What is Through Hole Technology?
Through Hole Technology (THT) is a traditional Mounting Method where electronic components have long leads that are inserted into drilled holes on a Printed Circuit Board (PCB). The leads are then soldered to the pads on the opposite side of the board, creating a strong mechanical and electrical connection.
Advantages of Through Hole Technology
- Strong mechanical bonding: THT components are securely fastened to the PCB, making them resistant to vibration and physical stress.
- Easy to replace: If a component fails, it can be easily removed and replaced without damaging the PCB.
- Suitable for high-power applications: THT components can handle higher power levels compared to SMT components.
- Ideal for prototyping: THT is a cost-effective method for low-volume production and prototyping.
Disadvantages of Through Hole Technology
- Larger footprint: THT components require drilled holes, which occupy more space on the PCB compared to SMT components.
- Limited component density: Due to the larger size of THT components, the overall component density on the PCB is lower.
- Slower assembly process: Inserting and soldering THT components is a more time-consuming process compared to SMT assembly.
- Higher assembly costs: The manual labor involved in THT assembly leads to higher costs, especially for high-volume production.
What is Surface Mount Technology?
Surface Mount Technology (SMT) is a modern mounting method where electronic components are placed directly onto the surface of a Printed Circuit Board (PCB). The components have small leads or terminations that are soldered to pads on the same side of the board.
Advantages of Surface Mount Technology
- Higher component density: SMT components are smaller in size, allowing for a higher density of components on the PCB.
- Faster assembly process: SMT assembly is highly automated, resulting in faster production times and lower labor costs.
- Improved performance: SMT components have shorter lead lengths, reducing parasitic inductance and capacitance, leading to better high-frequency performance.
- Cost-effective for high-volume production: The automated nature of SMT assembly makes it more cost-effective for large-scale production.
Disadvantages of Surface Mount Technology
- Difficult manual assembly: Due to the small size of SMT components, manual assembly and rework can be challenging.
- Specialized equipment required: SMT assembly requires specialized pick-and-place machines and reflow ovens, which can be expensive.
- Limited power handling: SMT components typically have lower power handling capabilities compared to THT components.
- Susceptible to thermal stress: SMT components are more susceptible to thermal stress during the soldering process, which can lead to component damage if not properly managed.
Factors to Consider When Choosing Between THT and SMT
When deciding between Through Hole and Surface Mount technologies, several factors should be considered:
- Application requirements: Consider the specific requirements of your application, such as power handling, mechanical strength, and environmental factors.
- Production volume: THT is more suitable for low-volume production and prototyping, while SMT is more cost-effective for high-volume production.
- PCB size and density: SMT allows for higher component density and smaller PCB sizes, which may be crucial for space-constrained applications.
- Available equipment and expertise: Ensure that you have access to the necessary equipment and expertise for the chosen mounting method.
- Cost considerations: Evaluate the overall cost implications of each method, including component costs, assembly costs, and equipment investments.
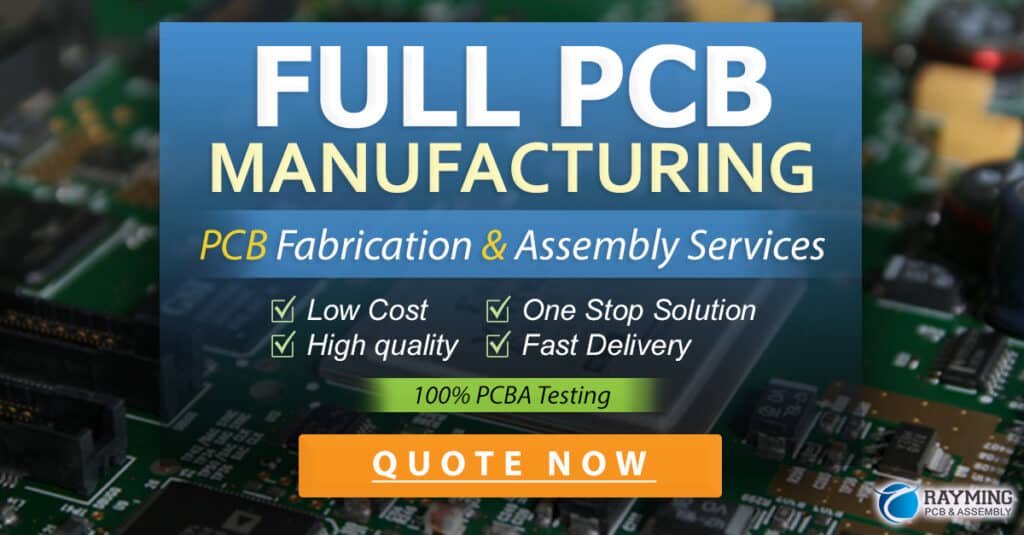
Comparing THT and SMT
To help you make an informed decision, let’s compare the key aspects of Through Hole and Surface Mount technologies:
Aspect | Through Hole Technology (THT) | Surface Mount Technology (SMT) |
---|---|---|
Component size | Larger | Smaller |
PCB space utilization | Lower density | Higher density |
Assembly process | Manual, slower | Automated, faster |
Assembly costs | Higher for high-volume | Lower for high-volume |
Power handling | Higher | Lower |
Mechanical strength | Stronger | Weaker |
Rework and replacement | Easier | More challenging |
Thermal stress | Less susceptible | More susceptible |
Frequently Asked Questions (FAQ)
-
Q: Can SMT and THT components be used together on the same PCB?
A: Yes, it is possible to use both SMT and THT components on the same PCB. This is known as a mixed-technology PCB. However, it’s essential to consider the assembly process and ensure compatibility between the components and the chosen mounting methods. -
Q: Are there any specific industries that prefer one mounting method over the other?
A: Industries that require high reliability, such as aerospace, military, and medical, often prefer THT due to its strong mechanical bonding and easier rework. Industries that prioritize miniaturization and high-volume production, such as consumer electronics, typically favor SMT. -
Q: How do the costs of THT and SMT components compare?
A: SMT components are generally less expensive than their THT counterparts due to their smaller size and higher production volumes. However, the overall cost of assembly should be considered, as SMT assembly requires specialized equipment and setup costs. -
Q: Can SMT components be manually soldered?
A: While it is possible to manually solder SMT components, it can be challenging due to their small size and close proximity to other components. Specialized tools, such as tweezers and a fine-tipped soldering iron, are required for manual SMT soldering. -
Q: Are there any environmental considerations when choosing between THT and SMT?
A: SMT is generally considered more environmentally friendly due to the reduced use of materials, such as lead and PCB substrate, compared to THT. Additionally, SMT allows for smaller PCB sizes, which can lead to reduced electronic waste.
Conclusion
Choosing the right mounting method between Through Hole and Surface Mount technologies is crucial for the success of your electronic project. By understanding the advantages, disadvantages, and specific applications of each method, you can make an informed decision based on your project requirements, production volume, available resources, and cost considerations.
THT is ideal for applications that require strong mechanical bonding, easy rework, and high power handling, while SMT excels in high-volume production, miniaturization, and improved high-frequency performance.
Ultimately, the choice between THT and SMT depends on the specific needs of your project. By carefully evaluating the factors discussed in this article, you can select the mounting method that best suits your requirements, ensuring the optimal performance and reliability of your electronic assembly.
No responses yet