Introduction to Thermocouple Sensors
A thermocouple sensor is a type of temperature measurement device consisting of two dissimilar metal wires joined at one end, called the hot junction or measuring junction. When this junction experiences a temperature change, a voltage is produced that can be correlated back to the temperature.
Thermocouples are widely used in industry, science, and engineering applications for temperature measurement and control due to their wide temperature range, low cost, ease of use, and durability. They can measure temperatures from -200°C to +2500°C depending on the metals used.
How Thermocouple Sensors Work
The operating principle of a thermocouple is based on the Seebeck effect, named after German physicist Thomas Johann Seebeck who discovered it in 1821. When two dissimilar metals are joined at both ends and one junction is hotter than the other, a voltage is generated that is approximately proportional to the temperature difference between the junctions. This voltage is called the Seebeck voltage.
In a practical thermocouple circuit, the two wires are joined at one end to form the measuring junction which is placed in the environment to be measured. The other end of the wires connect to a voltage measurement instrument such as a digital thermometer at the reference junction, which is usually kept at a known reference temperature such as 0°C in an ice bath.
The net open circuit voltage is a function of the temperatures of the two junctions and the composition of the two metals. This voltage can be looked up in standard thermocouple reference tables to determine the temperature at the measuring junction.
Types of Thermocouple Sensors
Thermocouples are designated by capital letters that indicate their composition according to American Society for Testing and Materials (ASTM) conventions. The four most common thermocouple types are J, K, T and E:
Type | Positive Wire | Negative Wire | Temperature Range | Typical Applications |
---|---|---|---|---|
J | Iron | Constantan | 0 to 750°C | Older industrial equipment, vacuum furnaces, inert atmospheres |
K | Chromel | Alumel | -200 to 1250°C | General purpose, oxidizing atmospheres, aircraft engines, industrial ovens |
T | Copper | Constantan | -250 to 350°C | Low temperature, oxidizing or reducing atmospheres, food industry |
E | Chromel | Constantan | -200 to 900°C | High temperature, oxidizing atmospheres, industrial ovens, plastics |
Other standardized thermocouple types include B, R, S, C, and M which use platinum or tungsten alloys for very high temperature applications up to 2500°C. There are also non-letter designated types for specific applications.
The choice of thermocouple type depends on the temperature range, atmosphere, required accuracy, and cost. In general, base metal thermocouples (J, K, T, E) are less expensive and more commonly used than noble metal types.
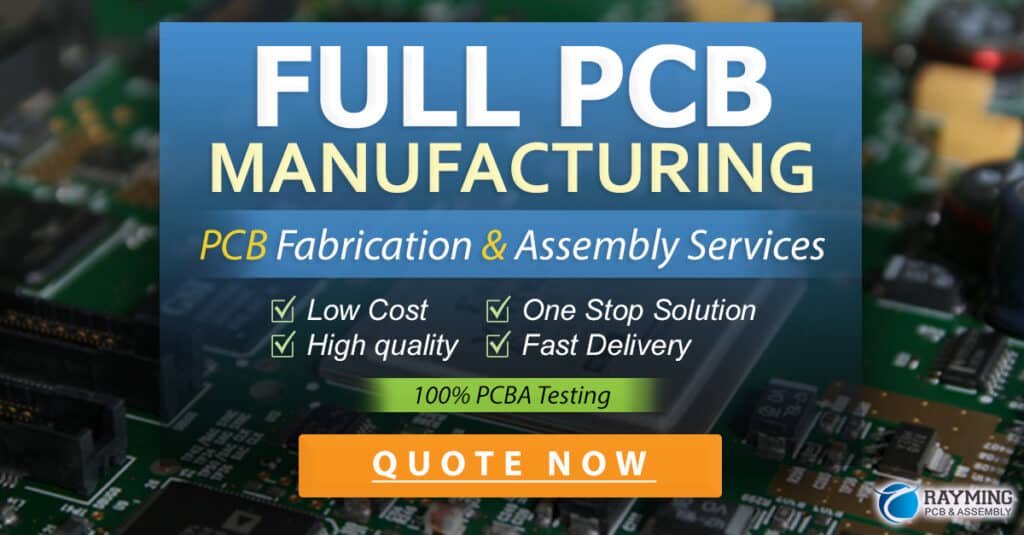
Thermocouple Construction and Protection
A typical industrial thermocouple probe consists of four parts:
- Thermocouple wires – the dissimilar metal wires that generate the Seebeck voltage
- Insulation – high temperature ceramic or mineral insulating material that provides electrical isolation and protection for the wires
- Protective sheath – a metal tube, usually stainless steel, that houses the insulated wires and provides mechanical protection and a means for mounting
- Connectors – a plug and jack for easily connecting the wires to the measuring instrument
Thermocouples can be made with bare wires for laboratory use or with a variety of sheath materials and diameters to suit different industrial application needs, such as fast response, high pressure, or corrosive environments. Protective sheaths can be made from stainless steel, Inconel, ceramic, or refractory metals.
The measuring junction can be made by welding, soldering, or mechanically joining the two wires. The most common configurations are:
- Grounded – the wires are welded to the inside of the sheath for fast response
- Ungrounded – the wires are isolated from the sheath for electrical noise reduction
- Exposed – the bare wires protrude from the sheath for fastest response and minimal sheath conduction error
Thermocouple Signal Conditioning
Since the Seebeck voltage produced by a thermocouple is only on the order of millivolts, it requires some signal conditioning before it can be accurately measured or used for control. The three main components of a thermocouple signal conditioning system are:
-
Cold Junction Compensation (CJC) – a means of measuring the reference junction temperature so it can be compensated for, since only the hot junction temperature is of interest. This can be done with a thermistor, diode, or RTD sensor incorporated into the measurement instrument.
-
Amplification – the low level thermocouple voltage is amplified by an instrumentation amplifier to increase the signal level and improve the signal-to-noise ratio. Typical gains are 100 to 1000.
-
Linearization – the Seebeck voltage is not perfectly linear with temperature, so the signal is often digitized and run through a microcontroller or PC-based lookup table to linearize it. NIST provides ITS-90 polynomial equations for voltage-to-temperature conversion.
In addition, the measurement instrument may provide other functions such as digital display, data logging, alarm outputs, or communication to a control system.
Thermocouple Accuracy and Sources of Error
The accuracy of a thermocouple measurement depends on several factors, including:
-
Thermocouple wire accuracy – the purity and homogeneity of the wire materials. Standard wire accuracy classes are 1, 2, and 3, with class 1 being the most accurate.
-
Extension wire errors – the wires that connect the thermocouple to the instrument can introduce errors if not properly matched or temperature-compensated.
-
Noise and interference – electrical noise from nearby equipment or power lines can couple into the signal wires. Shielded extension wire and filters can reduce interference.
-
Sheath conduction – heat transfer between the sheath and the wires can cause temperature gradients. Exposed junction probes minimize this effect.
-
Drift – the thermocouple output can change over time due to chemical and metallurgical changes in the wires, especially at high temperatures. Regular calibration or replacement may be needed.
Typical accuracy for an industrial thermocouple system is ±2°C or 0.75% of reading, although high accuracy systems can achieve ±0.5°C or better. Thermocouples are generally more accurate at high temperatures than at room temperature.
Advantages and Disadvantages of Thermocouples
The main advantages of thermocouple sensors are:
- Wide temperature range – from cryogenic to over 2000°C
- Rugged and durable – can withstand vibration, pressure, and harsh environments
- Fast response time – small junction gives rapid response to temperature changes
- Low cost – base metal types are inexpensive compared to other sensor types
- Simple and versatile – easy to install, replace, and interface with instruments
The main disadvantages of thermocouples are:
- Low accuracy – not as precise as RTDs or thermistors, especially at low temperatures
- Reference required – a stable reference junction temperature is needed for absolute accuracy
- Non-linear output – output is not perfectly proportional to temperature
- Least stable – more drift and variation than other temperature sensor types
- Noise sensitive – low voltage output is susceptible to electrical interference
Despite their limitations, thermocouples remain one of the most popular temperature sensors for industrial applications due to their unique advantages. Continuing development of materials and signal conditioning techniques helps to improve their performance.
Applications of Thermocouple Sensors
Some common applications of thermocouple sensors include:
- Industrial process control – monitoring and controlling temperature in ovens, furnaces, reactors, boilers, etc.
- Engine temperature measurement – measuring exhaust gas, cylinder head, and bearing temperatures in internal combustion engines
- HVAC and refrigeration – air and fluid temperature measurement for heating, ventilation, air conditioning, and refrigeration equipment
- Power generation – monitoring temperatures in power plant boilers, turbines, generators, and heat exchangers
- Medical equipment – temperature control in medical devices such as dialysis machines, sterilizers, and thermal therapy equipment
- Food processing – cooking, baking, pasteurizing, and freezing process temperature control
- Plastics manufacturing – melt and mold temperature measurement for injection molding and extrusion processes
- Aerospace – jet engine, rocket motor, and spacecraft temperature monitoring
- Meteorology – atmospheric and oceanographic temperature profiling
- Materials testing – measuring material properties as a function of temperature
New applications for thermocouples continue to be developed as the need for temperature measurement and control expands in various fields.
Frequently Asked Questions
1. What is the difference between grounded and ungrounded thermocouples?
A grounded thermocouple has the measuring junction welded directly to the protective metal sheath, providing faster response but also allowing any electrical noise on the sheath to affect the measurement. An ungrounded thermocouple has the junction insulated from the sheath, providing better noise immunity but slower response. The choice depends on the specific application requirements.
2. Can thermocouple wires be extended or spliced?
Yes, thermocouple wires can be extended using special extension wires that have the same material composition and Seebeck coefficient as the original wires. The extension wires must be connected with the correct polarity and should be protected from temperature gradients. Splices can be made but they will introduce an additional junction that must be kept at the same temperature as the reference junction.
3. How often should a thermocouple be calibrated?
The calibration interval depends on the application, the required accuracy, and the conditions of use. Thermocouples exposed to high temperatures or corrosive environments will drift faster and require more frequent calibration, typically every 3-12 months. For less critical applications, calibration every 1-2 years may be sufficient. It is important to have a regular calibration schedule and to keep records of the calibration data.
4. What is the cold junction compensation and why is it needed?
The cold junction, or reference junction, is the connection point between the thermocouple wires and the measuring instrument. Since the thermocouple output is a function of the temperature difference between the measuring and reference junctions, the reference junction temperature must be known in order to calculate the absolute temperature at the measuring junction. Cold junction compensation (CJC) is a way of measuring the reference junction temperature, typically using a thermistor or diode sensor, and adding it to the thermocouple output. Most modern thermocouple instruments have built-in CJC.
5. Can thermocouples be used in hazardous areas?
Yes, special thermocouple designs are available for use in hazardous areas such as explosive atmospheres. These designs use approved safety barriers, intrinsically safe circuits, or explosion-proof housings to prevent the thermocouple from becoming an ignition source. The specific requirements depend on the type of hazard and the local regulations. It is important to consult with a qualified engineer and to follow all relevant safety standards when using thermocouples in hazardous areas.
Conclusion
Thermocouple sensors are a versatile and cost-effective solution for temperature measurement in a wide range of applications. By understanding their operating principles, construction, signal conditioning requirements, and performance characteristics, users can select and apply thermocouples effectively for their specific needs. While thermocouples have some limitations in terms of accuracy and stability, they offer unique advantages in terms of wide temperature range, ruggedness, and fast response. As technology continues to advance, thermocouples will remain an important tool for temperature measurement and control in many fields.
No responses yet