Understanding the Basics of PCB Design
What is a PCB?
A PCB is a flat board made of insulating material, such as fiberglass or plastic, with conductive copper traces printed on one or both sides. These traces connect various electronic components, such as resistors, capacitors, and integrated circuits, to form a complete circuit.
Types of PCBs
There are three main types of PCBs:
- Single-sided PCBs: These have copper traces on only one side of the board.
- Double-sided PCBs: These have copper traces on both sides of the board, with through-hole connections between the layers.
- Multi-layer PCBs: These have multiple layers of copper traces, separated by insulating material, with through-hole or via connections between the layers.
PCB Design Software
To design a PCB, you will need to use specialized software. There are many options available, both free and paid, such as:
- KiCad (free and open-source)
- Eagle (free for non-commercial use, paid for commercial use)
- Altium Designer (paid)
- OrCAD (paid)
Planning Your PCB Design
Define Your Requirements
Before starting your PCB design, you need to clearly define your requirements. This includes:
- The purpose and functionality of the circuit
- The size and shape constraints of the PCB
- The power requirements and voltage levels
- The environmental conditions (temperature, humidity, etc.)
- The manufacturing and assembly processes
Create a Schematic
The first step in PCB design is to create a schematic of your circuit. This is a graphical representation of the electrical connections between the components. It helps you to visualize the circuit and check for errors before proceeding to the layout stage.
Choose Your Components
Once you have a schematic, you need to choose the specific components that will be used in your circuit. This includes:
- Resistors, capacitors, and inductors
- Integrated circuits (ICs)
- Connectors and switches
- Power supplies and regulators
When choosing components, consider factors such as:
- Electrical specifications (voltage, current, power rating, etc.)
- Physical size and package type
- Availability and cost
- Reliability and durability
Designing Your PCB Layout
Component Placement
The next step is to place the components on the PCB layout. This involves:
- Arranging the components in a logical and efficient manner
- Minimizing the distance between connected components
- Avoiding interference between components
- Ensuring adequate spacing for manufacturing and assembly
Routing the Traces
After placing the components, you need to route the copper traces that connect them. This involves:
- Choosing the appropriate trace width and spacing
- Avoiding sharp angles and creating smooth curves
- Minimizing the length of traces to reduce signal loss and interference
- Adding via holes to connect traces on different layers
Adding Power and Ground Planes
In addition to the signal traces, you need to add power and ground planes to your PCB. These are large areas of copper that provide a low-impedance path for power and ground signals. They help to reduce noise and improve signal integrity.
Design Rule Checking (DRC)
Before finalizing your PCB layout, you need to perform a Design Rule Check (DRC). This is an automated process that checks your design against a set of predefined rules, such as:
- Minimum trace width and spacing
- Minimum drill hole size
- Minimum clearance between components
- Maximum number of layers
DRC helps to ensure that your design is manufacturable and meets the required specifications.
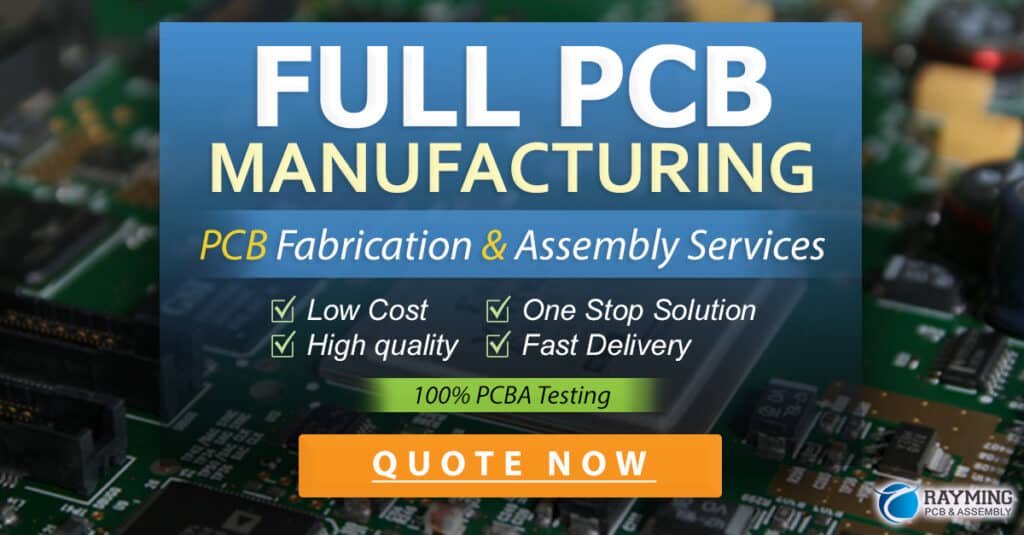
Manufacturing Your PCB
Choosing a PCB Manufacturer
Once your PCB design is complete, you need to choose a manufacturer to produce your boards. There are many factors to consider when choosing a manufacturer, such as:
- Quality and reliability
- Cost and lead time
- Minimum order quantity (MOQ)
- Capabilities and services offered
Preparing Your Design Files
Before sending your design to the manufacturer, you need to prepare the necessary files. This typically includes:
- Gerber files: These are the industry-standard format for PCB manufacturing data. They contain information about the copper layers, solder mask, silkscreen, and drill holes.
- Drill files: These specify the location and size of the drill holes in the PCB.
- Bill of Materials (BOM): This is a list of all the components used in the design, including their part numbers, quantities, and manufacturers.
- Assembly drawings: These provide instructions for assembling the components onto the PCB.
Prototype and Testing
Before mass production, it is essential to create a prototype of your PCB and test it thoroughly. This helps to identify any issues with the design or manufacturing process and ensures that the final product meets your requirements.
Common PCB Design Mistakes to Avoid
Incorrect Component Footprints
One of the most common mistakes in PCB design is using incorrect component footprints. This can lead to components not fitting properly on the board or not making proper electrical connections. Double-check the footprints of all components against their datasheets before finalizing your design.
Inadequate Power and Ground Connections
Another common mistake is not providing adequate power and ground connections to the components. This can lead to signal integrity issues, noise, and even component failure. Ensure that your power and ground planes are properly sized and connected to all the necessary components.
Ignoring Thermal Management
Electronic components generate heat during operation, and if this heat is not properly dissipated, it can lead to component failure and reduced reliability. When designing your PCB, consider the thermal management requirements of your components and include features such as heatsinks, thermal vias, and adequate spacing to promote heat dissipation.
Not Considering Manufacturing Constraints
PCB manufacturing processes have certain constraints and limitations that must be considered during the design process. For example, there are minimum trace widths and spacing requirements, minimum drill hole sizes, and maximum aspect ratios for via holes. Ignoring these constraints can lead to manufacturing issues and increased costs.
Not Testing Thoroughly
Finally, not testing your PCB thoroughly before mass production is a recipe for disaster. Even small issues can lead to significant problems down the line, resulting in costly rework or even product recalls. Always create a prototype and test it under various conditions to ensure that it meets your requirements and performs reliably.
FAQs
1. What is the difference between a schematic and a PCB layout?
A schematic is a graphical representation of the electrical connections between components, while a PCB layout is the physical arrangement of those components on a printed circuit board. The schematic shows how the components are connected electrically, while the layout shows where they are placed physically on the board and how the copper traces are routed to connect them.
2. How do I choose the right PCB manufacturer?
When choosing a PCB manufacturer, consider factors such as their quality and reliability, cost and lead time, minimum order quantity, and the capabilities and services they offer. Look for manufacturers with good reviews and a proven track record of delivering high-quality PCBs on time and within budget. Don’t just go with the cheapest option, as this can often lead to issues with quality and reliability.
3. What is the purpose of a ground plane in a PCB?
A ground plane is a large area of copper on a PCB that is connected to the ground (0V) potential. Its purpose is to provide a low-impedance return path for electrical currents, which helps to reduce noise and improve signal integrity. Ground planes also help to distribute heat evenly across the board, which can improve the overall reliability of the circuit.
4. Can I design a PCB without using specialized software?
While it is technically possible to design a PCB without using specialized software, it is not recommended. PCB design software provides many tools and features that make the design process much easier and more efficient, such as component libraries, autorouting, and design rule checking. Attempting to design a PCB manually would be extremely time-consuming and prone to errors.
5. How long does it typically take to manufacture a PCB?
The manufacturing time for a PCB can vary depending on several factors, such as the complexity of the design, the number of layers, the quantity ordered, and the capabilities of the manufacturer. For simple, low-quantity orders, the manufacturing time can be as short as a few days, while for more complex, high-quantity orders, it can take several weeks or even months. It’s important to plan ahead and allow sufficient time for manufacturing when developing your project timeline.
Conclusion
PCB design is a complex and multi-faceted process that requires a deep understanding of electronics, manufacturing, and design principles. By following the guidelines outlined in this article and avoiding common mistakes, you can create high-quality, reliable PCBs that meet your specific requirements. Remember to always plan ahead, choose your components and manufacturer carefully, and test thoroughly before committing to mass production. With the right approach and attention to detail, you can bring your electronic product ideas to life and create innovative solutions that make a real difference in the world.
No responses yet