected that the cost of transparent PCBs will decrease, making them more accessible for a wider range of applications.
Frequently Asked Questions (FAQ)
-
What is the typical optical transmissivity of transparent PCBs?
The optical transmissivity of transparent PCBs depends on the substrate material and the thickness of the conductive traces. Glass-based transparent PCBs can achieve optical transmissivity of up to 90%, while polymer-based boards typically have transmissivity in the range of 80-85%. -
Can transparent PCBs be used for high-frequency applications?
Yes, transparent PCBs can be designed for high-frequency applications. However, the conductive materials used in transparent PCBs, such as ITO or silver nanowires, have higher resistivity compared to copper, which is commonly used in traditional PCBs. This higher resistivity can limit the high-frequency performance of transparent PCBs. Careful design considerations and material selection are necessary to optimize the performance of transparent PCBs for high-frequency applications. -
Are transparent PCBs suitable for flexible electronics?
Yes, transparent PCBs can be fabricated on flexible substrates, such as clear polymers, making them suitable for flexible electronics applications. Flexible transparent PCBs offer the advantages of transparency, lightweight, and conformability, which are desirable for wearable devices, flexible displays, and sensors. -
How do the manufacturing costs of transparent PCBs compare to traditional PCBs?
Currently, the manufacturing costs of transparent PCBs are higher compared to traditional opaque PCBs. This cost difference is primarily due to the specialized materials and processes involved in transparent PCB fabrication. However, as the technology advances and production volumes increase, it is expected that the cost gap between transparent and traditional PCBs will narrow. -
What are the environmental considerations for transparent PCB manufacturing?
Transparent PCB manufacturing involves the use of chemicals and materials that can have environmental impacts. Proper handling, disposal, and recycling of these materials are important to minimize environmental risks. Additionally, the development of eco-friendly and biodegradable transparent substrates and conductive materials is an active area of research to improve the environmental sustainability of transparent PCBs.
Conclusion
Transparent PCBs represent a significant advancement in the field of electronic manufacturing, offering a unique combination of optical transparency and electronic functionality. With their high optical transmissivity, design flexibility, and enhanced durability, transparent PCBs are opening up new possibilities for a wide range of applications, including displays, lighting, wearable electronics, solar cells, and medical devices.
As the technology continues to evolve, efforts are being made to optimize transparent conductive materials, standardize manufacturing processes, and reduce costs. The integration of transparent PCBs with conventional electronics is also a key focus area for future developments.
Despite the challenges, the potential benefits of transparent PCBs are immense. They offer designers and engineers a new toolset to create innovative, visually appealing, and functionally advanced electronic devices. As research progresses and the technology matures, transparent PCBs are poised to revolutionize the electronics industry and enable the development of next-generation transparent electronic devices.
Substrate Material | Typical Optical Transmissivity | Key Characteristics |
---|---|---|
Glass | Up to 90% | High transparency, excellent mechanical strength and thermal stability |
Clear Polymers (PET, PC) | 80-85% | Good transparency, flexibility, suitable for wearable electronics |
Conductive Material | Deposition Method | Key Characteristics |
---|---|---|
Indium Tin Oxide (ITO) | Sputtering | Widely used, transparent, conductive |
Silver Nanowires | Coating | Transparent, conductive, flexible |
Conductive Inks | Inkjet Printing | Allows precise patterning, transparent |
No responses yet