Introduction to Thunderbolt Technology
Thunderbolt is a revolutionary high-speed serial data transfer technology developed by Intel and Apple. It combines PCI Express (PCIe) and DisplayPort (DP) into a single, compact interface, allowing for incredibly fast data transfer rates and high-resolution display support. Thunderbolt has become increasingly popular in recent years due to its versatility and performance, making it an attractive option for designers looking to incorporate high-speed data transfer capabilities into their PCB designs.
Key Features of Thunderbolt Technology
- High-speed data transfer rates (up to 40 Gbps with Thunderbolt 3 and 4)
- Daisy-chaining capabilities, allowing multiple devices to be connected in series
- Ability to transmit power, data, and video over a single cable
- Compatibility with a wide range of devices, including displays, storage devices, and peripherals
Thunderbolt PCB Design Considerations
When designing a PCB to incorporate Thunderbolt technology, there are several key considerations to keep in mind to ensure optimal performance and reliability.
Signal Integrity
Signal integrity is crucial in Thunderbolt PCB design due to the high-speed nature of the interface. Designers must carefully consider factors such as trace routing, impedance matching, and crosstalk to maintain signal quality and minimize interference.
Trace Routing
- Keep trace lengths as short as possible to minimize signal loss and reflections
- Maintain consistent trace widths and spacing to ensure proper impedance matching
- Use serpentine routing techniques to match trace lengths and minimize skew
- Avoid sharp bends and corners in traces to reduce reflections and signal distortion
Impedance Matching
- Design traces to match the characteristic impedance of the Thunderbolt interface (typically 100 ohms differential)
- Use controlled impedance techniques, such as stripline or microstrip, to maintain consistent impedance throughout the trace
- Employ termination resistors at the receiver end to minimize reflections and improve signal quality
Crosstalk Reduction
- Increase spacing between adjacent traces to minimize electromagnetic coupling
- Use ground planes and guard traces to shield sensitive signals from interference
- Employ differential signaling techniques to cancel out common-mode noise
Power Delivery
Thunderbolt technology allows for power delivery over the same cable used for data and video transmission. When designing a Thunderbolt PCB, it is essential to consider the power requirements of the connected devices and ensure that the power delivery system is capable of meeting those needs.
Power Budgeting
- Determine the power requirements of each connected device
- Calculate the total power budget for the system, taking into account the capabilities of the Thunderbolt controller and the power supply
- Ensure that the power delivery system can provide sufficient current to meet the demands of all connected devices
Power Integrity
- Use appropriate decoupling capacitors near power pins to minimize voltage ripple and ensure stable power delivery
- Employ solid power and ground planes to distribute power evenly across the PCB
- Use sufficient copper weight and via stitching to minimize voltage drop and maintain low impedance power distribution
Electromagnetic Compatibility (EMC)
Thunderbolt PCBs must be designed with EMC in mind to ensure that they do not emit excessive electromagnetic interference (EMI) and are not susceptible to external EMI sources.
EMI Reduction Techniques
- Use shielding techniques, such as metal enclosures or conductive coatings, to contain EMI generated by the PCB
- Employ filtering techniques, such as ferrite beads or LC filters, to suppress high-frequency noise
- Minimize the loop area of high-speed signals to reduce electromagnetic radiation
ESD Protection
- Incorporate electrostatic discharge (ESD) protection devices, such as transient voltage suppressors (TVS) or varistors, to protect sensitive components from ESD events
- Use proper grounding techniques and provide low-impedance paths to safely discharge ESD energy
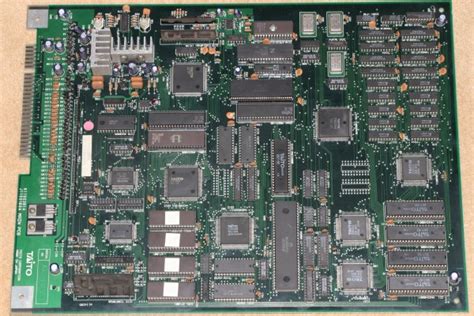
Thunderbolt Controller Selection
Selecting the appropriate Thunderbolt controller is essential for ensuring compatibility and optimal performance in your PCB design.
Thunderbolt Controller Options
Controller | Max Speed | Key Features |
---|---|---|
Intel JHL7540 (Titan Ridge) | 40 Gbps | Thunderbolt 3, USB 3.1 Gen 2, DisplayPort 1.4 |
Intel JHL7440 (Maple Ridge) | 40 Gbps | Thunderbolt 3, USB 3.1 Gen 2, DisplayPort 1.2 |
Intel JHL6540 (Alpine Ridge) | 40 Gbps | Thunderbolt 3, USB 3.1 Gen 1, DisplayPort 1.2 |
Intel JHL6340 (Alpine Ridge) | 20 Gbps | Thunderbolt 3, USB 3.1 Gen 1, DisplayPort 1.2 |
Considerations for Controller Selection
- Ensure compatibility with the desired Thunderbolt version (3 or 4)
- Consider the required data transfer speeds and video capabilities
- Evaluate the power consumption and thermal characteristics of the controller
- Assess the availability of driver support and firmware updates
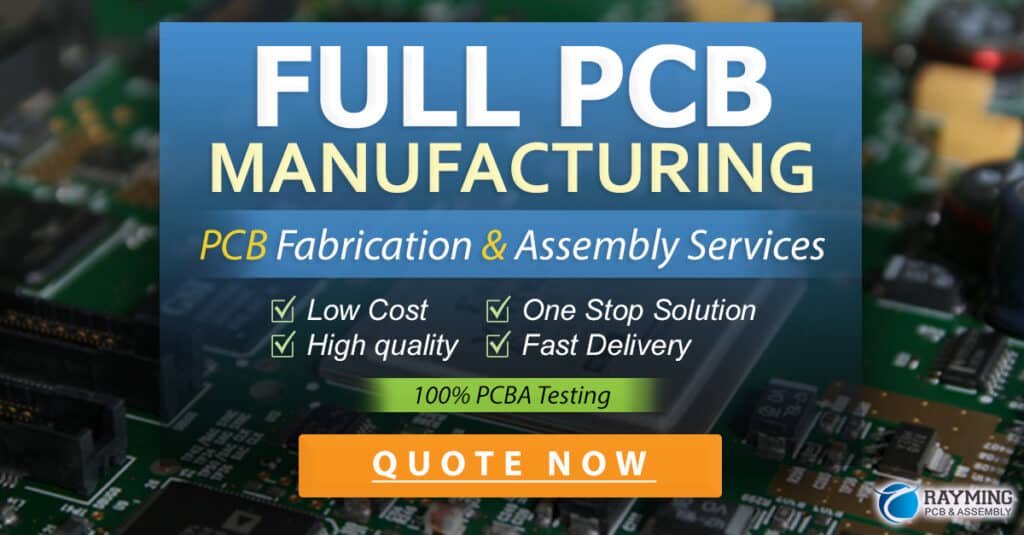
Thunderbolt Connector and Cable Selection
Choosing the appropriate connectors and cables is crucial for ensuring reliable and high-performance Thunderbolt connectivity.
Connector Types
- USB Type-C connector (used for Thunderbolt 3 and 4)
- Mini DisplayPort connector (used for earlier Thunderbolt versions)
Cable Considerations
- Use high-quality, certified Thunderbolt cables to ensure optimal signal integrity and reliability
- Consider the length of the cable and its impact on signal quality and power delivery
- Ensure that the cable supports the desired Thunderbolt version and data transfer speeds
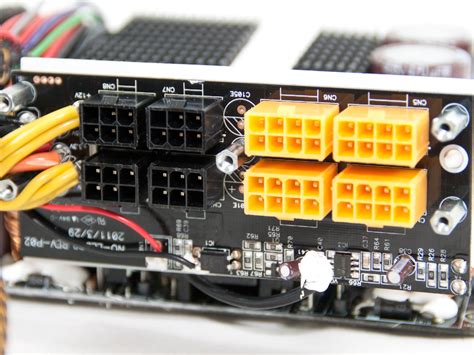
PCB Layout and Routing Guidelines
Proper PCB layout and routing are essential for achieving optimal performance and reliability in Thunderbolt designs.
Component Placement
- Place the Thunderbolt controller close to the connector to minimize trace lengths
- Ensure that power delivery components, such as regulators and capacitors, are located near the controller and connector
- Keep sensitive components away from high-speed traces and potential sources of EMI
Trace Routing
- Route high-speed traces on inner layers to minimize interference and improve signal integrity
- Use differential pair routing techniques for Thunderbolt data lines
- Maintain consistent trace widths and spacing throughout the design
- Avoid crossing high-speed traces over gaps or splits in ground planes
Ground and Power Planes
- Use solid ground and power planes to provide low-impedance return paths and minimize voltage drop
- Employ via stitching techniques to ensure good electrical connection between ground and power planes
- Use appropriate decoupling capacitors near power pins to minimize voltage ripple and ensure stable power delivery
Simulation and Verification
Simulating and verifying your Thunderbolt PCB design is essential for identifying and addressing potential issues before fabrication.
Signal Integrity Simulation
- Perform pre-layout and post-layout signal integrity simulations to assess the quality of high-speed signals
- Use tools such as IBIS models and S-parameter models to accurately simulate the behavior of Thunderbolt components
- Analyze simulation results to identify potential issues, such as reflections, crosstalk, and signal attenuation
Power Integrity Analysis
- Conduct power integrity simulations to ensure that the power delivery system can meet the demands of the connected devices
- Analyze voltage drop, current density, and power plane impedance to identify potential power delivery issues
- Use simulation results to optimize the placement and sizing of power delivery components
EMC Analysis
- Perform EMC simulations to assess the electromagnetic compatibility of the PCB design
- Identify potential sources of EMI and evaluate the effectiveness of shielding and filtering techniques
- Use simulation results to make necessary adjustments to the design to ensure compliance with relevant EMC standards
Testing and Validation
After fabrication, it is crucial to thoroughly test and validate your Thunderbolt PCB to ensure proper functionality and reliability.
Functional Testing
- Verify that the Thunderbolt interface is functioning correctly and can communicate with connected devices
- Test data transfer speeds and video output to ensure that they meet the desired specifications
- Validate power delivery functionality and ensure that connected devices receive sufficient power
Signal Integrity Measurements
- Use high-bandwidth oscilloscopes and probes to measure the quality of Thunderbolt signals
- Analyze eye diagrams and jitter measurements to assess the integrity of high-speed signals
- Compare measured results to simulation results and make necessary adjustments to the design
EMC Testing
- Conduct EMC testing to ensure that the PCB complies with relevant electromagnetic compatibility standards
- Measure radiated and conducted emissions to verify that they are within acceptable limits
- Test the susceptibility of the PCB to external EMI sources and validate the effectiveness of shielding and filtering techniques
Future Developments and Trends
As Thunderbolt technology continues to evolve, PCB designers must stay informed about the latest developments and trends to ensure that their designs remain competitive and future-proof.
Thunderbolt 4
Thunderbolt 4, the latest version of the technology, brings several improvements and new features, including:
- Increased minimum performance requirements for video and data
- Support for dual 4K displays or a single 8K display
- Improved security features, such as protection against unauthorized access and firmware updates
- Backward compatibility with Thunderbolt 3 devices and USB 4
USB 4 Integration
USB 4, the next generation of the USB standard, incorporates Thunderbolt 3 technology, allowing for high-speed data transfer and display capabilities over a USB Type-C connector. As USB 4 gains adoption, PCB designers will need to consider the implications of this integration and design their boards accordingly.
Increasing Adoption in Various Industries
Thunderbolt technology is finding applications in a wide range of industries, including:
- Professional audio and video production
- Automotive infotainment systems
- Industrial automation and control
- Medical imaging and diagnostics
As the adoption of Thunderbolt continues to grow, PCB designers will need to adapt their designs to meet the specific requirements of these industries.
Conclusion
Designing a PCB to incorporate Thunderbolt technology requires careful consideration of signal integrity, power delivery, electromagnetic compatibility, and component selection. By following best practices and guidelines for PCB layout and routing, simulation, and testing, designers can create high-performance, reliable Thunderbolt solutions that meet the demands of today’s data-intensive applications. As Thunderbolt technology continues to evolve and find new applications, staying informed about the latest developments and trends will be crucial for success in this exciting and rapidly-growing field.
Frequently Asked Questions (FAQ)
-
Q: What is the difference between Thunderbolt 3 and Thunderbolt 4?
A: Thunderbolt 4 builds upon the capabilities of Thunderbolt 3, offering increased minimum performance requirements, support for dual 4K displays or a single 8K display, improved security features, and backward compatibility with Thunderbolt 3 devices and USB 4. -
Q: Can Thunderbolt be used with non-Intel processors?
A: While Thunderbolt was initially developed by Intel and Apple, the technology has been opened up to other manufacturers. Thunderbolt controllers are now available from various vendors, allowing for integration with non-Intel processors. -
Q: What are the key considerations for ensuring signal integrity in Thunderbolt PCB designs?
A: To ensure signal integrity in Thunderbolt PCB designs, key considerations include trace routing (keeping traces short, maintaining consistent widths and spacing, using serpentine routing), impedance matching (matching the characteristic impedance of the interface, using controlled impedance techniques), and crosstalk reduction (increasing trace spacing, using ground planes and guard traces, employing differential signaling). -
Q: How does Thunderbolt handle power delivery?
A: Thunderbolt technology allows for power delivery over the same cable used for data and video transmission. When designing a Thunderbolt PCB, it is essential to consider the power requirements of the connected devices, ensure that the power delivery system can meet those needs, and employ proper power integrity techniques, such as decoupling capacitors and solid power and ground planes. -
Q: What are the important factors to consider when selecting a Thunderbolt controller for a PCB design?
A: When selecting a Thunderbolt controller for a PCB design, important factors to consider include compatibility with the desired Thunderbolt version (3 or 4), required data transfer speeds and video capabilities, power consumption and thermal characteristics, and availability of driver support and firmware updates.
No responses yet