1. Inadequate Power and Ground Plane Design
One of the most common PCB design mistakes is inadequate power and ground plane design. Power and ground planes are essential for providing a low-impedance path for current flow and minimizing noise in the circuit. When designed improperly, power and ground planes can lead to signal integrity issues, electromagnetic interference (EMI), and even component failure.
Common Power and Ground Plane Design Mistakes
Mistake | Consequence |
---|---|
Insufficient power and ground plane area | Increased impedance, voltage drop, and noise |
Improper placement of power and ground vias | Increased inductance and current density |
Lack of proper decoupling capacitors | Increased power supply noise and signal integrity issues |
Incorrect power plane split | Noise coupling between different voltage domains |
How to Fix Power and Ground Plane Design Mistakes
- Ensure adequate power and ground plane area by following the 20H rule: the power and ground plane area should be at least 20 times the total area of the traces on the signal layers.
- Place power and ground vias close to the components they serve to minimize inductance and current density.
- Use appropriate decoupling capacitors near power pins of ICs to reduce power supply noise and maintain signal integrity.
- If using split power planes, ensure proper isolation between voltage domains to prevent noise coupling.
2. Incorrect Trace Routing
Incorrect trace routing is another common PCB design mistake that can lead to signal integrity issues, crosstalk, and EMI. Trace routing involves the placement and routing of conductive traces on the PCB to connect components and carry signals between them.
Common Trace Routing Mistakes
Mistake | Consequence |
---|---|
Traces too close together | Crosstalk and signal integrity issues |
Traces routed at 90-degree angles | Increased inductance and EMI |
Traces not matched in length | Signal timing issues and reflections |
Traces not properly terminated | Signal reflections and ringing |
How to Fix Trace Routing Mistakes
- Follow proper trace spacing guidelines based on the signal type and speed. High-speed signals require greater spacing to minimize crosstalk.
- Route traces at 45-degree angles instead of 90-degree angles to reduce inductance and EMI.
- Match trace lengths for critical signals, such as clock and data lines, to ensure proper signal timing and minimize reflections.
- Use appropriate termination techniques, such as series termination and parallel termination, to reduce signal reflections and ringing.
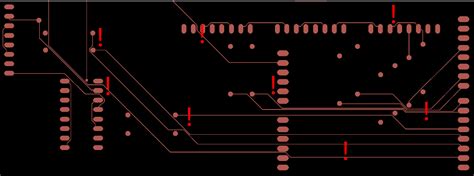
3. Insufficient Thermal Management
Insufficient thermal management is a PCB design mistake that can lead to component overheating, reduced reliability, and even failure. Thermal management involves the design of the PCB to dissipate heat generated by components and maintain safe operating temperatures.
Common Thermal Management Mistakes
Mistake | Consequence |
---|---|
Insufficient copper pour for heat dissipation | Component overheating and reduced reliability |
Improper placement of heat-generating components | Localized hot spots and thermal stress |
Lack of thermal vias for heat transfer | Reduced heat dissipation efficiency |
Incorrect thermal pad design | Poor thermal contact and increased thermal resistance |
How to Fix Thermal Management Mistakes
- Use sufficient copper pour on power and ground planes to facilitate heat dissipation. The larger the copper area, the better the heat dissipation.
- Place heat-generating components, such as power regulators and high-speed processors, away from thermally sensitive components and provide adequate spacing for airflow.
- Use thermal vias to transfer heat from components to the power and ground planes. Thermal vias should be placed close to the heat-generating components and have sufficient size and quantity.
- Design thermal pads for components with exposed pads or heat slugs to ensure proper thermal contact and minimize thermal resistance.
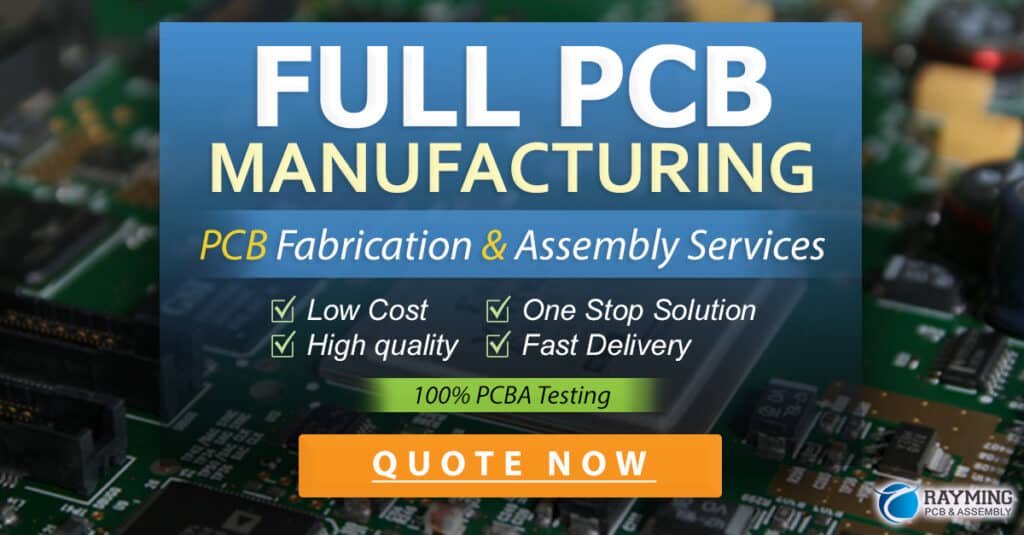
4. Improper Component Placement
Improper component placement is a PCB design mistake that can lead to signal integrity issues, increased noise, and manufacturing difficulties. Component placement involves the physical arrangement of components on the PCB to optimize performance, manufacturability, and reliability.
Common Component Placement Mistakes
Mistake | Consequence |
---|---|
Components placed too close together | Increased crosstalk and noise coupling |
Components not aligned with manufacturing grid | Increased manufacturing costs and reduced yield |
Incorrect orientation of polarized components | Reverse polarity and component damage |
Lack of consideration for mechanical constraints | Interference with enclosure and reduced reliability |
How to Fix Component Placement Mistakes
- Follow proper component spacing guidelines based on the component size, package type, and signal requirements. High-speed components should be placed closer to their associated traces to minimize parasitic effects.
- Align components with the manufacturing grid to ensure proper placement by pick-and-place machines and reduce manufacturing costs.
- Pay attention to the orientation of polarized components, such as electrolytic capacitors and diodes, to prevent reverse polarity and component damage.
- Consider mechanical constraints, such as component height and clearance requirements, to ensure proper fit within the enclosure and avoid interference with other components.
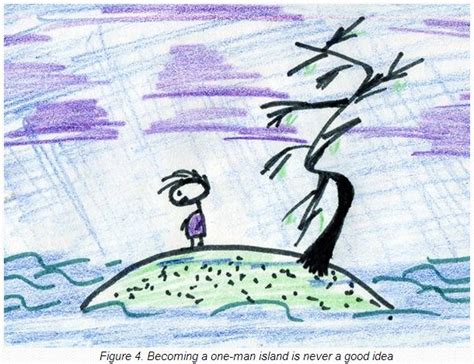
5. Insufficient Documentation and Labeling
Insufficient documentation and labeling is a PCB design mistake that can lead to assembly errors, debugging difficulties, and maintenance challenges. Documentation and labeling involve providing clear and comprehensive information about the PCB design, components, and assembly requirements.
Common Documentation and Labeling Mistakes
Mistake | Consequence |
---|---|
Incomplete or outdated schematics | Assembly errors and debugging difficulties |
Lack of component labeling on the PCB | Increased assembly time and errors |
Incorrect or missing polarity indicators | Reverse polarity and component damage |
Insufficient assembly instructions | Increased manufacturing time and costs |
How to Fix Documentation and Labeling Mistakes
- Maintain accurate and up-to-date schematics that reflect the latest design changes and component selections. Use clear and consistent naming conventions for components and nets.
- Label components on the PCB with their reference designators and values to facilitate assembly and debugging. Use silkscreen or other permanent marking methods.
- Provide clear polarity indicators, such as plus signs or dots, for polarized components to prevent reverse polarity and component damage.
- Create comprehensive assembly instructions that include step-by-step guidance, photos, and diagrams to ensure proper assembly and reduce manufacturing time and costs.
FAQ
1. What is the 20H rule for power and ground plane design?
The 20H rule states that the power and ground plane area should be at least 20 times the total area of the traces on the signal layers. This helps to provide a low-impedance path for current flow and minimize noise in the circuit.
2. Why is it important to route traces at 45-degree angles instead of 90-degree angles?
Routing traces at 45-degree angles instead of 90-degree angles helps to reduce inductance and EMI. Sharp 90-degree angles can create discontinuities in the trace that lead to increased inductance and radiated emissions.
3. What are thermal vias and why are they important for thermal management?
Thermal vias are plated through-holes that are used to transfer heat from components to the power and ground planes. They are important for thermal management because they help to dissipate heat more efficiently and prevent component overheating.
4. How can I ensure proper component placement on the manufacturing grid?
To ensure proper component placement on the manufacturing grid, use a grid size that is compatible with your manufacturing process and align components to the grid during placement. Most PCB design software tools have grid and snap features that can help with this process.
5. What are some best practices for creating assembly instructions?
Some best practices for creating assembly instructions include:
– Use clear and concise language
– Provide step-by-step instructions with photos or diagrams
– Specify the tools and materials required for assembly
– Include information about component orientation and polarity
– Provide troubleshooting tips and common pitfalls to avoid
By following these guidelines and best practices, you can avoid common PCB design mistakes and create more reliable, manufacturable, and cost-effective PCBs.
No responses yet