1. Incorrect tolerances
Tolerances are the acceptable range of variation in a part’s dimensions. Incorrect tolerances can lead to parts that don’t fit together properly or function as intended. This can result in assembly issues, performance problems, and increased scrap rates.
To avoid tolerance issues, designers should:
- Understand the manufacturing processes and their capabilities
- Specify tolerances that are appropriate for the manufacturing process and material
- Use geometric dimensioning and tolerancing (GD&T) to clearly communicate the design intent
- Collaborate with manufacturing engineers to ensure the tolerances are achievable and cost-effective
2. Inadequate draft angles
Draft angles are the tapers added to the sides of a part to allow it to be easily removed from a mold or die. Inadequate draft angles can cause parts to stick in the mold, leading to damage, increased cycle times, and higher manufacturing costs.
To ensure adequate draft angles, designers should:
- Understand the manufacturing process and the minimum draft angles required
- Add draft angles to all vertical surfaces, including ribs, bosses, and holes
- Use a minimum draft angle of 1° for most materials, and increase the angle for softer or stickier materials
- Avoid using zero draft angles unless absolutely necessary
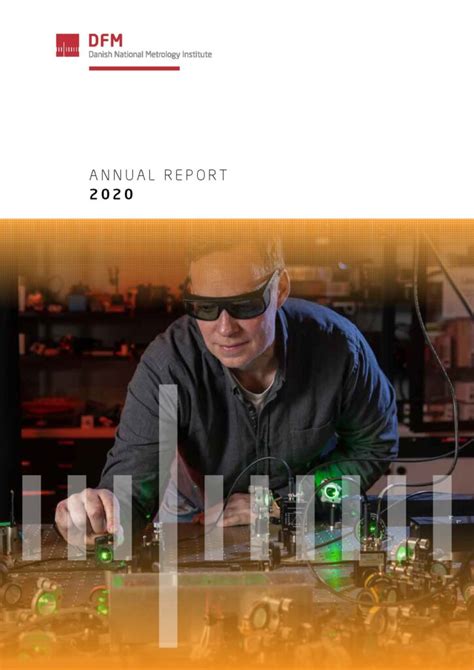
3. Improper wall thickness
Wall thickness refers to the thickness of the walls in a part. Improper wall thickness can lead to a variety of problems, including:
- Sink marks or voids in thick sections
- Warping or distortion in thin sections
- Increased cycle times and material costs
- Difficulty filling the mold cavity
To optimize wall thickness, designers should:
- Use a consistent wall thickness throughout the part
- Avoid thick sections that can cause sink marks or voids
- Use ribs or gussets to reinforce thin sections
- Follow the recommended wall thickness guidelines for the material and manufacturing process
Material | Minimum Wall Thickness |
---|---|
ABS | 1.0 mm |
Polypropylene | 0.75 mm |
Polycarbonate | 1.0 mm |
Nylon | 0.8 mm |
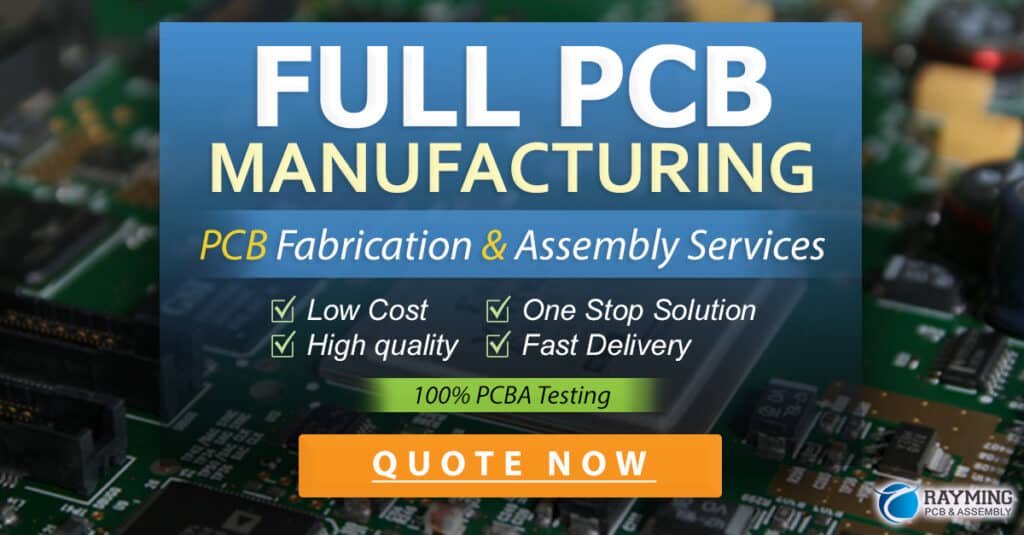
4. Poor gate and ejector pin placement
Gates and ejector pins are used to inject molten plastic into the mold cavity and eject the finished part from the mold. Poor placement of gates and ejector pins can cause a variety of problems, including:
- Visible gate marks or ejector pin marks on the part surface
- Warping or distortion due to uneven cooling
- Difficulty filling the mold cavity
- Increased cycle times and scrap rates
To optimize gate and ejector pin placement, designers should:
- Place gates and ejector pins in non-critical areas of the part
- Use multiple gates for large or complex parts to ensure even filling and cooling
- Avoid placing gates or ejector pins near thin sections or stress concentration areas
- Collaborate with manufacturing engineers to determine the best locations for gates and ejector pins
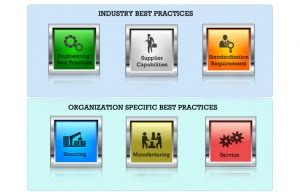
5. Undercuts and snap fits
Undercuts are features that prevent a part from being easily removed from a mold, such as holes or slots that are perpendicular to the direction of mold opening. Snap fits are features that allow two parts to be snapped together without the need for fasteners or adhesives. Both undercuts and snap fits can be challenging to manufacture and can lead to increased costs and quality issues.
To avoid undercut and snap fit issues, designers should:
- Minimize the use of undercuts and snap fits whenever possible
- Use side-action cams or slides to create undercuts in the mold
- Design snap fits with sufficient clearance and draft angles to allow for easy assembly and disassembly
- Use finite element analysis (FEA) to simulate the behavior of snap fits and ensure they will function as intended
6. Insufficient clearance for assembly
Clearance refers to the space between two mating parts that allows for easy assembly and disassembly. Insufficient clearance can lead to interference fits, which can cause parts to become stuck or damaged during assembly.
To ensure sufficient clearance for assembly, designers should:
- Understand the manufacturing processes and their tolerances
- Use a minimum clearance of 0.1 mm for most materials and processes
- Increase the clearance for larger parts or tighter tolerances
- Use 3D tolerance stackup analysis to ensure the clearances are adequate throughout the assembly
7. Unoptimized part orientation
Part orientation refers to the way a part is positioned in the mold or on the build platform during manufacturing. Unoptimized part orientation can lead to a variety of problems, including:
- Increased support material usage and post-processing time for 3D printed parts
- Warping or distortion due to uneven cooling in injection molded parts
- Difficulty filling the mold cavity or achieving uniform wall thickness
To optimize part orientation, designers should:
- Orient the part to minimize the amount of support material needed for 3D printing
- Orient the part to allow for easy ejection from the mold and minimize warping in injection molding
- Consider the flow of molten material and the location of gates and cooling channels
- Use simulation software to analyze the effects of part orientation on manufacturability and performance
8. Improper material selection
Material selection is a critical aspect of DFM that can have a significant impact on the manufacturability, performance, and cost of a part. Improper material selection can lead to a variety of problems, including:
- Difficulty processing the material due to its viscosity, shrinkage, or other properties
- Poor mechanical properties or dimensional stability
- Incompatibility with the intended use environment or regulations
- Higher material and processing costs
To select the proper material, designers should:
- Understand the requirements and constraints of the application, such as strength, stiffness, temperature resistance, and chemical resistance
- Consider the manufacturing process and its capabilities, such as the maximum achievable tolerances and surface finishes
- Use material property databases and supplier recommendations to identify suitable materials
- Conduct testing and prototyping to validate the material selection and performance
9. Lack of standardization
Standardization refers to the use of common parts, materials, and processes across a product family or organization. Lack of standardization can lead to increased complexity, higher costs, and longer lead times.
To improve standardization, designers should:
- Use off-the-shelf components whenever possible, such as fasteners, bearings, and connectors
- Develop a library of standard parts and features that can be reused across multiple designs
- Collaborate with suppliers to identify commonly available materials and processes
- Use modular design principles to create interchangeable subassemblies and components
10. Inadequate communication
Effective communication between designers, engineers, and manufacturers is essential for successful DFM. Inadequate communication can lead to misunderstandings, errors, and delays that can impact the quality, cost, and time-to-market of a product.
To improve communication, designers should:
- Use clear and concise documentation, such as 3D models, drawings, and specifications
- Collaborate with manufacturing engineers early in the design process to identify potential issues and opportunities for improvement
- Use design reviews and feedback loops to ensure that all stakeholders are aligned and informed
- Establish a culture of open communication and continuous improvement within the organization
FAQ
1. What is Design for Manufacturing (DFM)?
Design for Manufacturing (DFM) is a methodology that focuses on designing products that are easy to manufacture, assemble, and test. The goal of DFM is to reduce costs, improve quality, and accelerate time-to-market by optimizing the design for the manufacturing process.
2. Why is DFM important?
DFM is important because it can have a significant impact on the success of a product. By designing for manufacturability, companies can:
- Reduce manufacturing costs and lead times
- Improve product quality and reliability
- Increase production efficiency and capacity
- Accelerate time-to-market and customer satisfaction
3. What are some common DFM issues?
Some common DFM issues include:
- Incorrect tolerances
- Inadequate draft angles
- Improper wall thickness
- Poor gate and ejector pin placement
- Undercuts and snap fits
- Insufficient clearance for assembly
- Unoptimized part orientation
- Improper material selection
- Lack of standardization
- Inadequate communication
4. How can designers avoid DFM issues?
Designers can avoid DFM issues by:
- Collaborating with manufacturing engineers early in the design process
- Using DFM guidelines and best practices for the specific manufacturing process and material
- Conducting design reviews and simulations to identify potential issues
- Using standardized parts and materials whenever possible
- Communicating clearly and effectively with all stakeholders
5. What are the benefits of implementing DFM in product development?
The benefits of implementing DFM in product development include:
- Lower manufacturing costs and higher margins
- Faster time-to-market and increased competitiveness
- Improved product quality and customer satisfaction
- Reduced waste and environmental impact
- Enhanced collaboration and innovation within the organization
Conclusion
Design for Manufacturing (DFM) is a critical aspect of product development that can have a significant impact on the success of a product. By understanding and addressing the top 10 DFM problems that affect every design, designers and engineers can create products that are easier to manufacture, assemble, and test, resulting in lower costs, higher quality, and faster time-to-market.
To overcome these challenges, designers should collaborate closely with manufacturing engineers, use DFM guidelines and best practices, conduct thorough design reviews and simulations, and communicate effectively with all stakeholders. By implementing DFM principles and continuously improving their designs, companies can gain a competitive advantage and deliver innovative, high-quality products to their customers.
No responses yet