Introduction
When it comes to mounting heatsinks on electronic components, the choice between thermal pads and thermal paste can make a significant difference in the overall cooling performance. Both thermal pads and thermal paste are designed to enhance heat transfer from the heat-generating component to the heatsink, but they have distinct properties and use cases. In this article, we will explore the differences between thermal pads and thermal paste, their advantages and disadvantages, and help you determine the best choice for your specific application.
What are Thermal Pads?
Thermal pads, also known as thermal interface pads, are pre-cut, solid sheets of thermally conductive material. They are typically made from silicone or other polymer-based materials that are infused with thermally conductive fillers, such as ceramic particles or metal oxides. Thermal pads come in various thicknesses, ranging from 0.5mm to 5mm, and different thermal conductivity ratings, measured in W/mK (Watts per meter-Kelvin).
Advantages of Thermal Pads
- Easy to apply: Thermal pads are pre-cut to specific sizes and can be easily placed between the heat source and the heatsink without the need for spreading or curing.
- No mess: Unlike thermal paste, thermal pads do not require any cleaning or removal of excess material after application.
- Electrical insulation: Most thermal pads offer electrical insulation, preventing short circuits between the component and the heatsink.
- Gap-filling properties: Thermal pads can effectively fill small air gaps between the heat source and the heatsink, ensuring better contact and heat transfer.
Disadvantages of Thermal Pads
- Lower thermal conductivity: Compared to high-quality thermal pastes, thermal pads generally have lower thermal conductivity, which may result in slightly higher temperatures.
- Limited conformity: Thermal pads may not conform as well to surface irregularities as thermal paste, leading to potential air gaps and reduced heat transfer efficiency.
- Higher cost: Thermal pads are often more expensive than thermal paste, especially for larger applications or when covering multiple components.
What is Thermal Paste?
Thermal paste, also known as thermal grease or thermal compound, is a viscous substance applied between the heat source and the heatsink to enhance heat transfer. It is composed of a base material, such as silicone or zinc oxide, mixed with thermally conductive fillers, such as silver, aluminum, or ceramic particles. Thermal paste fills the microscopic air gaps and irregularities between the mating surfaces, allowing for better thermal contact and heat dissipation.
Advantages of Thermal Paste
- Higher thermal conductivity: High-quality thermal pastes offer superior thermal conductivity compared to thermal pads, enabling more efficient heat transfer from the component to the heatsink.
- Better conformity: Thermal paste can easily conform to surface irregularities, minimizing air gaps and ensuring optimal contact between the heat source and the heatsink.
- Thin bond line: Thermal paste allows for a thinner bond line between the mating surfaces, which can lead to improved heat transfer and lower overall thermal resistance.
- Cost-effective: Thermal paste is generally more affordable than thermal pads, making it a cost-effective solution for most applications.
Disadvantages of Thermal Paste
- Application process: Applying thermal paste requires a steady hand and proper technique to ensure an even spread and optimal coverage. Incorrect application can lead to air bubbles or uneven distribution, reducing cooling performance.
- Messy cleanup: Excess thermal paste needs to be cleaned from the surrounding area after application, which can be a messy and time-consuming process.
- Pump-out effect: In some cases, thermal cycling (repeated heating and cooling) can cause the thermal paste to deteriorate or pump out from between the mating surfaces, leading to reduced cooling performance over time.
- Electrical conductivity: Some thermal pastes contain electrically conductive particles, such as silver or aluminum, which can cause short circuits if they come into contact with exposed electrical components.
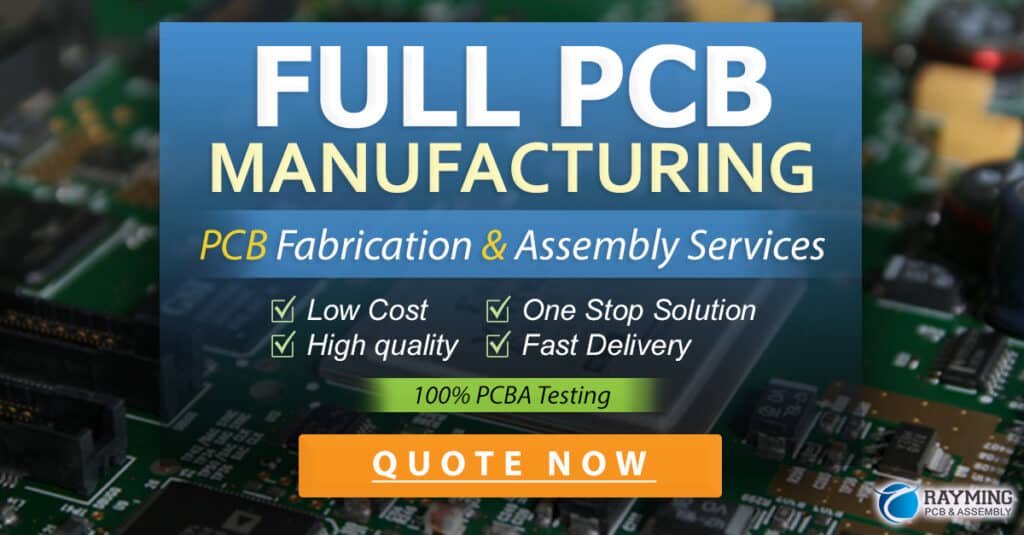
Choosing Between Thermal Pads and Thermal Paste
When deciding between thermal pads and thermal paste, consider the following factors:
-
Thermal performance requirements: If your application demands the highest possible cooling performance, thermal paste is generally the better choice due to its superior thermal conductivity. However, if the temperature difference is not critical, thermal pads can provide adequate cooling.
-
Ease of application: Thermal pads are easier to apply and do not require any spreading or curing. If you prioritize simplicity and quick installation, thermal pads may be the preferred option.
-
Gap-filling requirements: If your application involves mating surfaces with significant surface irregularities or air gaps, thermal pads can be a better choice due to their gap-filling properties. Thermal paste may not be able to fill larger gaps effectively.
-
Electrical insulation: If electrical insulation between the component and the heatsink is crucial, thermal pads are the safer choice. Most thermal pads offer inherent electrical insulation, reducing the risk of short circuits.
-
Cost considerations: Thermal paste is typically more cost-effective than thermal pads, especially for larger applications or when covering multiple components. However, the cost difference may be negligible for smaller projects.
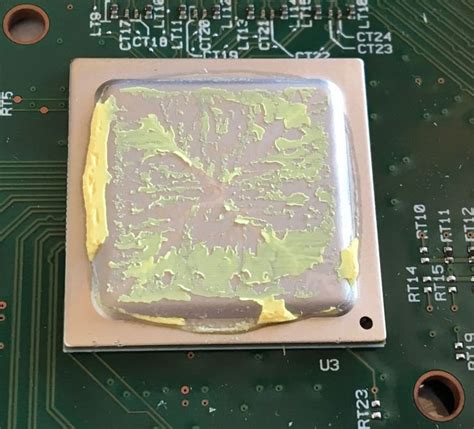
Application Techniques
Applying Thermal Pads
- Clean the surfaces: Ensure that the mating surfaces of the heat source and the heatsink are clean and free from dust, dirt, or old thermal material.
- Cut the thermal pad: If necessary, cut the thermal pad to the required size using scissors or a utility knife. Make sure the pad covers the entire heat source without overlapping.
- Remove the protective film: Thermal pads often come with a protective film on both sides. Remove the film before application.
- Place the thermal pad: Position the thermal pad on the heat source, ensuring that it is centered and covers the entire surface.
- Mount the heatsink: Place the heatsink on top of the thermal pad and apply even pressure to ensure good contact. Secure the heatsink using the appropriate mounting hardware.
Applying Thermal Paste
- Clean the surfaces: As with thermal pads, make sure the mating surfaces are clean and free from any contaminants.
- Apply the thermal paste: There are several methods for applying thermal paste, including the dot method, the line method, and the spread method. The most common approach is to apply a small dot (about the size of a rice grain) of thermal paste at the center of the heat source.
- Mount the heatsink: Carefully place the heatsink on top of the thermal paste, ensuring that it is centered and aligned with the heat source. Apply gentle pressure to spread the thermal paste evenly between the surfaces.
- Secure the heatsink: Use the appropriate mounting hardware to secure the heatsink in place, applying even pressure to maintain good contact with the heat source.
- Clean excess paste: Remove any excess thermal paste from the surrounding area using a lint-free cloth or a cotton swab dipped in isopropyl alcohol.
Thermal Conductivity Comparison
The thermal conductivity of thermal pads and thermal paste can vary significantly depending on the specific product and its composition. Here is a general comparison of the thermal conductivity ranges for common thermal interface materials:
Thermal Interface Material | Thermal Conductivity Range (W/mK) |
---|---|
Thermal Pads | 0.5 – 15 |
Thermal Paste (silicone-based) | 0.5 – 4 |
Thermal Paste (metal-based) | 2 – 80 |
It is essential to note that higher thermal conductivity does not always translate to better overall cooling performance. Factors such as bond line thickness, surface roughness, and pressure also play a crucial role in determining the effectiveness of the thermal interface material.
Frequently Asked Questions (FAQ)
- Can I use both thermal pads and thermal paste together?
-
No, it is not recommended to use both thermal pads and thermal paste together. Using both can create additional thermal resistance and may lead to uneven contact between the surfaces. Choose either thermal pads or thermal paste based on your specific requirements.
-
How often should I replace thermal pads or thermal paste?
-
The lifespan of thermal pads and thermal paste depends on various factors, such as temperature, humidity, and the quality of the material. As a general rule, if you notice a significant increase in temperatures or decreased cooling performance, it may be time to replace the thermal interface material. In most cases, replacing thermal pads or thermal paste every 2-3 years is sufficient.
-
Can I reuse thermal pads or thermal paste?
-
It is not recommended to reuse thermal pads or thermal paste. Once a thermal pad or paste has been used, it may have deformed or absorbed contaminants, reducing its effectiveness. Always use a new thermal pad or apply fresh thermal paste when remounting a heatsink.
-
What happens if I apply too much thermal paste?
-
Applying too much thermal paste can be counterproductive. Excess thermal paste can create a thicker bond line, increasing thermal resistance and potentially causing the paste to spill onto surrounding components. It is better to apply a small amount of thermal paste and allow the pressure from the heatsink to spread it evenly.
-
Can I use thermal pads or thermal paste on other components besides heatsinks?
- Thermal pads and thermal paste can be used on various components that require heat dissipation, such as power transistors, voltage regulators, and LED modules. However, always consult the manufacturer’s guidelines and specifications to ensure compatibility and optimal performance.
Conclusion
Choosing between thermal pads and thermal paste for mounting your heatsinks depends on various factors, including thermal performance requirements, ease of application, gap-filling properties, electrical insulation, and cost considerations. Thermal paste generally offers better thermal conductivity and conformity, while thermal pads provide easier application and inherent electrical insulation.
By understanding the advantages and disadvantages of each option and considering your specific application needs, you can make an informed decision to ensure optimal cooling performance and long-term reliability of your electronic components. Always follow proper application techniques and manufacturer guidelines to achieve the best results.
Remember, the key to effective heat dissipation is not only the choice of thermal interface material but also the overall design of the cooling solution, including heatsink size, surface finish, and airflow management. By taking a comprehensive approach to thermal management, you can keep your electronic components running cool and stable, even under demanding conditions.
No responses yet