Understanding PCB Tolerances and Their Impact on Manufacturing
Printed Circuit Boards (PCBs) are essential components in modern electronic devices, providing the foundation for interconnecting various electronic components. The manufacturing process of PCBs involves several critical stages, each requiring precise control and adherence to specified tolerances. PCB tolerances play a vital role in ensuring the proper functionality, reliability, and compatibility of the final product. This article delves into the world of PCB tolerances, exploring their significance, types, and the impact they have on the manufacturing process.
What are PCB Tolerances?
PCB tolerances refer to the acceptable range of variation in the physical dimensions and properties of a printed circuit board. These tolerances are specified by designers and engineers to ensure that the manufactured PCB meets the required specifications and functions as intended. Tolerances are typically expressed as a plus or minus (±) value, indicating the maximum allowable deviation from the nominal or ideal measurement.
Why are PCB Tolerances Important?
Adhering to PCB tolerances is crucial for several reasons:
-
Functionality: Proper tolerances ensure that the PCB functions as designed. Deviations beyond the specified tolerances can lead to issues such as signal integrity problems, improper component fitment, and reduced reliability.
-
Compatibility: PCBs often interface with other components or systems. Maintaining tolerances guarantees that the PCB will fit and function correctly within the larger assembly.
-
Manufacturing Feasibility: Tolerances impact the manufacturability of the PCB. Overly tight tolerances may require specialized equipment or processes, increasing production costs and lead times. On the other hand, excessively loose tolerances can result in inconsistent quality and performance.
-
Quality and Reliability: Adherence to tolerances contributes to the overall quality and reliability of the PCB. Consistent and well-controlled manufacturing processes within the specified tolerances reduce the likelihood of defects and failures.
Types of PCB Tolerances
PCB tolerances can be categorized into several types based on the specific aspect of the board they relate to. Let’s explore some of the most common types of PCB tolerances.
1. Dimensional Tolerances
Dimensional tolerances refer to the acceptable variation in the physical dimensions of the PCB, such as length, width, and thickness. These tolerances ensure that the PCB fits properly within its designated space and aligns correctly with other components.
For example, the tolerance for the length and width of a PCB might be specified as ±0.2 mm. This means that the actual length and width of the manufactured board can vary by up to 0.2 mm from the nominal dimensions without causing issues.
Here’s a table illustrating some common dimensional tolerances for PCBs:
Dimension | Nominal Value | Tolerance |
---|---|---|
Length | 100 mm | ±0.2 mm |
Width | 80 mm | ±0.2 mm |
Thickness | 1.6 mm | ±0.1 mm |
2. Hole Size and Position Tolerances
Hole size and position tolerances are critical for ensuring proper component placement and fitment. These tolerances specify the acceptable variation in the diameter and location of drilled holes on the PCB.
-
Hole Size Tolerance: This tolerance defines the allowable variation in the diameter of drilled holes. It is essential for achieving a reliable and secure fit for through-hole components. Common hole size tolerances range from ±0.05 mm to ±0.1 mm, depending on the hole size and the specific requirements of the design.
-
Hole Position Tolerance: Hole position tolerance specifies the acceptable deviation in the location of drilled holes relative to their intended coordinates. Maintaining accurate hole positions is crucial for aligning components correctly and ensuring proper connections. Typical hole position tolerances range from ±0.1 mm to ±0.2 mm.
The table below shows some typical hole size and position tolerances:
Hole Type | Hole Size | Size Tolerance | Position Tolerance |
---|---|---|---|
Standard Hole | 0.8 mm | ±0.05 mm | ±0.1 mm |
Large Hole | 3.0 mm | ±0.1 mm | ±0.2 mm |
Micro Via | 0.2 mm | ±0.02 mm | ±0.05 mm |
3. Copper Thickness Tolerance
Copper thickness tolerance refers to the acceptable variation in the thickness of the copper layers on the PCB. The copper thickness plays a vital role in the electrical performance and current-carrying capacity of the traces.
PCB Manufacturers typically specify copper thickness in ounces per square foot (oz/ft²). Common copper thicknesses include 0.5 oz/ft², 1 oz/ft², and 2 oz/ft². The tolerance for copper thickness is usually expressed as a percentage of the nominal value.
For example, a 1 oz/ft² copper layer with a ±10% tolerance means that the actual copper thickness can range from 0.9 oz/ft² to 1.1 oz/ft².
Here’s a table showing copper thickness tolerances for different nominal values:
Nominal Copper Thickness | Tolerance |
---|---|
0.5 oz/ft² | ±10% |
1 oz/ft² | ±10% |
2 oz/ft² | ±10% |
4. Trace Width and Spacing Tolerances
Trace width and spacing tolerances are essential for ensuring proper signal integrity and preventing short circuits or signal crosstalk. These tolerances specify the acceptable variation in the width of copper traces and the spacing between them.
-
Trace Width Tolerance: This tolerance defines the allowable deviation in the width of the copper traces on the PCB. Maintaining consistent trace widths is crucial for controlling impedance and ensuring reliable signal transmission. Common trace width tolerances range from ±0.05 mm to ±0.1 mm, depending on the trace width and the manufacturing capabilities.
-
Trace Spacing Tolerance: Trace spacing tolerance specifies the minimum allowable distance between adjacent copper traces. Adequate spacing is necessary to prevent short circuits and minimize signal crosstalk. The tolerance for trace spacing depends on factors such as the PCB’s voltage rating, the manufacturing process, and the design requirements. Typical trace spacing tolerances range from ±0.1 mm to ±0.2 mm.
The following table illustrates some common trace width and spacing tolerances:
Trace Parameter | Nominal Value | Tolerance |
---|---|---|
Trace Width | 0.2 mm | ±0.05 mm |
Trace Spacing | 0.2 mm | ±0.1 mm |
5. Solder Mask Tolerances
Solder mask tolerances relate to the acceptable variation in the dimensions and registration of the solder mask layer on the PCB. The solder mask is a protective coating applied over the copper traces, leaving exposed areas for component soldering.
-
Solder Mask Aperture Tolerance: This tolerance specifies the allowable deviation in the size of the openings (apertures) in the solder mask layer. Accurate solder mask apertures are essential for proper component soldering and preventing solder bridging. Common solder mask aperture tolerances range from ±0.05 mm to ±0.1 mm.
-
Solder Mask Registration Tolerance: Solder mask registration tolerance defines the acceptable offset between the solder mask layer and the underlying copper features. Proper registration ensures that the solder mask aligns correctly with the copper traces and pads. Typical solder mask registration tolerances range from ±0.1 mm to ±0.2 mm.
Here’s a table summarizing solder mask tolerances:
Solder Mask Parameter | Tolerance |
---|---|
Aperture Size | ±0.05 mm |
Registration | ±0.1 mm |
Impact of PCB Tolerances on Manufacturing
PCB tolerances have a significant impact on the manufacturing process and the overall quality of the final product. Let’s explore how tolerances influence various aspects of PCB manufacturing.
1. Design for Manufacturability (DFM)
Design for Manufacturability (DFM) is the practice of designing PCBs with manufacturing considerations in mind. When designing a PCB, engineers must take into account the capabilities and limitations of the manufacturing process, including the achievable tolerances.
By adhering to DFM guidelines and specifying appropriate tolerances, designers can ensure that the PCB can be manufactured efficiently and reliably. This involves considering factors such as minimum feature sizes, clearances, and manufacturing process capabilities.
Failing to design within the acceptable tolerances can lead to manufacturing issues, such as difficulty in achieving the required dimensions, increased production costs, and potential delays.
2. Manufacturing Process Control
PCB manufacturers rely on precise process control to maintain the specified tolerances throughout the production process. This involves implementing strict quality control measures and utilizing advanced manufacturing techniques.
-
Imaging and Etching: The imaging and etching processes are critical for achieving accurate trace widths and spacings. Manufacturers use high-resolution imaging systems and well-controlled etching processes to ensure that the copper features are formed within the specified tolerances.
-
Drilling and Hole Plating: Precise drilling and hole plating are essential for maintaining hole size and position tolerances. Manufacturers employ CNC drilling machines and advanced plating techniques to achieve consistent and accurate hole formation.
-
Lamination and Pressing: The lamination and pressing processes involve bonding the PCB Layers together under controlled temperature and pressure conditions. Proper control of these processes helps maintain the overall dimensional stability and flatness of the PCB within the specified tolerances.
3. Quality Inspection and Testing
To ensure that the manufactured PCBs meet the specified tolerances, rigorous quality inspection and testing procedures are implemented. These include:
-
Visual Inspection: Visual inspection is performed to check for any visible defects, such as misaligned features, incomplete etching, or solder mask irregularities. Automated optical inspection (AOI) systems are often used to detect and measure deviations from the specified tolerances.
-
Dimensional Measurement: Dimensional measurement techniques, such as coordinate measuring machines (CMMs) or vision systems, are employed to verify that the PCB dimensions, hole sizes, and positions are within the specified tolerances.
-
Electrical Testing: Electrical testing is conducted to validate the functionality and performance of the PCB. This includes continuity testing, insulation resistance testing, and high-potential (hipot) testing to ensure that the PCB meets the electrical requirements and tolerances.
By implementing comprehensive quality inspection and testing procedures, manufacturers can identify and address any deviations from the specified tolerances, ensuring that only compliant PCBs are delivered to customers.
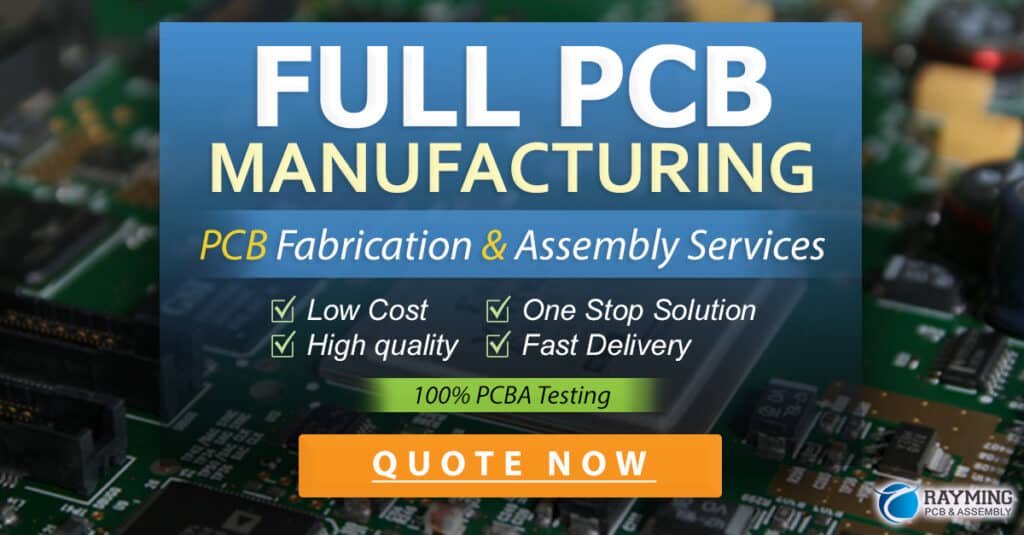
Frequently Asked Questions (FAQ)
-
What happens if the PCB dimensions exceed the specified tolerances?
If the PCB dimensions exceed the specified tolerances, it can lead to fitment issues when integrating the PCB into the final product. Excessive deviations can cause problems with component placement, alignment, and overall compatibility. In such cases, the PCB may need to be reworked or rejected, resulting in additional costs and delays. -
How can designers ensure that their PCB design is within the acceptable tolerances?
Designers can ensure that their PCB design is within the acceptable tolerances by following DFM guidelines and consulting with the PCB manufacturer. They should consider factors such as minimum feature sizes, clearances, and manufacturing process capabilities when specifying tolerances. Designers can also use PCB Design Software that includes DFM checks to identify and resolve any tolerance issues early in the design phase. -
What are the consequences of specifying overly tight tolerances?
Specifying overly tight tolerances can have several consequences. It may require specialized manufacturing equipment and processes, which can increase production costs and lead times. Tight tolerances also increase the likelihood of manufacturing defects and yield issues, as it becomes more challenging to consistently achieve the required dimensions and properties. Designers should strike a balance between the necessary tolerances for functionality and the practicality of manufacturing. -
How do PCB tolerances affect the cost of manufacturing?
PCB tolerances have a direct impact on manufacturing costs. Tighter tolerances generally require more precise manufacturing processes, specialized equipment, and increased inspection and testing. This can result in higher production costs compared to PCBs with more relaxed tolerances. Designers should consider the cost implications when specifying tolerances and work closely with the PCB manufacturer to find a cost-effective solution that meets the functional requirements. -
Can PCB tolerances be modified after the design is finalized?
Modifying PCB tolerances after the design is finalized can be challenging and may require significant changes to the design and manufacturing process. It is always better to consider and specify appropriate tolerances during the initial design phase. If changes are necessary, designers should communicate with the PCB manufacturer to assess the feasibility and impact of the modifications on the manufacturing process and timeline.
Conclusion
PCB tolerances play a crucial role in ensuring the proper functionality, reliability, and manufacturability of printed circuit boards. Understanding the different types of tolerances, such as dimensional, hole size and position, copper thickness, trace width and spacing, and solder mask tolerances, is essential for designers and engineers.
Adherence to PCB tolerances has a significant impact on the manufacturing process, influencing factors such as design for manufacturability, process control, and quality inspection. By specifying appropriate tolerances and working closely with PCB manufacturers, designers can optimize the performance and reliability of their PCBs while minimizing manufacturing issues and costs.
As technology advances and electronic devices become more complex, the importance of PCB tolerances will only continue to grow. By staying informed about tolerance considerations and best practices, designers and manufacturers can collaborate effectively to produce high-quality PCBs that meet the evolving demands of the electronics industry.
No responses yet