What is Thermal Shock?
Thermal shock refers to the stress induced in a material due to sudden and significant changes in temperature. When a material experiences a rapid temperature change, it can lead to the development of thermal gradients within the material, causing different parts to expand or contract at varying rates. This differential expansion or contraction can result in the formation of cracks, warping, or even complete failure of the material or component.
Factors Influencing Thermal Shock Resistance
Several factors influence a material’s ability to withstand thermal shock:
- Coefficient of thermal expansion (CTE): Materials with lower CTE values are generally more resistant to thermal shock.
- Thermal conductivity: High thermal conductivity allows for faster heat dissipation, reducing thermal gradients and the risk of thermal shock.
- Mechanical properties: Materials with higher strength, toughness, and ductility are more likely to withstand thermal shock without failing.
- Geometry: The shape and size of a component can affect its susceptibility to thermal shock, with thinner and more complex geometries being more vulnerable.
Importance of Thermal Shock Testing
Thermal shock testing is essential for ensuring the reliability, durability, and safety of materials and components subjected to extreme temperature fluctuations. By simulating real-world conditions in a controlled environment, thermal shock testing helps identify potential weaknesses and failure modes before the product is released to the market.
Industries and Applications
Thermal shock testing is relevant to a wide range of industries and applications, including:
- Automotive: Engine components, exhaust systems, and brake discs.
- Aerospace: Jet engine components, spacecraft heat shields, and satellite systems.
- Electronics: Printed circuit boards, solder joints, and electronic packaging.
- Energy: Power plant components, solar panels, and wind turbine blades.
- Ceramics: Refractories, cookware, and dental implants.
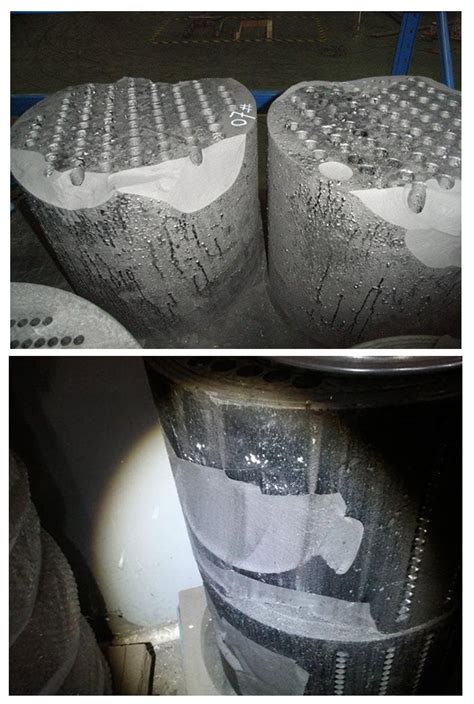
Thermal Shock Testing Methods
There are several methods employed for thermal shock testing, each with its own advantages and limitations. The choice of method depends on the specific material, component, and application being tested.
Air-to-Air Thermal Shock Testing
Air-to-air thermal shock testing involves exposing the test specimen to alternating cycles of hot and cold air. The sample is typically placed in a chamber with two compartments maintained at different temperatures. The specimen is then automatically transferred between the hot and cold chambers at predetermined intervals.
Advantages:
– Relatively simple and cost-effective
– Suitable for testing larger components
– Allows for testing at a wide range of temperatures
Limitations:
– Slower heating and cooling rates compared to other methods
– Less severe thermal shock compared to liquid-based methods
Liquid-to-Liquid Thermal Shock Testing
Liquid-to-liquid thermal shock testing involves submerging the test specimen in alternating baths of hot and cold liquids, such as water, oil, or molten salt. This method provides a more severe thermal shock due to the higher heat transfer rates of liquids compared to air.
Advantages:
– Rapid heating and cooling rates
– More severe thermal shock compared to air-to-air testing
– Suitable for testing smaller components
Limitations:
– More complex and expensive setup
– Limited temperature range due to the boiling and freezing points of the liquids used
– Potential for contamination of the test specimen
Laser Thermal Shock Testing
Laser thermal shock testing utilizes high-power lasers to rapidly heat the surface of the test specimen, followed by quick cooling using either air or a liquid. This method allows for precise control over the heated area and the temperature gradient induced in the material.
Advantages:
– Highly localized heating, enabling testing of specific regions
– Rapid heating rates
– Non-contact method, minimizing the risk of contamination
Limitations:
– Limited to testing surface effects
– Expensive equipment and setup
– Potential for surface damage or modification due to laser irradiation
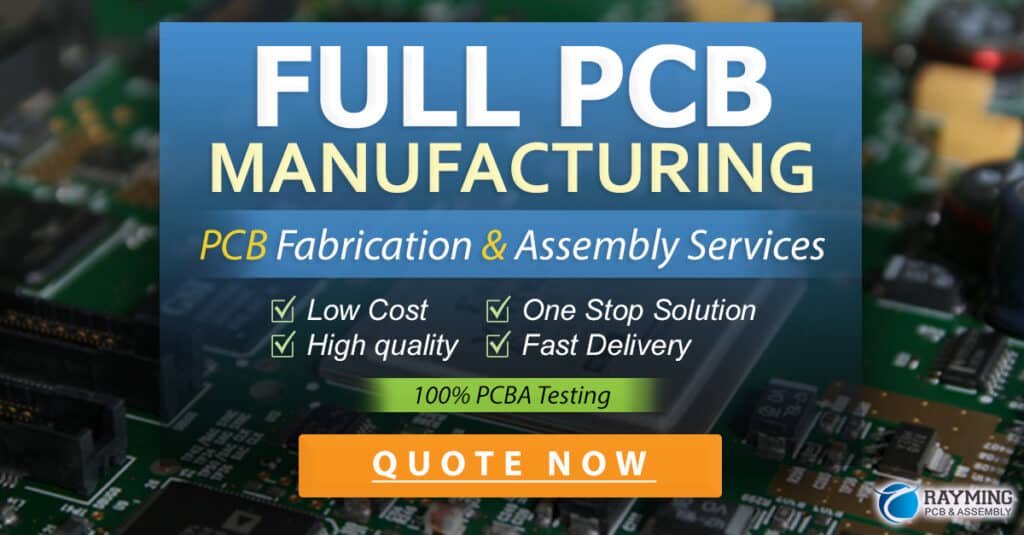
Thermal Shock Testing Standards
Several international standards provide guidelines and requirements for thermal shock testing, ensuring consistency and comparability of results across different laboratories and industries. Some of the most widely used standards include:
- ASTM C1100: Standard Test Method for Thermal Shock Resistance of Graphite Materials by Water Quenching
- ASTM C1525: Standard Test Method for Determination of Thermal Shock Resistance for Advanced Ceramics by Water Quenching
- IEC 60068-2-14: Environmental testing – Part 2-14: Tests – Test N: Change of temperature
- MIL-STD-883: Test Method Standard for Microcircuits
These standards specify the test procedures, equipment requirements, sample preparation, and data analysis methods to be followed for reliable and reproducible thermal shock testing results.
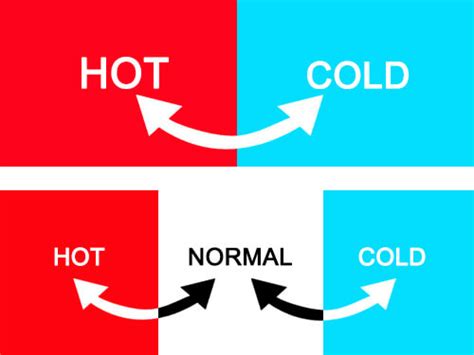
Interpreting Thermal Shock Testing Results
Interpreting the results of thermal shock testing requires a thorough understanding of the material properties, failure mechanisms, and the specific application requirements. The following factors are typically considered when analyzing thermal shock testing results:
- Visual inspection: Examining the test specimen for signs of cracking, warping, or other visible damage.
- Non-destructive testing: Utilizing techniques such as ultrasonic testing, X-ray imaging, or thermography to detect internal defects or stress concentrations.
- Mechanical testing: Evaluating the post-shock mechanical properties, such as strength, hardness, or fracture toughness, to assess the extent of degradation.
- Microstructural analysis: Investigating the material’s microstructure using microscopy techniques to identify any changes or damage at the microscopic level.
Based on the analysis of the thermal shock testing results, engineers and material scientists can make informed decisions regarding material selection, design optimization, and process improvements to enhance the thermal shock resistance of the final product.
Case Studies
To illustrate the practical applications of thermal shock testing, let’s consider a few case studies from different industries.
Automotive Exhaust Systems
Exhaust systems in vehicles are subjected to extreme temperature fluctuations, with temperatures ranging from ambient to over 1000°C during operation. Thermal shock testing is crucial for evaluating the durability and performance of exhaust components, such as manifolds, catalytic converters, and mufflers.
In a study conducted by Zhang et al. (2019), a stainless steel exhaust manifold was subjected to air-to-air thermal shock testing, with temperatures cycling between 100°C and 800°C. The results showed that the manifold experienced significant thermal fatigue cracking after 500 cycles, highlighting the need for improved material selection and design optimization to enhance thermal shock resistance.
Ceramic Matrix Composites for Aerospace Applications
Ceramic matrix composites (CMCs) are increasingly being used in aerospace applications due to their high-temperature stability, low density, and excellent mechanical properties. However, CMCs are susceptible to thermal shock damage, particularly in applications such as jet engine components and spacecraft heat shields.
A research study by Singh et al. (2018) investigated the thermal shock behavior of a SiC/SiC ceramic matrix composite using water quenching. The samples were heated to temperatures ranging from 400°C to 1200°C and then quenched in water at room temperature. The results demonstrated that the CMC maintained its structural integrity and mechanical properties up to a quench temperature of 800°C, indicating its suitability for high-temperature aerospace applications.
Electronic Packaging Materials
Electronic packaging materials, such as solder joints and printed circuit boards, are subjected to thermal shock during the assembly process and in-service conditions. Thermal shock testing is essential for evaluating the reliability and durability of these materials to ensure the long-term performance of electronic devices.
A study by Yin et al. (2020) investigated the thermal shock resistance of lead-free solder joints using a liquid-to-liquid thermal shock testing method. The solder joints were subjected to temperature cycling between -40°C and 125°C, with a dwell time of 10 minutes at each temperature. The results showed that the lead-free solder joints experienced a significant reduction in shear strength and an increase in crack propagation after 1000 thermal shock cycles, emphasizing the need for improved solder alloy formulations and joint designs.
Frequently Asked Questions (FAQ)
- What is the difference between thermal shock and thermal cycling?
-
Thermal shock involves rapid and significant temperature changes, typically over a short period, while thermal cycling involves more gradual temperature changes over a longer period. Thermal shock testing focuses on the material’s ability to withstand sudden temperature fluctuations, while thermal cycling testing evaluates the material’s long-term performance under repeated temperature variations.
-
How do I select the appropriate thermal shock testing method for my application?
-
The choice of thermal shock testing method depends on several factors, including the material type, component size and geometry, expected service conditions, and the severity of the thermal shock required. Air-to-air testing is suitable for larger components and a wide temperature range, while liquid-to-liquid testing provides more severe thermal shock for smaller components. Laser thermal shock testing is ideal for localized testing and surface effects.
-
What are the key standards for thermal shock testing?
-
Some of the key standards for thermal shock testing include ASTM C1100 for graphite materials, ASTM C1525 for advanced ceramics, IEC 60068-2-14 for environmental testing, and MIL-STD-883 for microcircuits. These standards provide guidelines and requirements for test procedures, equipment, sample preparation, and data analysis.
-
How can I improve the thermal shock resistance of my product?
-
Improving thermal shock resistance involves a combination of material selection, design optimization, and process control. Selecting materials with low CTE, high thermal conductivity, and good mechanical properties can enhance thermal shock resistance. Optimizing the component geometry to minimize thermal gradients and stress concentrations can also help. Process control measures, such as controlled cooling rates and minimizing residual stresses, can further improve the product’s thermal shock performance.
-
What are the potential consequences of thermal shock failure?
- Thermal shock failure can lead to various consequences depending on the application, ranging from reduced performance and reliability to complete failure and safety hazards. In the automotive industry, thermal shock failure of exhaust components can result in leaks, reduced engine efficiency, and increased emissions. In the aerospace sector, thermal shock failure of critical components like jet engine parts or spacecraft heat shields can have catastrophic consequences. In the electronics industry, thermal shock failure of solder joints or printed circuit boards can lead to device malfunction, short circuits, and premature failure.
Conclusion
Thermal shock testing is a critical process for evaluating the ability of materials and components to withstand sudden and significant temperature changes. By simulating real-world conditions in a controlled environment, thermal shock testing helps identify potential weaknesses and failure modes, ensuring the reliability, durability, and safety of products across various industries.
This article has provided an in-depth overview of thermal shock testing, covering its importance, methods, standards, and interpretation of results. By understanding the fundamentals of thermal shock testing and its applications, engineers and material scientists can make informed decisions to improve the thermal shock resistance of their products, ultimately leading to better performance and customer satisfaction.
As technology advances and new materials emerge, the field of thermal shock testing will continue to evolve, with more sophisticated testing methods and analysis techniques. Staying up-to-date with the latest developments and best practices in thermal shock testing is crucial for organizations to remain competitive and deliver high-quality, reliable products to their customers.
No responses yet