What is Through-Hole Technology (THT)?
Through-hole technology, also known as through-hole mounting or thru-hole mounting, is the traditional method of assembling electronic components onto a PCB. In THT assembly, component leads are inserted into drilled holes on the PCB and then soldered onto pads on the opposite side of the board.
Advantages of THT Assembly
- Strong mechanical bonds between components and PCB
- Can handle high power and high voltage components
- Easier to visually inspect solder joints
- Components can be easily swapped out or replaced
- Well-suited for prototyping and low-volume production
Disadvantages of THT Assembly
- Requires drilling holes in the PCB
- Takes up more space due to larger component footprints
- Generally slower assembly process than SMD
- Higher labor costs for manual insertion and soldering
- Not well-suited for high-density designs
What is Surface Mount Technology (SMD/SMT)?
Surface mount technology, also called surface mount device or SMD, is a more modern PCB Assembly method where components are mounted directly onto the surface of the PCB instead of being inserted through holes. The components used for SMD assembly are smaller and have either flat contact pads or short pins for soldering.
Advantages of SMD Assembly
- Smaller component and PCB sizes allow for higher density designs
- Faster automated assembly process
- Lower labor costs due to automation
- Better mechanical performance under shake and vibration conditions
- Suited for high-volume production
Disadvantages of SMD Assembly
- Requires specialized equipment for precise component placement
- Not well-suited for high power/voltage components
- Visual inspection of solder joints is more difficult
- Components are harder to replace or rework
- Higher initial setup costs for automated assembly
THT vs. SMD Component Sizes and Packages
One of the key differences between THT and SMD is the size and packaging of the components used. THT components have long leads that are inserted into holes, while SMD components have small metal tabs or pads for soldering directly to the PCB surface.
Common THT component packages include:
– DIP (Dual Inline Package)
– TO-220 (Transistor Outline)
– TO-92 (Transistor Outline)
– Axial and radial lead
Typical SMD component packages include:
– Chip resistors and capacitors
– SOT (Small Outline Transistor)
– QFP (Quad Flat Pack)
– QFN (Quad Flat No-leads)
– BGA (Ball Grid Array)
Here is a table comparing some common THT and SMD package sizes:
Package | THT Size (mm) | SMD Size (mm) |
---|---|---|
Resistor | 3.6 x 1.7 | 1.0 x 0.5 |
Capacitor | 5.2 x 2.5 | 1.6 x 0.8 |
IC | 16 x 6 | 7 x 7 (QFP) |
Transistor | 4.5 x 3.5 (TO-92) | 3 x 1.75 (SOT-23) |
As you can see, SMD components are significantly smaller than their THT counterparts, which allows for much higher component density on SMD boards.
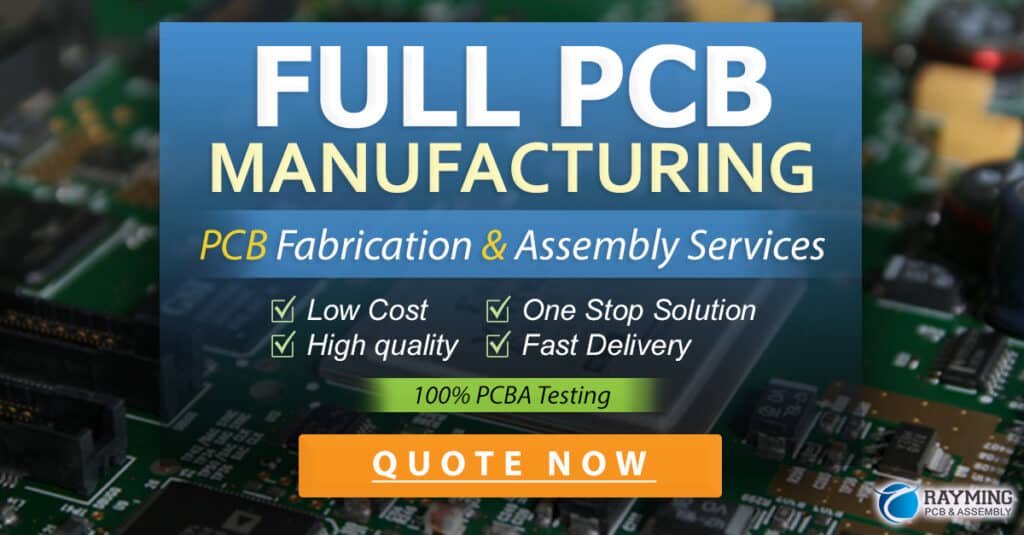
PCB Design Considerations for THT vs. SMD
The choice between THT and SMD assembly impacts the PCB design process. Here are some key considerations:
THT Design Considerations
- Larger drilled holes and annular rings needed for component leads
- Wider spacing required between components for soldering access
- Traces and vias must be routed around/between holes
- Larger overall board size compared to SMD
SMD Design Considerations
- Smaller pad sizes and spacing allows for higher density layout
- Traces can be routed underneath components
- Thermal management is critical due to higher power densities
- May require additional copper layers for routing
- Requires tighter manufacturing tolerances
When designing a PCB for either THT or SMD assembly, it’s important to adhere to the relevant design rules and guidelines to ensure manufacturability, reliability, and optimal performance.
THT vs. SMD Manufacturing Process
The manufacturing process is another area where THT and SMD differ significantly. Here’s a comparison of the typical steps involved:
THT Manufacturing Process
- Drill holes in blank PCB according to design file
- Apply solder mask and silkscreen
- Manually insert components into holes
- Wave solder components to board
- Clean flux residue from board
- Visually inspect solder joints
- Test and debug assembled board
SMD Manufacturing Process
- Apply solder paste to PCB pads via stencil
- Place components onto solder paste using automated pick-and-place machine
- Run board through reflow oven to melt solder and bond components
- Visually inspect placement and solder joints
- Perform automated optical inspection (AOI) to check for defects
- Test and debug assembled board
The SMD process is generally faster and more automated than THT, which translates to lower labor costs and higher throughput. However, SMD does require more specialized equipment and has higher initial setup costs.
Reliability and Durability of THT vs. SMD
Both THT and SMD assemblies can be highly reliable when designed and manufactured properly. However, there are some differences in terms of durability under various conditions.
THT Reliability Factors
- Strong mechanical bonds between components and PCB
- Can handle higher power and voltage levels
- Less susceptible to vibration and mechanical stress
- Easier to visually inspect and rework
- Well-suited for high-reliability applications
SMD Reliability Factors
- More resistant to shock and vibration due to lower mass
- Better thermal performance due to smaller size and direct PCB contact
- Higher component density can lead to increased heat generation
- More complex inspection and rework processes
- Requires strict adherence to design and manufacturing guidelines
In general, THT is often preferred for high-power, high-reliability applications such as aerospace, military, and industrial equipment. SMD is more commonly used in consumer electronics, telecommunications, and other applications where size and weight are critical factors.
Rework and Repair of THT vs. SMD Assemblies
The ease of rework and repair is another consideration when choosing between THT and SMD. In general, THT assemblies are easier to rework and repair than SMD.
THT Rework and Repair
- Components can be easily desoldered and replaced
- Visual inspection of solder joints is straightforward
- Manual soldering techniques can be used for rework
- Requires basic soldering tools and skills
SMD Rework and Repair
- Components are more difficult to remove and replace
- Specialized equipment (hot air, tweezers, microscope) is often required
- Visual inspection of solder joints is more challenging
- Risk of damaging nearby components during rework
- Requires advanced soldering skills and training
While SMD rework and repair is certainly possible, it does require more specialized tools, skills, and techniques compared to THT.
Cost Comparison of THT vs. SMD Assembly
The cost of THT vs. SMD assembly can vary depending on factors such as the complexity of the design, the volume of production, and the level of automation used. Here’s a general comparison:
THT Assembly Costs
- Lower initial setup costs (no specialized equipment required)
- Higher labor costs for manual insertion and soldering
- Higher component costs due to larger size and packaging
- Slower assembly process leads to lower throughput and efficiency
SMD Assembly Costs
- Higher initial setup costs for automated equipment and tooling
- Lower labor costs due to automated placement and soldering
- Lower component costs due to smaller size and standardized packaging
- Faster assembly process leads to higher throughput and efficiency
In general, SMD assembly is more cost-effective for high-volume production, while THT may be more economical for low-volume or prototype runs. However, the specific cost breakdown will depend on the details of the project.
Choosing Between THT and SMD Assembly
With all of the factors we’ve discussed in mind, how do you choose between THT and SMD for your PCB assembly project? Here are some guidelines:
Consider using THT if:
– Your design requires high power or high voltage components
– Mechanical strength and durability are top priorities
– You need to easily rework or replace components
– You’re producing prototypes or low volumes
Consider using SMD if:
– Your design requires high component density and small form factor
– You need faster assembly and higher throughput
– You’re producing high volumes and need to minimize labor costs
– Your application requires better shock and vibration resistance
In some cases, a mix of THT and SMD components (known as a hybrid assembly) may be the best option. This allows you to take advantage of the benefits of both technologies where they’re best suited.
Frequently Asked Questions (FAQ)
-
Can SMD components be used on a THT board?
While it’s not common, SMD components can be used on a THT board with the use of adapters or by creating SMD footprints on the PCB. However, this may negate some of the size and density advantages of SMD. -
Are THT assemblies more reliable than SMD?
Both THT and SMD assemblies can be highly reliable when designed and manufactured properly. THT is often preferred for high-power and high-reliability applications, while SMD is known for its resistance to shock and vibration. -
Is it possible to rework SMD assemblies?
Yes, SMD assemblies can be reworked, but it requires specialized equipment, skills, and techniques compared to THT rework. It’s important to follow proper procedures to avoid damaging components or the PCB. -
Which is cheaper, THT or SMD assembly?
The cost comparison depends on various factors, but in general, SMD assembly is more cost-effective for high-volume production due to lower labor costs and faster assembly speeds. THT may be more economical for low-volume or prototype runs. -
Can you mix THT and SMD components on the same board?
Yes, it’s possible to use a mix of THT and SMD components on the same PCB, known as a hybrid assembly. This can be a good option when you need to take advantage of the specific benefits of each technology for different parts of the design.
Conclusion
In the battle of THT vs. SMD, there’s no one-size-fits-all answer. The choice between these two PCB assembly technologies depends on a variety of factors, including the specific requirements of your design, the production volume, and the available resources.
THT assembly is often preferred for its mechanical strength, ease of rework, and suitability for high-power applications, while SMD assembly offers advantages in terms of size, density, speed, and cost-effectiveness for high-volume production.
By understanding the key differences between THT and SMD, and carefully considering the needs of your project, you can make an informed decision on which PCB assembly process is the best fit for your application. And in some cases, a hybrid approach combining both technologies may be the optimal solution.
Ultimately, the goal is to choose the assembly method that will result in a reliable, high-quality PCB that meets all of your design and performance requirements, while also balancing cost and manufacturing efficiency.
No responses yet